- FMA
- The Fabricator
- FABTECH
- Canadian Metalworking
Unique thread form taps for high volume CNC production
Spiralock thread form has been used in extreme fastening applications.
- By Canadian Metalworking
- November 3, 2014
- Article
- Cutting Tools
Machinists can now add a locking feature to tapped holes by utilizing specialized Spiralock taps. These taps are based on a unique thread form that resolves the thread loosening and joint integrity problems common to standard fasteners.
The Spiralock thread form has been used in extreme fastening applications where joint failure or loosening is not an option: from the main engines of NASA’s Space Shuttle, the Saturn Cassini orbiter and Titan Huygens probe to deep sea oil rigs, military and aerospace vehicles, as well as medical implants, artificial limbs, and heart pumps.
In traditional 60-degree threads, the gap between the upper edges of the male and female threads can lead to vibration-caused thread loosening.
Stress concentration and fatigue at the first few engaged threads is also a problem, particularly with softer metals. The profile of Spiralock threads closes the gap that causes loosening, improving the integrity and reliability of threaded joints.
“Compared to other machining operations, thread form tapping has been relatively slow,” says Jeff Jungmann, a Spiralock engineering manager.
“The entire cut has to be made in one pass with little to no visibility, so most machinists are very conservative about their speeds.”
The Spiralock product line of machine taps have been improved for CNC machining in regards to the tool’s geometry, surface coatings, flute angles as well as shapes, nose size and other key factors.
The new thread form taps include four styles: Multi-Purpose, T-10 Straight Flute, Cold Forming, and High Performance, of which all but the Cold Forming include a physical vapor deposition (PVD) coating.

Spiralock’s upgraded cold forming taps produce a thread by deforming material instead of removing it. It is ideal for aluminium, brass, copper and mild steels.
Tap blanks include a neck behind the threads on most sizes. The neck allows more room for coolant to get into the hole being tapped, and more room for chips to get cleared away from outside a blind hole. This decreases heat buildup and further increases wear life.
The four tap styles are offered in plug chamfer for through holes or a bottom chamfer for bottom holes.
Minor changes to flute shape have also improved tap usability across a broader range of materials for each style. For instance, hook, rake, and spiral point angles are tailored to specific purposes corresponding to each tap style.
Since the point diameter at the front of all tap styles is now larger, the taps start cutting material sooner and spread the load more evenly over all the cutting edges, improving wear life.
“By improving the quality of the tapping tool, machinists can now have the confidence they are making the proper cut without having to be as conservative in their speeds,” says Jungmann.
For information, visit www.StanleyEngineeredFastening.com.
About the Author
subscribe now
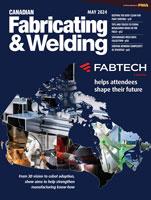
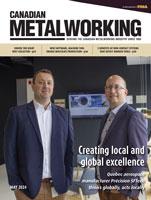
Keep up to date with the latest news, events, and technology for all things metal from our pair of monthly magazines written specifically for Canadian manufacturers!
Start Your Free Subscription- Industry Events
Automate 2024
- May 6 - 9, 2024
- Chicago, IL
ANCA Open House
- May 7 - 8, 2024
- Wixom, MI
17th annual Joint Open House
- May 8 - 9, 2024
- Oakville and Mississauga, ON Canada
MME Saskatoon
- May 28, 2024
- Saskatoon, SK Canada
CME's Health & Safety Symposium for Manufacturers
- May 29, 2024
- Mississauga, ON Canada