Associate Editor
- FMA
- The Fabricator
- FABTECH
- Canadian Metalworking
What information is needed to develop a special tool?
Special or custom tools are designed based on an application and the manufacturing environment
- By Lindsay Luminoso
- October 23, 2023
- Article
- Cutting Tools
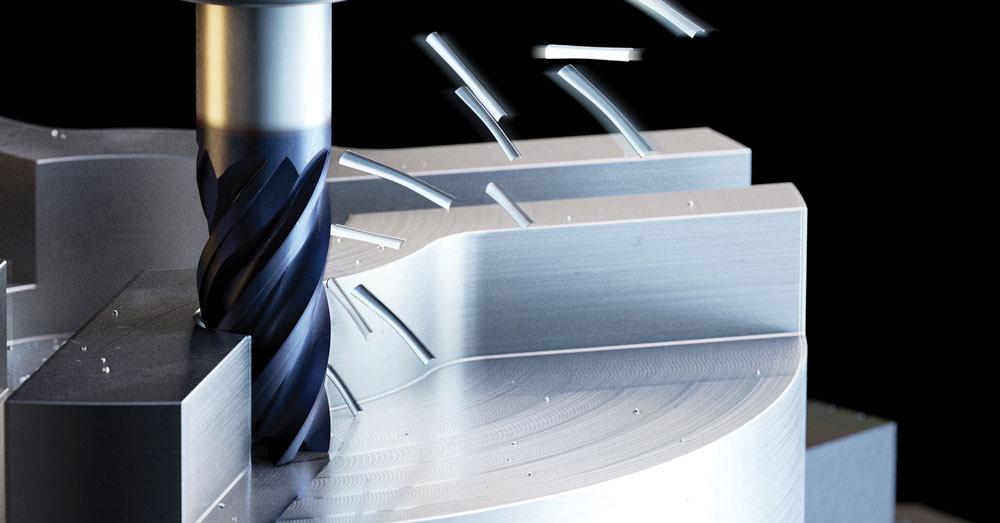
Today’s special tools can include custom geometries, like chipbreakers; a special edge prep; or a coating that is not found on the shelf. It all depends on the application, machining capabilities, and specifications. YG-1
In today’s competitive landscape, special tools are one way to help shops think outside of the box and push the boundaries of their existing capabilities. In many instances, shops leave a lot on the table because they are comfortable with how things have always been done or they are unfamiliar with the benefits of working with custom or special tooling. Partnering with a reputable and experienced tooling manufacturer can make all the difference during the development process.
Custom tools are not for everyone, but some applications demand them. Check out our Guide to Special Tools!
Special tools can provide significant production value and efficiency. But not all special tools make sense in the real world. Tool manufacturers use their expertise to provide users with the best possible option. A lot goes into making an effective special tool. Here are just a few things that help tooling manufacturers design the best special tool for any given application.
What Is Your Why?
Tooling manufacturers will often want to start with why? Why do you want to look at a special tool? The answer is going to vary depending on the work environment, but it will help determine the exact specifications needed.
“Are you looking for a tooling provider that will help you from the ground up on an application, with recommendations on what to use for a particular area that you're trying to machine?” said Lee Goad, technical supervisor, Horn, Franklin, Tenn. “Or are we trying to help you improve an existing process? Are we reducing scrap? Or has the surface finish changed, or are tight tolerances no longer being met? These are important questions to answer before we really start to dig in.”
What Type of Tool Will It Be?
There are varying degrees of special tools. Some special tools are as simple as taking a standard tool and modifying it with one or two special features to make it suit a specific need.
“In these instances, it can be as simple as adding a special edge prep or coating that is not found on the shelf,” said Yair Bruhis, global product and application manager, YG-1 USA, Vernon Hills, Ill. “These types of tools can take as little as five to six days to produce. Whereas a full special, where we are starting from scratch if we can get the blanks and materials needed, can take quite a bit longer, and that’s important to take into consideration.”
What Are The Machine or Equipment Capabilities?
