Senior Product Specialist
- FMA
- The Fabricator
- FABTECH
- Canadian Metalworking
5 considerations for selecting boring tools
Your tooling setup includes everything from the spindle to the insert
- By Matt Tegelman
- Updated July 30, 2023
- August 23, 2023
- Article
- Cutting Tools
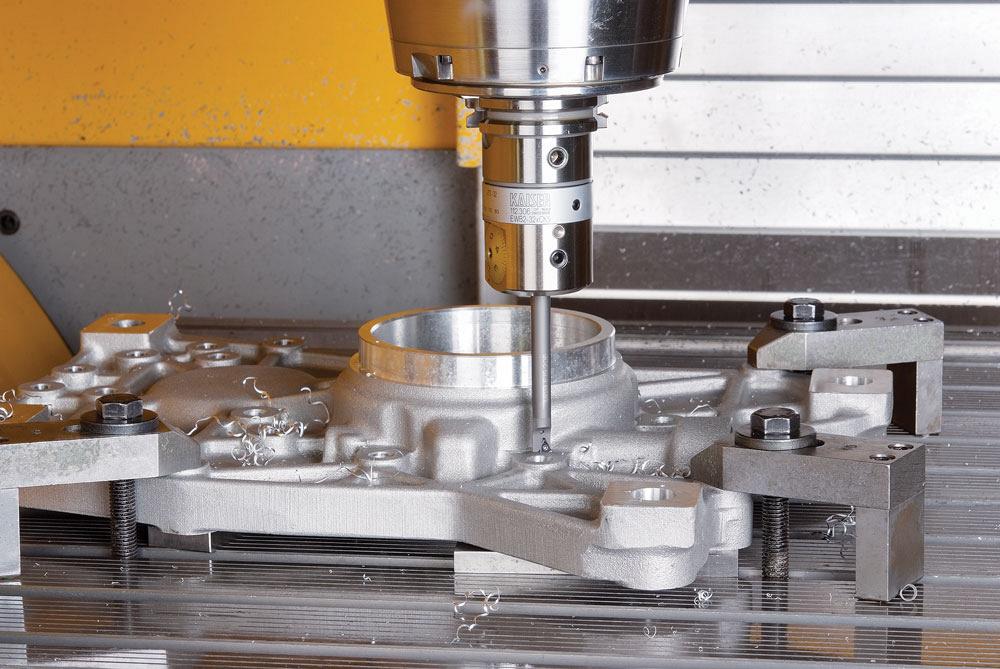
Improve cutting performance by optimizing tool length with a minimal number of components. Modular tooling systems are available for all common types of machine tool spindles, including BIG-PLUS for improved repeatable accuracy.
Boring can be tricky business, with several variables that can impact performance.
And, as with many things metal cutting-related, many boring issues can be solved by troubleshooting tooling implementation, including lengthy cycle times, short tool life, and poor part quality.
Furthermore, skimping on quality boring tools and accessories can cost more in the long run. Five important considerations should be examined when selecting boring tools and accessories.
1. Consider Modular Boring Systems
Modular tool systems allow you to create tool assemblies for specific applications quickly and easily without the need for new, specialized tooling and toolholders. This is helpful in challenging boring applications because it allows machinists to troubleshoot with the components they have on hand.
This flexibility--plus quick and easy changeouts--greatly reduces setup and engineering time. Keep in mind, however, that modular boring assemblies should always be as short as possible to reduce vibration.
Modular boring assemblies should contain no more than five components (ideally four or fewer), not including boring head insert holders.
2. Leverage Digital Boring Heads to Improve Performance
Digital boring heads display setup measurements on a small readout right on the tool.
This allows for faster, more streamlined precision adjustments. Bluetooth-enabled versions even allow for more efficiency. But perhaps most important, this technology improves performance and eliminates costs related to test cuts and scrapped parts.
Digital boring heads are most effective in applications that call for tight tolerances or when cutting difficult-to-machine materials. In fact, some digital boring heads have adjustment increments as fine as 50 millionths of an inch in diameter.
