- FMA
- The Fabricator
- FABTECH
- Canadian Metalworking
High-efficiency milling speed changes rules
Tooling, software, and equipment combine capabilities to make the process work
- By Sue Roberts
- January 10, 2018
- Article
- Cutting Tools
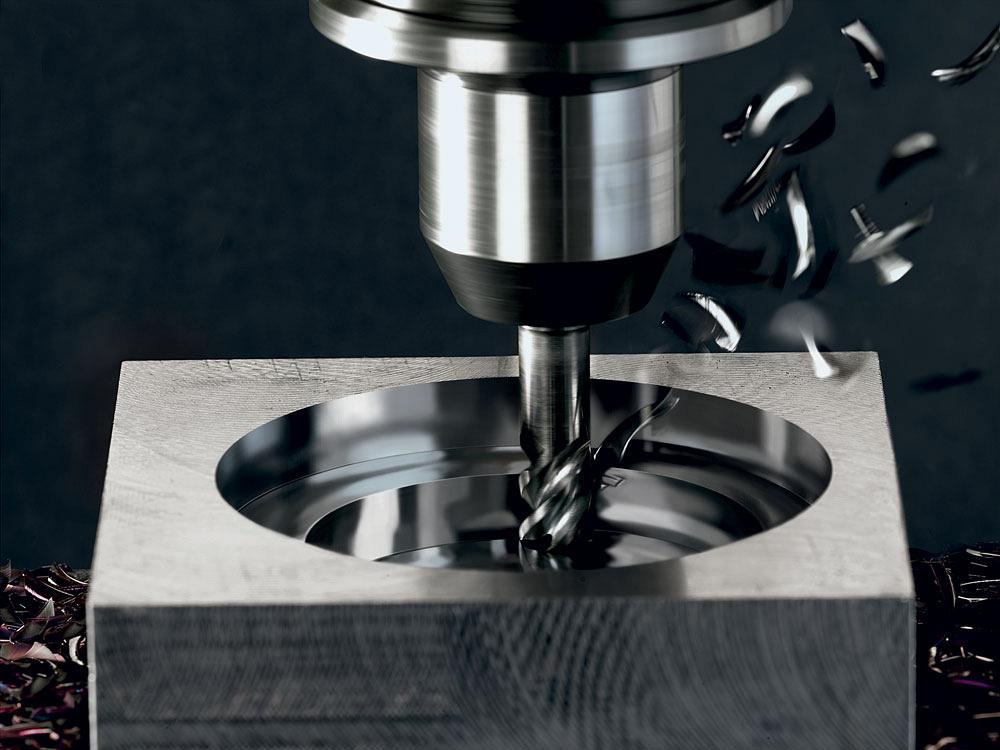
By taking light radial depths of cut, it is possible to use long axial engagement of the cutting edge to maximize tool efficiency. Photo courtesy of Walter USA LLC.
Stepping from the world of standard milling to high-efficiency milling (HEM) can change just about everything. HEM’s lower radial depth of cut (RDOC) and a higher axial depth of cut (ADOC) create consistent wear across the end mill cutting edge, generate less heat, and lessen the chance of tool failure. Machines can sustain less stress and tooling can last much longer.
Two basic concepts differentiate HEM from standard milling. One is radial chip thinning and the other is a constant tool engagement angle. Machine, software, and tooling must combine forces to make the process possible. The process is known by different names, frequently assigned by software companies as they design programs for the high-speed process, including dynamic milling, advanced roughing, and high-efficiency machining. The principles behind the various names, however, are basically the same.
Thinner Chips
Luke Pollock, product manager at Walter USA, described the process. “Machining with a light RDOC creates a chip that is thinner than the advance per tooth. This means that to get the correct chip thickness, the feed rate needs to be higher. We can increase the feed rate, sometimes by as much as three times the normal calculated rate. When machining into a corner, however, the tool engagement increases and the feed rates must be decreased to avoid chatter or tool breakage.
“To combat this, the tooling software develops a toolpath that maintains a constant tool engagement angle (TEA). By maintaining a constant TEA, the tool never gets over-engaged in the material and the machining condition stays constant. Combine this with elevated feed rates from radial chip thinning because of light RDOC and you have the concept of dynamic milling.”
