- FMA
- The Fabricator
- FABTECH
- Canadian Metalworking
The many angles of centerless grinding
This extremely effective grinding process relies on basic geometry for high precision and high-volume applications.
- By Canadian Metalworking
- May 18, 2015
- Article
- Metalworking
It’s not uncommon to find centerless grinding machines in operation today that have been running for decades. A precision grinding process suited to any cylindrical part that requires a tight tolerance, centerless grinding machines have few moving parts and perform their grinding magic through a miracle of basic physics. What’s really changing with today’s more modern machines is the addition of computer controls that take a very efficient process and make it even more productive.
Centerless grinding is an outer diameter finishing process that is revered for maintaining a high tolerance for roundness on metal parts and working very quickly, making it ideal for high-volume applications. And it’s the relative simplicity of centerless grinding that separates it from other cylindrical grinding technologies.
At first glance the process appears almost primitive. The part to be ground is simply placed on a workpiece rest blade that is situated between two rotating cylinders: a regulating wheel (made of a dense rubber compound that controls the rotational speed and feed rate of the workpiece) and the larger abrasive grinding wheel.
The part simply sits on the work rest blade, no fixturing involved, and then the rotating regulating wheel engages and spins the part at one speed while pushing it towards the larger grinding wheel that’s spinning even faster—the greater the difference in speed the faster the removal rate.
As unlikely as it may seem, the workpiece is held in place simply by the pressure of the rotating wheels. With the wheels rotating at speeds above 30 rpm, it’s a wonder the parts are not flying out of the machine. But it all comes down to geometry, explains Harry Schellenberg, founding partner of Echo Hill Automation in Beamsville, Ontario, manufacturer of the Tactic 8 centerless grinding machine.
“Centerless grinding is really good at making round parts, because of the geometry that’s involved in it,” says Schellenberg.
To get that roundness the angles that the wheels contact the part are critical.
In most cases the centers of the opposing regulating and grinding wheels are set at the same height on the machine, and the work rest blade is designed so the center of the workpiece sits slightly above the centerline of the wheels. By creating a triangular relationship among the centers of the two wheels with the center of the workpiece at the apex, the force being applied to the part by one wheel is never directly applied to the opposite side of part on the other wheel. This principle allows for the precise roundness to be achieved.
“As long as you have good spindles you’re going to make a round part if your geometry is right,” says Schellenberg. He adds that you can also take a part that’s out of round from a turning machine and achieve roundness in a centerless grinding machine.
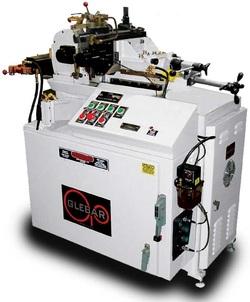
The Glebar GT-610M is a compact centerless grinding system with an 8-5/8” wide grinding wheel built for machine shops. WWW.GLEBAR.COM
Because of the relative simplicity of the process, the speed of centerless grinding is also one of its primary advantages. “You don’t have to fixture each part,” notes Schellenberg. “You simply set it in place, the wheels come together, grind the part and you’re done.”
For this reason, anywhere high volumes of small cylindrical parts are required makes this process a prime candidate. Industries that demand the tolerance and roundness of centerless grinding include aerospace, automotive, defense and medical.
The bolts in a motorcycle chain for instance are ground, notes Ralf Scheurl, sales manager with Mikrosa, the centerless grinding unit of the United Grinding Group. “That’s a lot of bolts,” he says, adding “The centerless grinding process is very good at putting parts into buckets.”
And it’s the consistency of the process; its ability to maintain its tolerance within microns that makes it first class. “I have a background of grinding parts between centers,” says Scheurl, referring to where a workpiece is clamped between two centers before grinding. “When I first came in contact with Mikrosa (centerless grinding) I couldn’t believe it. You can’t compare it with grinding between centers.”
