- FMA
- The Fabricator
- FABTECH
- Canadian Metalworking
Technology Spotlight: Vibration-free boring tools
Anti-chatter technology produces better, quieter boring
- By Canadian Metalworking
- February 18, 2019
- Article
- Cutting Tools
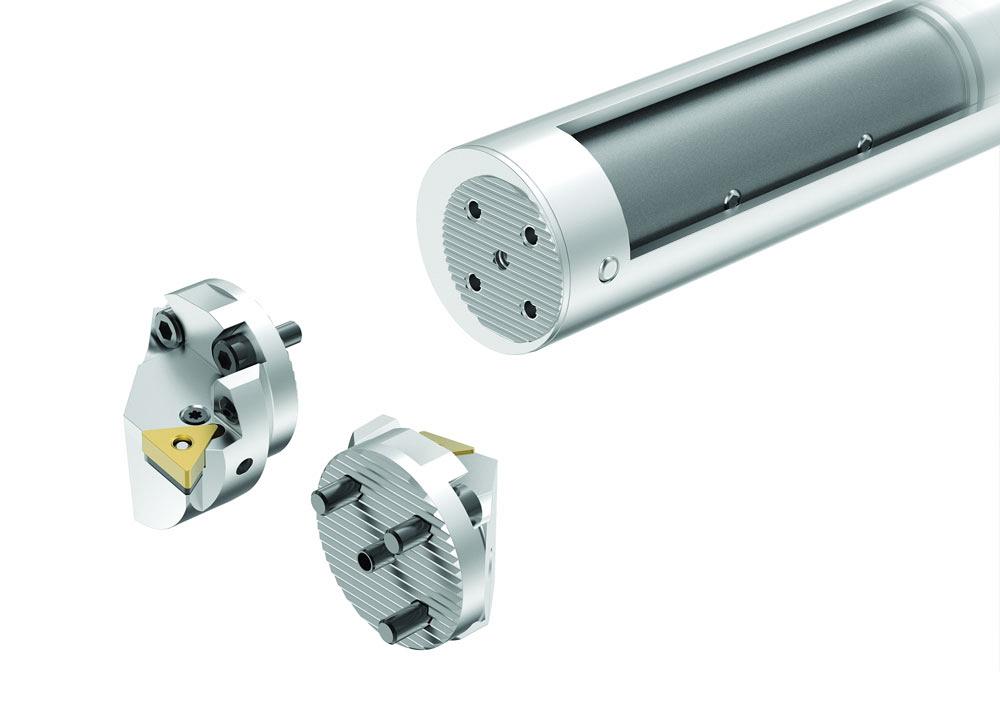
Kennametal’s new vibration-free boring system features interchangeable heads that include screw-on and lever-style clamping mechanisms in positive- and negative-rake configurations.
It’s a sound that every machinist dreads: the high-pitch whine of a deep-boring operation complete with chatter loud enough to seep through even the best earplugs.
It’s a problem that plagues many machine shops that produce long, deep holes, and it only gets worse in materials that are tough and more difficult to machine.
To battle the vibration of deep boring, which can cause drifting, out-of-round holes, and poor surface quality, tooling supplier Kennametal has introduced a new boring system with a new anti-chatter mechanism and numerous indexable heads and shank sizes.
This vibration-free boring system also is essentially plug-and-play with an array of interchangeable heads, including screw-on and lever-style clamping mechanisms in positive- and negative-rake configurations.
Vibration-free cutting
Sam Eichelberger, Kennametal product engineer for lathe systems engineering, is part of the team that developed the tool’s internal dampening mechanism.
“Perhaps the most important thing to know about the new bar is that it’s plug-and-play,” said Eichelberger. “There's no need whatsoever for tuning or adjustments; you simply pull it out of the package, mount it in the turret, and get boring.”
There’s more to the story than making the shop a quieter place to work, however. Eliminating vibration and therefore chatter extends tool life and improves surface finish. And when tools last longer, they can be pushed harder, increasing feed rates, cutting speeds, and depths of cut.
The anti-chatter boring bars have a serrated, bolt-on connection at the front of the bar that securely clamps a variety of styles and sizes of indexable heads.
The heads themselves for this tool also have changed and now are shorter and lighter. This helps provide greater stability, contributing to the bar’s improved performance, the company states. They’re also coolant-fed, precisely directing a stream of high-pressure coolant where it’s needed most. The result is improved chip control together with maximum cooling in the cutting zone.
The inner works
None of the changes matter much without the most important feature of them all: the internal dampener.
