- FMA
- The Fabricator
- FABTECH
- Canadian Metalworking
Technology Spotlight: Toolholding system
Taper-to-taper toolholding simplifies operator training
- July 5, 2023
- Article
- Cutting Tools
Of all the post-pandemic challenges facing the manufacturing industry, employee recruitment and retention remains at the top of the list. Frankly, finding and replacing good operators is difficult in the current market.
Thankfully, technology can fill in some of the gaps.
A part’s quality and cycle time depend on a proper and efficient tooling setup. Excessive runout, premature tool wear, and in a worst case, tool crashes and scrapping parts all can be caused by improper tool setup. In today’s manufacturing environment, the time to train an operator on efficient, correct toolholder setup is at a premium.
Some machines, such as Swiss-style lathes and multitasking machines take long periods to setup and retool, even with experienced operators at the helm.
Technologies like taper-to-taper toolholding systems ease the learning curve to get new employees up to speed quickly.
Removing Guesswork
Instead of needing a bench full of collets, wrenches, and nuts that require proper assembly for hydraulic-based toolholding systems or dealing with the heat, fumes, and cooling units required for shrink-fit-type systems, taper-to-taper systems consist of three basic components: holders, collets, and a press-fit assembly mounting unit.
Those three together form the REGO-FIX powRgrip system.
Mounting units are available in manual or automatic configurations, but both operate using the same taper-to-taper design with hydraulic press-fit. The collets have tapers that perfectly match the internal tapers of the holders.
To set up the tooling, operators only need to select and load the die that fits the holder, and the pre-fit assembly unit automatically applies the correct pressure (up to 9 tons) to properly hold the tool. Tool changeouts can be done in as little as 10 seconds, the company states. Tools are immediately ready for handling, and operator safety is ensured by the unit’s interlocked doors that enclose the assembly area during press-in and removal.
Tool length settings can be adjusted during setup with a Z-level adjustment screw on the system’s collet. The screw is manipulated with an adjustment tool from a standard presetter and has repeatability within 10 m. The automatic press unit plugs into standard wall receptacles, which makes it portable.
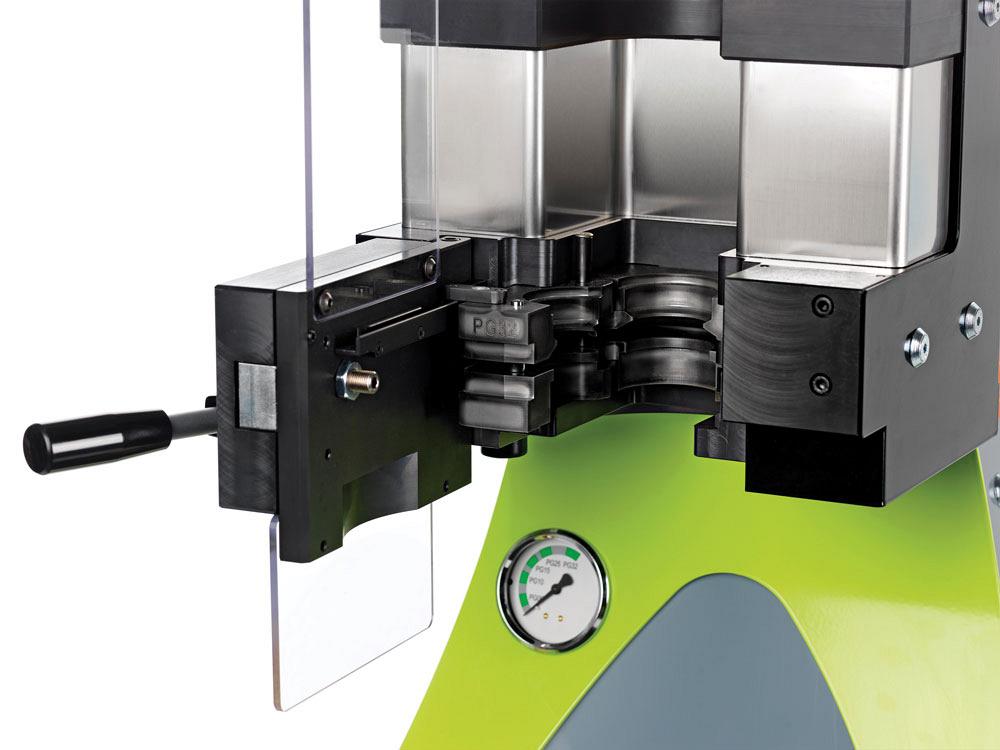
To set up the tooling, operators only need to select and load the die that fits the holder, and the pre-fit assembly unit automatically applies the correct pressure to properly hold the tool.
