Editor
- FMA
- The Fabricator
- FABTECH
- Canadian Metalworking
Supplier Side Talk: Hexagon Manufacturing Intelligence Canada
David Hill talks about metrology, the Canadian market, and technology adoption
- By Joe Thompson
- March 28, 2023
- Article
- Measurement
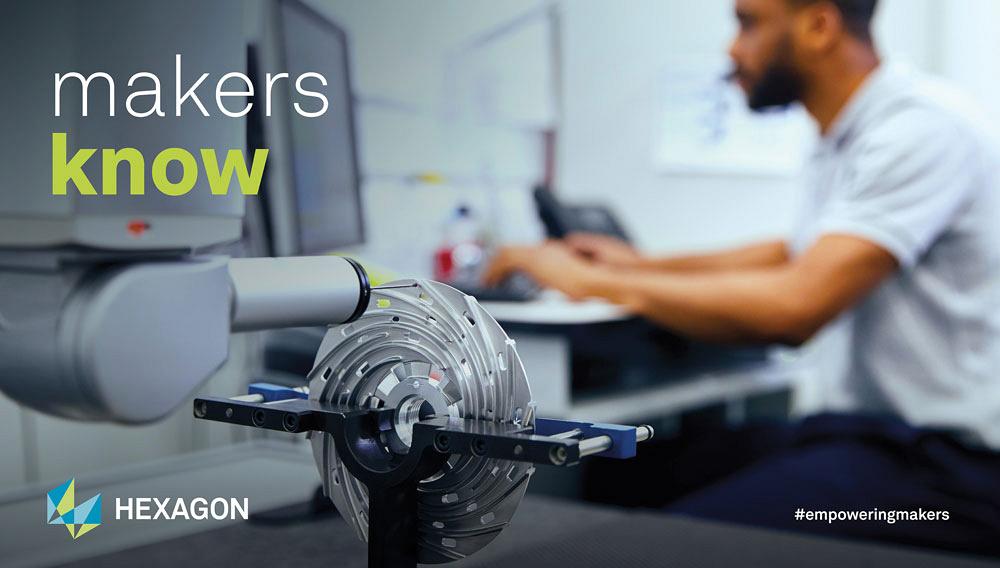
Dimensional analysis enables manufacturers to produce perfect parts. Hexagon Manufacturing Intelligence
Hexagon Manufacturing Intelligence has three locations in Canada. In addition to its Oakville, Ont., headquarters, which is a stand-alone Hexagon office, it also has a presence in Calgary (co-located with NovAtel), and in Montreal (co-located with Leica Geosystems).
Each location is committed to helping manufacturers improve their metal processing tasks, automation deployment, and, of course, metrology work. The company’s “empowering makers” mantra makes it clear that it understands the breadth of need their audience is looking for.
Hexagon provides makers with new ways of innovating and optimizing products and production from design through to service life. Its technology portfolio includes measurement hardware and software, hand tools, coordinate measuring machines (CMMs), portable measuring arms, laser trackers and 3D optical scanners, and PC-DMIS.
The company also provides products and expertise in CAD and CAM work, as well as computer-aided engineering (CAE), finite element analysis (FEA), computational fluid dynamics (CFD), and multi-body dynamics (MBD), as well as cost estimation and design optimization.
Recently, Editor Joe Thompson spoke with David Hill, director of commercial operations for Canada, about the company’s recent growth and investments in Canada, technology adoption, and how metrology and measuring tasks fit into the overall part manufacturing process. Here is part of that conversation.
Thompson: Hexagon recently has invested in classic bricks-and-mortar infrastructure in Canada. What are the benefits of being geographically close to your customers?
Hill: We started this journey of expanding our footprint in the Canadian market based purely on the needs of our customers. Our Oakville office has design and engineering, production software, and metrology all under one roof, and we have 115 employees in this location in a mix of sales, design and engineering services, and service support.
By having this staff close to our customers, we can respond quickly to support calls to calibrate machines, whether it be portable arms, trackers, or CMMs, as well as fix machines that are down. And then there’s demos and training. Whether it's Oakville, Montreal, or Calgary, the idea was to open solution centres where our customers can see all of our technology and where we can perform demonstrations for them.
And, while we can do on-site training in a customer’s location, by having these, as you say, bricks-and-mortar locations, we can also provide in-house training on all of our systems and software.
