Technical Advisor
- FMA
- The Fabricator
- FABTECH
- Canadian Metalworking
Technology Spotlight: Tools for small diameters
Indexable tools challenge solid carbide for creating small holes
- By Andrei Petrilin
- July 17, 2018
- Article
- Cutting Tools
Rotating, one-piece, solid-carbide tools traditionally dominate the market for creating holes with diameters up to 20 mm. Indexable tool manufacturers have not traditionally been successful in penetrating this stronghold.
Several important factors contribute to the historical perception that solid-carbide tools are a better bet for tooling reliability in these situations.
Solid-carbide tool accuracy compares favorably with that of indexable tools, particularly for small-diameter end mills and for tools with diameters beyond the range. However, the role of reduced accuracy for tools of small diameter (for example, a milling cutter’s radial runout) increases in significance as a factor affecting tool life.
An indexable tool comprises a tool body; replaceable inserts; and mechanical parts such as clamping screws and wedges, which secure the inserts in the body. Decreasing the tool diameter necessitates reducing dimensions of the assembly components. Reducing the size of the securing elements weakens their strength, and the tool becomes unable to withstand cutting loads using normal machining data.
This seriously limits the tool application, and any further decrease may cause degradation of the entire assembly structure.
The prices of small, rotating tools often are high, which adds to the perceived limitations of indexable tools in the small-diameter range.
The indexable option
Indexable tools possess several distinct advantages. In many cases, especially in rough machining, changing a worn cutting edge by simply indexing it provides economic benefits compared with having to replace a whole life-expired solid tool with a new tool. In addition, there is no need to use up time and resources on regrinding and recoating worn-out, one-piece cutters.
Tool manufacturers have made significant progress in developing reliable indexable products that can be commercially viable in small diameters. Work in this direction has shown results already, and assembled mills and drills with interchangeable cutting heads are proving to be a realistic alternative to solid-carbide tools.
Competitive performance
The introduction of tools with replaceable solid-carbide cutting heads signifies a change in focus. Two examples of this concept are Iscar’s Multi-Master milling line and the ChamDrill drilling tools.
Performance and accuracy characteristics have positioned the new tools to be functionally competitive with solid-carbide designs. Versatility of these lines, in which a head can be mounted in different bodies and vice versa, a single body can carry different heads, facilitates various assembly combinations and contributes to reducing items in tool stock.
Another important design approach of these lines is that a worn-out head does not require spending time on setting up a new tool and can be replaced while the tool is still clamped in the machine tool spindle. This reduces non-cutting time and, consequently, reduces production costs. In contrast, replacing a worn-out, solid-carbide mill or drill inevitably leads to a new setup procedure.
In addition, the concept ensures sustainable use of cemented carbide with all the associated advantages. The principle of indexable carbide tools has distinct merits and features strongly in tool design within the diameter range that is under discussion here.
The minimum diameter of Multi-Master milling heads, for example, is 5 mm and that of SumoCham drilling heads is 6 mm, while the Multi-Master combined countersink heads for centre drilling havee a 1 mm dia.
Small change, large impact
Is a 1-mm change in size a lot or a little? For indexable tools in the small-diameter range, it makes a noticeable difference. The new SumoCham 5-mm-dia. drilling head represents an important step in expanding the application fields of indexable drills (see Figure 1).
Within the small-diameter range, indexable tools can offer precision and performance advantages that position them competitively against the more traditional solid-carbide tools.
The LOGIQ factor
Iscar recently introduced a new range of small indexable rotating tools under its new LOGIQ line campaign. The company proposes several families of cutters with a nominal diameter of up to 20 mm.
These indexable milling cutters within the diameter range of 8 to 16 mm attract the most interest. They have common features, including the fact that the cutters carry triangular-shaped inserts with three cutting edges and the mechanical part of the setup that secures the inserts is a screw.
These families are intended for milling square shoulders or fast-feed (high-feed) milling.
But here the similarity ends, and the difference begins.
While the design of the Heli3Mill and Micro3Feed families for tool diameters of 10 to 16 mm is committed to the classical principle of insert securing by clamping screw through the central hole of an insert, the NanMill and NanFeed families for tool diameters of 8-10 mm have adopted another concept.
Within such a small diameter range, the central clamping screw, as noted previously, does not provide acceptable holding. In the new design, the screw is located above the insert, and the screw head plays the role of a wedge (see Figure 2). This approach provides reliable and rigid clamping, ensures a durable homogeneous insert structure with no hole, and allows insert indexing to be quick and simple.
It is predicted that these new families will be particularly effective in manufacturing compact parts and in machining small cavities, pockets, and small parts used in industrial sectors such as die and mouldmaking, as well as in producing miniature components.
About the Author
Andrei Petrilin
2100 Bristol Circle
Oakville, L6H 5R3 Canada
905-829-9000
Related Companies
subscribe now
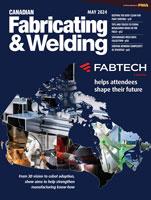
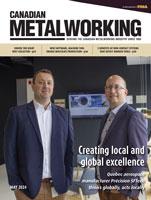
Keep up to date with the latest news, events, and technology for all things metal from our pair of monthly magazines written specifically for Canadian manufacturers!
Start Your Free Subscription- Industry Events
MME Saskatoon
- May 28, 2024
- Saskatoon, SK Canada
CME's Health & Safety Symposium for Manufacturers
- May 29, 2024
- Mississauga, ON Canada
DiPaolo Machine Tools Open House 2024
- June 4 - 5, 2024
- Mississauga, ON Canada
FABTECH Canada
- June 11 - 13, 2024
- Toronto, ON Canada
Zoller Open House & Technology Days 2024
- June 12 - 13, 2024
- Ann Arbor, MI