Editor
- FMA
- The Fabricator
- FABTECH
- Canadian Metalworking
Resistance welding takes on difficult materials
Aluminum, hot-stamped high-strength steels, and other challenging materials require more precise resistance welding techniques
- By Rob Colman
- Updated February 13, 2023
- June 16, 2017
- Article
- Welding
The increased use of aluminum and hot-stamped high-strength steels, particularly in the automotive industry, has required welding experts to explore new approaches to their discipline. Resistance welding is no exception.
Electric resistance welding creates a weld with heat generated by the electrical resistance of material combined with the time and the force used to hold the materials together during the weld.
The challenge with resistance welding aluminum is that when the polarity of the electrodes remains the same, you start to magnetize the tooling and can get more wear on the upper electrode. This causes the weld nugget to shift from the focal point of the weld, essentially creating a weaker weld.
The challenge with high-strength lightweight steels is that if too much heat is applied to them, they can become brittle and crack. To effectively resistance-weld this kind of steel, you have to apply very high force and very high currents for a very short amount of time.
“The magic number for the current is between 3 and 4 milliseconds,” said Bob Donovan, sales engineer, Dengensha America. “What is interesting about welding this material is it doesn’t get hot like standard resistance welds because it is not hot enough for a long enough period of time to transfer the heat through the material. You are not damaging the metallurgical structure of the material because it is processed so fast.”
Resistance Welding Choices
Dengensha has been working on a couple of different options for producing effective resistance welds with these and other materials. The “big brother” among these technologies is its Flexwave Welder, which is equipped with an inverter in its output stage.
“What that technology allows us to do is control the output waveform and deliver it precisely as needed by the user for the product being welded,” said Donovan. “Because we can control the waveform, we can have it switch polarity on-the-fly. This way, we can offset for the sort of nugget shift you get with aluminum if you magnetize the tooling.” Dengensha has patented this technology.
Making it Easier
"There are some other ways that resistance welding machine manufacturers are trying to manage this problem now with transformers, but with this technology it is built right into the machine, which simplifies the process,” Donovan explained.
The Flexwave system is also designed to deliver a high current to the material quickly, and for a short amount of time, if that is what is required for the material. It doesn’t discharge its capacitor completely in the process, either, which means that recharge time is also shorter.
This system is the company’s large-capacity machine. It has a maximum short-circuit current of 150,000 amps with a maximum electrode force of 30 kN. With the combined capabilities of a capacitor discharge welder and a medium frequency direct current system, it is suitable for making large or special projection welds.
The company’s NDZ Capacitor Discharge Welder, meanwhile, is designed for making smaller projection welds. It has a short-circuit current of 50,000 amps and an electrode force up to 10 kN. This resistance welding machine doesn’t require as large a power supply, has a much smaller footprint than the Flexwave, and is relatively easy to set up. It doesn’t have an inverter at the output stage, but it does allow control of the waveform in three different modes – energy, peak current, and constant current.
“Energy mode allows you to dump all the energy in the capacitor bank right across the load,” explained Donovan. This setting is ideal for creating a strong weld.
“Peak current allows you to charge the capacitors up and discharge at a certain current level. Once it discharges, you can say how long you want it to discharge and then shut it off so you don’t have to use the entire stored capacity of the bank,” Donovan continued. “Constant-current mode, meanwhile, allows you to set the weld at a lower current level for a longer period of time. This is ideal for post-weld heat treatment.
“So although this smaller system doesn’t have an inverter in it, it is like a pseudo-inverter. You have control in three different modes, whereas in traditional capacitor discharge welders you typically discharge the entire capacitor bank by just shorting the capacitor out through the electrodes.”
Both systems can be used in the challenging applications mentioned here. And as Donovan explained, the controls that accompany them are relatively easy to learn.
“Within about 10 minutes someone who understands what they need to do can become comfortable with the controls,” he noted.
Editor Robert Colman can be reached at rcolman@canadianfabweld.com.
Dengensha America, 440-439-8081, http://dengensha.comAbout the Author
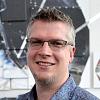
Rob Colman
1154 Warden Avenue
Toronto, M1R 0A1 Canada
905-235-0471
Robert Colman has worked as a writer and editor for more than 25 years, covering the needs of a variety of trades. He has been dedicated to the metalworking industry for the past 13 years, serving as editor for Metalworking Production & Purchasing (MP&P) and, since January 2016, the editor of Canadian Fabricating & Welding. He graduated with a B.A. degree from McGill University and a Master’s degree from UBC.
subscribe now
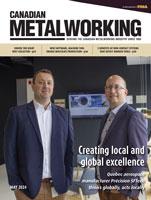
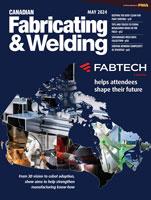
Keep up to date with the latest news, events, and technology for all things metal from our pair of monthly magazines written specifically for Canadian manufacturers!
Start Your Free Subscription- Industry Events
MME Saskatoon
- May 28, 2024
- Saskatoon, SK Canada
CME's Health & Safety Symposium for Manufacturers
- May 29, 2024
- Mississauga, ON Canada
DiPaolo Machine Tools Open House 2024
- June 4 - 5, 2024
- Mississauga, ON Canada
FABTECH Canada
- June 11 - 13, 2024
- Toronto, ON Canada
Zoller Open House & Technology Days 2024
- June 12 - 13, 2024
- Ann Arbor, MI