Dan Doiron, milling products manager for Emuge Corp., referred to the process as advanced roughing. “Advanced roughing can be described as more of a transition into aggressive milling. It’s no longer the boxy, zig-zag, small-depth cuts. Today’s technology enables lead-in, lead-out, helical entry, ramping, trochoidal or circular style patterns, and in some cases, use of the full length of an end mill’s cutting flutes. It used to be roughing from the top down, but now it has turned into roughing from the bottom up.”
Variable Trajectories and Feed Rates
Software and tooling have necessarily advanced along with the milling processes.Alan Levine, managing director of Open Mind Technologies USA Inc. , said that advanced roughing techniques have been incorporated into most CAM software over the last five to 10 years. Rather than being considered advanced programs, these complex programs are now becoming the new norm.
“Traditional roughing toolpaths would be derived by taking a series of offsets from the internal or external boundaries of the desired region. This was fairly straightforward from a mathematical point of view, but was not necessarily ideal for metal removal.
“In a simple example of a rectangular pocket, the cutter would take a prescribed cut along the rectangle sides. Then in the corners the cutter would have increased material engagement as well as a change of direction. A shrieking sound would indicate poor cutting conditions, and a common solution would be to reduce feed rate. In some cases, that reduction would last for the rest of the program,” Levine said.
“Advanced roughing technique software sees these challenging areas and changes the toolpath trajectory to nibble into the corners and change feed rates to unify material removal and cutter performance. Then feed rates can be increased. With lower stress on the cutter, the deeper cuts are possible.”
Levine compared the new tooling paths with a circular, trochoidal-style motion to a spirograph. “The cutter motion includes nibbles and return moves to align for the next cut. Without incorporating additional software technology in the toolpath, the resulting cut time can actually increase due to the longer toolpath motion. Tool paths should be smooth so the machine tool servos do not detect acceleration spikes and force a feed rate reduction. The return moves between trochoidal passes should have increased feed rate and a small lift to avoid rubbing and recutting previously cut regions.”
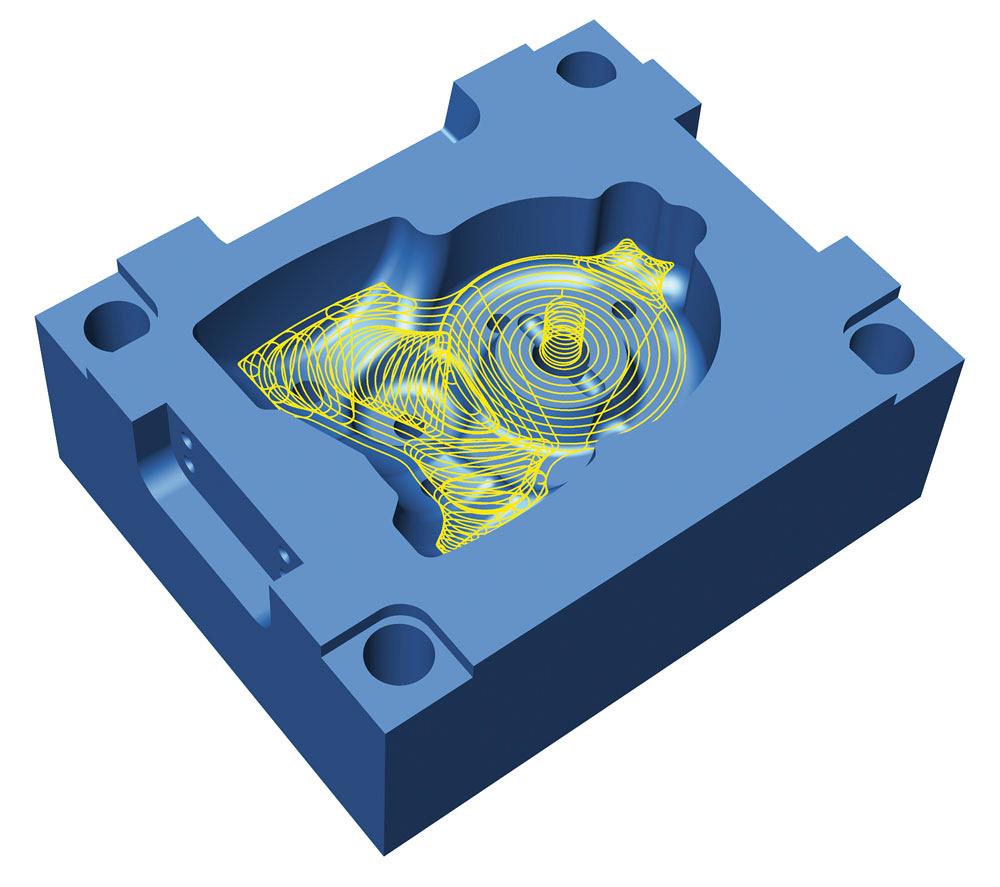
The path of a new 3-D roughing strategy is shown in yellow in a cavity. Illustration courtesy of Open Mind Technologies.
