Editor
- FMA
- The Fabricator
- FABTECH
- Canadian Metalworking
Technology Spotlight: Your coolant system is emailing you
Automatic coolant management is the last link in the autonomous manufacturing chain
- By Joe Thompson
- November 3, 2023
- Article
- Metalworking
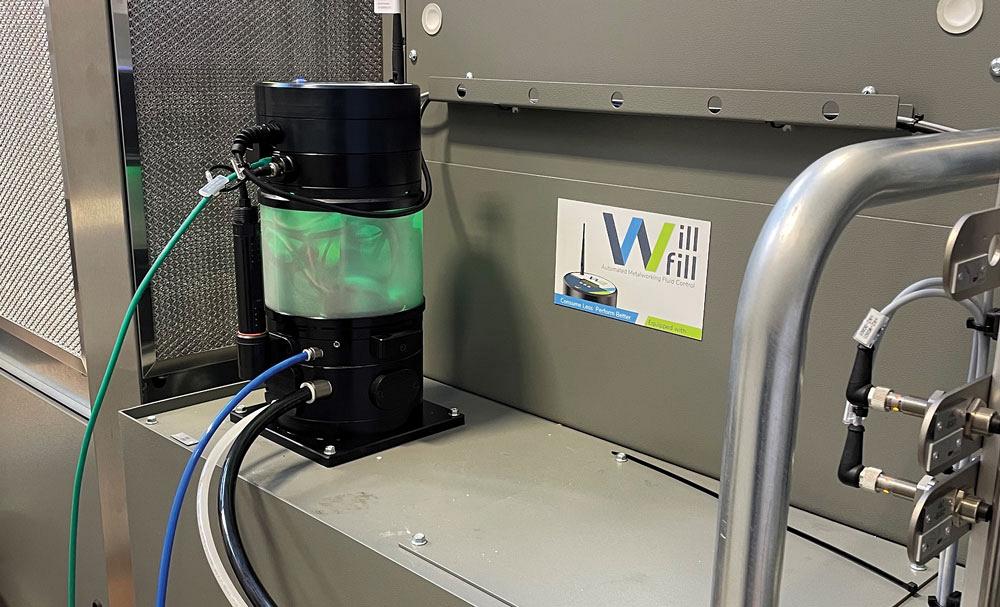
The Will-Fill Premium Coolant Controller automatically measures and analyzes a machine’s coolant mix, determining coolant tank level and refilling it if necessary with the proper coolant concentration, and conditioning the coolant before adding it to the machine’s tank.
Connected technology is ubiquitous in everyday life. And as manufacturers continue to develop digitalization and automation strategies, the use of this technology will only increase.
One aspect of shop floor operation has seen only small steps toward this automated, connected future, however. The missing element to a totally integrated and automated metal cutting operation is its coolant management and maintenance. Until now.
The Will-Fill Premium Coolant Controller, available from Jorgensen Conveyor and Filtration Solutions, Mequon, Wis., manages every aspect of coolant use. It automatically carries out multiple tasks including measuring and analyzing a machine’s coolant mix, determining coolant tank level and refilling it if necessary with the proper coolant concentration, and conditioning the coolant before adding it to the machine’s tank.
The system then manages and records the accumulated data that is available to users to download. It also provides digital connectivity via a cloud interface that allows users to view all measurement data and analysis online and route specific information to relevant parties.
Automating Coolant Management
“Today, in many factories, fluid management is a very manual process,” explained Karl Kleppek, president/COO of Jorgensen Conveyor and Filtration Solutions. “In most cases, a refractometer is used to measure the coolant concentration. Then, based on the findings, a calculation is made taking the estimated amount of emulsion [coolant and water mixture] that is left in the tank to determine the appropriate mix of new coolant and water emulsion that will be added to the coolant tank, so the new resulting mixture meets the emulsion specification for proper lubricity.”