Thompson: Hexagon has grown organically, as shown by the opening of new locations, but the company also grows by acquisition. What makes a company a good target for acquisition and how does it help the customer?
Hill: It's a good point. Hexagon grows in a number of ways, including by reinvesting a large portion of earnings back into R&D to continuously improve our existing products.
But at the same time, M&A [mergers and acquisitions] is another way to grow. There's a lot of technology that exists in the marketplace that could be an immediate value-add for our customer base. In these cases, Hexagon definitely looks at whether an acquisition makes sense. And if you look at our history, in the case of Sheffield, Brown & Sharpe, and Romer, these all brought something to the company to fill a need. In fact, this year celebrates the 50th anniversary of the Hexagon Absolute Arm. It was created in 1973 as a bench-mounted articulating arm designed to measure tubes and pipes.
We acquired these companies to make Hexagon better and bring the best available technology to our customers.
Thompson: Hexagon describes the industries it serves as “ecosystems,” and I think that’s a good descriptor. In today’s manufacturing ecosystems, once disparate departments like IT, sales, customer relationship management, machining, and metrology all seem more closely linked now than in the past. What are the benefits of these departments working together, and is the creation and management of data one of the things that connects them?
Hill: Well, you're spot on. It's funny that for years data was collected just for the sake of collecting it. But now you have to treat data like an asset.
We're entering a point where we're truly focusing on smart factory initiatives that puts collected data to work and puts it in the hands of the people that make decisions. And that's really the start of the journey of digitalization. Within that journey we focus on empowering makers to overcome design, production, and inspection challenges. Simply, manufacture with confidence and get it right first time.
Connecting stock ordering, scheduling, maintenance, design, and engineering with the factory floor is at the heart of smart manufacturing. It allows manufacturers to react quickly by pulling the data from the manufacturing systems themselves and pointing someone in the direction of a future issue that they can now head off by making some small change before things break down or get out of tolerance.
Thompson: Technology adoption remains key for Canadian manufacturers to keep pace in the global marketplace. So, how important is it for shops to make technology adoption part of their continuous improvement efforts?
Hill: If you’re not investing in and utilizing technology to its fullest, I don't think you're doing yourself any favours. Take a look at your process. Most companies that are investing in technology today, it’s to create a competitive advantage. It’s a way to create efficiencies that positively affect the bottom line.
It’s also a good idea to think about technology adoption as more than just a new machine or new automation. Software matters. Metrology matters. CNC machines just keep getting better and better.
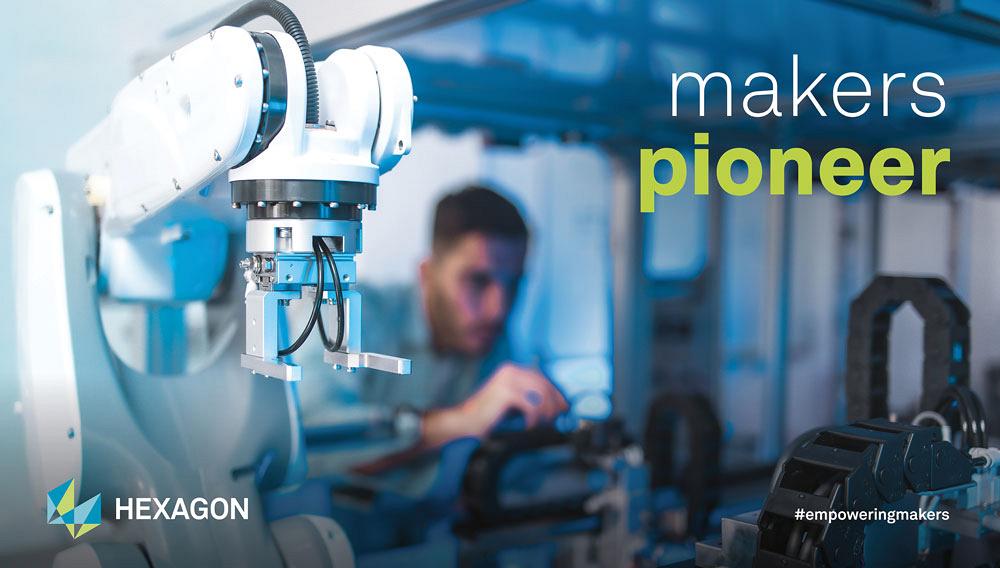
Deploying automation helps 21st-century manufacturers to increase throughput. Hexagon Manufacturing Intelligence
I mean, if you look at the surface finishes that they can achieve and the complexity of the components that they can produce with the tolerances that they can hold, it’s a good time to invest in technology.
