Associate Editor
- FMA
- The Fabricator
- FABTECH
- Canadian Metalworking
New multitasking machine leads to significant efficiency gains
Ofir Machine Shop adds Okuma LB3000 EX II machines to expand capabilities
- By Lindsay Luminoso
- September 13, 2023
- Article
- Metalworking
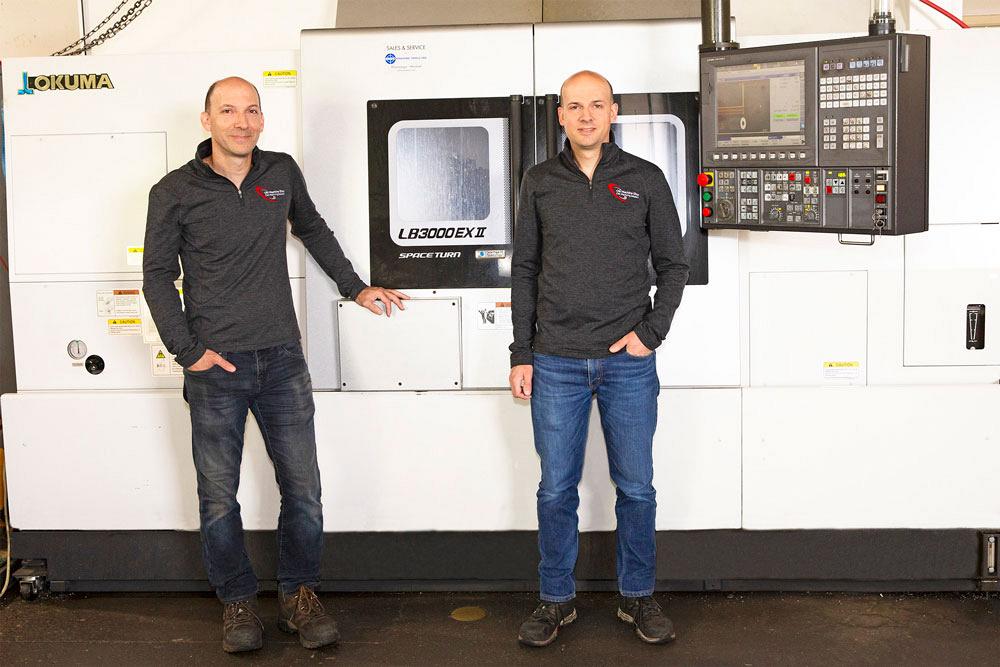
(From left) Brothers Ran and Shai Ofir stand in front of their Okuma LB3000 EX II MY horizontal lathe, which includes C-axis and Y-axis for milling capabilities. Images: Ofir Machine Shop
Ofir Machine Shop’s history dates back to 1965, when it got its start as a manufacturer of components for the military industry. In the mid 1980s, the Ofir family emigrated from Israel to Canada and settled in Toronto, bringing their machining skills and expertise to the local community.
Both Josef and his son Ike set up shop in Toronto with just one Okuma CNC lathe and several manual machines. Until Josef’s retirement in 1987, the two worked to establish Ofir as a reputable machine shop and expand to meet the needs of current and future customers.
The shop quickly grew into a true CNC shop as the focus shifted to investing in additional CNC machines. From the late 1980s and into the early 2000s, Ike worked closely with the Mississauga, Ont.-based EMEC Machine Tools team to find the best machines for the shop’s needs.
By 2002, it had four Okuma CNC lathes and four Okuma CNC mills, as well as an experienced and stable workforce.
Ofir Machine Shop has always been a family business. It became a third-generation shop when two of Ike’s sons, Shai and Ran, joined the company in 2015 and 2017, respectively. The two now lead the company as co-presidents.
While the shop’s original focus was on military components, the move to Canada allowed it to branch out into more diverse and less military-focused work. And although the shop continues to be involved in military projects, it now serves customers in the machinery manufacturing, automation, oil and gas, and medical industries, to name a few.
“There's so much that we've done over nearly 40 years in Toronto,” said Shai Ofir, co-president. “As a custom shop, we have the opportunity to work directly with our customers to tailor projects that best meet their needs. We work with a wide range of materials like various grades of steel and stainless steel, brass and other copper alloys, aluminum, exotic materials, and plastics. We work with materials in the form of round bar, flat bar, castings, extrusions, and plate. Our goal is to be as versatile as possible.”
