Editor
- FMA
- The Fabricator
- FABTECH
- Canadian Metalworking
New technologies, employee profiles warrant a safety refresher
Does your safety training address the needs of your team and equipment?
- By Rob Colman
- January 17, 2023
In almost all shops I visit, at some point its focus on safety is raised in a positive way. Company representatives explain to me how a particular project or initiative addresses particular health and safety goals for their employees. It’s not a nice-to-have addition to profit goals or a cost-of-doing-business discussion, it’s a genuine understanding that employee safety is an integral part of a company’s success.
But in the rush to get the job done, sometimes regular safety practices fall by the wayside. For instance, Threads of Life surveyed members of the Angus Reid Forum in spring 2022 to learn more about employers’ hiring intentions and safety programs for young workers. A majority of businesses that responded to the survey – 66 per cent – said they planned to hire as many or more young workers (less than 25 years old) in 2022 than they have in the past two years. While 69 per cent of the employers have an orientation program for new workers and more than half (51 per cent) have a safety program, 19 per cent said that they have no orientation, onboarding, emergency, or safety training for new employees.
Even for those shops that do have a robust safety training system in place, it’s of course important to revisit and revamp these programs to keep them fresh and relevant to all employees. The new year is a good time to take a new look at your safety training.
Two reasons why it can’t hurt to revisit these processes is the changing equipment mix on your shop floor and the changing demographic profile of employees.
For instance, the introduction of cobots or hand-held laser welding requires a fresh look at safety rules around certain processes. When a welding cobot is moved from one area to another, what are the procedures to ensure proper fume extraction measures are in place? What rules are in place to ensure those close to the welding cobot are properly protected? For a hand-held laser welding setup, is the operator wearing all the necessary safety equipment? Are they in an enclosed area so all surrounding employees are safe?
In terms of employee mix, do you have personal protective equipment (PPE) that is properly sized for women working in your shop? According to a new CSA Group report, many women struggle to find equipment that fits them properly. If an employee has to adjust or modify PPE on the job, that can be both a safety and legal issue for an employer. It’s worth it to perform a staff safety gear audit to make sure employee PPE is doing what is required to keep them safe at work.
Adapting to changes in the market is an evergreen theme, and safety is an integral part of that. Wishing you a healthy, busy, productive, and, of course, safe 2023.
subscribe now
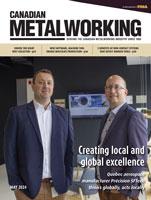
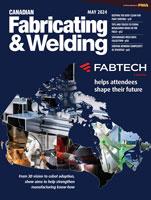
Keep up to date with the latest news, events, and technology for all things metal from our pair of monthly magazines written specifically for Canadian manufacturers!
Start Your Free SubscriptionAbout the Author
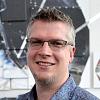
Rob Colman
1154 Warden Avenue
Toronto, M1R 0A1 Canada
905-235-0471
Robert Colman has worked as a writer and editor for more than 25 years, covering the needs of a variety of trades. He has been dedicated to the metalworking industry for the past 13 years, serving as editor for Metalworking Production & Purchasing (MP&P) and, since January 2016, the editor of Canadian Fabricating & Welding. He graduated with a B.A. degree from McGill University and a Master’s degree from UBC.
- Industry Events
Automate 2024
- May 6 - 9, 2024
- Chicago, IL
ANCA Open House
- May 7 - 8, 2024
- Wixom, MI
17th annual Joint Open House
- May 8 - 9, 2024
- Oakville and Mississauga, ON Canada
MME Saskatoon
- May 28, 2024
- Saskatoon, SK Canada
CME's Health & Safety Symposium for Manufacturers
- May 29, 2024
- Mississauga, ON Canada