- FMA
- The Fabricator
- FABTECH
- Canadian Metalworking
Traditional vs. Modern Thinking in the Die and Mold Industry
Die and mold machining can be done with a wide range of cutting tools.
- By Canadian Metalworking
- March 27, 2015
The die and mold industry dates back to ancient times; one of the first mold making practices was the production of patterns for coins and medals. Today’s mold makers are very qualified and skilled, using a wide variety of techniques and knowledge including metal removal, metallurgy, polymers, plastic flow, EDM and wire cut technology, and in many cases the key personnel in some enterprises will say that since mold or die making is not a mass production process there is no pressure to change tooling and technology.
One of the ways to analyze a mold shop’s technology level is to look at its machining methods and tools. Many shops are “loyal” to their old instruments. Die and mold machining can be done with a wide range of cutting tools which are selected and optimized in accordance with the process chain, process step specifications, final required geometry and surface integrity, workpiece material and its properties, as well as machine tool specifications and different environmental conditions.
A typical mold shop will still use standard round-shaped milling inserts for its rough milling applications, standard ISO turn inserts for rough turning on a lathe, and HSS (high-speed steel) drill or a tap. A common belief is that mold and die shops only have a specific hole to drill and only one or two threads to tap, so why change to newer tools and add cost. However, in reality, there is a huge difference for shops that do adopt new technology.
Traditional Rough Milling with Round Inserts
For rough milling of a mold cavity or a core, traditionalists believe there is no replacement for the standard round insert geometry; methods of using either an endmill (shank adaptation) or a shell mill (screw + 2 keyways) with round inserts are well known and still widely used. There are many milling applications well suited to this type of tooling such as face milling, shoulder milling, linear and circular ramp milling, and this, in addition to relatively low prices for the cutting inserts, is the main reason for the wide use of the round inserts/tools.
However, while looking at each parameter or application of the whole milling process, and trying to efficiently optimize the common roughing technology, new cutting technologies, tools and methods can dramatically change the manufacturing process.
When approaching the metal, a round-shaped insert creates different approach angles at each depth of cut. Basically there is a need to change the machining parameters for each depth. A common method adopted by mold shops is to apply certain consistent machining parameters for all mold parts using the same tool. However, it limits productivity and efficient machining.
An alternative solution developed by ISCAR, the HELIDO H600 (figure A), enables mold shops to expedite the time on the machine for each part. The approach angle is a linear constant 17º or 30º for fast feed (FF) or medium feed (MF) implementation. For each depth of cut applied the same machining parameters can be used.
Rough Turning with ISO Standard Inserts
Using ISO standard turning inserts was the only turning method in the market for lathe products. Rough turning was commonly done with a diamond (80°) shaped insert, clamped with a well-known lever-clamping mechanism.
Under heavy loads, micro lifts of the back of the insert occur and create micro chipping and breakage. One solution is to use a top clamping mechanism, but only for light depth of cuts due to the fact that large chips can rub the top arm which clamps the insert.
An ISCAR solution is a diamond and trigon-shaped turning line of tools and inserts. At the clamping face there are dovetailed prisms that prevent movement even under extremely high loads and ultimately provide increased tool life (figure B).
Technology in the metalworking industry is constantly being updated and the development of new cutting tools, combined with machining processes and improvements in the complete process chain, are essential for higher productivity and improved performance for the age-old practice of manufacturing dies and molds.
[gallery type="slideshow" link="none" size="large" ids="109530,109531"]
subscribe now
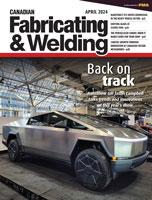
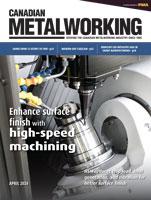
Keep up to date with the latest news, events, and technology for all things metal from our pair of monthly magazines written specifically for Canadian manufacturers!
Start Your Free SubscriptionAbout the Author
- Trending Articles
Automating additive manufacturing
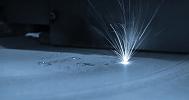
Sustainability Analyzer Tool helps users measure and reduce carbon footprint
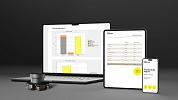
CTMA launches another round of Career-Ready program
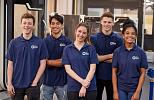
Sandvik Coromant hosts workforce development event empowering young women in manufacturing
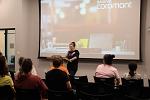
GF Machining Solutions names managing director and head of market region North and Central Americas
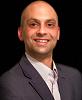
- Industry Events
MME Winnipeg
- April 30, 2024
- Winnipeg, ON Canada
CTMA Economic Uncertainty: Helping You Navigate Windsor Seminar
- April 30, 2024
- Windsor, ON Canada
CTMA Economic Uncertainty: Helping You Navigate Kitchener Seminar
- May 2, 2024
- Kitchener, ON Canada
Automate 2024
- May 6 - 9, 2024
- Chicago, IL
ANCA Open House
- May 7 - 8, 2024
- Wixom, MI