One of the benefits of working with a special tool is that it can make up for some of the limitations of existing machine tools. For example, combining multiple operations in one tool means that there are fewer toolholder spots needed. Or, a shop working with a 3-axis machine can use special tools to reach features that would normally require a 5-axis. In theory, the sky is the limit. In practice, there are a number of constraints that need to be taken into account, especially when it comes to the machine the tools will be run on.
“We always ask the horsepower of the machine to make sure it can handle the necessary operations, especially if the tool performs multiple machine features at the same time,” said David Vetrecin, product manager, holemaking, ISCAR, Oakville, Ont.
The machine horsepower is especially significant when it comes to adding coatings.
“A lot of special geometries, as far as chipbreakers and what not, will have special coatings incorporated,” said Damon Wherry, technical design supervisor, Horn USA. “The horsepower of a machine will help it reach certain temperatures and heat to allow the coating to perform effectively.”
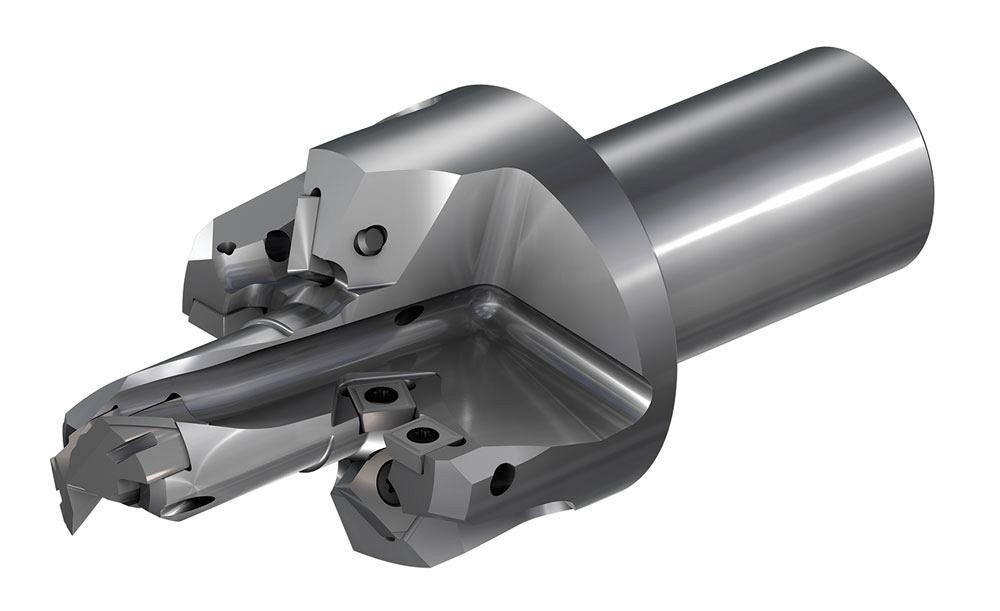
As ISCAR’s David Vetrecin explained, if a supplier is to create a tool that performs multiple steps at the same time, it needs to know if there will be enough coolant pressure to evacuate all the chips in the drilling application. ISCAR
Every machine, even if it is the exact same machine located in the same shop, will perform slightly differently. There are a lot of variables that influence the cutting actions.
“There are so many complex engineering relationships that go on inside the machine, and every machine has their own specific set of circumstances. It’s important for us to know exactly what we are dealing with to ensure that the nuances that we put into the geometries make sense,” said Jason Wells, president, Tech Hub, KYOCERA SGS Precision Tools, Danville, Va.
Can the machine handle a form? Can it handle a specific tolerance? These are just a few things that tooling suppliers will look at when designing a special tool.
What Is The Coolant Pressure?
Coolant type and pressure play a pivotal role when it comes to special tools, especially those that combine multiple operations in one tool.
“We need to know if the coolant pressure be enough to evacuate all the chips in a drilling application if we create a tool that performs multiple steps at the same time,” said Vetrecin.
Beyond coolant pressure and capacity, it’s important to know if the tool itself will require through-coolant. There are a number of different types of tools where through-coolant does not come standard, which means a special is needed.
“In some cases, when a special tool requires internal coolant, that can take much longer to produce, thus elongating the deliver process, which can be challenging for some,” said Bruhis. “This is an important consideration up front from both a design and delivery expectations. In some cases, adding through-coolant can take between two to eight weeks before we can get the tool to the user.”