New mixtures are manually added to individual machine tool coolant tanks, which should not be done while a machine is running because much of the machine’s available coolant is in use and pumping through the coolant circuit.
“Using Will-Fill, the unit does the measuring, the calculations, and the refill automatically and can be programmed to determine the frequency of measurement and the timing of when the measurements take place based on the machine status,” said Kleppek.
The unit also measures the coolant’s PH level, temperature, oil/water mix concentration, water hardness (EC), and oil and water usage. A mixing unit ensures new coolant is properly mixed in the tank. It also is programmable, so it can condition the coolant tank even when the machine is not in use, which helps reduce bacterial growth.
Using that data, the system performs automatic topping up and refilling and adjusts the coolant mix to the desired concentration. An automatic proportional-integral-derivative (PID) controller adjusts the oil dosing process. Based on coolant condition data that may vary depending on the shop temperature, for example, the system will mix an emulsion that best supports the particular metal cutting operation and workpiece material machining characteristics at hand.
Developed by Dierickx Tools, this coolant management system was designed to minimize the vulnerability of its sensors to coolant residue, which can affect sensor accuracy. As a result, the system is able to perform between 400 and 1,000 measurements before manual cleaning of the sensors is necessary.
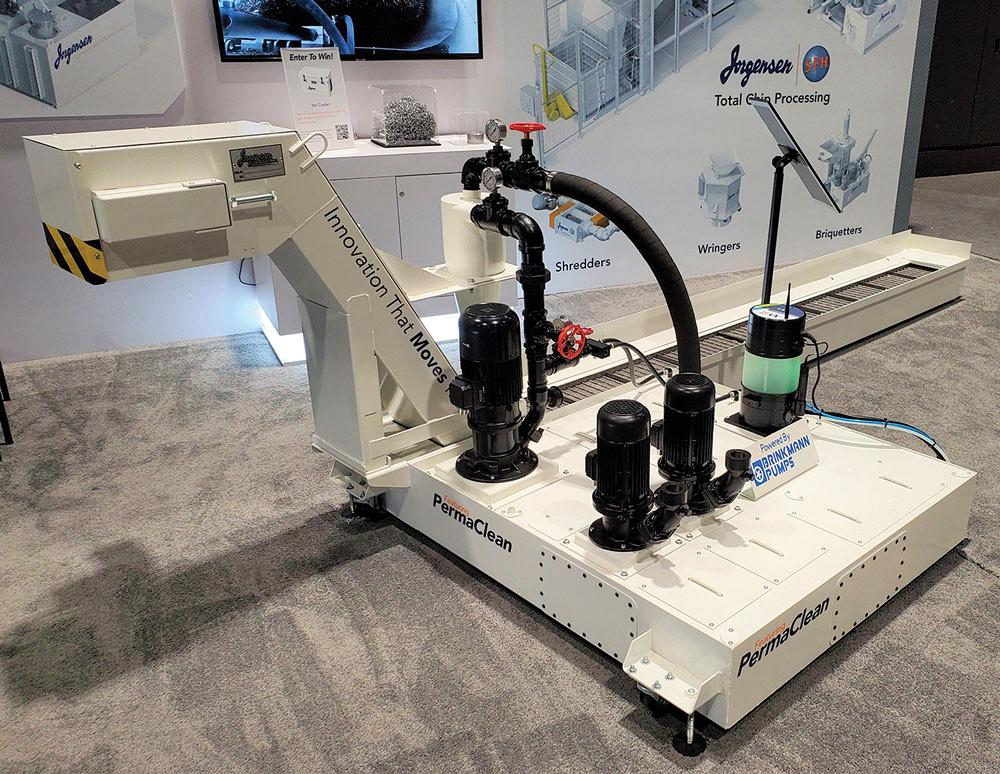
A Jorgensen PermaClean system with Will-Fill combine to create a maintenance-free coolant system by eliminating sludge buildup and monitoring the system for proper coolant concentration.
