- FMA
- The Fabricator
- FABTECH
- Canadian Metalworking
SME success stories: Small parts, complex configurations
The shop makes components for the medical, telecommunications and scientific research sectors.
- By Nate Hendley
- August 21, 2014
- Article
- Metalworking
This spring, D-M Precision Products, a custom machining shop in small-town Dunnville, Ontario went on something of a machine tool bender.
“We bought one Haas VF-3 VMC along with a TR160 Platter for an existing machine and a TR160-2 Platter for a new machine,” reports Chad Plath, shop floor manager at D-M.
The shop also acquired a Hardinge Super-Precision Quest CHNC 42 turning center for small part turning.
Including the shop’s most recent purchases, D-M “currently has 10 CNC milling centers, five CNC lathes and an EDM sink and wire cutter … Haas and Hardinge brands make up around 70 percent of the machine tools on our shop floor,” reports Plath.
Founded in 1960, D-M Precision is housed in a 10,000 square foot facility. The shop makes components for the medical, telecommunications and scientific research sectors. D-M specializes in machining tight tolerances, small components and complex configurations.
The new machine tools were bought to enhance growth: D-M wants to boost its work load while maintaining on time delivery and high quality, says Plath.
[gallery type="slideshow" link="none" ids="105155,105156"]
The Haas VMC and rotary tables were installed in late April, 2014 while the Hardinge lathe was installed the first week of May.
Installation of the VF-3 took one day and “went very smoothly,” according to Dan Ferko, president of Sirco Machinery Company Limited, a Haas distributor with branches in Toronto, Montreal and Windsor.
Sirco sold D-M the VF-3 and the TR160 and TR160-2 Platters and was responsible for delivery and installation. The Hardinge turning center came from EMEC Machine Tools, a Mississauga, ON-based machine tool distributor.
As far as Ferko is concerned, D-M made a wise move in their purchase decisions.
“Clearly, based on the number of VF-3 frame-size machines that D-M runs in its day-to-day operations, the VF-3 is a very good fit for D-M,” says Ferko.
The VF-3 features x, y, z axis travels of 40 x 20 x 25 inches (1,016 x 508 x 635 mm), a 20-station carousel tool changer, 1,000 ipm (25.4 m/min) rapids and a 15 inch colour LCD monitor. The VMC table is 48 inches long by 18 inches wide (1,219 x 457 mm) and can handle a maximum table weight of 3,500 pounds (1,588 kilos). The spindle can achieve 8,100 rpm and maximum torque of 90 feet-pound @ 2,000 rpm.
D-M has very specific plans for the VF-3, which was running jobs one day after installation.
“D-M Precision currently machines parts that are what we call high complex, low volume part families. Some jobs require fifth axis rotation and run times between 180 minutes to 240 minutes per part. With the added capabilities of a twin spindle, fifth axis rotation will allow us to fixture two parts at a time and in most cases run the machines well into the evening hours as we are running one day shift (7 am – 5:30 pm) four days a week,” says Plath, of the VF-3.
[gallery type="slideshow" link="none" ids="105158,105159"]
The TR160, meanwhile, is a 160 mm (6.3 inch) tilting, two-axis trunnion rotary table with a platter diameter of 6.3 inches (160 mm). The platter can take a maximum weight of 80 pounds (36.3 kilos). Both Spindle A (tilt) and Spindle B (rotary) on the TR160 have a maximum speed of 0.001 to 80 °/sec.
The TR160-2 is a 160 mm (6.3 inch) dual spindle, tilting two-axis trunnion rotary table with a platter diameter of 6.3 inches (160 mm). Spindle A (tilt) and Spindle B (rotary) both have a maximum speed of 0.001 to 80°/sec.
The Haas VMC and rotary tables “allow us to be more productive, have better quality parts and shorter lead times,” he adds.
For its part, the Quest CHNC 42 turning center features an A2-5 16C spindle capable of 5,000 rpm, 152.4 mm (six inch) jaw chuck capacity and interchangeable 8-position or 4-position gang tool-style top plates. The CHNC 42 has a maximum turning diameter of 203 mm (8 inches), maximum turning length (with collet) of 101.6 mm (4 inches), maximum travels of 310.9 mm (12.24 inches) on the x axis and 311.2 mm (12.25 inches) on the z-axis.
The Hardinge turning center will allow D-M to “turn small parts roughly 30 percent faster with an increased value of part finishes and accuracy,” says Plath.
According to Plath, D-M staff didn’t face much of a learning curve with the VF-3.
“We currently have similar machine tools on our floor so the adjustment was minimal,” he states.
While very pleased with D-M’s current acquisitions, Plath doesn’t rule out more machine tool purchases for the rest of the year: “We are always looking at machine tools that will help us either gain new business or help with productivity,” he says.
[gallery type="slideshow" link="none" ids="105161,105160,105163"]
About the Author
subscribe now
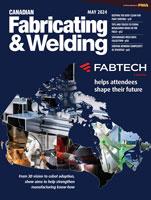
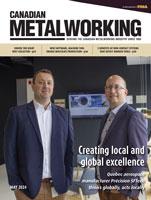
Keep up to date with the latest news, events, and technology for all things metal from our pair of monthly magazines written specifically for Canadian manufacturers!
Start Your Free Subscription- Trending Articles
Automating additive manufacturing
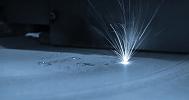
Sustainability Analyzer Tool helps users measure and reduce carbon footprint
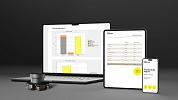
GF Machining Solutions names managing director and head of market region North and Central Americas
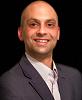
Mitutoyo updates its end-user portal
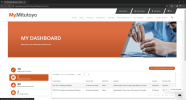
Enhance surface finish with high-speed machining
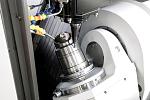
- Industry Events
CTMA Economic Uncertainty: Helping You Navigate Kitchener Seminar
- May 2, 2024
- Kitchener, ON Canada
Automate 2024
- May 6 - 9, 2024
- Chicago, IL
ANCA Open House
- May 7 - 8, 2024
- Wixom, MI
17th annual Joint Open House
- May 8 - 9, 2024
- Oakville and Mississauga, ON Canada
MME Saskatoon
- May 28, 2024
- Saskatoon, SK Canada