For the corners, Levine said, advanced roughing should combine a variable engagement with changes to feed rate and spindle speed to ensure a constant cutting load. A properly implemented advanced roughing technique will reduce cutting time by 50 to 70 per cent compared to traditional techniques, and it can increase cutter life by approximately a factor of three.
Multi-purpose Tools
HEM can be a more economical way to machine when the right variables—machine, software, and tooling—are present. One tool can be used to produce various groove widths and corner radii.
“Due to the small RDOC producing smaller side loads on the tool, it is possible to take a deep ADOC with the tools, using the entire flute length. Using the full cutting edge of the tool is more economical than using only the tip of the tool,” said Pollock.
“A large- diameter tool is not needed to create deep pockets. A small-diameter tool using a dynamic milling strategy can remove the same amount of material as a large tool using a traditional slotting strategy. The same work can be done with a less expensive tool,” said Pollock. “Producing less side load allows using a smaller tool at deeper depths of cut, but it also means that less machine and workpiece setup rigidity are required. In theory, the same parts could be produced on a smaller spindle with less machine horsepower.”
End Mill Characteristics
Tools specifically designed for HEM have some special characteristics that help them produce for up to two or three times longer than standard tooling used in a standard milling process. Their longevity is largely accredited to the fact that less heat is generated because the flute is engaged with the material a shorter amount of time. The heat that is produced is directed to the chip rather than the tool. As a rule of thumb, many flutes and chip cutters are good tooling characteristics for HEM.
Pollock said, “The tools normally contain a high number of teeth or cutting edges. Since deep depths of cut are achieved by this strategy, long lengths of cut are also incorporated into the cutting tools.
“The light RDOC produces a very short chip in the radial direction due to the chip thinning, but since we are taking advantage of deep depths of cut, the chip in the axial direction can be very long and tend to cling, making chip evacuation more difficult. Chip splitters or chipbreakers along the cutting edge can solve the problem.”
Doiron said, “Many of today’s end mills are specifically designed to handle such machining—for example, our trochoidal end mill line. These tools use the full range of the flute length, cutting in circular patterns, peeling material in a climb cut direction, and pushing chips away from the tool. Tools that are 4XD in length can have problems evacuating long chips that can get entangled and packed into the tool, causing tool failure. To avert this problem, our trochoidal tools feature a chipbreaker designed in a staggered pattern that enables the tool to break the chips in shorter segments. This makes it easier to flush out the chips and still provide an excellent finish.
“Feed rates can be faster because the tool, being fully engaged in a side milling position, is stable. Cutting forces are consistent throughout the flute length, and the tool is designed with a variable helix along with irregular flute spacing, which reduces vibration.”
Typically Advantageous
Alternative toolpaths can be applied to most milling processes as long as the equipment can accommodate the faster speeds and read the process program quickly, but for some types of jobs, the advantages and savings may not be as dramatic as for others.