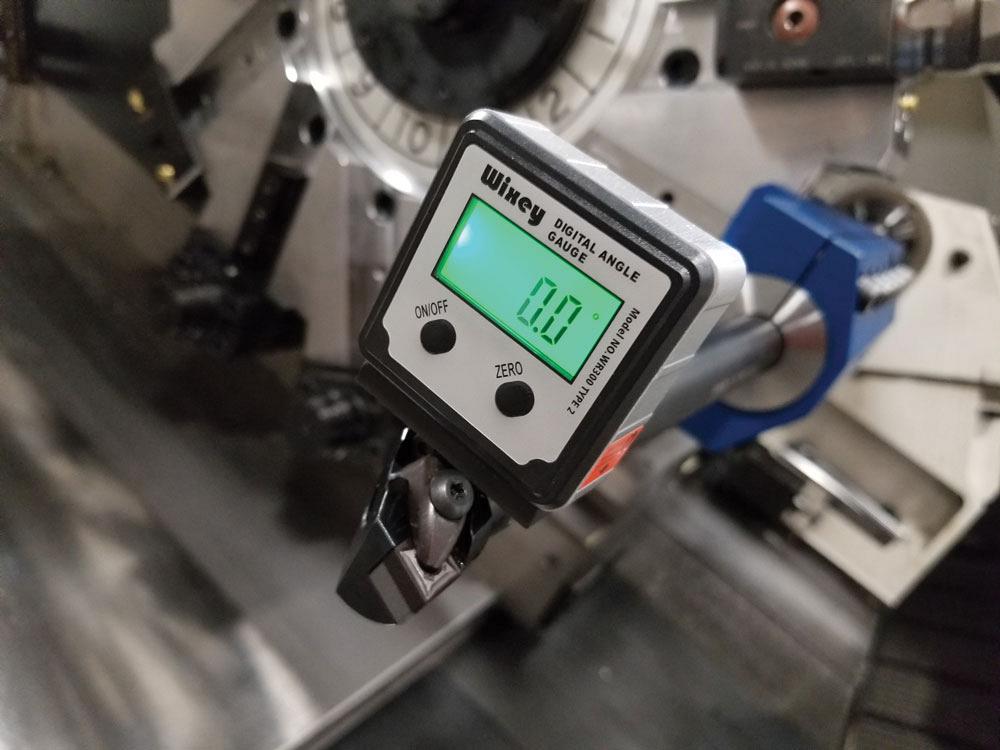
Setting the head exactly on centreline is accomplished by bringing the angle finder display to zero and locking the bar in place.
“The bars are both vibration- and maintenance-free. Within the bar there sits a mass that's supported by a pair of elastic supports, inside of which sits a dampening fluid. This mass vibrates at a predetermined frequency during machining, attenuating the natural frequency of the bar around it to suppress vibration. There are no wear components to worry about [and] no tuning,” said Eichelberger.
Setting the head exactly on centreline is accomplished by bringing the angle finder to zero and then locking the bar in place.
The vibration-free system has been shown to offer better boring performance in applications up to 10xD, explained Eichelberger, which is much deeper than solid-carbide or heavy metal boring bars are capable.
Setup important for stability
Of course, boring bars are only as good as the method by which they’re clamped in the machine.
The manufacturer has addressed this critical consideration by supplying machine-specific turret adapters, along with a special split sleeve bushing for maximum rigidity.
“That’s the goal of this product,” said Kennametal Global Product Manager John Gable. “The greatest stability possible and the most effective dampening solution available, period.”
Anyone who’s ever struggled to get a boring bar exactly on centre will appreciate the fact that setup has been simplified.
“There’s a reference flat on the top of the head that accommodates a visual angle finder,” Eichelberger said. “You just rotate the bar until the indicator reads zero, then clamp it in place.”
Considering the higher cost of such a boring system, it’s important that heads can be replaced in the event of a crash, avoiding damage to the bar itself. And users of the company’s older boring system will find that their new heads fit with the use of an adapter.
“The portfolio for our imperial bars ranges from 1 inches in diameter up to four in., while the metric version starts at 25 mm and goes to 100 mm,” Gable said. “There are a variety of interchangeable head styles available as well, everything from screw-on, positive-rake inserts for fine-finishing needs to negative-rake, clamp-style geometries for heavy roughing.”
Kennametal Inc., 1600 Technology Way, Latrobe, PA 15650, www.kennametal.com.
About the Author
Related Companies
subscribe now
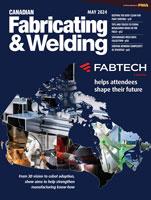
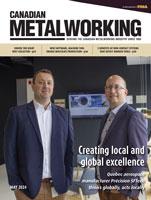
Keep up to date with the latest news, events, and technology for all things metal from our pair of monthly magazines written specifically for Canadian manufacturers!
Start Your Free Subscription- Trending Articles
Sustainability Analyzer Tool helps users measure and reduce carbon footprint
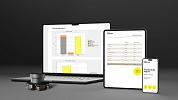
Mitutoyo updates its end-user portal
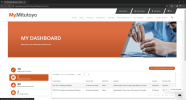
Enhance surface finish with high-speed machining
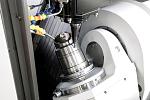
Equispheres secures $20 million investment round
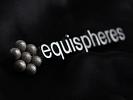
Solid carbide drills produce precision holes in short chipping materials
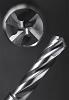
- Industry Events
Automate 2024
- May 6 - 9, 2024
- Chicago, IL
ANCA Open House
- May 7 - 8, 2024
- Wixom, MI
17th annual Joint Open House
- May 8 - 9, 2024
- Oakville and Mississauga, ON Canada
MME Saskatoon
- May 28, 2024
- Saskatoon, SK Canada
CME's Health & Safety Symposium for Manufacturers
- May 29, 2024
- Mississauga, ON Canada