- FMA
- The Fabricator
- FABTECH
- Canadian Metalworking
A smooth finish
Cermet inserts perform in high-speed machining
- By Sue Roberts
- October 24, 2017
- Article
- Cutting Tools
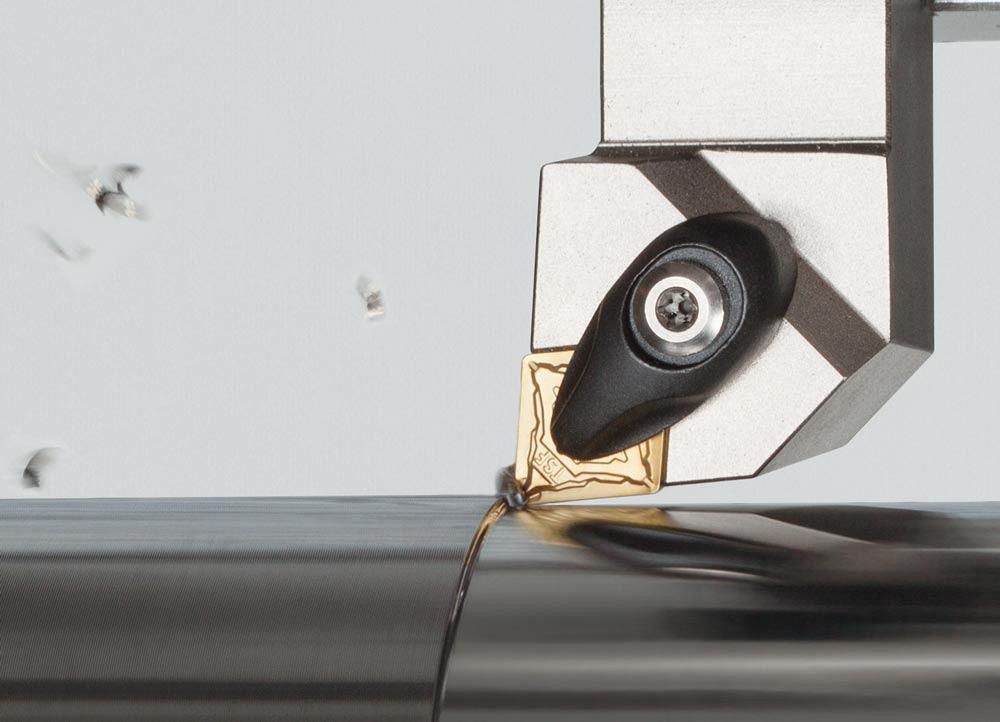
The smooth cutting edge of a cermet insert leaves a high-quality surface finish. Photo courtesy of Tungaloy Canada.
Cermet, a combination of ceramic particles held together by nickel or cobalt, is typically not the first choice when choosing an insert material.
Unlike machining shops in North America, Japanese shops use cermet to cut chips about 20 per cent of the time. “Japan has been adding cermet to its everyday arsenal of cutting tool options so it has a larger piece of the insert market, but in North America that percentage drops to about 3 per cent,” said John Mitchell, general manager of Tungaloy Canada.
“Some machinists still view cermet as too brittle to use. That characteristic, however, has been dramatically changed. Today there are cermet grades that have the same traverse rupture strength as many carbide materials,” he said.
While technology has made cermet easier to use, cemented carbide has also advanced, gaining finer finishing capabilities in hard materials. In some cases, new carbide grades have nudged cermet out of jobs. But cermet’s thermal stability in high heat, resistance to oxidation, wear-resistant properties, and the recent reduction in brittleness is keeping it at the top of lists, particularly when a smooth surface is a crucial specification.
Kevin Burton, product and industry specialist for turning products at Sandvik Coromant, said, “Many modern cermet inserts are nickel-free, which eliminates the environmental concerns. They have a core particle structure of titanium carbonitride which adds to the wear resistance. The second hard phase of a titanium-based carbonitride, with niobium and tungsten, gives it more plastic deformation resistance, so it holds its shape longer. The amount of cobalt controls the toughness to extend the tool life.
“Depending on the material being cut, coatings can increase the wear resistance and extend the tool life,” Burton explained.
EXTEND CERMET USE
The cutting performance of cermet is about midway between that of ceramic and carbide. Cermet inserts are used most frequently in finishing applications. Their high heat- and wear-resistant properties allow machining at the high revolutions per minute and light feed rates that best produce high quality surface finishes.
The smooth finish of the cermet insert cutting edge prevents material build-up, making it a good choice for cutting gummy materials like low-carbon steel.
“The smooth surface structure allows a much smoother flow of material during the cutting process. The edge stays sharper longer. It retains its original micro-geometry longer than carbide,” Burton said.
“Uncoated cermet is a good choice for finishing low-alloy and alloy steels. It’s also good for cast iron work where good surface quality, close tolerances, and/or low cutting forces are involved. A PVD [polyvinyl dichloride] coating helps when the job involves finishing and semifinishing of the low-alloy, alloy steels, or stainless.”
