Industry 4.0 System Specialist
- FMA
- The Fabricator
- FABTECH
- Canadian Metalworking
Whose factory of the future is it anyway?
Building a unique shop maximizes investments, streamlines processes
- By Asvin Parsad
- March 13, 2019
With Industry 4.0 revolutionizing the world of manufacturing, it is essential for facilities (both large and small) to keep up if they want to remain competitive.
Increased cost pressures, heightened quality standards, and shorter lead times are just a handful of expectations now being placed on the industry. That makes efficient working practices more important than ever before.
As a result, the factory of the future (FOTF) is what everybody is speculating about. How can shops evolve to accommodate the varying demands placed on them? How can existing legacy equipment be brought into the realm of the smart factory? How can small manufacturers keep up without undergoing a complete digital overhaul?
In the FOTF model, we examine the technological tools that currently are available to get a business through the Fourth Industrial Revolution. The biggest barrier is not technology, it’s people.
If companies do not have the desired behavioural profile, however, these tools are quite useless. The successful candidates need to have an adaptable mindset and a culture that views change as an opportunity. They need to have creativity, visionary thinking, and be critical enough to question past behaviour and processes.
They also should have an awareness of lean manufacturing principles, continuous improvement process (CIP), and good interpersonal communication skills.
Other competency barriers, like a lack of data analytics skills, IT staffing, data security, and cloud platforms may become apparent, but usually at a later stage.
An example is a tool called ActiveCockpit. This tool automates information flow by pulling information from multiple data sources (like KPIs, WIP, available resources, deviations, and OEE). This information is used in real time by the production manager to make decisions regarding schedule and fixing quality issues. However, if an organization does not have a culture of CIP, trusting feedback from the shop floor and using KPIs to measure how close they are to their goals, this tool just ends up being an expensive display board.
Achieve competitiveness through flexibility
Think about an existing factory as a place where the only fixed elements are the walls, floors, and ceilings. Everything else is mobile, with modular assembly lines and machines that freely adapt to new purposes. That flexibility delivers a competitive advantage for manufacturers and tangible benefits for their customers.
For manufacturers that are operating in a more competitive global marketplace than ever before, enhancing levels of quality and elevating affordability by decreasing overheads are even more crucial. The good news is that the FOTF makes all of this possible.
For smaller manufacturers in particular, finding the right answer for their needs is critical. Their concerns are more immediate than those of larger manufacturers, and generating efficiencies or lowering overheads could be the difference between success and stagnation in a fast-paced, digital environment.
The key for them is to remain agile, creating a smart factory that allows production lines to be reconfigured easily so that they can adapt to fast-changing requirements.
That is where small manufacturers have a significant advantage. With less infrastructure, shorter chains of command, and fewer layers to production methodologies, these companies can adopt change easily. Once these pieces are in place, small manufacturers have the ability to be more agile.
Keep an eye on ROI
Before manufacturers make any changes, making sure the changes deliver the impact you need is crucial. New configuration technology allows them to create a virtual replica of their entire facility, which essentially becomes a test bed for any new systems. From there processes can be mimicked so that any new equipment can be assessed before being implemented, giving manufacturers detailed insights into how their facility can be improved.
Once implemented in the FOTF, all hardware modules and functions can be represented digitally in real time. Sophisticated software now can collect, transfer, and process data to continuously improve processes and facilitate machine learning. Wireless technology has the potential to mobilize machines and plants, with inductive charging and 5G connectivity making for a faster and more stable means of data transfer.
However, while being up-to-date with technology, such as cloud data, IT security, and ERP interfaces, is an essential aspect of the FOTF, it is not a prerequisite.
The starting point should be about identifying what the pain points are. It starts by asking a few important questions.
- What are the breakdown or maintenance issues?
- How do we track and prevent machine downtime?
- What are the data connectivity issues?
- What are the logistical issues?
- Where are our parts along the supply chain?
- What are the quality issues?
At that point shops can look at the available technology, whether that’s lean principles, machine learning, or digital twinning, to address the issue at hand.
The key is to start small, get comfortable with the data, trust the data, apply the information to make improvements in the process, and then expand the concept to the rest of the organization.
In practice, that means simplified conversions to new processes for maximum flexibility. Production configures itself independently inline with the product to be manufactured, communication between machines and systems is wireless, and production layouts are optimized for greater efficiency. Coupled with real-time data capture and analysis, continuous improvement becomes reality.
With all that flexibility, the FOTF is an entirely adaptable place, perfectly positioning manufacturers to create products of enormous variety while maintaining constantly high standards of quality.
That combination makes every manufacturer unique, delivering an undeniable edge when competing on the world stage – something made possible by the digitalization of the industry.
Keep cybersecurity top of mind
With an estimated 50 billion connected devices existing by 2020, it is forecast that $172 billion will be spent on internet of things (IoT) security (that’s 4.5 per cent of global IT expenditure). This means cybersecurity is very important.
Security threats can come at the device level, network level, and platform level and be in the form of illegal access, malicious code insertion, data leakage, unapproved sensors, wiretapping, and privacy violation, among others. The impact of such a breach can be catastrophic for a company, its customers, and even public safety.
Fortunately, all standard IoT protocols like MQTT, CoAP, Zigbee, BLE, and HTTP/REST have a basic security mode that can be configured using the authentication options. In addition, there are design frameworks and best practices from different organizations (OTA, IOTFS, GSMA, OWAS) that address specific issues like encryption, de-identification, access control, data disposal, secure coding, security patch, and simulated hacking.
Bosch’s viewpoint is that there has to be a “trusted IoT label” that allows customers to compare the abilities of different products without feeling overwhelmed with the technical details and security certificates.
But, of course, there is no one-size-fits-all system.
Asvin Parsad is industry 4.0 system specialist for Bosch Rexroth Canada, 3426 Mainway Dr., Burlington, Ont. L7M 1A8, 905-315-6043, www.boschrexroth.ca/fotf.
subscribe now
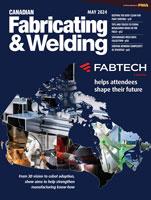
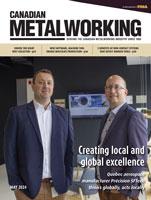
Keep up to date with the latest news, events, and technology for all things metal from our pair of monthly magazines written specifically for Canadian manufacturers!
Start Your Free SubscriptionAbout the Author
Related Companies
- Trending Articles
Automating additive manufacturing
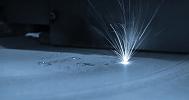
Sustainability Analyzer Tool helps users measure and reduce carbon footprint
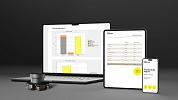
GF Machining Solutions names managing director and head of market region North and Central Americas
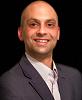
Mitutoyo updates its end-user portal
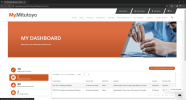
Enhance surface finish with high-speed machining
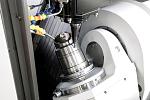
- Industry Events
CTMA Economic Uncertainty: Helping You Navigate Kitchener Seminar
- May 2, 2024
- Kitchener, ON Canada
Automate 2024
- May 6 - 9, 2024
- Chicago, IL
ANCA Open House
- May 7 - 8, 2024
- Wixom, MI
17th annual Joint Open House
- May 8 - 9, 2024
- Oakville and Mississauga, ON Canada
MME Saskatoon
- May 28, 2024
- Saskatoon, SK Canada