Editor
- FMA
- The Fabricator
- FABTECH
- Canadian Metalworking
How will you address your automation education gap?
Growing trend toward reshoring, nearshoring operations demands automation know-how
- By Rob Colman
- November 1, 2022
A global ABB survey has revealed a growing trend in U.S. and European businesses toward reshoring or nearshoring operations to build resilience in the face of global challenges. It also noted that there is a significant education gap in the skills necessary for these strategies to succeed.
“The world is constantly evolving—businesses are shifting existing structures and adopting new technologies to future-proof their operations for a variety of challenges and uncertainties, with robotic automation playing a key role,” said Sami Atiya, president of ABB’s Robotics & Discrete Automation Business. “We need significant investment in continuous education to prepare our existing and future workforce to thrive in an age of robotics and automation, important not only to prepare for the widespread shifts we are seeing, but to create prosperous societies going forward.”
ABB’s 2022 survey of U.S. and European business leaders revealed that 74 per cent of European and 70 per cent of U.S. businesses are planning to re- or nearshore operations to build their supply chain resilience in response to labour shortages, the need for a more sustainable global footprint, and global uncertainty.
Most of these businesses view automation as the enabler of these shifts, with the majority planning to invest in robotics and automation in the next three years to facilitate this shift.
The survey, however, also found a significant gap in the education and training needed to ensure the skills necessary to make it happen. Fab shops across Canada have been trying to manage this issue for years; they know they want to advance their capabilities with robotics, but who is going to carry the team forward?
Most shops I’ve spoken to in the past few years who have successfully introduced robotics onto the shop floor have had a champion for the initiative on staff and then developed the shop’s internal knowledge base from there. These days, some shops are implementing cobots as a way of easing team members into the idea of robotics use.
There never seem to be enough students coming out of schools to cover the skills needed on a shop floor. However, if you already have a skilled welder in your shop with an aptitude for electronics, or a new, young welding recruit who, due to their very age, is a “digital native,” you can, with the right support, develop your robotics champion from within.
This is another example of when it can be useful to reach out to colleges in your area to get a better sense of how they may be able to help you. For instance, Sheridan now has its micro-credential course in robotics and industrial applications. Could it be worthwhile to send a new young hire back to school to build your future strength?
For those readers who will be joining us at FABTECH in Atlanta, if you’re taking steps to push your robotics and automation further, it’s worth talking to suppliers about how they can assist with training and rollout initiatives.
subscribe now
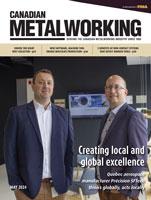
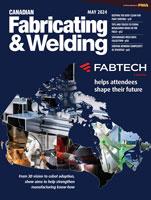
Keep up to date with the latest news, events, and technology for all things metal from our pair of monthly magazines written specifically for Canadian manufacturers!
Start Your Free SubscriptionAbout the Author
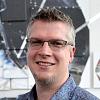
Rob Colman
1154 Warden Avenue
Toronto, M1R 0A1 Canada
905-235-0471
Robert Colman has worked as a writer and editor for more than 25 years, covering the needs of a variety of trades. He has been dedicated to the metalworking industry for the past 13 years, serving as editor for Metalworking Production & Purchasing (MP&P) and, since January 2016, the editor of Canadian Fabricating & Welding. He graduated with a B.A. degree from McGill University and a Master’s degree from UBC.
- Industry Events
Automate 2024
- May 6 - 9, 2024
- Chicago, IL
ANCA Open House
- May 7 - 8, 2024
- Wixom, MI
17th annual Joint Open House
- May 8 - 9, 2024
- Oakville and Mississauga, ON Canada
MME Saskatoon
- May 28, 2024
- Saskatoon, SK Canada
CME's Health & Safety Symposium for Manufacturers
- May 29, 2024
- Mississauga, ON Canada