- FMA
- The Fabricator
- FABTECH
- Canadian Metalworking
Common CNC Grinding Mistakes
Exploring the grinding wheel and the dressing of the grinding wheel.
- By Canadian Metalworking
- February 3, 2015
Have you ever heard the saying that “CNC grinding is a black art”? To some extent this is true, but with the proper grinding process parameters, a lot of the “black art” can be eliminated and productivity and quality can be improved. While there are many variables that go into a sound grinding process, I would like to focus on the grinding wheel and the dressing of the grinding wheel.
Mistake #1: Grinding Wheel
Over my 20 years of CNC grinding experience, one common mistake I see is not having the right grinding wheel for the application. The workpiece material, material hardness, and surface finish required must all be taken into consideration when choosing the correct grinding wheel.
A grinding wheel is made up of the abrasive, which does the cutting, and the bond, which holds the abrasive in place. Just like sandpaper, the size of the abrasive is determined by the grit. The higher the grit number, the smaller the abrasive.
One common mistake is using too coarse of a grinding wheel for the surface finish required. A finer finish can be obtained by slowing down the dressing feedrate, but slowing down the dressing feedrate can also result in dulling the abrasive grain. A dull wheel results in more heat generation and more grinding forces, neither of which are good for productivity or quality. A finer grit wheel with sharp abrasive grains is always better than a coarser grit wheel with dull abrasives grains. The following chart will provide some guidance on the proper grit size for the surface finish required:
Mistake #2: Dressing
Dressing too frequently. In many cases, with the proper grinding wheel specification multiple parts can be ground without the need to dress the wheel. The abrasive grain will become dull the more material it removes, but dressing every part is often not necessary. By reducing the frequency of dress, the cycle time is reduced and the grinding wheel and dressing diamond life are extended. This reduces the tooling cost per part and increases productivity.
The diamond dresser that is used to dress the grinding wheel can also have an effect on productivity and quality. A common method for dressing is using a single point diamond. A single point diamond will work fine as long as it is rotated frequently. Over time, the single point diamond will wear and develop a flat. Dressing with a single point diamond that has too large of a flat on it will result in dulling the abrasive grain on the grinding wheel when it is dressed. In high-production applications, I would highly recommend a rotary dresser. Rotary dressing uses an electric spindle to rotate a diamond disc to dress the grinding wheel. Rotary dressing provides a more consistent dress as the diamonds on the dressing disc do not wear flats as quickly as a single point diamond.
Hopefully you will find this information useful in improving productivity and quality in your CNC grinding process.
Rob Titus is Applications Engineer, Grinder Products, Okuma America Corporation.
This blog originally appeared on www.okuma.com. It has been republished on Canadian Metalworking’s website with permission from the Okuma America Corporation.
subscribe now
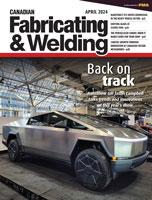
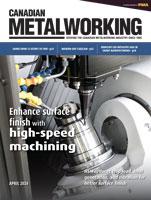
Keep up to date with the latest news, events, and technology for all things metal from our pair of monthly magazines written specifically for Canadian manufacturers!
Start Your Free SubscriptionAbout the Author
- Trending Articles
Automating additive manufacturing
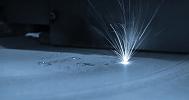
Sustainability Analyzer Tool helps users measure and reduce carbon footprint
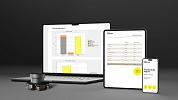
CTMA launches another round of Career-Ready program
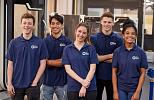
Sandvik Coromant hosts workforce development event empowering young women in manufacturing
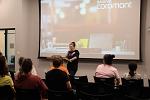
GF Machining Solutions names managing director and head of market region North and Central Americas
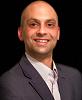
- Industry Events
MME Winnipeg
- April 30, 2024
- Winnipeg, ON Canada
CTMA Economic Uncertainty: Helping You Navigate Windsor Seminar
- April 30, 2024
- Windsor, ON Canada
CTMA Economic Uncertainty: Helping You Navigate Kitchener Seminar
- May 2, 2024
- Kitchener, ON Canada
Automate 2024
- May 6 - 9, 2024
- Chicago, IL
ANCA Open House
- May 7 - 8, 2024
- Wixom, MI