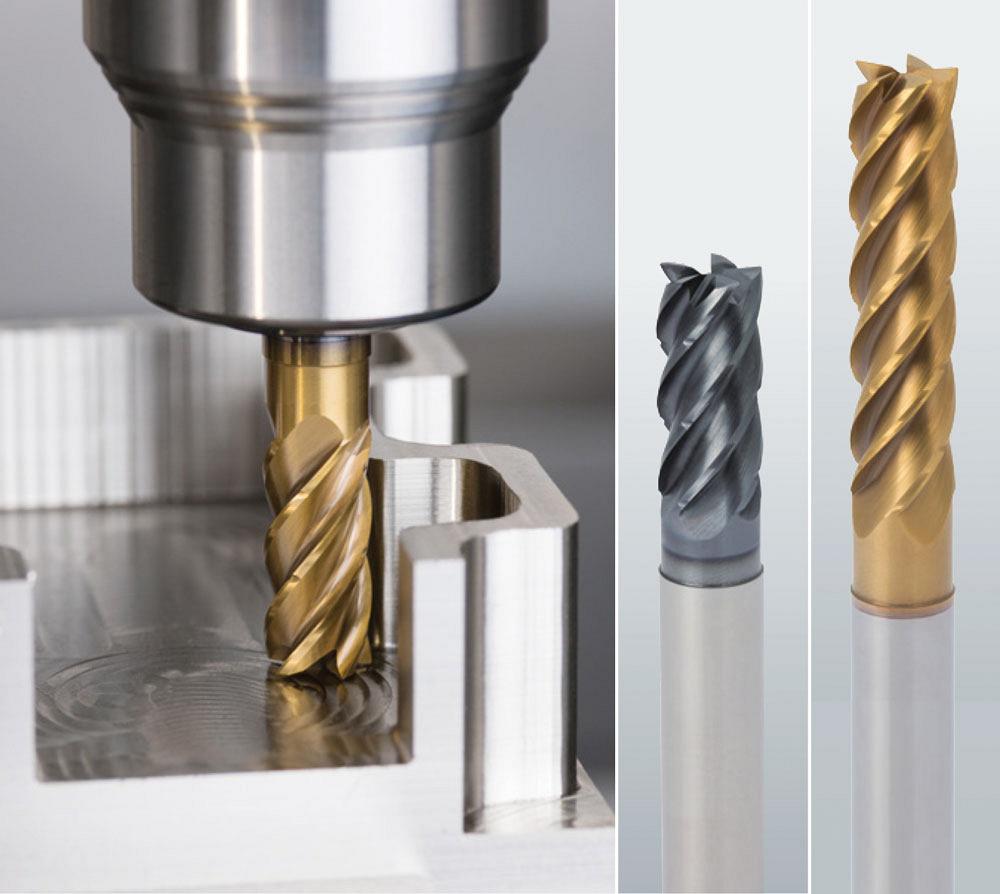
Trochoidal end mills can be fully engaged in a side milling position, adding to the stability of the process. Photo courtesy of Emuge Corp.
“There are no hard and fast rules for using advanced roughing,” said Doiron. “It is up to the user, the equipment, and the application. One needs to evaluate the specific needs--perhaps conduct a time study on a conventional CAM system using a traditional pocket mill and compare it to an advanced milling scenario. The results of the time calculated by the CAM systems can provide an accurate time difference between the two.”
Pollock said that shallow pockets or depths of cut bring the production closer to standard slotting since the full-length-of-cut machining cannot be used and some materials, such as aluminum, are already machined at such high surface footage that the productivity is already close to that of dynamic milling.
“One of the most important reasons to use dynamic milling,” Pollock said, “is process reliability or security. Because of only using light radial engagement of the tool, and a program maintaining a constant TEA, the tool is never in a situation where there is a chance of becoming over-engaged or at risk of packing chips. The machining condition stays consistent, which provides for consistent tool life and very little risk of having a crash or tool breakage situation.”
Emuge Corp., www.emuge.com
Open Mind Technologies, www.openmind-tech.com
Walter USA LLC, www.walter-tools.com
About the Author
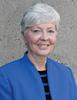
Sue Roberts
2135 Point Blvd
Elgin, IL 60123
815-227-8241
Sue Roberts, associate editor, contributes to both Canadian Metalworking and Canadian Fabricating & Welding. A metalworking industry veteran, she has contributed to marketing communications efforts and written B2B articles for the metal forming and fabricating, agriculture, food, financial, and regional tourism industries.
Roberts is a Northern Illinois University journalism graduate.
subscribe now
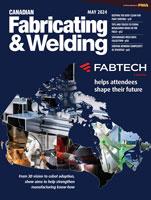
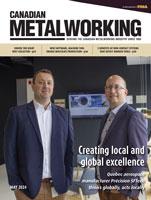
Keep up to date with the latest news, events, and technology for all things metal from our pair of monthly magazines written specifically for Canadian manufacturers!
Start Your Free Subscription- Industry Events
Automate 2024
- May 6 - 9, 2024
- Chicago, IL
ANCA Open House
- May 7 - 8, 2024
- Wixom, MI
17th annual Joint Open House
- May 8 - 9, 2024
- Oakville and Mississauga, ON Canada
MME Saskatoon
- May 28, 2024
- Saskatoon, SK Canada
CME's Health & Safety Symposium for Manufacturers
- May 29, 2024
- Mississauga, ON Canada