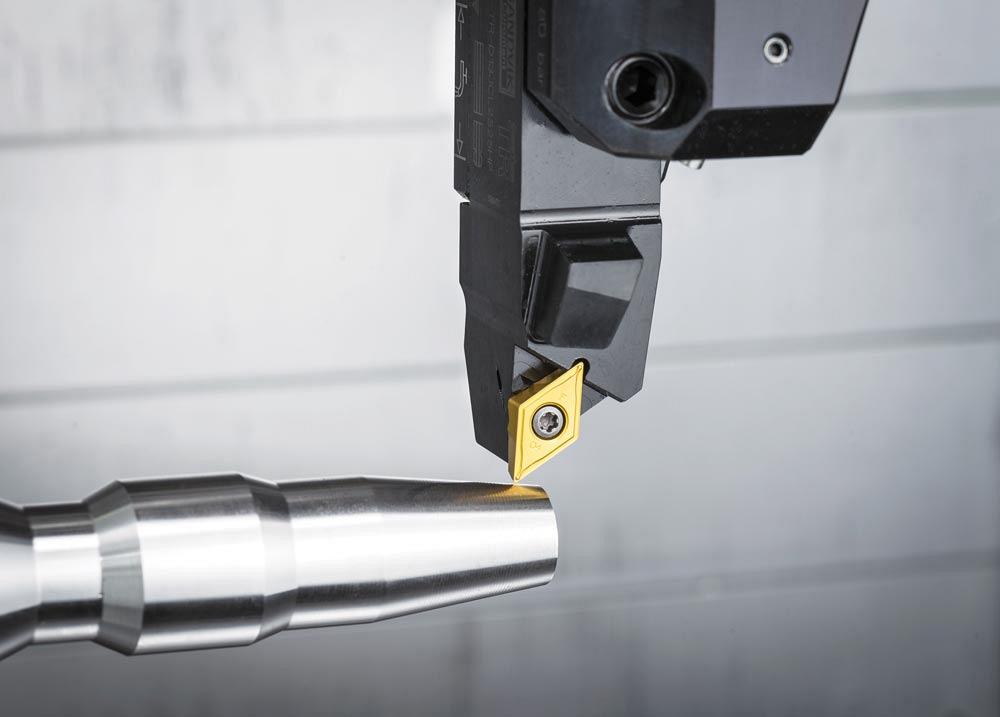
The smooth surface structure of a cermet edge allows for a smoother flow of material during the cutting process. Photo courtesy of Sandvik Coromant.
Other applications, however, can benefit from cermet inserts. Mitchell said, “They can be used in many applications from finish to medium cutting applications where the depth of cut is 0.80 inch or less. In low-carbon steel and powdered material applications, they are usually a good first choice.”
PREDICT TOOL LIFE
Using cermet does have a downside. Even though it can provide a long cutting life, Burton said there is no indication of when the edge is going to chip or become ineffective.
“With carbide you can dial in the cutting parameters and get a gradual flank wear which is very predictable. You set the size just above nominal and wear down to just below. For example, you can say that after 500 parts, we change the edge.
“With cermet there are so many variables that it is difficult to predict the exact length of tool life. So you set a timeframe for its use and leave it there. Based on our cutting data, we suggest using a 15- to 20-minute tool life as a rule of thumb. There are times when you can get a half-hour or an hour but it is difficult to pin down because of variances in the material being processed. You can order the same material from the same foundry and it might be one or two points different in hardness. That difference can make the interaction between the material and the cermet insert totally different and impact the insert cutting life,” said Burton.
CONSIDER THE ALTERNATIVE
Take the time to check on advances in insert technologies for both carbide and cermet. Both types of inserts are incorporating advanced technologies to make difficult machining easier. It’s a bit like leapfrog. Carbide advances, cermet advances--repeat.
“I think advances in carbides have pushed cermet a little to the side, but machining is not black and white. No carbide insert will give the best results 100 per cent of the time,” said Burton. “Cermet is a good alternate for those applications.”
When using cermet cutting inserts, Sandvik Coromant suggests:
- Use low feed and depth of cut
- Change the insert edge when flank wear reaches 0.3 millimeter
- Avoid thermal cracks and fractures by machining without coolant
Tungaloy Canada, 519-758-5779, www.tungaloy.com/ca
Sandvik Coromant, 800-726-3845, www.sandvik.coromant.com
About the Author
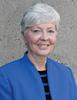
Sue Roberts
2135 Point Blvd
Elgin, IL 60123
815-227-8241
Sue Roberts, associate editor, contributes to both Canadian Metalworking and Canadian Fabricating & Welding. A metalworking industry veteran, she has contributed to marketing communications efforts and written B2B articles for the metal forming and fabricating, agriculture, food, financial, and regional tourism industries.
Roberts is a Northern Illinois University journalism graduate.
subscribe now
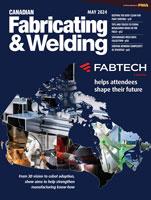
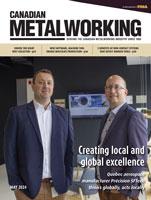
Keep up to date with the latest news, events, and technology for all things metal from our pair of monthly magazines written specifically for Canadian manufacturers!
Start Your Free Subscription- Industry Events
Automate 2024
- May 6 - 9, 2024
- Chicago, IL
ANCA Open House
- May 7 - 8, 2024
- Wixom, MI
17th annual Joint Open House
- May 8 - 9, 2024
- Oakville and Mississauga, ON Canada
MME Saskatoon
- May 28, 2024
- Saskatoon, SK Canada
CME's Health & Safety Symposium for Manufacturers
- May 29, 2024
- Mississauga, ON Canada