Thompson: I think if you talk about metrology with a lot of shop owners/managers, they think of it in terms of dimensional analysis. No doubt this is important to them. What technology leaps forward have happened recently that they should investigate?
Hill: In-process inspection with portable arms and trackers. In-machine inspection with probing today makes sense in a lot of cases, but it is a trade-off. It’s probably necessary for critical features, but checking a part inside a CNC machine means you’ve stopped making chips.
What becomes extremely important in these cases is scheduling. You have to ask: Can I afford not to check the part? If you take the part of the machine and it’s not perfect, can you schedule it to get it right back on to another machine to make a correction? And what does that cost entail?
Or has the part gotten so far along the process, with all of the real value-added work finished, just to become scrap that could have been caught early on?
Probes are getting smaller and can make more accurate measurements. If you’ve looked at this technology in the past, it’s a great time to have another look.
Laser scanning is another in-machine option. The same 10.10 laser scanner that is part of our CMMs has been built into an IP68 enclosure that fits in a tool changer. So, I can put a large casting on the CNC machine and use the laser scanner to grab scan data.
We've also got a new NDT probe for CNC machines and for portable arms, which is a game-changer.
Thompson: I’ve talked to many shop owners that absolutely hate buzzwords. Is Industry 4.0 simply a buzzword? What does a practical, pragmatic view of this term mean to you?
Hill: Definitely digitalization, in my opinion.
I mean, we live in a world of buzzwords, right? But it's 2023. This should be the year of digitalization.
If you go back just a couple of years, Industry 4.0 was all about automation. But, if you think in terms of digitalization, it encompasses automation processes and it also encompasses the automation of data usage. Digitalization helps disseminate data quickly to those who need it so that they can be proactive, as opposed to scrambling and reactive.
Automation today isn’t just about machine tending. You can apply automation in your design process, in your CAM processes, and during inspection. These aren’t separate anymore, it's really all one large start-to-finish process.
You now design with manufacturability intent and create cutter paths based on real-time data. Measurement automation comes in the form of routines, and you can do on-machine inspections.
It’s about wrapping your arms around total process control. That’s the key.
Hexagon Manufacturing Intelligence, www.hexagonmi.com
About the Author
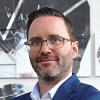
Joe Thompson
416-1154 Warden Avenue
Toronto, M1R 0A1 Canada
905-315-8226
Joe Thompson has been covering the Canadian manufacturing sector for more than two decades. He is responsible for the day-to-day editorial direction of the magazine, providing a uniquely Canadian look at the world of metal manufacturing.
An award-winning writer and graduate of the Sheridan College journalism program, he has published articles worldwide in a variety of industries, including manufacturing, pharmaceutical, medical, infrastructure, and entertainment.
Related Companies
subscribe now
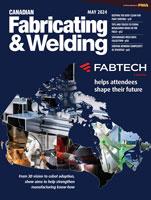
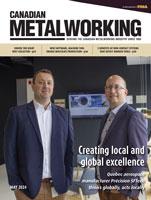
Keep up to date with the latest news, events, and technology for all things metal from our pair of monthly magazines written specifically for Canadian manufacturers!
Start Your Free Subscription- Trending Articles
Sustainability Analyzer Tool helps users measure and reduce carbon footprint
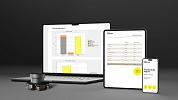
Mitutoyo updates its end-user portal
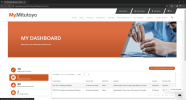
Enhance surface finish with high-speed machining
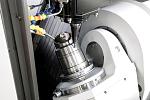
Equispheres secures $20 million investment round
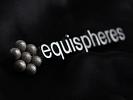
Solid carbide drills produce precision holes in short chipping materials
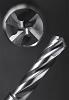
- Industry Events
Automate 2024
- May 6 - 9, 2024
- Chicago, IL
ANCA Open House
- May 7 - 8, 2024
- Wixom, MI
17th annual Joint Open House
- May 8 - 9, 2024
- Oakville and Mississauga, ON Canada
MME Saskatoon
- May 28, 2024
- Saskatoon, SK Canada
CME's Health & Safety Symposium for Manufacturers
- May 29, 2024
- Mississauga, ON Canada