Editor
- FMA
- The Fabricator
- FABTECH
- Canadian Metalworking
Technology Spotlight: Large-part multitasking
Multitasking machining of large parts requires large tool capacities, temperature control
- By Joe Thompson
- August 27, 2019
- Article
- Metalworking
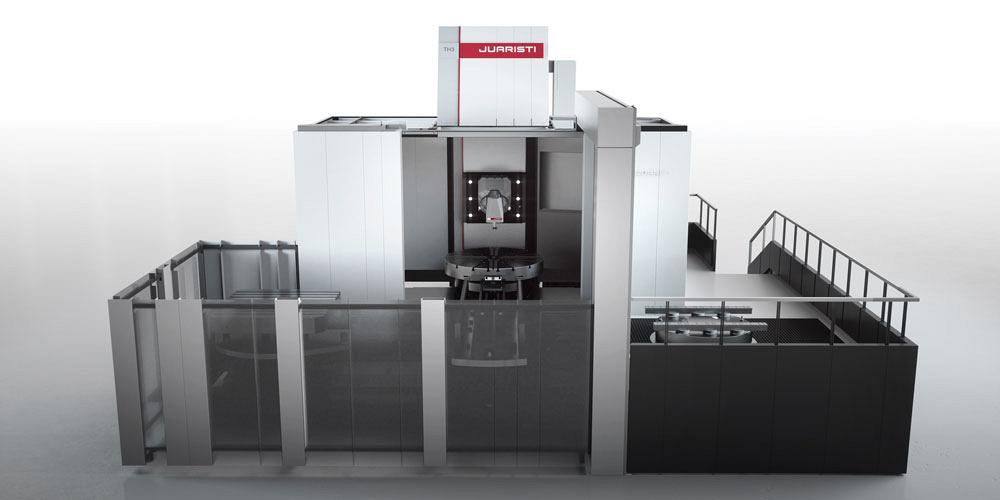
Cutting power and thermal stability of the TH3-MT are optimized thanks to the machine’s symmetrical design, including a column-centred head and four guides.
The theory of multitasking is straightforward: Combine processes in a single work envelope to increase part accuracy by eliminating setups and reduce work-in-process caused by machining parts on multiple, separate machines.
As machines evolve, more processes are being integrated into multitasking machines. This ensures that more shops can take advantage of the technology.
In the case of machine builder Juaristi, Azkoitia, Spain, this meant the development of a new multitasking platform, which will be presented at this year’s EMO fair in Hannover, Germany.
The TH3-MT multitasking machining centre combines boring, milling, and turning operations. It is suitable for many different industry segments and components, including aeronautic and aerospace (aero engine cases, structural parts), energy (hydraulic turbines, gearboxes, pumps), oil and gas (valves, compressors), die/mould, and general machining.
The new machining centre, the company’s latest development in the TH series, includes a milling and turning table and a special milling head that is optimized for milling and turning operations. The machine also includes a comprehensive automation package that, according to the company, has been redesigned to improve ergonomics, extend service life, and optimize swarf and cutting fluid management.
“In the new design, the improvement of chip and coolant management was one of the main goals in order to achieve a real autonomous machine. The design of the enclosure tries to reduce areas where chips accumulate, and coolant jets with high volume drive the chips to the chip conveyors. The high-capacity chip conveyors do the rest,” said Juaristi Technical Director Eneko Ariznabarreta.
Legacy benefits
According to Ariznabarreta, the machine continues to offer the key features of the TH series, including high dynamics (up to 40 m/min.-rapid feed with 3 m/s² acceleration) and interoperability with the next-generation high-feed and high-swarf-removal tools. Cutting power and thermal stability are optimized thanks to the machine’s symmetrical design, including a column-centred head and four guides (two front and two rear).
“The thermosymmetric concept, which is the basis of the design of the TH3-MT, is focused on keeping the accuracy in the presence of temperature changes,” said Ariznabarreta. “On top of that, main heat sources such as motors and drives are isolated, and gearboxes, bearings, and torque motors are all refrigerated by a chiller. Finally, the machine is equipped with the software to compensate the small deformations that could happen.”
Adding turning
The introduction of a new head for turning and a turning table adds significant flexibility in large, complex part production. The new head, called the ACD8, is a universal model that also allows for 5-axis machining, reaching rotation speeds of up to 8,000 RPM, with high power (60 kW) and spindle torque of 1,600 Nm.
The milling and turning table has a 5-tonne maximum part capacity in turning and 10 tonnes for milling. Rotation speeds reach 400 RPM.
