Digital Machining Specialist
- FMA
- The Fabricator
- FABTECH
- Canadian Metalworking
Aerospace manufacturers keep their edge by adopting digitalization
How to go from trailing to leading
- By Cory Carpenter
- October 13, 2023
- Article
- Cutting Tools
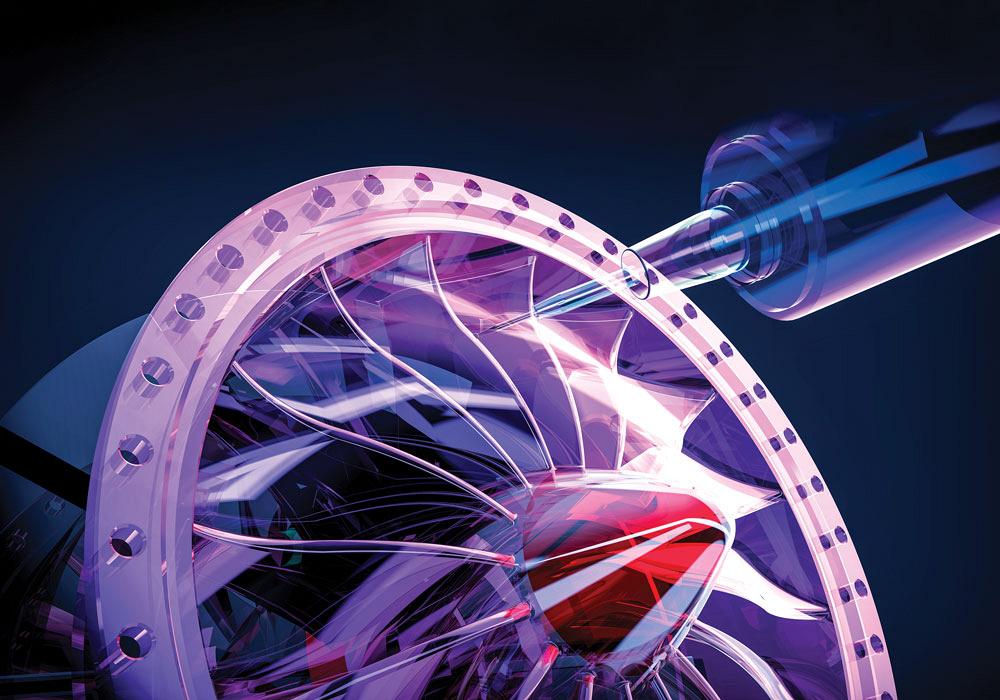
With the right digitalization strategy, condition monitoring platform, and technology partners for connected machining, aerospace manufacturers give their operators crucial insights into their work.
According to the Aerospace Industries Association of Canada (AIAC), the Canadian aerospace industry is making a strong post-pandemic recovery. It’s also a leading driver in innovation.
The AIAC’s “State of Canada’s Aerospace Industry Report” highlights Canada’s aerospace industry as the leader in R&D investment, outpacing other Canadian industries by more than double.
For Canadian aerospace machine shops, maintaining a strong pace of growth and leading-edge productivity should include considerations for digital technology and Industry 4.0 capabilities. This is where real-time data collected from equipment can be displayed in easy-to-understand visualizations that can help operators, plant managers, and engineers make better decisions.
Understanding Machine Tool Data
When machine shops solely depend on the status of green, yellow, and red Andon lights, they’re not making the best use of the data their machines are generating. What does that red light mean? Has the machine crashed? Is engineering doing a test, or is the machine out of work material?
In aerospace work, where digitalization is common, manufacturers often have in-house analytics that take historical data exported from machines to assess processes after the fact. But if they take advantage of the latest generation of connected machine monitoring systems, they can get real-time, in-depth analytics that capture and report the data underlying those green, yellow, and red lights.
That data is based on rules that are established in collaboration between the condition monitoring software provider and the machining operation. These rules can follow industry-standard measurements, incorporating factors such as utilization, performance, and production quality. These platforms are designed to capture and report the kind of data that machining operations have determined to be crucial to sustain continuous improvement and lean manufacturing efforts.
Pinpoint Your Data Pain Points
With a lot of machines generating a lot of data, how do you determine what data to focus on? Start by applying classic lean principles.
Identify persistent issues or bottlenecks—waste, unscheduled downtime, and quality issues with specific parts or machines—where more complete data can help you implement a root cause analysis.
For example, many shops find that they spend more time in machine setup than actual machining. The right condition monitoring software can be configured to track key parameters: setup times; part load/unload time; and time spent on fixture changes, tool changes, and blow-off cycles.
Reducing cost per part is one of the most common pain points for aerospace part manufacturers. Without overarching communication between different machines, it is impossible to monitor the points of production that are making cost-per-part reduction difficult. This typically is caused by numerous variables, including excess waste, product defects, and poor management practices. Adequate connectivity can help you identify this and make adaptations.
