- FMA
- The Fabricator
- FABTECH
- Canadian Metalworking
Tool Tech: Keeping cool under pressure
Machine tool manufacturers have developed and launched hundreds of High Pressure Coolant turning tools.
- By Canadian Metalworking
- May 14, 2015
The many advantageous properties associated with so called ‘exotic metals’ such as titanium and superalloys, Hastelloy, Inconel and Waspaloy, have resulted in the ever rising use of these advanced materials within the global aerospace industry and beyond.
Usually alloyed with aluminum and nickel, titanium boasts a high tensile strength-to-density ratio, excellent corrosion and fatigue resistance, high crack resistance and the ability to withstand moderately high temperatures without creeping.
These beneficial characteristics render titanium an ideal material for use in a wide range of aerospace components, including critical structural parts, landing gear, hydraulic systems, critical fastener applications, springs and in hydraulic tubing. Titanium’s suitability for use in the above areas is reflected in the fact that approximately two-thirds of all titanium metal currently produced is used in the manufacture of aircraft engines and frames.
Superalloys typically have a matrix with an austenitic face-centered cubic crystal structure. Superalloys’ base alloying element is usually nickel, cobalt, or nickel-iron. Prompted by the demands of the aerospace and power industries, chemical and process innovations have enabled significant progress to be made within the field of superalloys. Typical applications within the aerospace industry include turbine blades and use within hot sections of jet engines.
The increasing complexity of titanium and superalloy aerospace parts and the burgeoning demand for ever more efficient manufacturing methods has prompted the introduction of new machining technologies and the development of innovative tooling solutions, all aimed at assisting users to increasing their productivity.
High Pressure Coolant (HPC) delivery maximizes machine performance.
Given the availability of high speed machines that offer standard or optional 70-bar coolant systems with through-spindle delivery, HPC technology has become much more accessible. For many years, machine tool manufacturers, including Iscar, have developed and launched hundreds of HPC turning tools. HPC solutions have been employed by customers throughout the world on turning applications involving difficult-to-machine materials such as titanium and Inconel, and they have consistently delivered impressive removal rates, up to three times greater than conventional flood coolant systems.
Users report the elimination of chip jamming, much faster cutting and significantly longer edge life when performing outer and inner diameter turning, grooving, parting and hole making. The advantages gained by the use of Iscar’s JETHP line, including improved tool life, are also evident when machining steel parts, where the chips are more manageable.
The configuration of the JETHP line ensures that coolant is delivered with enough force and fast enough to reach the cutting zone as a liquid—unlike systems that may result in the delivery of a less-effective coolant vapor to the critical zone. When high pressure coolant is applied in the liquid state it effectively lubricates the cutting process, and as it quenches the molten chips they shatter into smaller, more manageable, pieces. In addition, the product’s internal flow path keeps the tool, insert and workpiece cooler, resulting in longer tool and equipment life.
The JETHP tools are designed to operate at extreme pressure and high cutting rates across a wide range of turning applications. The advantages of HPC can be implemented on multiple tool set-ups.
For example, Iscar’s DO-GRIP can deliver the coolant jet through the insert directly to the cutting edge (fig. 1). Its Pentacut five-cornered insert and tangential clamping has a short distance between cooling outlet and cutting edge providing a continuous stream (fig. 2). And for Iscar’s ISOTURN lines an HPC system composed of a static housing and telescopic tube directs coolant to the cutting edge (fig. 3).
[gallery type="slideshow" link="none" size="large" ids="110427,110428,110429"]
Rafi Ravoach, ISO Turning Products product manager, Iscar Global.
subscribe now
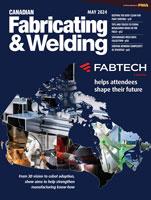
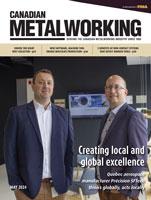
Keep up to date with the latest news, events, and technology for all things metal from our pair of monthly magazines written specifically for Canadian manufacturers!
Start Your Free SubscriptionAbout the Author
- Trending Articles
Sustainability Analyzer Tool helps users measure and reduce carbon footprint
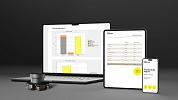
Enhance surface finish with high-speed machining
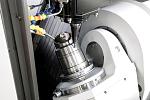
Equispheres secures $20 million investment round
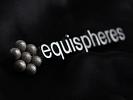
Solid carbide drills produce precision holes in short chipping materials
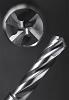
Okuma announces new personnel appointments
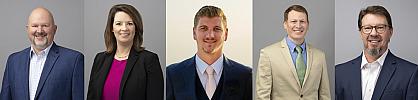
- Industry Events
Automate 2024
- May 6 - 9, 2024
- Chicago, IL
ANCA Open House
- May 7 - 8, 2024
- Wixom, MI
17th annual Joint Open House
- May 8 - 9, 2024
- Oakville and Mississauga, ON Canada
MME Saskatoon
- May 28, 2024
- Saskatoon, SK Canada
CME's Health & Safety Symposium for Manufacturers
- May 29, 2024
- Mississauga, ON Canada