- FMA
- The Fabricator
- FABTECH
- Canadian Metalworking
Business Profile: Burloak Technologies
Canada’s first advanced manufacturing facility anticipates a wave of innovation to thanks to 3D metal printing technology.
- By Canadian Metalworking
- January 30, 2015
- Article
- Metalworking
The smell of fresh paint still lingers in the air of the shop floor at Burloak Technologies where space has been prepared for Canada’s first additive and automated machining production facility—bringing 3D metal printing together with subtractive technologies for a full service state-of-the-art offering. It’s a move the company’s management team believes will jump start the next generation of advanced metalworking manufacturing in this country and lead to the return of innovative high-value part production to North America.
Set up in Dundas, Ontario, this past August Burloak unveiled phase one of its $11.5 million five-year strategic plan to establish its advanced manufacturing centre. To date the company has spent $2.5 million equipping its new plant with an EOS M 290 production direct metal laser sintering (DMLS) 3D printing system and a selective laser sintering (SLS) 3D printer for plastic parts, as well as a complement of automated Matsuura CNC machining systems including five-axis and three-axis milling machines, a four-axis turning machine and a Zeiss CMM system.
Peter Adams originally founded Burloak in 2005 as a supply chain management specialist for large industrial companies seeking to optimize their manufacturing processes.
A mechanical engineer, Adams spent years in management positions within large-scale organizations working on the machining and assembly side of manufacturing. In his experience he witnessed a disconnect between engineering design and the shop floor, especially when part manufacturing was moved from one shop to another or taken offshore. The supply chain was broken, and where executives expected cost savings they discovered a lack of planning and oversight, which ultimately led to poor results.
Adams formed Burloak to provide engineering expertise, quality control and ensure the optimized production of high performance components for these large players.
“We took a very different approach to supply chain and have been very successful at managing and taking very complex products overseas, or sourcing locally, and delivering great results,” says Adams.
In the eyes of its customers Burloak was effectively a virtual manufacturer, taking ownership of the parts being manufactured, right down to onsite quality inspection at offshore sites. “When you’re sourcing low volume, highly complex projects you only have one chance to get it right,” says Adams.
Having established itself as a reliable supply chain specialist in metalworking manufacturing, Burloak began investigating its next steps. Three years ago Jim Glover joined the company. A long-time friend of Adams, Glover is an engineer who had had spent the last decade involved in venture capital. Glover looked at Burloak’s existing supply chain business and the emergence of production-quality additive technology in the metalworking industry, and he saw all that was missing was a supply chain providing the 3D printing capability.
“And we didn’t see that supply chain happening in China,” says Glover, “we saw it here.”
Small companies similar to Burloak in the U.S. and the U.K. were already sprouting up and offering these supply chain solutions to customers. “We decided this is the sweet spot to go for,” he says, and it became not a matter of if, but when. So in late 2013 Adams and Glover developed their business plan, raised some private equity, and began the process.
Today Burloak Technologies Inc. is comprised of two wholly-owned subsidiaries, Burloak Advanced Manufacturing (the new production facility) and Burloak Engineered Solutions (the supply chain specialists).
This past July the company moved from Burlington to its new building in Dundas, just outside of Hamilton, to set up its manufacturing plant.
The timing of the launch required confidence in the maturity of the DMLS technology and the necessary demand for the products it can produce.
“The defining moment for us was seeing what GE had accomplished,” says Adams, referring to GE Aviation’s upcoming LEAP engine program that incorporates 3D-printed fuel nozzles. “When a company like GE is putting the parts in aircraft engines, you’re sure it’s a mature technology.”
According to Glover, what really attracted them to the DMLS technology was the complexity that could be built into the parts. And he knew they needed to get involved early to gain that hands-on knowledge. “If we didn’t make the move now, we’d risk being further back in that wave.”
“The great thing I see is that outsourcing to China is likely to dry up because of this technology,” says Adams. “You’re not going to bring the widgets back to North America. Instead we’re going to be creating high-tech components here.
“Today people design to the constraints of the regular machine shop, but as this technology matures and becomes more widely accepted you’re going to see the very nature of the designs change. And when they do, you’re going to be looking at very complex lightweight components.
“If customers are able to print their high-value products close to the source in no time at all, why would they go offshore. And for designers creating highly complex products, it’s advantageous to keep the manufacturing close to protect their intellectual property.”
As for generating the demand, Glover admits that’s a critical piece, which he describes as a chicken and egg situation. “The designers won’t design a product into something if there is no supply chain, and the supply chain won’t be created if there is no load for it. We see ourselves as the first on the block, and we’re talking to a lot of companies that want to design their products in.”
