- FMA
- The Fabricator
- FABTECH
- Canadian Metalworking
Keeping your cool
Exploring the benefits of in-house coolant recycling.
- By Canadian Metalworking
- December 12, 2014
- Article
- Metalworking
According to some coolant recycling manufacturers, their systems can have an average return on investment of under a year. These calculated savings for machining and grinding operations can come from a range of areas including the long-term reduction of waste hauling costs, reduction in new fluid purchases, enhanced machine performance, less downtime, increased tool life, and an improved working environment.
Canadian Metalworking spoke with Tom Tripepi, technical director for the fluid filtration division of PRAB, based in Kalamazoo, Michigan to discuss the basics of coolant filtration and recycling systems.
With over 30 years of industry experience working in R&D, designing and developing tramp oil separators and coolant recycling systems, Tripepi shares valuable insights on the subject and the benefits he’s witnessed.
CM: WHAT ARE THE MAIN DIFFERENT TYPES OF COOLANTS, AND ARE SOME MORE DIFFICULT TO WORK WITH FROM A FILTRATION/RECYCLING PERSPECTIVE?
TT: There are three basic types of coolant. There is the water-soluble coolant, basically an oil with some surfactants and wetting agents that cause the oils to emulsify with the water, so that as you’re cutting/machining/grinding you’ll have the properties of the oil for lubricity and you have the water cooling the parts.
Then there is the semi-synthetic, which is again a soluble oil but there are components that are synthetic (non-petroleum-based oil) to give it more lubricity and a tighter emulsion.
And finally there is synthetic coolant, which means there are no petroleum-based hydrocarbons in the coolant at all. And then there is what is known as a true solution, which is all chemical and others that are called macro-emulsions where it is still an emulsion rather than a true solution.
In terms of recyclability, it varies, because with soluble oils you have to be aware of how tight the emulsion is. For some manufacturers the oil droplets could be 20-microns in size, meaning they’re hard to recycle because in the filtration process you might start separating that emulsion, basically removing the coolant from the water. Semi-synthetics tend to be a tighter emulsion, the tighter the emulsion the easier it is to filter out the impurities without affecting the coolant. The straight soluble oils would be the harder ones to deal with.
CM: HOW DO YOU DEAL WITH THAT FROM A FILTRATION PERSPECTIVE?
TT: Part of establishing a whole recycling process requires working with the customer’s chemical supplier. If they come back and say, “This is a fairly loose emulsion, you do not want to put a centrifuge on it, it will rip the emulsion apart,” or “You don’t want to filter any less that say 25 micron,” That will determine what equipment you’re going to be using.
As an example, I’m working with a customer who’s doing aerospace work, and with the aerospace aluminums the coolant starts to get grey because of the fine aluminum oxides from the machining. To take those out you’re looking at about 1-micron filtration. This particular coolant manufacturer said, “No, you don’t want to filter any less than 10-micron.” They’re recommendation was to filter 25-micron first and then 10-micron second, where originally the customer told us they wanted 5 and 1. If we filtered that way, it would destroy the coolant.
CM: CHIPS AND SWARF GET FILTERED OUT, WHAT ELSE ARE YOU REMOVING? ARE YOU ABLE TO REMOVE BACTERIA FROM THE COOLANT?
TT: You can’t really filter out bacteria from coolant itself, because bacteria typically is about 0.45 microns, so if you try to filter out bacteria you will actually destroy your coolant. What you’re removing are the chips, solids generated from the process, but you also filter out oils, be it from the machines themselves, lube oil or hydraulic oil, and often parts come in and they have oil on them (sometimes rust inhibitors), these are all considered tramp oils. And sometime the parts maybe sit outside, in the case of steel coils and that type of thing, and they’ll pick up dirt, so you want to pick up those solids as well.
By removing all of those materials and oils that’s how you prevent bacteria from forming, because you’re eliminating their food source.
In some shops, where they’re not removing tramp oils and over the weekend they don’t machine, the tramp oils float to the top of the coolant and seal the fluids preventing oxygen from getting in and the anaerobic bacteria develop. One of the byproducts is the sulphuric rotton-egg smell.
Most concentrates have some form of biocide in them that helps to prevent bacteria from growing in the coolants, and there are coolants out now called biostable, they’re formulated so that they cannot support bacteria growth at all.
CM: CAN YOU ADDRESS WHERE THE SAVINGS ARE ACHIEVED FROM COOLANT RECYCLING?
TT: Very basically, most people are looking to mix a coolant to a certain concentration say five or 10 per cent.
So some shops follow a good practice and have someone with a refractometer to read concentrations, or they have a central mixing station and that helps. In some facilities they leave it up to the operators, and for some operators, instead of getting the refractometer they’ll rub the coolant between their fingers and if it doesn’t feel slippery enough they’ll add concentrate to a machine. Then the guy on second shift will come in and feel the coolant is too rich, so he adds water to the machine, so the concentrations are all over the place.