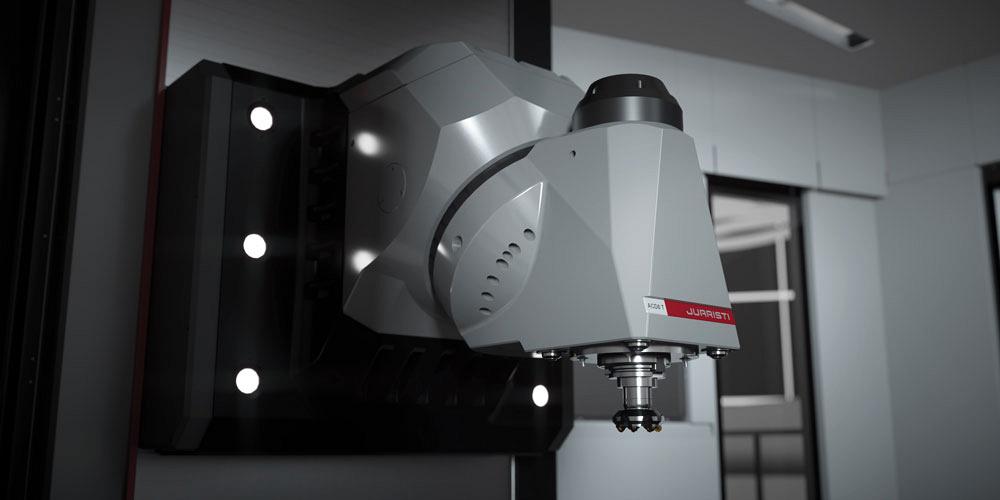
The TH3-MT multitasking machining centre combines boring, milling, and turning operations thanks to a special milling head that is optimized for both milling and turning.
“One of the main challenges in machining large parts is keeping the accuracy level in the presence of temperature changes, both room temperature and machine structure temperature,” said Ariznabarreta. Compared to small parts, big parts are really sensitive to this issue, and the current tendency is to make the tolerances narrower. The thermosymmetric structure of the TH3 is a key factor to maintain the high accuracy. On top of that, a new software package developed by Juaristi helps to improve the accuracy.”
Large parts also typically are high-cost parts, which means that zero-defect manufacturing is essential to prevent costly losses.
Large tool capacity
A quick-change matrix tool changer also is necessary for machining large parts with long cut times. This machine has the capacity to hold 200 tools and also features an FMS multi-pallet system.
“Highly automated machines enable autonomous operation, and long processes usually require a great number of tools. In many cases, the use of sister tools is necessary because of the life of the cutters. With 200 tools the machine can work without the intervention of the operator refreshing the tools. On top of that, if the machine is combined with a multi-pallet system, a large number of tools are even more important to perform different works, for example, over the weekend,” said Ariznabarreta.
Another design enhancement is the stainless steel housing of the fully enclosed guarding, which protects and extends the life of the machine. The ergonomics of the machine gives the operator control of operations, machine monitoring, and maintenance with maximum safety.
Measuring probes are standard in all machines, and automatic measuring cycles enable part quality to be tested during machining.
“There is of course a concept issue that has to be overcome. If measurement is carried out with the same strategy (and machine) as the machining, the error will be copied and not noticed,” said Ariznabarreta. “That is why we are working on different options to offer customized technology depending on the accuracy level the customer needs and the investment level they can assume.”
This measuring technology starts with automatic machine verification cycles that certify the machine, which means that the measurement is also certified; automatic measuring cycles, which perform the measurement with a completely different strategy from the one used for machining (using alternative axes or paths); and the integration of the laser tracker technology in milling heads.
Editor Joe Thompson can be reached at jthompson@canadianmetalworking.com.
Juaristi, www.juaristi.com
About the Author
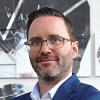
Joe Thompson
416-1154 Warden Avenue
Toronto, M1R 0A1 Canada
905-315-8226
Joe Thompson has been covering the Canadian manufacturing sector for more than two decades. He is responsible for the day-to-day editorial direction of the magazine, providing a uniquely Canadian look at the world of metal manufacturing.
An award-winning writer and graduate of the Sheridan College journalism program, he has published articles worldwide in a variety of industries, including manufacturing, pharmaceutical, medical, infrastructure, and entertainment.
Related Companies
subscribe now
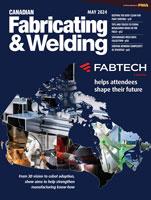
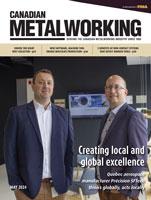
Keep up to date with the latest news, events, and technology for all things metal from our pair of monthly magazines written specifically for Canadian manufacturers!
Start Your Free Subscription- Trending Articles
Automating additive manufacturing
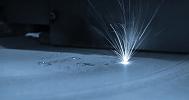
Sustainability Analyzer Tool helps users measure and reduce carbon footprint
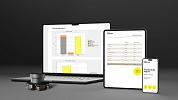
GF Machining Solutions names managing director and head of market region North and Central Americas
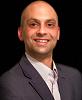
Mitutoyo updates its end-user portal
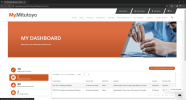
Enhance surface finish with high-speed machining
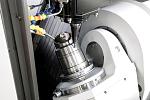
- Industry Events
CTMA Economic Uncertainty: Helping You Navigate Kitchener Seminar
- May 2, 2024
- Kitchener, ON Canada
Automate 2024
- May 6 - 9, 2024
- Chicago, IL
ANCA Open House
- May 7 - 8, 2024
- Wixom, MI
17th annual Joint Open House
- May 8 - 9, 2024
- Oakville and Mississauga, ON Canada
MME Saskatoon
- May 28, 2024
- Saskatoon, SK Canada