Editor
- FMA
- The Fabricator
- FABTECH
- Canadian Metalworking
Know your machine shop jargon
We get into trouble is when there is too much of it
- By Joe Thompson
- February 15, 2022
The manufacturing industry is under threat.
And I don’t mean a threat like poor business conditions, supply chain disruptions, shifting consumer appetites, or a lack of skilled labour. Even though all of these are true, manufacturing--and those involved in it--are in trouble of being drowned by jargon.
Jargon plays a role in every job and, in fact, every industry actually has its own almost-secret language. If you listen closely enough you can hear manufacturers talk about catheads, Boolean operations, and a rake’s face. Not to mention shanks, shims, and shoulders. It’s even true that jargon can differ from one shop to another.
Jargon is not slang, however, which typically is a less formal version of a word or saying. It’s simply the words and expressions members of a profession use in their day-to-day work. It’s also necessary. Where we get into trouble is when there is too much of it.
Describing coolant flow to the work zone has to be the No. 1 jargon-heavy example in the industry.
Forget flood coolant for the moment.
Coolant-through-the-spindle, through-spindle coolant, coolant-through, through-coolant, and even thru-coolant and coolant-thru are all used to describe the same machine feature, although you’ll have a tough time finding the word thru in any of Mr. Webster’s books. These same modifiers now also can be applied to advanced toolholders and even the tools themselves.
Not even the machine tools themselves are immune. It’s G-code jargon.
Different machines will read G-codes differently. Specifically, they are affected by the presence (or absence) of spaces between the commands and in the number of zeros between the letter and number. For example, one type of machine may use G4 as the code to dwell while another machine may use G04. Better make sure you get this one right.
A material’s hardness is another jargon trap. Brinell, Knoop, Vickers, Scleroscope, and Rockwell (in all of its forms) all are standard hardness tests. These all use indenters that are pushed into a metallic surface with a given force to determine hardness. Geography, education background, generation, and, most important, part specification including the material being tested all affect which of these you likely are most familiar with.
One of my favourites, though, is the ubiquitous thou. It’s not thou as in “Wherefore art thou Romeo?” but instead it’s a machinist’s term for a unit of measurement equalling 0.001 in. (one-thousandth of an inch). Building on this theme is the term tenth, which of course is not one-tenth of an inch, but instead one ten-thousandth of an inch (0.0001 in).
You really better be sure you don’t get that one wrong.
subscribe now
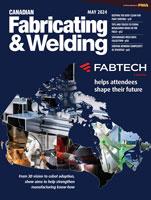
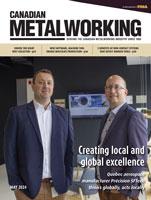
Keep up to date with the latest news, events, and technology for all things metal from our pair of monthly magazines written specifically for Canadian manufacturers!
Start Your Free SubscriptionAbout the Author
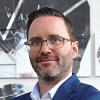
Joe Thompson
416-1154 Warden Avenue
Toronto, M1R 0A1 Canada
905-315-8226
Joe Thompson has been covering the Canadian manufacturing sector for more than two decades. He is responsible for the day-to-day editorial direction of the magazine, providing a uniquely Canadian look at the world of metal manufacturing.
An award-winning writer and graduate of the Sheridan College journalism program, he has published articles worldwide in a variety of industries, including manufacturing, pharmaceutical, medical, infrastructure, and entertainment.
- Trending Articles
Sustainability Analyzer Tool helps users measure and reduce carbon footprint
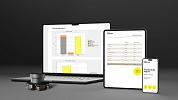
Mitutoyo updates its end-user portal
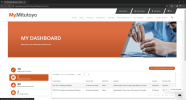
Enhance surface finish with high-speed machining
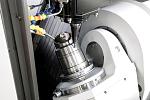
Equispheres secures $20 million investment round
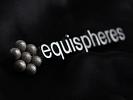
Solid carbide drills produce precision holes in short chipping materials
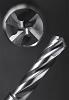
- Industry Events
Automate 2024
- May 6 - 9, 2024
- Chicago, IL
ANCA Open House
- May 7 - 8, 2024
- Wixom, MI
17th annual Joint Open House
- May 8 - 9, 2024
- Oakville and Mississauga, ON Canada
MME Saskatoon
- May 28, 2024
- Saskatoon, SK Canada
CME's Health & Safety Symposium for Manufacturers
- May 29, 2024
- Mississauga, ON Canada