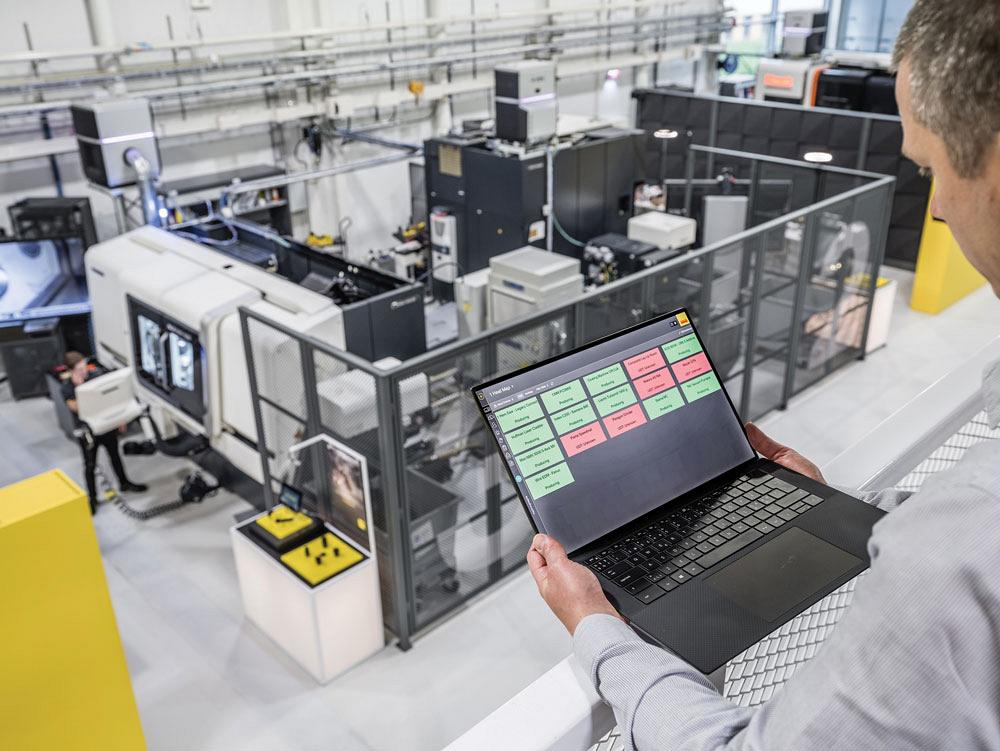
Sandvik Coromant’s CoroPlus Machining Insights is machine monitoring software deployed as a cloud-based application without any hardware installation. It is accessible from tablets, phones, and computers with an Internet connection, enabling remote monitoring.
Today’s machining condition monitoring platforms let you easily configure, track, and zero in on these data points. More importantly, this data is now available in real time and is much more accurate, equipping you with the data to make operational changes and business decisions much more rapidly and with confidence that you will achieve your optimization goals.
Classifying Data for Meaningful Business Decisions
In lean manufacturing continuous improvement processes, the first step is often to ask operators on the shop floor about their persistent issues. With today’s condition monitoring software, you now can start collecting dynamic input from ongoing operator input to identify patterns. In addition, you can directly ask the digitally connected machines what’s going on—eliminating the need to manually monitor machines with a stopwatch and spreadsheets.
One important step in the process is classifying the data that the system captures into categories that can drive meaningful business decisions. For example, you could focus on a machine or group of machines and find out how much time was spent cutting a specific part. Further analysis then identifies the part or parts that caused the most unscheduled downtime on those machines.
Comparing the most optimized machines running that part with other machines enables you to make decisions about how different machines are scheduled to improve maintenance, replace tooling, and determine if additional capacity is needed.
Choosing a Condition Monitoring Provider
So, you’ve identified the need for condition monitoring software. How do you navigate selecting the right one?
There are many commercially available condition monitoring software platforms. However, CNC machines have many unique operating factors, so these general packages may require significant customization to generate actionable, real-time data applicable to common machining utilization and quality manufacturing challenges.
That’s why it is advantageous to select a platform created by a manufacturer that has in-depth machining expertise. Platforms from these suppliers are already configured to capture, organize, and analyze machining data, eliminating the need for extensive configuration and saving valuable time when you begin using them.
Manufacturing companies that supply high-quality condition monitoring software also should offer valuable technical support—both remotely and on-site. They also should continue the partnership, working hand in hand on improvement efforts and offering their expertise in aerospace manufacturing knowledge for support through the whole process.
The initial payback typically occurs through waste reduction efforts in your processes because of the insights gleaned from the software. This is mainly because the average shop typically, and most often unknowingly, operates at a 30 per cent to 40 per cent utilization rate of its assets.
