- FMA
- The Fabricator
- FABTECH
- Canadian Metalworking
The need for speed
When machining many parts at high speed, cutting parameters are crucial.
- By Canadian Metalworking
- November 19, 2014
- Article
- Cutting Tools
Productivity in milling
Productivity in milling, when defined as metal removal rate, Q cm³/min, can be optimized in many different ways. Choosing the right tool for the application is important, but the choice of cutting parameters is equally critical. The seven examples below show how cutting data can be increased above normal recommendations and contribute to a higher productivity.
- Face milling – High cutting speed, vc . In machining aluminium, and sometimes in machining cast iron with CBN or ceramic inserts, cutting speeds of more than 1000 m/min can be used, which results in a very high table feed, vf. Also, this type of machining can be called High Speed Machining (HSM).
- Peripheral milling – High cutting speed, vc, and feed, fz. When the cutter has a small radial depth of cut, ae, the time in cut per rev. is short, consequently the cutting edge temperature will be low. This means that the cutting speed can be raised above normal recommendations. Also, the feed, fz, can be increased, because the maximum chip thickness, hex, will be low. The feed will be limited by the surface finish requirement.
- Profile milling – High spindle speed, n. This milling technique is often called High Speed Machining (HSM) and is typical in finishing or super-finishing profiling operations with a ball nose end mill.
- Face milling with small entering angle and high feed, fz. Cutters with very small entering angles enable a dramatic increase in the feed, fz, due to the chip thinning effect
when ap is small.
- Heavy duty milling – large depth of cut – heavy duty In heavy duty applications, large insert cutters with large diameters are used. Cutting speed is normal, but high ap and fz, combined with a large ae, make it very productive.
- Finishing with wiper inserts. In a finishing operation with a large face milling cutter, the feed, fz, normally has to be kept low. However, by using wiper inserts in the cutter, the feed can be raised 2–3 times without sacrificing the surface quality.
- Face milling – extra close pitch cutter In milling short-chipping materials, like grey cast iron, a face milling cutter with an extra close pitch can be used, resulting in high table feed. Also, in HRSA material where cutting speed is normally low, an extra close pitch results in a high table feed.
NOTE: “Light and fast” technique: Methods 2, 3 and 4 are based upon small depth of cut, ae, and/or ap, which generate low cutting forces and heat, making it possible to increase speed and/or feed.
The Milling Process
[gallery type="slideshow" link="none" ids="107018,107016"]
Cutting speed – vc (m/min)
This indicates the surface speed at diameter and forms a basic value for calculating cutting data.
Recommended cutting speeds for all materials and for different hex values are available in the Main catalogue.
Effective or true cutting speed
Indicates the surface speed at the effective diameter (Dcap). This value is necessary for determining the true cutting data at the actual depth of cut (ap). This is a particularly important value when using round insert cutters, ball nose end mills and all cutters with larger corner radii, as well as cutters with an entering angle smaller than 90 degrees.
Spindle speed – n (rpm)
The number of revolutions the milling tool makes per minute on the spindle. This is a machine oriented value, which is calculated from the recommended cutting speed value for an operation.
Feed per tooth – fz (mm/tooth)
A basic value for calculating cutting data, such as table feed. It is also calculated with consideration of maximum chip thickness (hex) and entering angle.
Feed per revolution – fn (mm/rev)
Auxiliary value indicating how far the tool moves during one complete rotation.
It is used specifically for feed calculations and often to determine the finishing capability of a cutter.
Feed per minute – vƒ (mm/min)
The table feed, machine feed or feed speed in mm/min it represents the movement of the tool in relation to the workpiece, dependent on feed per tooth (fz) and number of teeth in the cutter (zn).
Maximum chip thickness – hex (mm)
This value is a result of the cutter engagement as it is related to (fz), (ae) and (kr).
The chip thickness is an important consideration when deciding the feed per tooth, to ensure that the most productive table feed is employed.
Average chip thickness – hm (mm)
A useful value in determining the specific cutting force, used for net power calculations.
Metal removal rate – Q (cm³/min)
The volume of metal removed in cubic mm per minute. It is established using the values for cutting depth, width and feed.
Specific cutting force – kct (N/mm²)
A factor used for power calculations. The specific cutting force relates to the material resistance when cut at a specific chip thickness value.
Power Pc and efficiency – nmt
Machine tool oriented values, which assist in calculating the net power to ensure that the machine can handle the cutter and operation.
Machining time – Tc (min)
Machining length (lm) divided by the table feed (vf).
About the Author
subscribe now
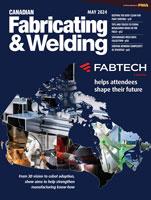
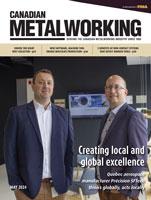
Keep up to date with the latest news, events, and technology for all things metal from our pair of monthly magazines written specifically for Canadian manufacturers!
Start Your Free Subscription- Industry Events
Automate 2024
- May 6 - 9, 2024
- Chicago, IL
ANCA Open House
- May 7 - 8, 2024
- Wixom, MI
17th annual Joint Open House
- May 8 - 9, 2024
- Oakville and Mississauga, ON Canada
MME Saskatoon
- May 28, 2024
- Saskatoon, SK Canada
CME's Health & Safety Symposium for Manufacturers
- May 29, 2024
- Mississauga, ON Canada