- FMA
- The Fabricator
- FABTECH
- Canadian Metalworking
View from the floor: Bringing work back
The timing is right to be getting on board.
- By Canadian Metalworking
- January 15, 2015
Speaking with Peter Adams, founder of Burloak Technologies in Dundas, Ontario, Canada’s first production-level 3D metal printing facility, you get the feeling that additive manufacturing is on the threshold of gaining critical acceptance in the metalworking industry.Adams will be investing $11.5 million over five-years to make sure his company leads the way as this advanced manufacturing process takes hold, spending not only on part making technology but also on automating processes to be as productive as possible. He foresees a new generation of sophisticated parts being designed, parts previously unimaginable due to limitations of conventional machining. And as he tells it, these complex, high-value parts, will play a role in bringing manufacturing back to North America, because there is no cost advantage to low labour rates for products like these.
The picture Adams paints corresponds to a recent report from the Boston Consulting Group. In a survey of senior manufacturing execs, they found the number of companies repatriating production from China is on the rise.
And the survey found these companies see a payoff coming from investments in technologies such as 3D printing, robotics and digital manufacturing, with 72 per cent planning to make such investments in the next five years.
And the timing is right to be getting on board, especially if you’re in the auto sector.
Speaking to a full house at the Metalworking Manufacturing & Production Expo held last month in Windsor, Canada’s auto industry expert Dennis DesRosiers presented a beaming forecast for the industry.
Based on a series of trending factors, including a record number of new vehicle models coming to market, he sees the industry in growth mode through 2018, maybe through 2020 or later.
“I have the most positive possible outlook for the MTDM (machine tool, die & mold) sector in the Windsor Essex County that you can possibly have, and that I have ever had in my 44 years of studying this industry,” said DesRosiers.
But he warned the audience: “This is now an intellectual-based industry. It’s not just product development and R&D, it’s as much to do with process as it is with product.”
That takes me back to Adams, who identifies the mold industry as a prime market for 3D-printed tools, where conformal cooling channels built into molds will lead to better products and faster cycle times. One of the many huge opportunities he sees to bring work back.
DOUG PICKLYK, EDITOR
subscribe now
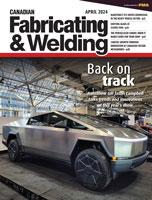
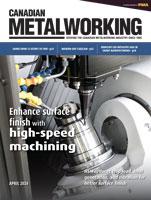
Keep up to date with the latest news, events, and technology for all things metal from our pair of monthly magazines written specifically for Canadian manufacturers!
Start Your Free SubscriptionAbout the Author
- Trending Articles
Automating additive manufacturing
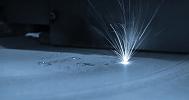
Sustainability Analyzer Tool helps users measure and reduce carbon footprint
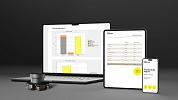
CTMA launches another round of Career-Ready program
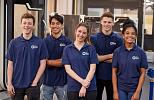
Sandvik Coromant hosts workforce development event empowering young women in manufacturing
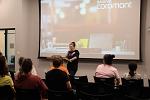
GF Machining Solutions names managing director and head of market region North and Central Americas
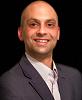
- Industry Events
MME Winnipeg
- April 30, 2024
- Winnipeg, ON Canada
CTMA Economic Uncertainty: Helping You Navigate Windsor Seminar
- April 30, 2024
- Windsor, ON Canada
CTMA Economic Uncertainty: Helping You Navigate Kitchener Seminar
- May 2, 2024
- Kitchener, ON Canada
Automate 2024
- May 6 - 9, 2024
- Chicago, IL
ANCA Open House
- May 7 - 8, 2024
- Wixom, MI