By implementing a coolant recycling program one of the steps is how you monitor and mix your coolant. As an example, our coolant recycling system has an automatic proportionating system on it, so when the level drops down we make up coolant. And it’s made up of the correct concentration. That process itself can probably save 10 to 20 per cent in new coolant purchases, just because it’s giving you control over how you’re mixing your coolant.
But coolant will only last so long in a machine, and some shops will only replace their coolant two or three times a year. They know it should be more frequent, but it’s too expensive for them to have it hauled away.
Then you have shops that are getting rid of coolant every month, up to 1,000 gallons of coolant a month, and it’s costing them 50-cents a gallon to get rid of it. When they start recycling their coolant they eliminate their haul away cost, typically by 80 or 90 per cent. And by reusing their coolant they’re reducing their coolant purchases by 40 to 75 per cent. That’s where the real savings come. And when you recycle, you’re not throwing large amounts of coolant away, so you’re reducing the amount of liability you have going out the door in the way of hazardous waste.
CM: IS RECYCLING REALLY ONLY ECONOMICAL FOR THE LARGE SHOPS?
TT: We’ve got shops where we’ve sold recycling stations that have as few as four machines. A typical machine shop that is looking at recycling their coolant will probably have somewhere between 15 and 20 machines, and from there on up to the larger shops with 80 to 100 machines or more. It just depends, because of the other benefits of recycling. By removing tramp oils you stop a lot of the smoking and misting that takes place in the machines, so it cleans up your shop environment.
There have been studies done in the UK that claim you can save up to 209 per cent on your tool life. We typically tell customers you can figure that you’ll increase your tool life by at least 25 to 50 per cent. By taking out the tramp oils that hamper the cooling, your tools last longer, you get better finishes, and the quality of your machining increases dramatically.
Those are some of the additional benefits to consider when you’re justifying your return on investment.
CM: YOU MENTIONED IMPROVED AIR QUALITY, WHAT OTHER HEALTH BENEFITS ARE LINKED TO RECYCLING?
TT: One of the big things is avoiding dermatitis.
This skin condition will typically come from contact with coolants that are contaminated with bacteria. Not all operators wear gloves, and they will be pulling parts in and out of a machine. By eliminating the bacteria you can eliminate the dermatitis. We had one guy that was complaining about the coolant and he broke out in dermatitis. The cause was actually a rag that he always kept in his back pocket. He’d wipe off the parts and then put it back in his pocket and sit on it.
CM: HOW LONG CAN YOU RECYCLE COOLANT?
TT: Theoretically, you can recycle the coolant indefinitely. Typically you’ll get between 10 to 20 per cent evaporation or carry-off. For example, if you have a 55 gallon drum with chips, you’ll have somewhere between 5 to 20 gallons of fluid trapped in those chips. You can process those chips, spinning them and recovering that fluid, but still you may be losing 10 per cent out of your machine every day. So if every day you’re topping up with 10 per cent new coolant, over a 10 day period you’ve completely displaced the volume of that machine.
So it isn’t a case where you put in a coolant recycling system and you run that same batch forever. The answer is, you’ve filtered it, you’ve fortified it with new coolant, and you’ve brought it back to concentration. It keeps the coolant within an acceptable workable range for a long time.
We have people with recycling stations that tell us they maybe dump their whole recycling station every five years, some as long as every 10.
CM: HAVE YOU SEEN AN INCREASE IN DEMAND FOR RECYCLING STATIONS?
TT: Over that last couple of years yes, we have seen an increase. Because it’s only costing people more and more to haul contaminated coolant away, so it makes sense for them to recycle and reuse it back in their shop.
About the Author
subscribe now
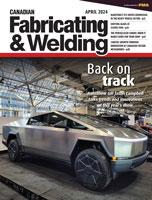
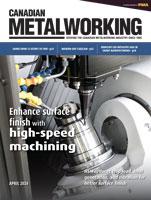
Keep up to date with the latest news, events, and technology for all things metal from our pair of monthly magazines written specifically for Canadian manufacturers!
Start Your Free Subscription- Trending Articles
Automating additive manufacturing
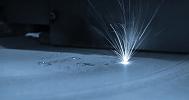
Sustainability Analyzer Tool helps users measure and reduce carbon footprint
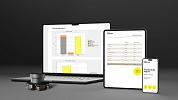
CTMA launches another round of Career-Ready program
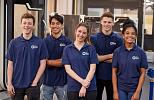
Sandvik Coromant hosts workforce development event empowering young women in manufacturing
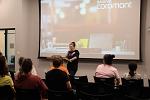
GF Machining Solutions names managing director and head of market region North and Central Americas
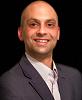
- Industry Events
MME Winnipeg
- April 30, 2024
- Winnipeg, ON Canada
CTMA Economic Uncertainty: Helping You Navigate Windsor Seminar
- April 30, 2024
- Windsor, ON Canada
CTMA Economic Uncertainty: Helping You Navigate Kitchener Seminar
- May 2, 2024
- Kitchener, ON Canada
Automate 2024
- May 6 - 9, 2024
- Chicago, IL
ANCA Open House
- May 7 - 8, 2024
- Wixom, MI