- FMA
- The Fabricator
- FABTECH
- Canadian Metalworking
Technology Spotlight: Mass finishing of 3D printed parts
Finishing system creates smoothness and luster in one step
- By Canadian Metalworking
- October 1, 2020
- Article
- Metalworking
Walther Trowal, Haan, Germany, has developed an additive manufacturing (AM) post-process machine, model range AM, for refining the surface of components produced with AM.
Most 3D-printed components are produced by placing material layers on top of each other, creating a “staircasing” effect on their surface with, generally, a very high initial surface roughness. For this reason, many of these components must undergo a surface smoothing or polishing operation. Also, most of the time the markings of removed support structures and sintered-on powder residue must be removed before the components can be further processed or utilized.
Mass finishing now is a suitable method of surface finishing for 3D-printed components, the company states.
Parts are completely embedded in the moving grinding media, a gentle process that produces homogeneous and repeatable surface finishes. Moreover, the media also reaches internal passages and undercuts in the components.
The AM Post-process
Depending on the size of the processing bowl, up to 100 small workpieces with a size of 900 by 500 mm can be treated in the machine’s multivibrators. The workpieces are mounted on a carrier plate, which in turn is clamped to the bottom of the processing bowl by mechanical or electromagnetic means. Once the workpieces are in place, the media is filled into the processing bowl. During the process a compound and water are continuously added.
Three vibratory motors induce an intensive vibration into the processing bowl. Because the vibratory movement generated by the motors is overlapping, the component surface becomes smoother, while the edges are left intact. After a predetermined cycle time, the process is completed and the finished workpieces can be removed.
These machines reduce the surface roughness of raw workpieces from around Ra = 2 to 80 µm down to a value of 0.025 µm.
“Additive manufacturing and mass finishing are an ideal combination because most 3D-printed components must have an excellent surface finish to fulfill their function,” said Maximilian Beien, sales manager at Walther Trowal. “For example, turbine blades require an airflow with minimal friction loss. Components with stringent specifications for hardness and strength benefit from the homogeneous peening effect induced by mass finishing. This finishing method is especially advantageous for 3D-printed components with bionic shapes.”
Bionic shapes are shapes found in nature that are inspired by biological structures.
Numerous Workpiece Materials
Mass finishing is suitable for numerous materials commonly used in AM, including high-performance, difficult-to-machine metals like titanium, nickel-based and cobalt-chrome alloys, non-ferrous metals, and plastic.
“Compared to electrochemical finishing methods, mass finishing achieves the desired surface smoothness and luster in one single operation. Another advantage is that the mass finishing equipment is very compact with a small footprint. The result is an excellent surface finish, surprisingly short cycle times, and an overall high cost efficiency not only with regard to the capital expenditures, but also the operating costs,” said Beien
Topologically optimized workpieces with complex – frequently bionic – shapes often have difficult-to-reach internal passages. Manual finishing of these surface areas is not possible, especially when the workpieces are subject to strict safety and manufacturing standards, which is the case in the aerospace industry. Moreover, 3D printing is already used for serial manufacturing with continuously increasing production volumes.
Tailored Approach
The optimum parameters for the finishing process are determined through processing trials conducted by process engineers at the Walther Trowal test centre. The trials also include the selection of the most suitable grinding or polishing media and compound. The process parameters for every single workpiece are stored in the PLC and can be retrieved at any time.
“Compared to other finishing systems, the single-stage process facilitates and shortens the surface finishing operation significantly,” said Michael Becker, manager of the Walther Trowal test centre. “Of course, the finishing operation can be further optimized, when all surface treatment considerations are already taken into account during the design phase for the 3D-printed components and the parameterization of the printer. For example, this applies to determining the material layer thickness and the material feed rate of the printer. We gladly support our customers in resolving these issues.”
Walther Trowal, walthertrowal.com
About the Author
subscribe now
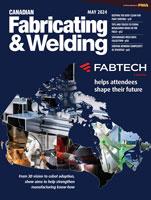
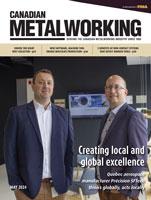
Keep up to date with the latest news, events, and technology for all things metal from our pair of monthly magazines written specifically for Canadian manufacturers!
Start Your Free Subscription- Industry Events
Automate 2024
- May 6 - 9, 2024
- Chicago, IL
ANCA Open House
- May 7 - 8, 2024
- Wixom, MI
17th annual Joint Open House
- May 8 - 9, 2024
- Oakville and Mississauga, ON Canada
MME Saskatoon
- May 28, 2024
- Saskatoon, SK Canada
CME's Health & Safety Symposium for Manufacturers
- May 29, 2024
- Mississauga, ON Canada