Editor
- FMA
- The Fabricator
- FABTECH
- Canadian Metalworking
Is machine monitoring creating trust issues in your shop?
Make sure your workers know it’s about machine performance, not their performance.
- By Joe Thompson
- June 6, 2023
British mathematician and data scientist Clive Humby once said that data is the new oil. He meant that it’s an incredible resource, but one that’s fairly useless until it has been refined.
In your shop, data is everywhere. It’s created by manufacturing sensors and software, as well as all other operational technology (OT) and information technology (IT) systems. Some of it is generated automatically, while other data needs to be manually entered. It may even come to you via an ancient form of communication: fax.
One popular technology that generates data is a machine tool monitoring system. It provides a real-time look at the data coming from your equipment and is designed give you the insight you need to optimize your production processes.
Data collected from manufacturing equipment, including temperature, spindle and axis load, power consumption, and spindle uptime, helps manufacturing companies track cycle time but also overall equipment effectiveness, non-productive time, and other key performance indicators.
By monitoring the status of machines, a baseline can be created, tracked, and then dissected to find ways to improve. These systems deliver data to three teams.
1. Management. Shop owners/managers use monitoring data to judge production and workflow costs at the plant level and over time for long-term planning purposes.
2. Production/Operation Team Leaders. Production supervisors use this data to optimize current operations to help reduce downtime, costs, and unused capacity.
3. Machinists/Operators. Machine tool monitoring data provides shop personnel with information on how best to optimize their machining operations in the short term.
Over the past several years, machine tool monitoring has become a huge part of process improvement strategies. But how do your machinists and operators feel about it? Do they see it as a 30,000-ft. view of shop floor operations or do they feel like Jim Carrey’s character Truman Burbank from the hit movie The Truman Show?
When implementing this technology into your facility, it’s a good idea to reassure your shop floor team that it’s a machine monitoring system, not an employee monitoring system.
It’s all about the machining process. Machine monitoring is a great way find efficiency improvements that lead to better productivity, and therefore, profitability. But it also can upset employees who may see it as a loss of privacy or even as a test to find slackers and time sinks.
The best way to alleviate these feelings is by being transparent. Make sure your workers know it’s about machine performance, not their performance.
subscribe now
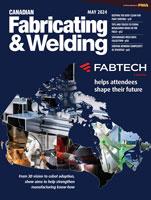
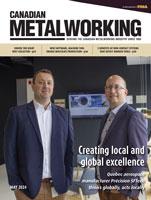
Keep up to date with the latest news, events, and technology for all things metal from our pair of monthly magazines written specifically for Canadian manufacturers!
Start Your Free SubscriptionAbout the Author
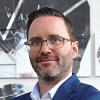
Joe Thompson
416-1154 Warden Avenue
Toronto, M1R 0A1 Canada
905-315-8226
Joe Thompson has been covering the Canadian manufacturing sector for more than two decades. He is responsible for the day-to-day editorial direction of the magazine, providing a uniquely Canadian look at the world of metal manufacturing.
An award-winning writer and graduate of the Sheridan College journalism program, he has published articles worldwide in a variety of industries, including manufacturing, pharmaceutical, medical, infrastructure, and entertainment.
- Industry Events
Automate 2024
- May 6 - 9, 2024
- Chicago, IL
ANCA Open House
- May 7 - 8, 2024
- Wixom, MI
17th annual Joint Open House
- May 8 - 9, 2024
- Oakville and Mississauga, ON Canada
MME Saskatoon
- May 28, 2024
- Saskatoon, SK Canada
CME's Health & Safety Symposium for Manufacturers
- May 29, 2024
- Mississauga, ON Canada