3. Think About Vibration Resistance
Vibration can wreak havoc on boring operations, affecting the speeds and feeds that can be used, shortening cutting tool life, and reducing the quality of the finished part.
Preventing vibration through tooling selection can be done in two ways:
- Select the largest diameter and smallest length possible for your boring assembly.
- Consider licensed, dual-contact tooling.
Dual-contact holders provide simultaneous contact between the machine spindle and the holder’s taper and flange. This clean mating of the toolholder and spindle greatly increases rigidity to reduce vibration.
But buyer beware: Only choose dual-contact holders that are licensed for your machine spindle.
Non-licensed toolholder manufacturers do not have the critical specifications necessary to make true dual-contact holders. The result, at best, is less-than-ideal boring performance; at worst, you could damage your machine’s spindle.
4. Research Twin Boring Cutters
When it comes to making holes at volume, balancing speed with performance can be challenging.
A common answer often is helical interpolation with a mill for roughing out holes, but twin boring cutters offer an alternative to helical interpolation milling that has several advantages.
Twin boring cutters for roughing operations are fairly simple. They require only one setup, use no specialized equipment, and require less programming time than helical interpolation.
Performance is very good as well. There is a good load balance in the cut for reliable and consistent performance and better chip evacuation because smaller chips are made. Finally, the plunging motion of twin boring results in axial load rather than radial, which better preserves machine and spindle components.
5. Remember the Importance of Inserts, Grades, Geometries
Optimize your boring applications with suitable insert grades and geometries. It may seem like metal cutting 101, but sometimes the details get lost in the shuffle.
General Tips For Quality Boring
- Pressed geometry inserts typically last longer (in stable conditions), but the radial cut depth should be at least one-half of the insert’s nose radius.
- Look for inserts with ground geometry because they are suitable for deep or long-reach bores, long-chipping materials, and for instability issues.
- Stay on top of the latest insert grades and coatings when they become available. There’s always something new to help maximize performance.
Regardless of how simple or complex your boring application is, it pays to have numerous options and expert guidance when challenges arise. Make sure your tooling provider is up to the challenge too.
Matt Tegelman is senior product specialist for BIG DAISHOWA, 2600 Huntington Blvd., Hoffman Estates, Ill. 60192, 224-770-2999, www.bigdaishowa.com.
About the Author
Related Companies
subscribe now
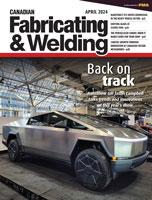
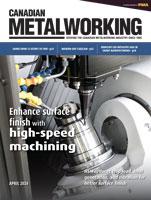
Keep up to date with the latest news, events, and technology for all things metal from our pair of monthly magazines written specifically for Canadian manufacturers!
Start Your Free Subscription- Trending Articles
Automating additive manufacturing
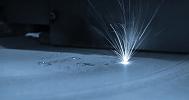
Sustainability Analyzer Tool helps users measure and reduce carbon footprint
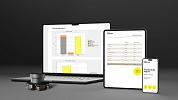
CTMA launches another round of Career-Ready program
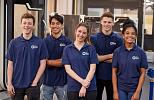
Sandvik Coromant hosts workforce development event empowering young women in manufacturing
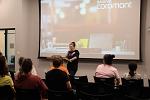
GF Machining Solutions names managing director and head of market region North and Central Americas
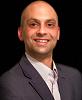
- Industry Events
MME Winnipeg
- April 30, 2024
- Winnipeg, ON Canada
CTMA Economic Uncertainty: Helping You Navigate Windsor Seminar
- April 30, 2024
- Windsor, ON Canada
CTMA Economic Uncertainty: Helping You Navigate Kitchener Seminar
- May 2, 2024
- Kitchener, ON Canada
Automate 2024
- May 6 - 9, 2024
- Chicago, IL
ANCA Open House
- May 7 - 8, 2024
- Wixom, MI