In many shops, taper-to-taper tooholding systems can help reduce the amount of training operators need. Machinists simply load a holder into a die, insert the collet into the assembly unit, and the changeover is made. According to the manufacturer, in some applications, it can be learned in less than an hour. As a result, even inexperienced operators can quickly and correctly set up tooling while significantly reducing setup times to keep machines running efficiently and profitably.
Performance
This toolholding system applies up to 1,100 nm of clamping torque and is designed to reduce vibration. It maintains a total indicated runout (TIR) of less than 0.0001 in. through five years or 20,000 cycles with no erosion of impregnated surface treatment, the company states.
This system’s holders accommodate tool diameters from 0.2 mm to 25 mm and 1/16 to 1 in. and hold any collet diameter in metric and standard units within that specified range. It also works with all standard taper types, such as BT, CAT, HSK, and Capto, as well as standard forms, sizes, and gauge lengths.
Swiss-style Turning
Applications that turn slender, delicate, and complex parts on live-tool Swiss-style machines often can take hours to set up and retool. However, the lion’s share of steps required in the time-consuming and tedious process of setting up, reloading, and touching off new cutting tools on a Swiss lathe are eliminated with this toolholding system.
SwissQuick adapter holders provide a rigid ER-to-ER reduction with a larger ER body at the rear that remains in the machine, allowing operators to install a new cutting tool into the turret in seconds without removing the entire live head. Fine-thread and coarse-thread options are available with solid ER connections ranging from ER11 to ER25. Runout inside taper to outside taper is less than 0.0001 in.
In combination, the two systems allow operators to bench set and measure their tools for the next job while the machine is running. To retool the machine turret, the operator simply threads in the new tool without the necessity of removing the entire toolholder from the turret. Retooling is reduced to minutes with benefits that include nominal TIR, good repeatability, high tool rigidity, and vibration damping.
An Ongoing Challenge
Indications are that workforce challenges will not ease in the foreseeable future, forcing manufacturers to evaluate systems and technology for the most efficient use of their personnel. Applications and technologies like taper-to-taper toolholding systems that can streamline training and learning while increasing employee productivity are where shops will need to focus to meet the challenge and maintain profitability.
REGO-FIX, www.rego-fix.com
Related Companies
subscribe now
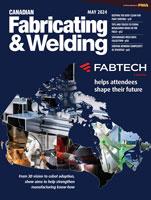
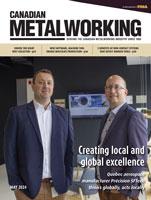
Keep up to date with the latest news, events, and technology for all things metal from our pair of monthly magazines written specifically for Canadian manufacturers!
Start Your Free Subscription- Industry Events
Automate 2024
- May 6 - 9, 2024
- Chicago, IL
ANCA Open House
- May 7 - 8, 2024
- Wixom, MI
17th annual Joint Open House
- May 8 - 9, 2024
- Oakville and Mississauga, ON Canada
MME Saskatoon
- May 28, 2024
- Saskatoon, SK Canada
CME's Health & Safety Symposium for Manufacturers
- May 29, 2024
- Mississauga, ON Canada