The design of the system also is aimed at efficiency improvement. When water and oil are added in combination, the system mixes them before they are added to the coolant tank to ensure the emulsion is homogeneous. This same circulation and mixing unit is used for regular conditioning of the coolant. By moving the coolant around, it has no time to settle, and anaerobe bacteria cannot grow, resulting in increased coolant lifespan.
The unit is mounted on the top of a machine tool’s coolant tank. Mounting requires a 180-mm opening on the coolant tank, and the unit itself is 200 by 200 by 500 mm in size. Eight different models are available to detect level fluctuations from 120 to 820 mm, depending on the depth of the machine’s sump. Mixing capacity is +/- 800 litres per hour.
The setup ensures that proportions of oil and coolant are added independently of each other before mixing them with existing coolant. This is critical, especially when cutting materials like titanium, where the water tends to evaporate faster, making the coolant replacement required to reach desired concentration consisting largely of water.
Installation of the system does require a water source. Another hose from the unit feeds a shop’s standard coolant from a barrel located near the machine.
Connected Manufacturing Technology
The unit has both Wi-Fi and LAN connections. With those, it provides real-time information and fulfills customer needs for traceability. The data is routed to a cloud server for storage or for presentation on a graphical dashboard for online monitoring. This includes collected data on actual water and oil consumption because many shops have only vague knowledge of their actual water consumption, which can become a significant business cost factor that will rise in importance as water becomes a scarcer resource.
The system’s automation and connectivity facilitate implementation of productivity strategies such as lights-out machining. Automatic monitoring of coolant application allows instant cloud notifications to be sent in case of anomalies that can interrupt unattended production. Additionally, because the data management is a cloud-based system, users can send emails immediately to appropriate staff members when unexpected events like a dirty sensor, an empty oil barrel, and an unexpectedly closed water tap occur.
Automated coolant management also enables use of supplementary coolant-related systems, including Jorgensen’s PermaClean filtration system. These filtration systems help eliminate tank sludge, reducing the labour required for tank cleanings. Plus, when combined with the cyclonic filtration option and a Will-Fill, the system is fully automated and nearly maintenance free, the company states.
As an additional benefit, automating coolant management enables shops to reduce health risks associated with coolant handling and to apply its labour force more efficiently. If coolant maintenance tasks for a machine require three hours per week, for instance, that is time an operator will not be machining parts.
“There are lot of costs associated with proper coolant maintenance,” said Kleppek. “First, there is the cost of the manual process, which is the cost of an employee managing the manual process of measurement, calculation, and refill. This could even be a full-time job depending on the number of machines and the frequency of measurement, which should be--at the least—occurring daily. Second are the costs of the problems that come from improper coolant concentrations.”
4 Benefits of Having Proper Coolant Concentration
- Reduces Tool Costs. Proper coolant concentration provides adequate lubricity for machining applications and lengthens tool life. Improper concentrations lead to shorter tool life, which increases tooling spend.
- Creates Better Finishes and Reduces Scrap. Improper coolant concentration reduces tool effectiveness and reduces cooling capabilities, which results in poor part finishes and, in some cases, increases the amount of scrap caused by out-of-spec parts.
- Reduces Machine Flooding. Emulsions without proper concentration levels can foam, and in many cases, cause flooding, which may require shutting down a machine to clean up.
- Reduces Bacterial Growth. Improper concentrations lose their effective bacteria-fighting capabilities, resulting in rancid smelling coolant and skin irritation.
One Big Question
Q: Can this technology help shops ease into a more automated, data-centric operating style?
