- FMA
- The Fabricator
- FABTECH
- Canadian Metalworking
Technology Spotlight: Next-generation gundrilling machines
Deep-drilling machines come as automation-ready systems
- By Canadian Metalworking
- November 4, 2020
- Article
- Metalworking
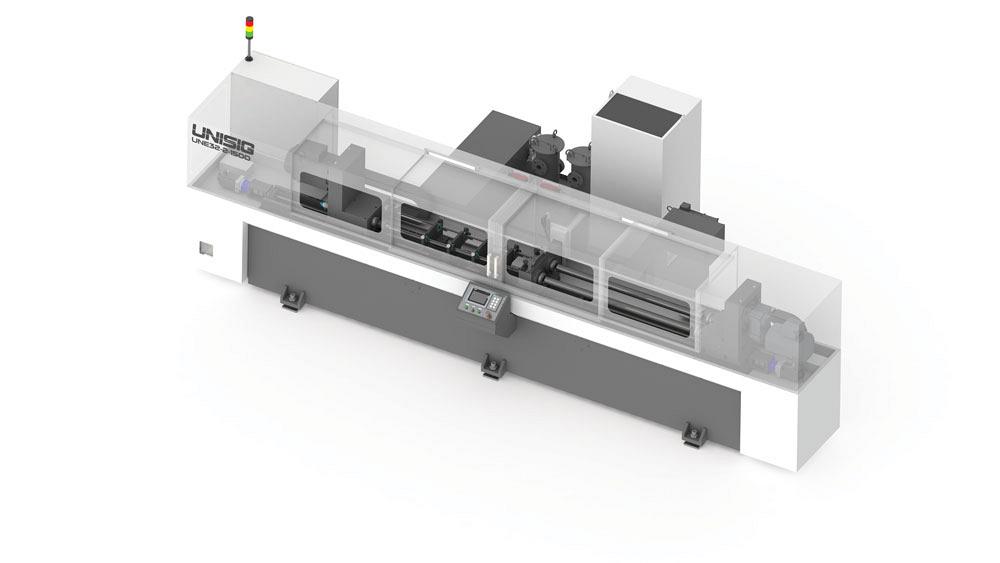
Unisig’s next generation of UNE series gundrilling machines deliver operational flexibility and improved performance.
Suitable for manufacturers with high-volume/low-mix or low-volume/high-mix production environments, Unisig’s next generation of UNE series gundrilling machines deliver operational flexibility and improved performance.
The new generation is engineered and designed to simplify gundrilling operations. These machines are suitable for numerous industries, including firearms, automotive, medical, energy, defence, and aerospace.
With five models built from two frame sizes, these machines can drill hole diameters from 1.4 to 40 mm and depths up to 3,000 mm. The compact frame construction saves valuable floor space as well. Each machine can fit in close proximity to a shop’s existing equipment for efficient part-processing strategies.
Automate Today or Tomorrow
Built with quick and simplified setup in mind, the machines are also small enough to be relocated when necessary. For added flexibility to grow with future production needs, all models are robot-ready, allowing shops to add a robot whenever it fits into their budget and production schedule.
“Our feature-rich UNE machines give customers a compact gundrilling solution equipped with the ability to grow alongside them,” said Anthony Fettig, CEO of Unisig. “A lot of job shops and OEMs have the desire to automate but lack a timeline to do so. Our UNE series gives them gundrilling benefits for today. It also provides them with security for tomorrow knowing that they can further improve production by adding automation.”
Several features contribute to the performance and productivity of these machines.
Spindle servomotor. The single main spindle servomotor delivers the necessary horsepower for two-spindle machines. When power is applied in single-spindle mode, however, shops can produce larger-diameter holes to increase their capabilities and add new business without purchasing a new machine.
Programmable coolant flow. Instead of a pressure-based coolant system,these gundrills have a programmable, flow-based coolant delivery system designed to provide the right amount of coolant to the tool’s cutting edge. The end result for the operator is their ability to predict tool breakage and spend less downtime recovering an interrupted process, the company states.
Intuitive control. Powered by Siemens, these machines have intuitive controls that give operators a full process picture at a glance on a colour interface with touchscreen capability. The control’s heavy-duty buttons also function well when operators are wearing gloves.
Automated door. Ergonomically designed and engineered with the building owner and operator in mind, the machines offer an automated door option, which can benefit companies with or without automation.
“Adding an automated door eliminates the repetitive task of opening and closing machine doors,” said Fettig. “Not only does this reduce fatigue, but it improves throughput and gives the operator an opportunity to focus on adding value in other areas.”
Simplified installation. All machine bases are FEA-optimized and machined on five sides in a single setup for high overall precision. This allows for simplified installation with no foundation work required, and three-point levelling on machines rated up to 1,000 mm length.
UNE Series Overview
- Three two-spindle models available with maximum hole diameters of 12, 20, and 32 mm. Hole diameters can be even greater when used in single-spindle mode.
- Two single-spindle models available with maximum hole diameters of 25 and 40 mm.
- Five rated workpiece designation options between 750 and 3,000 mm.
- Solid-carbide, brazed, and indexable gundrill tools.
- Automation-ready.
Unisig
About the Author
subscribe now
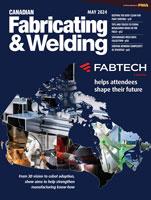
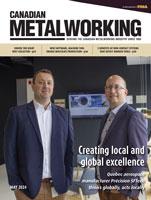
Keep up to date with the latest news, events, and technology for all things metal from our pair of monthly magazines written specifically for Canadian manufacturers!
Start Your Free Subscription- Industry Events
Automate 2024
- May 6 - 9, 2024
- Chicago, IL
ANCA Open House
- May 7 - 8, 2024
- Wixom, MI
17th annual Joint Open House
- May 8 - 9, 2024
- Oakville and Mississauga, ON Canada
MME Saskatoon
- May 28, 2024
- Saskatoon, SK Canada
CME's Health & Safety Symposium for Manufacturers
- May 29, 2024
- Mississauga, ON Canada