What Workpiece Material Is Being Machined?
Workpiece material type is one of the most fundamental features that determine the type of tooling that can be used. Every material has different machining requirements.
“In order to pick the proper inserts and coatings, we need to know the exact application type and material being used,” said Vetrecin. “This will also help determine what type of material we use for the tool itself.”
What Processing Features Are Required?
Many shops have strong engineering departments and machine operators with the deep knowledge to know exactly what is needed and how it will function. But that’s not always the case, and tooling manufacturers can help with this expertise.
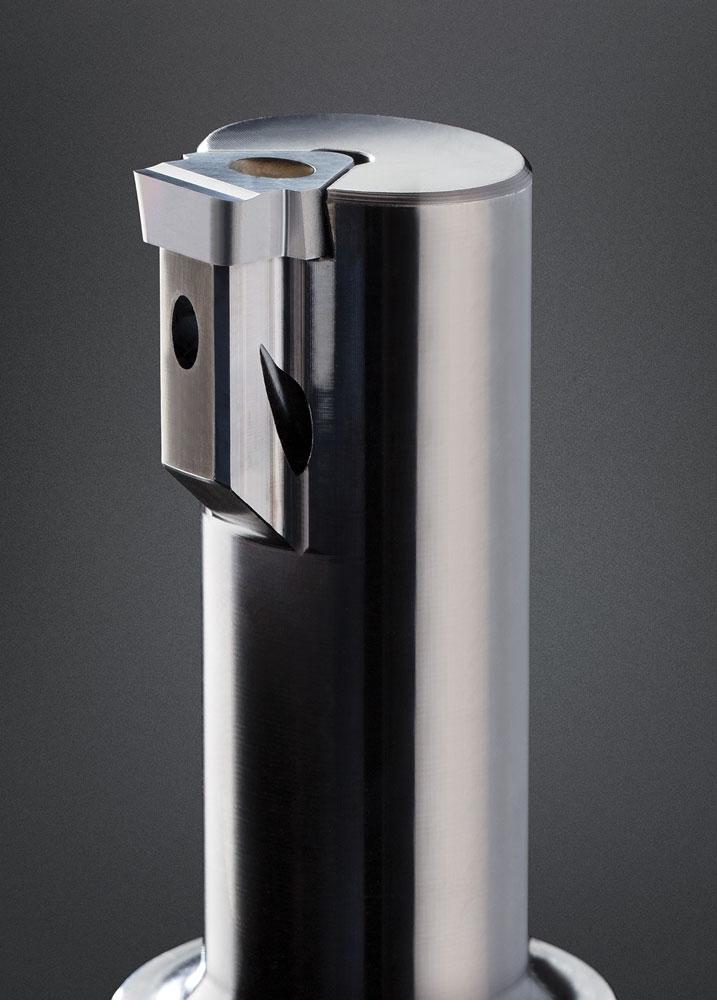
Made-to-order widths, shapes, forms, support, and coolant are just some of the ways Horn can customize a tool. Horn
“When we designed the tool, we actually design the part to make sure it looks good going in the part, flip it around, look for clearance issues and things like that,” said Goad. “We can actually send screenshots of how we intend for this tool to work. Programming wise, we can provide a STEP file where the user can plug it into their CAM software to help them use the tool effectively.”
Is a Drawing Available?
There are some instances where a shop will have certain expectations top of mind, but they don’t always necessarily translate to reality or the application.
“It can be incredibly helpful if we can get a drawing of the part, or if not the whole part, because of confidentiality or control issues, a drawing or a rendering of the feature to machine so that we can better understand all aspects of the process,” said Wells. “We sometimes run into situations where people tell us one thing, and we design a tool based on the information, and then all of a sudden it doesn’t work or we didn't realize that the tool had to reach around feature to get to another feature, or there was a cross hole that was going to create an interruption that we didn’t except.”
Looking at the entire component and all aspects of the machining process will give tooling manufacturers a clear view of any potential obstacles or challenges.
Are There Any Other Special Considerations?
Beyond the machining environment, part features and specifications, and operations needed, there are a few other things to consider.