The set up for a centerless grinding job requires first selecting a grinding wheel suited to the metal and the desired surface finish. Tooling required for set up includes a custom work rest blade to suit the part. As mentioned, the height of the work rest blade is critical. The top of the work rest blade generally has an angle of 30-degrees sloping towards the regulating wheel. This keeps the part in contact with—and rotating at the slower speed of—the regulating wheel.
There are two ways centerless grinding machines operate, either infeed (also called plunge grind) or throughfeed.
The infeed is used to grind cylindrical workpieces with notches or complex shapes, such as gear shafts. In the setup, the work rest blade needs to be tooled to match the shape of the part. The grinding wheel and regulating wheel must also be dressed—having the part’s desired profile cut into them with a stationary diamond or diamond wheel (this process is done on the machine and takes some time).
To begin, the workpiece is placed on its customized work rest blade, coolant flows, the wheels engage the part, sparks fly, and in seconds the part is removed and the next workpiece is set in place. As the grinding wheel wears it will need to be redressed on an ongoing basis.
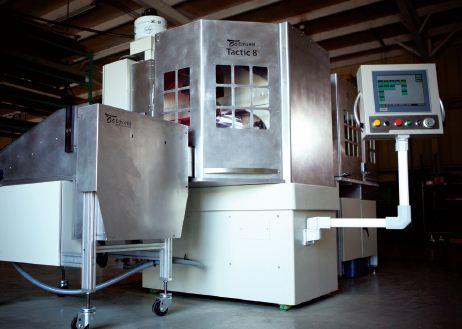
The Tactic 8 centerless grinding system with an 8-inchwide wheel, designed and manufactured by Echo Hill Automation in Beamsville, Ontario is an integrated cell with auto handling, gauging and closed-loop accuracy controls. WWW.ECHOHILLAUTOMATION.COM
For throughfeed grinding, the workpiece travels along the rest blade between the grinding and regulating wheel. The part is driven through by a slight angle applied to the regulating wheel relative to the grinding wheel, basically squeezing the workpiece across the grinding wheel and out the other side. A throughfeed set up is typically used for parts with a consistent roundness across the length of the part.
While centerless grinding machines have been around for decades, new technologies continue improving the process. The introduction of CNC controls and direct drive motors are reducing the time and complexity of the setup and enhancing the already tight tolerance holding capability.
Robotic automation to load and unload the workpieces is also speeding up the process and ensuring accuracy, while automated gauges, set up at the delivery end to measure part diameters are ensuring accuracy and keeping the variance from part to part in the low micron level. These advancements are all making centerless grinding a cut above when it comes to finishing round parts.
About the Author
subscribe now
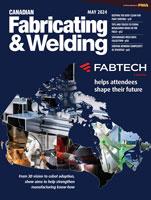
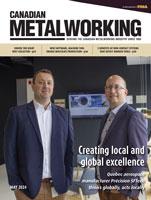
Keep up to date with the latest news, events, and technology for all things metal from our pair of monthly magazines written specifically for Canadian manufacturers!
Start Your Free Subscription- Trending Articles
Sustainability Analyzer Tool helps users measure and reduce carbon footprint
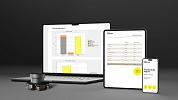
Enhance surface finish with high-speed machining
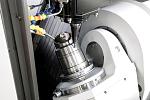
Equispheres secures $20 million investment round
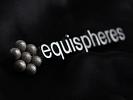
Solid carbide drills produce precision holes in short chipping materials
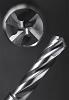
Okuma announces new personnel appointments
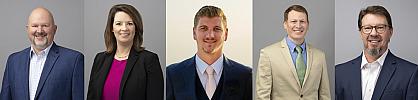
- Industry Events
Automate 2024
- May 6 - 9, 2024
- Chicago, IL
ANCA Open House
- May 7 - 8, 2024
- Wixom, MI
17th annual Joint Open House
- May 8 - 9, 2024
- Oakville and Mississauga, ON Canada
MME Saskatoon
- May 28, 2024
- Saskatoon, SK Canada
CME's Health & Safety Symposium for Manufacturers
- May 29, 2024
- Mississauga, ON Canada