Once the two brothers settled into their roles, they focused on getting a handle on the business and the ups and downs of the industry. They recognized that while the shop equipment was still working well, it was starting to age. Even though the machines tend to last a long time if they are properly cared for, it was time to look at some advanced technology.
Shop Capabilities
Shai noted that new machines are often faster and can facilitate the combining of operations to minimize setups and handling time.
“If our father hadn’t purchased the first CNC machine in the early 80s, where would our shop be today?” said Shai. “That really set the tone for how we operate. In the last five years, we’ve really focused on the latest technology for our shop. Our father focused on investing in 2-axis CNC lathes and 3-axis CNC mills. Part of our job is to focus on the multiaxis front, particularly on our lathes. That has really transformed the way that we think about the business, the jobs that we can do, how we price the jobs, and how we're competing. It's really changed a lot for us.”
In late 2018, the brothers set out to learn about the newest CNC technology available. The more the Ofir team looked at their options, the more they realized the endless capabilities a lathe with milling capabilities would offer them. They immediately began to see how existing jobs could be done more efficiently and how they would be able to compete for more jobs because of those capabilities.
“That was our trigger to go and buy that first one in 2019,” said Shai. “We're in business and we take risks, but we take calculated risks. As business owners, we're probably relatively conservative in terms of the risks that we take. We didn't want to venture into territory that we didn't know much about. But we have lathes and mills here, so our thinking was, ‘Why can't we handle a lathe that can also perform milling tasks?’”
EMEC was instrumental in helping the shop gain the necessary information and examine what machine would make the most sense. The machine tool distributor facilitated a visit to an existing customer using similar machines to demonstrate what the machines could do, which provided the brothers with the proper intel to set them on the right path.
“This really assured us that we would not regret the investment,” said Shai. “And we certainly haven’t. I would not have believed four years ago, after having purchased the first Okuma LB3000 MY multitasking machine, that we would end up with another four Okuma CNCs in less than four years, including one with a subspindle, the LB3000 MYW.”
On-boarding the first Okuma multitasking lathe was a relatively seamless process, but it took building confidence one job at a time to get to a point where the machine was running an array of jobs.
Multitasking Productivity Gains
Since the arrival of the first multitasking machine, the shop has seen efficiency gains.
“The Okuma LB3000 MYW is an excellent machine for us because it has a C-axis and a Y-axis for milling capabilities, as well as a subspindle,” said Shai. “With these features, we can run a first operation and transfer the piece to a secondary spindle, which combines multiple turning and milling operations into one. It’s all automated, so we've done many jobs on this machine, but there are a couple of jobs that really stand out.”
One of the projects the shop has taken on is a repeat job with an annual requirement of about 2,000 pieces. Before investing in multitasking technology, each part needed to make multiple trips across the shop floor from one machine to another.
“We can now load the raw material onto our LB3000 MYW and a few minutes later, a finished piece comes out,” said Shai. “When our customer tells us they have an immediate requirement for more parts, we don’t have to cycle through several operations or tie up multiple machines for the job. We just set it up on the one machine and start running it until the project is finished. We can start supplying complete parts right away, keeping our customer’s production running without any delays.”
Another realized advantage is in precision. Transferring a part from one spindle to the other is extremely accurate and repeatable. The shop produces a lot of components with tight length tolerances, and having a subspindle allows for it to achieve exact dimensions and meet that high accuracy standard every time.
