- FMA
- The Fabricator
- FABTECH
- Canadian Metalworking
Toolholder trouble
How to avoid it!
- By Nate Hendley
- March 25, 2015
- Article
- Metalworking
Want to avoid toolholder trouble? The first step is recognizing the importance of toolholders in the manufacturing process. While toolholders are the vital link between machine and cutting tool, they are all too often overlooked and abused.
“Here’s a scenario: I’m buying a new machine tool. I spend a lot of time with the machine builder looking at different designs. I pick out the one that has the best criteria within my affordability. I make the choice of that machine. And I’ve already had a lot of time spent looking into what types of cutting tools I buy … but when the machine’s on its way in, that’s when all of a sudden I think, ‘Oh, I’ve got to get some new toolholders.’ Or maybe I just find some lying around. [The toolholder] becomes the afterthought,” says Dave Hartman, senior product manager rotating products, Parlec in Fairport, New York.
Customers “don’t understand the importance of the interface. The toolholder is the connecting device between two precision elements. It’s important to make sure that the toolholder is seen as importantly as the other two elements,” Hartman continues.
“A lot of time and effort is spent specifying high dollar machine tools and the vital toolholder and workholding systems which we outfit these precision machines with are often forgotten,” agrees Matt Panosh, group manager tooling at Schunk in Morrisville, North Carolina.
“In most cases, the toolholder is the most critical part of the system…a cheap toolholder gives you cheap results,” echoes David McHenry, engineering and technical manager at REGO-FIX Tool Corp. in Indianapolis, Indiana.
“You buy a half-million dollar machine. You put a junk holder on it. The holder falls apart and breaks the turret,” adds Leigh Bickham, general manager at ITI Group in Ramsey, New Jersey.
Hartman cites another scenario in which a machinist tests a brand-new, expensive cutting tool. A salesperson has promised definitive results. When the machinist puts the cutting tool to the test, however, he grabs the first toolholder he can find, regardless of how old, worn or cheap it is. The machinist is disappointed with the results of his test and blames the cutting tool, rather than the toolholder. This outcome could have been avoided had the cutting tool
been matched with a better toolholder in the first place.
So, with all this in mind, what characteristics should you look for in a toolholder?
“There are three key components you should always consider when choosing a toolholder. A toolholder should have good run-out/repeatability, good balance qualities and be easy to use. These three key components are the gateway to increasing toolholder knowledge and cost savings,” says Panosh.
Other important characteristics include vibration dampening, increased radial stiffness, length adjustment or adjustable run-out, he adds.
This list comes with a caveat: “Depending on the job you’re doing, one of these features will be more important. So, for me to say concentricity is the most important, that’s true if you’re doing high speed machining of a relatively fine nature—meaning a precision, high-speed machining job. But if you’re doing a big piece of titanium air frame, you really need rigidity and non-pullout capability. So, all of [the features cited] are important, but everybody’s level of importance changes based on what they’re doing,” explains Hartman.
A best practice is to “look at the application as a whole” before selecting a toolholder, says Panosh.
“What is the capability of my machining center? How am I processing the part? What is my application: milling, drilling, reaming or threading? Have you considered clearance? The toolholder profile is critical when working with five-axis machines or mill-turns. All of these things come into play. In addition, a job shop may look at part processing differently than an OEM,” he states.
Acquiring a decent toolholder is only the first step, however, in the proper care and handling of such devices. Even if a machinist avoids the temptation of purchasing bargain basement toolholders, rough handling and improper cleaning can also spell disaster.
Machinists see toolholders “as something that lasts forever. And how long does a toolholder last? Well, it depends. If you’re routing a piece of sheet metal, the tool may be in the spindle for eight hours and you may only do one of those parts a week. You may have a total of one tool change per week and [the toolholder] could last forever. But if you’re using a much smaller workpiece, doing six parts per minute, and you might have a tool change 30 times a day, that’s going to wear out [the toolholder] much quicker,” says Hartman.
“A lot of times what happens, the end-users forget what it takes to maintain the tooling … a lot of the times the cleaning aspect is very much forgotten about because they need that tool, they need it now and don’t have time to clean it. They might grab a rag out of their pocket, wipe [the toolholder] off, put it back together. Then they wonder, ‘What happened? Why am I getting bad results?’ If you want to hold a tool to tenths or microns of run-out, you have to clean it,” adds McHenry.
That said, neglectful toolholder maintenance is sometimes simply the end-result of running full-out operations.
“Most of the time, the plant manager looks at a down machine as losing money. To put a machine [off-line] to take the toolholder out to inspect it and rebuilt it, is very rare [in my experience],” says Bickham.
Over-torqueing retention knobs is another common mistake.
“Over tightening of the retention knob can affect the performance of a toolholder. We have inspected toolholders for run-out or vibration only to find that the retention knob has been over tightened and deformed the taper,” says Panosh.