Why Manufacturing Dashboards Matter
A key factor to consider when selecting condition monitoring platforms is the design and ease of use of the operator dashboards they offer.
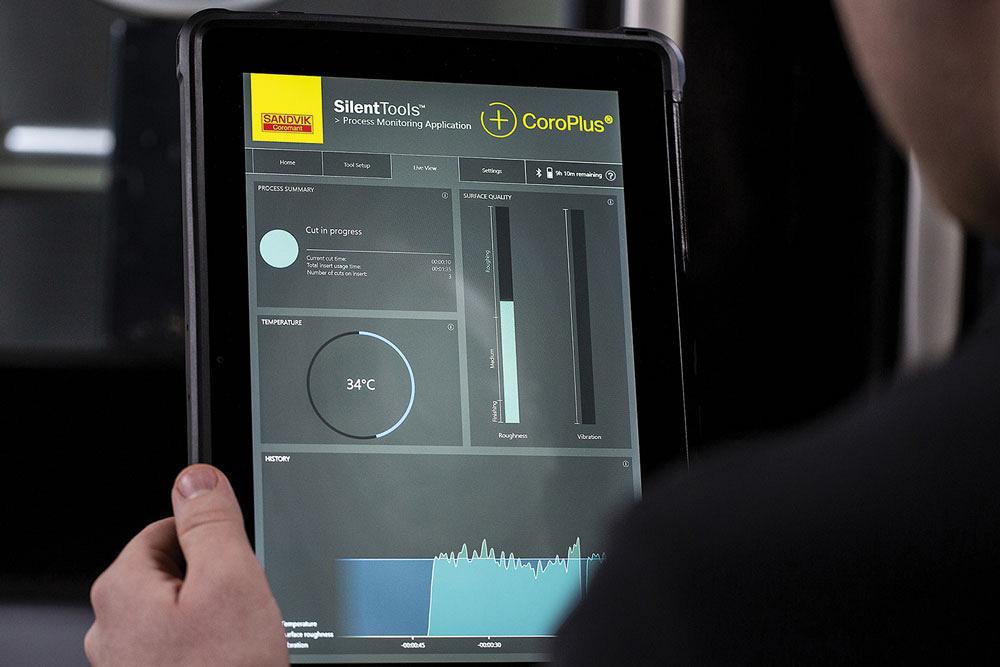
A machine-integrated version of Sandvik Coromant’s Silent Tools Plus, with CoroPlus Connected, uses data generated at the cutting zone to identify potential problems.
Well-designed dashboards provide critical visual metrics and alerts on the key indicators you’ve established to assess machining performance. This real-time data about machine stop causes, faults, and alarms enables operator and engineering intervention to prevent issues from becoming serious problems. These dashboards also provide insights into opportunities to improve resource planning, asset management, and cost and time prediction.
The best platforms support drag-and-drop programming for easier setup and configurability within the system to help address your needs and workflows. They should also support tablet and smartphone displays so operators can receive alerts and respond to issues without having to go to specific machines.
Improving Machine Connectivity With the Cloud
Cloud-based condition monitoring platforms offer multiple advantages compared to systems that must be installed and networked on servers at your shop. Most new machine tools have high-speed Ethernet-based interfaces that make it much easier to connect machine tools on production floors to external networks with access to cloud-based applications.
The kind of complex, real-time analysis and reporting provided by these condition monitoring programs uses advanced algorithms and significant processing power, which the cloud is much more able to support than on-site servers. Additionally, cloud-based platforms offer the ability to see not only the current state of the machines but also how those machines have performed since the first day they were connected.
With cloud-based technology, data is protected behind firewalls, with condition monitoring providers offering systems that typically comply with strict government security protocols covering sensitive defence and intelligence applications. A cloud-based application is managed and kept up to date by the platform provider. This means that machining company IT departments are not required to maintain expertise in managing and updating this kind of application.
One further advantage is that cloud-based condition monitoring programs can be rapidly implemented without any additional hardware, with the same system supporting multiple locations worldwide. They also allow for remote support capabilities, enabling technicians to collaborate with end users on a specific machine issue and implement the resolution over the network.
Embracing Edge Computing in Aerospace
Looking to the future, it is likely that connected machining will evolve into a hybrid environment that uses cloud-based analytics alongside edge computing.
Edge computing describes data capture, processing, and analysis that take place on a device—on the “edge” of the process—in real time. Unlike cloud-based methods, which typically collate data from several machines at a centralized store, edge computing is distributed computing that brings computation and data storage of a single machine or a group of machines closer to the sources of data. This improves response times and saves bandwidth.
In aerospace manufacturing, conducting analytics at an individual device can save costs and resources in data processing. To be clear though, edge computing is not an alternative to cloud-based methods. In fact, each is making the other’s job easier.
