- FMA
- The Fabricator
- FABTECH
- Canadian Metalworking
Join This!
Hybrid laser welding expert Ed Hansen looks inside the multi-faceted future of hybrid laser welding.
- By Canadian Metalworking
- October 8, 2014
- Article
- Welding
Hybrid laser welding started in the ship building industry. What progress has it made here?
Major shipbuilders in Europe are systematically implementing hybrid laser welding. The technology generates enormous savings. Cruise ship manufacturer Meyer Werft, for example, has reported reducing total build time by 30 per cent due to implementing hybrid laser welding.
WHAT’S PREVENTED MORE WIDESPREAD ADOPTION?
Early adopters have been very secretive owing to the strong competitive advantage the technology creates. Without published case studies and data on economic return, it’s been difficult to grow awareness and acceptance of the technology.
WHAT ARE THE ECONOMIC BENEFITS?
In one automotive industry example, we showed a reasonable, four-year amortization on the costs incurred when adding the technology to their existing production. But if the company were to redesign the product, amortization would take less than a year, thanks to reduced material use. In another example, one redesigned rail car’s weight was reduced by 30 per cent. This translates into 30 per cent more payload for each rail car.
WHAT PARTICULARLY COST-EFFECTIVE APPLICATIONS HAVE YOU SEEN?
Hybrid laser welding is particularly well suited for mass production welding at high capacity utilization. Depending upon the application, hybrid laser welding can be three to ten times faster than conventional processes. The technology can lower heat input by as much as 90 per cent and this reduces the typical macroscopic distortion.
Additionally, we’ve seen benefits in weight-sensitive applications. We’ve also seen significant fatigue life improvement in products exposed to cyclical loading, such as car suspensions, pressure vessels, and bridge components.
WHAT DEVELOPMENTS IN LASER TECHNOLOGY HAVE INFLUENCED HYBRID LASER WELDING?
The continued development of high-power solid-state lasers with smaller form factors, greater efficiency, and lower cost has had a big effect on hybrid laser welding. Our transition to solid-state lasers in 2001 made it feasible to apply the technology to industrial settings. New technologies, particularly fibre delivery, let us integrate the process into conventional motion systems — robots, gantries and automation — which increased acceptance. Many laser improvements benefit other applications more than ours. We’re currently limited in how much laser power or brightness we can use productively. But in the future I see less expensive, compact lasers, which are easier for us to incorporate into existing production operations.
WHAT DOES THE FUTURE OF PROCESS CONTROL LOOK LIKE?
So far, most advances in process control have focused on visible surface features. In the future, we’ll look inside the weld and manage the process based on what we see below the surface, using a closed-loop, real-time control system. Improving weld stability inside the material and preventing the creation of discontinuities inside the weld will enhance quality control and allow us to reliably apply the process to thicker, larger sections.
EVERY TECHNOLOGY HAS ITS LIMITS. WHAT ARE THE CURRENT LIMITATIONS OF HYBRID LASER WELDING?
The thinnest application we’ve seen is around one millimetre. The fastest is a pressure vessel, three to four millimetres thick, welded at 6.1 metres per minute. This, by the way, makes it almost seven times as fast as conventional butt welding. There’s a big advantage to one-sided welds, particularly inside pressure vessels like those used for petrochemical tanks, hot water heaters, and in power plants. Using laser-augmented welding with filler wire, we can weld thicker segments with a non-penetrating hybrid laser variant. Our thickest one-sided, single-pass application was in half-inch thick steel, butt welded at 2.3 metres per minute.
WHAT APPLICATIONS SHOW THE MOST PROMISE?
We’ve seen significant interest from the energy industry. Over the next twenty years, production will be increased and many pipelines will be replaced. Many of these applications use high-strength materials and manufacturers will have to automate to keep up with demand. Promising opportunities exist in bridge building, where designs are moving toward more cable-stayed suspension and long span bridges. Weight is critical here. As manufacturing moves to lighter products, structures get thinner and distortion becomes a bigger problem.
HOW IS THIS TECHNOLOGY EXPANDING IN AUTOMOTIVE MANUFACTURING?
Transportation — shipbuilding, rail cars, truck trailers, mobile equipment, automobiles — offers the biggest area of growth. New efficiency standards and high fuel prices are driving higher structural efficiency. Hybrid laser welding is an enabling technology for the distortion reduction, mass reduction, and high-strength alloys important in steel and aluminum vehicle construction. In one recent project, an automotive manufacturer redesigned a product for hybrid laser welding and high-strength material. It not only improved the structure’s crashworthiness; it also reduced the weight by 40 per cent. Generally, automotive manufacturers find the cost per pound goes up when using high-strength materials, but when the overall weight drops, so does the total cost.
WHAT ROLE WILL HYBRID LASER WELDING HAVE IN THE FUTURE?
It’s exciting to think about the global effect hybrid laser welding can have in creating lighter, high-strength structures and reducing material consumption. Hybrid laser welding will change the way structures are built. I think we’ll see larger scale adoption of the technology, particularly as costs drop and more welding codes incorporate the technology.
About the Author
subscribe now
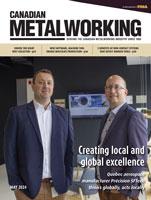
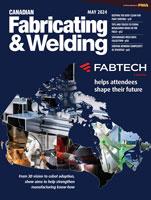
Keep up to date with the latest news, events, and technology for all things metal from our pair of monthly magazines written specifically for Canadian manufacturers!
Start Your Free Subscription- Industry Events
Automate 2024
- May 6 - 9, 2024
- Chicago, IL
ANCA Open House
- May 7 - 8, 2024
- Wixom, MI
17th annual Joint Open House
- May 8 - 9, 2024
- Oakville and Mississauga, ON Canada
MME Saskatoon
- May 28, 2024
- Saskatoon, SK Canada
CME's Health & Safety Symposium for Manufacturers
- May 29, 2024
- Mississauga, ON Canada