“The other issue is doing the same thing to a collet chuck. If you over-torque a retention knob on a steep taper you can swell the nose of your toolholder … because of the risk of something coming loose—which would be catastrophic—you get people using the adage, ‘Tight is good, tighter is better.’ What we recommend is not to over-tighten them but to use a serviceable thread lock … that will allow it not to come loose,” says Hartman.
Other pointers: the type of cutting tool being used will determine the type of toolholder that should be matched with it.
“If I have a jobber high speed steel drill, I’m going to use a standard collet system. If I have a $300 G drill, I’m going to use a high performance, high precision holding system. If I’m using a high speed steel end-mill with a Weldon flat, I’m going to use a Weldon toolholder. If I’m using a high helix carbide solid carbide round tool, I’m going to use a high performance, high precision holding system … the cutting tool should define the type of toolholder system you use,” says Hartman.
The material being worked on can also influence toolholder preference.
“As far as the actual material you’re cutting, sometimes the easiest tools to machine are the worst for the toolholder. For instance, when you’re machining aluminum, it’s soft, but it can turn the coolant into mud [which] can get lodged in all sorts of places. With a hardened steel ... you don’t get it muddying the coolant as much,” says Hartman.
In terms of the type of material being worked on, “again, you have to look at the application and process as a whole. I may choose a different toolholder to cut a material on a high speed machine than I would on a machine with a lot of horsepower.
A vertical machining center may have different toolholder requirements than a horizontal. For example, a horizontal may require a minimum gage length of six inches just to reach the part. In this scenario, due to the length, in a rough milling application you’re going to want [a toolholder] with good radial stiffness as well as good clamping force. A balance of them both,” adds Panosh.
Experts cite other important toolholder characteristics: “in general, most customers want rigidity. They don’t want the tool to deflect. When they go to setup and optimize their process, they know what that toolholder can give them. If you can find a toolholder that is rigid and has some vibration dampening to it at the same time, it’s golden,” says McHenry.
Anti-pullout capability is a popular feature on some new toolholding systems. At IMTS 2014 in Chicago, for example, REGO-FIX rolled out a new version of its secuRgrip anti-pullout toolholding system that can be used with the company’s ER collets and milling chucks. The secuRgrip system locks collet and cutter to the body of the toolholder via a proprietary method involving a profiled locking key insert that fits into a tool’s standard Weldon endmill flat. When the insert is put into the tool flat, screwing the tool into a collet or milling chuck with a matching internal diameter profile locks the two together in a highly secure fashion.
“The big advantage we have in the secuRgrip system is that it uses a standard Weldon flat cutting tool. It doesn’t require any special groove or grinding to be done to the cutting tool. We try to make it nice and easy for the customer,” says McHenry.
Schunk’s recently released Tendo Aviation toolholder system also has prominent anti-pullout characteristics. The Tendo Aviation toolholder is designed to ensure secure, form-fit tool clamping with a standard Weldon shank. Machinists can maximize efficiency with their tools and machines while incurring minimal material wear. Advantages include boosted process reliability and the elimination of the need for time-wasting tool shank modifications.
“Anti-pullout is for expensive parts where you absolutely cannot have any risk of tool creepage. You have a solidified process; you just need that added protection with giving consideration to tool life, because tool life is very important. You’re using expensive tools on an expensive part,” explains Panosh.
Parlec, for its part, also introduced some new products at IMTS 2014 including the ERos high performance toolholder.
“It’s an extremely high speed, high concentricity toolholder with good grip force. When you are trying to get a perfectly sized hole using a reamer, or trying to get a high metal removal rate, or high precision drilling and milling, or something where you’re doing a finish pass and you want maximum tool life … the ERos is based on a collet system, there’s no high start-up cost. You just need a wrench and the chuck and collet. It gives you that level of performance with low start-up costs,”
says Hartman.
The discussion of new and/or newly improved toolholder systems leads back to the original point: treat your toolholder with respect. Don’t buy a toolholder solely because of its price, match it with an appropriate cutting tool and be sure to take care of the toolholder once it’s in your possession through proper storage and cleaning.
“As cutting tools become more capable and machine tools become more capable, then the [toolholding] itself has to become more capable as well,” says Hartman.
[gallery type="slideshow" link="none" ids="109492,109493,109494,109495"]
About the Author
subscribe now
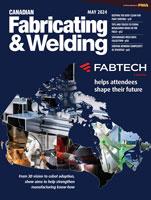
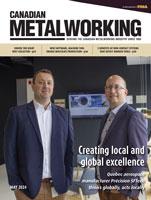
Keep up to date with the latest news, events, and technology for all things metal from our pair of monthly magazines written specifically for Canadian manufacturers!
Start Your Free Subscription- Industry Events
Automate 2024
- May 6 - 9, 2024
- Chicago, IL
ANCA Open House
- May 7 - 8, 2024
- Wixom, MI
17th annual Joint Open House
- May 8 - 9, 2024
- Oakville and Mississauga, ON Canada
MME Saskatoon
- May 28, 2024
- Saskatoon, SK Canada
CME's Health & Safety Symposium for Manufacturers
- May 29, 2024
- Mississauga, ON Canada