In an aerospace manufacturing environment, edge analytics might be used when boring large components, such as metal cutting of a large aircraft part. One small mistake here can be incredibly costly.
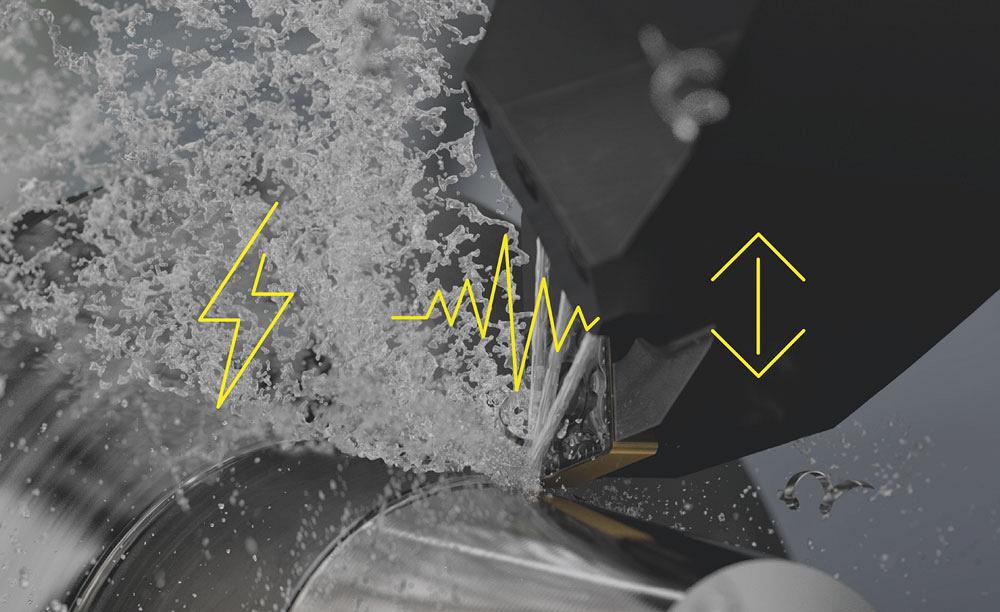
In the aerospace industry, the latest generation of connected machine monitoring systems capture and provide real-time, in-depth analytics and cutting data.
Data generated at the cutting zone is used to identify potential problems. Automated cutting actions are then applied to avoid any disastrous mistakes. This methodology helps ensure that decentralized problems are identified immediately—at the edge—while data from wider machining processes are correlated to be analyzed separately.
Moving Aerospace Manufacturing Forward With Digitalization
As reported by AIAC, Canada’s aerospace industry is investing heavily in innovation. While intense aerospace R&D might include things like robotics, materials science, and additive manufacturing, it’s important to remember that digitalization is an essential advancement that ties these technologies together.
With the right digitalization strategy, condition monitoring platform, and technology partners for connected machining, operations can give their human operators crucial insights to keep aerospace manufacturing moving forward.
Cory Carpenter is a digital machining specialist for Sandvik Coromant, 2550 Meadowvale Blvd., Mississauga, Ont. L5N 8C2, 905-826-8900, www.sandvik.coromant.com.
About the Author
Related Companies
subscribe now
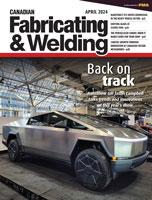
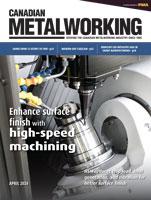
Keep up to date with the latest news, events, and technology for all things metal from our pair of monthly magazines written specifically for Canadian manufacturers!
Start Your Free Subscription- Trending Articles
Automating additive manufacturing
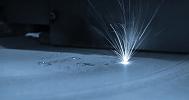
Sustainability Analyzer Tool helps users measure and reduce carbon footprint
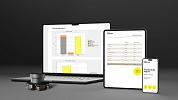
CTMA launches another round of Career-Ready program
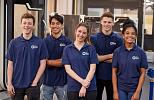
Sandvik Coromant hosts workforce development event empowering young women in manufacturing
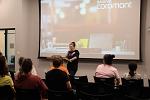
GF Machining Solutions names managing director and head of market region North and Central Americas
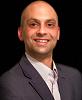
- Industry Events
MME Winnipeg
- April 30, 2024
- Winnipeg, ON Canada
CTMA Economic Uncertainty: Helping You Navigate Windsor Seminar
- April 30, 2024
- Windsor, ON Canada
CTMA Economic Uncertainty: Helping You Navigate Kitchener Seminar
- May 2, 2024
- Kitchener, ON Canada
Automate 2024
- May 6 - 9, 2024
- Chicago, IL
ANCA Open House
- May 7 - 8, 2024
- Wixom, MI