Both Adams and Glover note that the aerospace and energy sectors are acutely aware of the technology and the medical market has huge growth potential. They also see huge opportunity locally in the mold and die industry, specifically 3D metal printing of molds with conformal cooling inside—functionality that gives mold makers a strong competitive advantage.
“Mass customization is what it’s good for, low volume with options,” says Adams. “If the product is complex, high value and very difficult to manufacture, then it’s a good candidate for going to production on an additive machine.”
In setting up their production facility they knew there couldn’t just be a 3D metal printer, or plastics printer. “We needed to offer a full suite of services: the machining capability, the CMM and the post processing to be a true advanced manufacturing centre,” says Glover.
“What we’re uncertain of right now is how those things play off each other,” admits Glover. “How much business is the metal 3D printer going to drive on the subtractive (machining) side, and vice versa.” It is likely that work from the supply chain side of Burloak’s business that was previously being sourced offshore will be repatriated and placed on its new CNC machines.
Overall, as some of the equipment is still being unwrapped and set up for production both Adams and Glover are brimming with confidence. Their new Dundas location was a strategic decision. “When a customer puts their manufacturing load on you, they want to know you have the capacity and capability to scale. That’s part of the reason for moving here,” notes Glover. Their space now occupies 10,000 sq. ft., with an adjacent building allowing for easy expansion of another 6,000 sq. ft., and when necessary another 12,000+ sq. ft. beside that, all under one roof.
Dundas is also located down the road from Mohawk College, where there are EOS machines installed (Burloak is in talks of setting up a co-op program with the school) and also McMaster University is nearby. The company currently employs nine people, but Adams suspects that number will be up to 15 by early 2015 and at 22 by next summer.
Being first to the Canadian market as a 3D metal printing production facility is something the partners expect will be short lived. “It’s a growing market and by next year we expect to have competition. In the U.S. there are some successful operations that have done what we’re doing, and the good problem for us is that most of those are already at capacity and waiting for new machines, and/or they have been acquired by other companies,” smiles Glover.
The barrier to entry in this market is the significant investment in high-end equipment that is required. And the real advantage for Burloak is their plan to automate their operation to the utmost.
“That’s the beauty of the way we’re setting up this facility,” says Adams. “Even the subtractive machines we’re installing are highly automated, so we’re going to run one-offs as efficiently as some companies will run 50.”
Burloak has partnered with Elliott Matsuura Canada for its CNC technologies. “There are a lot of good quality CNC machines out there, but when we put it all together, Elliott just stood out,” notes Adams. “They’ve got such depth in what they could offer, both now and as we grow, especially with all of the automation we are planning.”
Part of the efficiency will come from a common pallet system that will be able to move parts from machine to machine with basically zero set-up time. “The reference tooling system from 3R was all Elloitt Matsuura Canada’s idea,” says Adams. “And the beauty of this is, as our manufacturing load grows and we start running lights-out production, Elliott will supply robotic loading systems that will manage the process, actually taking pallets in and out of the machines.”
It’s this next level of advanced manufacturing automation combined with intelligent 3D printing that Burloak believes will set it apart and position it well for the next wave of part design innovation.
“Having watched the decline of manufacturing in Western countries, I think this is a brilliant opportunity for us to step up and take the lead in that market again. That’s what excites me,” says Adams.
About the Author
subscribe now
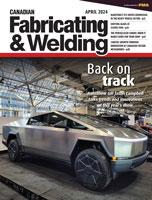
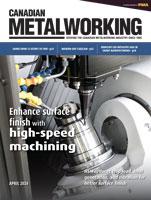
Keep up to date with the latest news, events, and technology for all things metal from our pair of monthly magazines written specifically for Canadian manufacturers!
Start Your Free Subscription- Trending Articles
Automating additive manufacturing
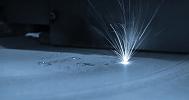
Sustainability Analyzer Tool helps users measure and reduce carbon footprint
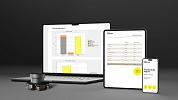
CTMA launches another round of Career-Ready program
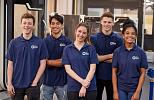
Sandvik Coromant hosts workforce development event empowering young women in manufacturing
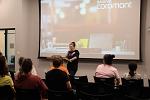
GF Machining Solutions names managing director and head of market region North and Central Americas
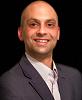
- Industry Events
MME Winnipeg
- April 30, 2024
- Winnipeg, ON Canada
CTMA Economic Uncertainty: Helping You Navigate Windsor Seminar
- April 30, 2024
- Windsor, ON Canada
CTMA Economic Uncertainty: Helping You Navigate Kitchener Seminar
- May 2, 2024
- Kitchener, ON Canada
Automate 2024
- May 6 - 9, 2024
- Chicago, IL
ANCA Open House
- May 7 - 8, 2024
- Wixom, MI