- FMA
- The Fabricator
- FABTECH
- Canadian Metalworking
Pushing profit with Preventive Maintenance Program
Live tool heads are a big contributor to improving machine tool efficiency.
- By Canadian Metalworking
- April 13, 2015
- Article
- Metalworking
Shops that regularly inspect and maintain their live tool heads can achieve up to five times more service life and lower overall toolholder costs than those that do not. A live tool system preventive maintenance (PM) program ensures part accuracy, increased cutting tool life, reduced scrap, improved reliability and overall confidence in lights-out operations. Furthermore, such a program dovetails with OEE and Six Sigma practices that focus on the effectiveness and efficiency of a manufacturing facility.
Tool system suppliers often come in contact with shops that have two completely different viewpoints when it comes to live tool heads, either they are considered perishable items or everlasting solutions. Unfortunately, both of these perspectives lead to a costly mistake and one that can be avoided with the implementation of a simple PM plan.
It is difficult to quantify the exact maintenance intervals and service life for a live tool head because every shop has its own unique manufacturing methods. Plus, several application variables must be taken into consideration. These can include everything from workpiece material type, to cycle times, to coolant condition. Consider that two hours machining titanium, for example, is much harder on a live tool head than 10 hours of cutting graphite.
Five-Point PM Inspection
Proper coolant care is probably the only controllable variable, amongst all manufacturing facilities, in increasing live tool head service life. However, there is a general five-point PM inspection that EXSYS/Eppinger suggests shops perform at least every three months. And while these are just recommendations, machine operators will have to make the judgment call for exactly how often the inspections are needed based on the variables of the particular mill/turn operations at hand.
Inspection Point #1
First, measure spindle runout. Operators can determine runout by simply resting a dial test indicator tip on the inner surface of the collet pocket and rotating the live tool head. The maximum runout for live tools is around five microns in the collet pocket. Excessive runout in the spindle puts an additional load on the bearings, decreasing overall service life.
Inspection Point #2
While the dial test indicator is in the collet pocket, it is also possible to simultaneously check for radial play, the second inspection point. If movement shows up on the indicator when you toggle the spindle, then there is some sort of problem that can be anything from a bent spindle to a bad bearing.
Inspection Point #3
Ease of rotation marks the third inspection point. Live tool heads should rotate smoothly, be free of any binding, and should have no real audible noise coming from the bearings while spinning the tool.
Inspection Point #4
The fourth inspection point involves a visual inspection of the live tool head, with a particular focus on the collet pocket and the system’s drive connection, to check for any damage, wear or rust.
Inspection Point #5
If the live tool holder has an easily accessible cover plate, the operator should remove it and inspect for coolant contamination. But remember, if a live tool head is still under warranty, it should not be disassembled completely.
After PM Inspection
A down machine is an unproductive machine, and it takes little time to perform the five-point inspection that could prevent such a scenario. In fact, once an operator gets acclimated to the process, it should only take a few minutes.
It is best for operators to create and make entries in a maintenance log. Over time, operators will be able to tell when they should remove a live tool head for routine service as well as establish an accurate maintenance budget.
This log should also include information about coolant maintenance to give an idea of when the system requires cleaning.
Live heads with minor problems, such as those requiring seal and bearing replacements, should be sent out for service as many times as possible before being discarded. Keep in mind that if a live head suffers a catastrophic crash, it is most likely past the point of inspection.
Conclusion
While live tool heads only represent a small portion of the overall machining process, they are a big contributor to improving machine tool efficiency. Therefore, shops should never view them as perishable items. When properly cared for, live tool heads can deliver high value and production accuracy over a long service life—making a PM program much more important.
About the Author
subscribe now
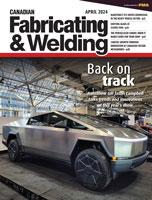
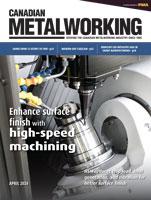
Keep up to date with the latest news, events, and technology for all things metal from our pair of monthly magazines written specifically for Canadian manufacturers!
Start Your Free Subscription- Trending Articles
Automating additive manufacturing
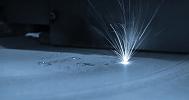
Sustainability Analyzer Tool helps users measure and reduce carbon footprint
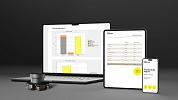
CTMA launches another round of Career-Ready program
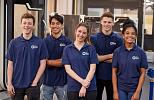
Sandvik Coromant hosts workforce development event empowering young women in manufacturing
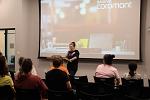
GF Machining Solutions names managing director and head of market region North and Central Americas
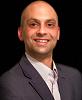
- Industry Events
MME Winnipeg
- April 30, 2024
- Winnipeg, ON Canada
CTMA Economic Uncertainty: Helping You Navigate Windsor Seminar
- April 30, 2024
- Windsor, ON Canada
CTMA Economic Uncertainty: Helping You Navigate Kitchener Seminar
- May 2, 2024
- Kitchener, ON Canada
Automate 2024
- May 6 - 9, 2024
- Chicago, IL
ANCA Open House
- May 7 - 8, 2024
- Wixom, MI