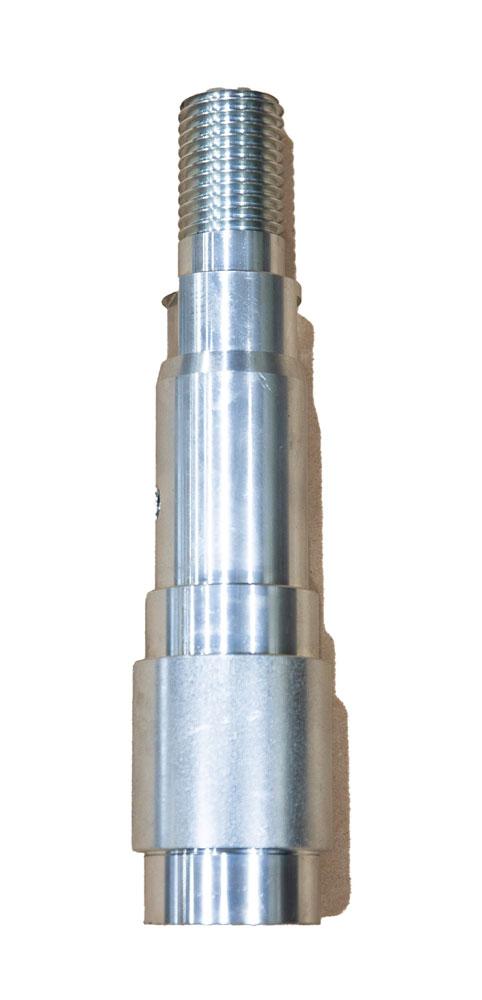
This part were fully produced on Okuma LB3000 MYW with features including keyways, cross-holes, and flats.
“Without that subspindle, and with more traditional machines, we weren’t able to accomplish that level of repeatability with such efficiency,” said Shai.
Next Steps at Ofir Machine Shop
Today, the shop has 13 Okuma CNCs within its 12,000-sq.-ft. facility, and the Ofir brothers are looking for ways to continue the family legacy.
“We are in this for the long haul, especially as the third generation of Ofirs,” said Shai. “We are hands-on owners, involved in every aspect of the business.”
The pair is focused on maintaining their equipment, while growing their existing client base. And because the brothers are on the same page, they are able to make quick decisions when it comes to the direction of the company.
“When an opportunity arises, we are absolutely willing to pull the trigger on additional equipment or real estate to increase our capacity or diversify our capabilities,” said Shai. “It’s important for us to keep growing and diversifying what we offer our customers.”
Associate Editor Lindsay Luminoso can be reached at lluminoso@canadianmetalworking.com.
Ofir Machine Shop, ofirmachine.com
EMEC Machine Tools, www.emecmt.com
About the Author
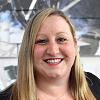
Lindsay Luminoso
1154 Warden Avenue
Toronto, M1R 0A1 Canada
Lindsay Luminoso, associate editor, contributes to both Canadian Metalworking and Canadian Fabricating & Welding. She worked as an associate editor/web editor, at Canadian Metalworking from 2014-2016 and was most recently an associate editor at Design Engineering.
Luminoso has a bachelor of arts from Carleton University, a bachelor of education from Ottawa University, and a graduate certificate in book, magazine, and digital publishing from Centennial College.
subscribe now
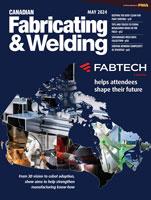
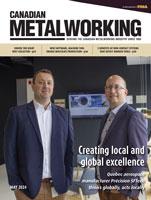
Keep up to date with the latest news, events, and technology for all things metal from our pair of monthly magazines written specifically for Canadian manufacturers!
Start Your Free Subscription- Trending Articles
Automating additive manufacturing
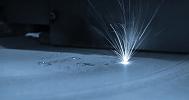
Sustainability Analyzer Tool helps users measure and reduce carbon footprint
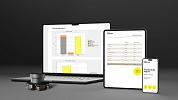
GF Machining Solutions names managing director and head of market region North and Central Americas
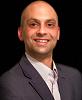
Mitutoyo updates its end-user portal
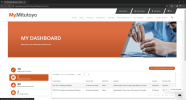
Enhance surface finish with high-speed machining
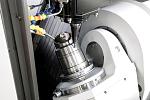
- Industry Events
Automate 2024
- May 6 - 9, 2024
- Chicago, IL
ANCA Open House
- May 7 - 8, 2024
- Wixom, MI
17th annual Joint Open House
- May 8 - 9, 2024
- Oakville and Mississauga, ON Canada
MME Saskatoon
- May 28, 2024
- Saskatoon, SK Canada
CME's Health & Safety Symposium for Manufacturers
- May 29, 2024
- Mississauga, ON Canada