- FMA
- The Fabricator
- FABTECH
- Canadian Metalworking
Engaging the oilfield
Alberta manufacturer uses new machine for BOP production
- By Canadian Metalworking
- December 9, 2019
- Article
- Made In Canada
Situation
Lee Specialties, Blackfalds, Alta., was looking for a way to bring more production back in-house by replacing an older-model horizontal machining centre.
Although the company was still using it to produce oil well blowout preventers (BOPs), the machine was no longer able to keep up with new tooling technology advancements. Lee Specialties felt like it wasn’t maximizing its potential efficiencies. It tried different tooling, workholding, and machining techniques to try to reduce production costs, but results were limited. That is when it realized that new equipment was going to be necessary.
Some of the key features the company was looking for included a large pallet weight capacity, big machining work envelope, large tool magazine, and more speed.
Resolution
The manufacturer decided that a Toyoda FH1250SX horizontal machining centre was a fit. The 11,000-lb.-capacity pallet-changing machine had long travels, and the 120-tool magazine was the correct size for what it needed moving forward.
However, there was risk involved in implementing the system. The machine itself is very large, weighing more than 100,000 lbs., and it has a large footprint. This meant it didn’t fit perfectly into the shop space. There was a problem where one of the support beams was in the way of the tool magazine access door.
Lee Specialties didn’t want that to stop them from going forward with their plan, so they turned to the local distributor for help.
“LaMarche Machinery and Toyoda were able to identify a modification to the door so we could still put the machine where we wanted and eliminate any potential risk of it not being set up perfectly,” said Dave Halladay, manufacturing supervisor at Lee Specialties.
As a result of the new addition, especially because of the high horsepower and rigidity of the machine, Lee Specialties was able to improve almost every facet of the roughing operation, which is crucial to the machining process.
“The most pleasant surprise is the consistency and rigidity of the machine. The build of this machine allows you to push your tooling to the limit and maximize production. We have been able to reduce production time by 30 per cent on average. These results have been outstanding for us as we can now reduce lead times and get more production through the machine,” said Halladay.
Photos courtesy of Lee Specialties, www.leespecialties.com
Toyoda, www.toyoda.com
About the Author
Related Companies
subscribe now
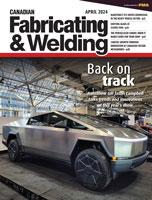
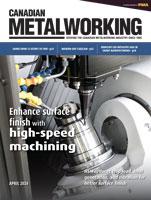
Keep up to date with the latest news, events, and technology for all things metal from our pair of monthly magazines written specifically for Canadian manufacturers!
Start Your Free Subscription- Trending Articles
Automating additive manufacturing
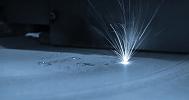
Sustainability Analyzer Tool helps users measure and reduce carbon footprint
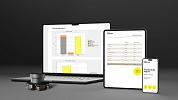
CTMA launches another round of Career-Ready program
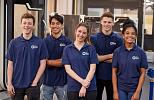
Sandvik Coromant hosts workforce development event empowering young women in manufacturing
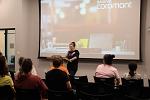
GF Machining Solutions names managing director and head of market region North and Central Americas
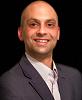
- Industry Events
MME Winnipeg
- April 30, 2024
- Winnipeg, ON Canada
CTMA Economic Uncertainty: Helping You Navigate Windsor Seminar
- April 30, 2024
- Windsor, ON Canada
CTMA Economic Uncertainty: Helping You Navigate Kitchener Seminar
- May 2, 2024
- Kitchener, ON Canada
Automate 2024
- May 6 - 9, 2024
- Chicago, IL
ANCA Open House
- May 7 - 8, 2024
- Wixom, MI