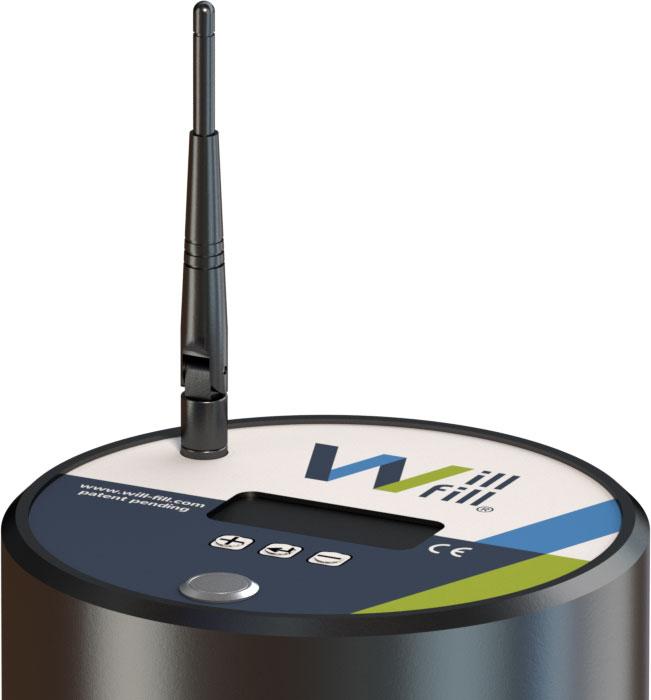
The Will-Fill unit has both Wi-Fi and LAN connections to provide real-time information and fulfill any customer need for traceability.
Kleppek: Absolutely. There is a very well-designed wizard, which makes start-up and configuration of the unit easy and straightforward. It fits in practically any tank and only needs a small cut-out to be placed in a tank. And, finally, the data that is available from the unit is configurable, so important filling and monitoring data is easy to access.
Editor Joe Thompson can be reached at jthompson@fmamfg.org.
Jorgensen Conveyor and Filtration Solutions, www.jorgensenconveyors.com
Will-Fill, www.will-fill.com
About the Author
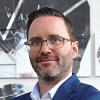
Joe Thompson
416-1154 Warden Avenue
Toronto, M1R 0A1 Canada
905-315-8226
Joe Thompson has been covering the Canadian manufacturing sector for more than two decades. He is responsible for the day-to-day editorial direction of the magazine, providing a uniquely Canadian look at the world of metal manufacturing.
An award-winning writer and graduate of the Sheridan College journalism program, he has published articles worldwide in a variety of industries, including manufacturing, pharmaceutical, medical, infrastructure, and entertainment.
Related Companies
subscribe now
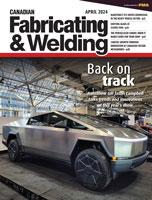
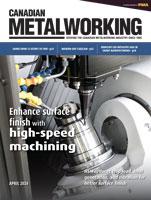
Keep up to date with the latest news, events, and technology for all things metal from our pair of monthly magazines written specifically for Canadian manufacturers!
Start Your Free Subscription- Trending Articles
Automating additive manufacturing
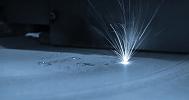
Sustainability Analyzer Tool helps users measure and reduce carbon footprint
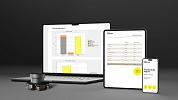
CTMA launches another round of Career-Ready program
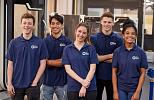
Sandvik Coromant hosts workforce development event empowering young women in manufacturing
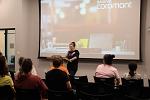
GF Machining Solutions names managing director and head of market region North and Central Americas
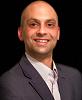
- Industry Events
MME Winnipeg
- April 30, 2024
- Winnipeg, ON Canada
CTMA Economic Uncertainty: Helping You Navigate Windsor Seminar
- April 30, 2024
- Windsor, ON Canada
CTMA Economic Uncertainty: Helping You Navigate Kitchener Seminar
- May 2, 2024
- Kitchener, ON Canada
Automate 2024
- May 6 - 9, 2024
- Chicago, IL
ANCA Open House
- May 7 - 8, 2024
- Wixom, MI