“A lot of special tools require NDAs [non-disclosure agreements] because they are being used for military of aerospace applications,” said Bruhis. “In certain instances, especially in military applications, this may mean that we cannot work with certain suppliers in certain countries for our materials. This is extremely important to integrate into the design and quoting process. These restrictions can also add extra delivery time to the process, as sourcing materials becomes more difficult.”
Choosing a tooling supplier with experience in working with special considerations will help smooth the process and provide favorable results.
Associate Editor Lindsay Luminoso can be reached at lluminoso@fmamfg.org.
Horn, www.hornusa.com
ISCAR Cutting Tools, www.iscar.com
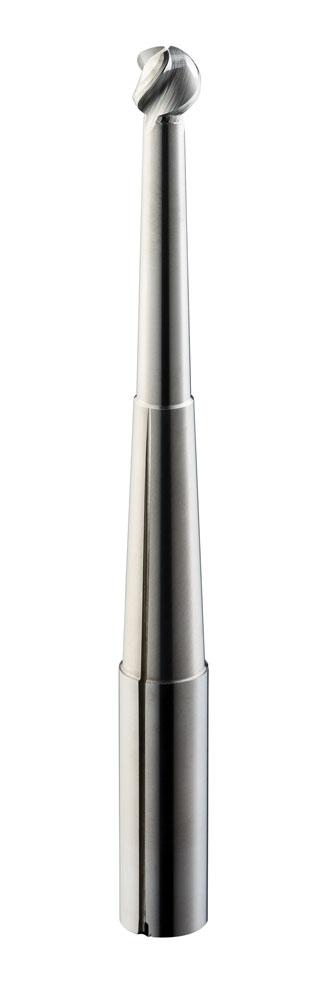
There are varying degrees of special tools. Some special tools are as simple as taking a standard tool and modifying it with one or two special features to make it suit a specific need. Kyocera SGS
Kyocera SGS Precision Tools, www.kyocera-sgstool.com
YG-1, www.yg1.ca
About the Author
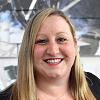
Lindsay Luminoso
1154 Warden Avenue
Toronto, M1R 0A1 Canada
Lindsay Luminoso, associate editor, contributes to both Canadian Metalworking and Canadian Fabricating & Welding. She worked as an associate editor/web editor, at Canadian Metalworking from 2014-2016 and was most recently an associate editor at Design Engineering.
Luminoso has a bachelor of arts from Carleton University, a bachelor of education from Ottawa University, and a graduate certificate in book, magazine, and digital publishing from Centennial College.
subscribe now
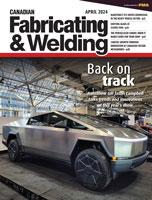
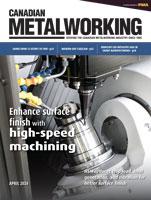
Keep up to date with the latest news, events, and technology for all things metal from our pair of monthly magazines written specifically for Canadian manufacturers!
Start Your Free Subscription- Trending Articles
Automating additive manufacturing
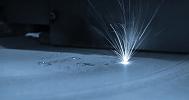
Sustainability Analyzer Tool helps users measure and reduce carbon footprint
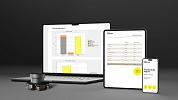
CTMA launches another round of Career-Ready program
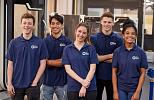
Sandvik Coromant hosts workforce development event empowering young women in manufacturing
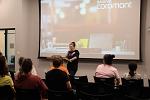
GF Machining Solutions names managing director and head of market region North and Central Americas
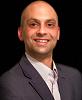
- Industry Events
MME Winnipeg
- April 30, 2024
- Winnipeg, ON Canada
CTMA Economic Uncertainty: Helping You Navigate Windsor Seminar
- April 30, 2024
- Windsor, ON Canada
CTMA Economic Uncertainty: Helping You Navigate Kitchener Seminar
- May 2, 2024
- Kitchener, ON Canada
Automate 2024
- May 6 - 9, 2024
- Chicago, IL
ANCA Open House
- May 7 - 8, 2024
- Wixom, MI