- FMA
- The Fabricator
- FABTECH
- Canadian Metalworking
Get a grip on toolholding systems with HAIMER
A new toolholding system began doubling tool life and cutting overall costs.
- By Canadian Metalworking
- March 20, 2015
Like many shops, Applied Engineering, Inc., spends quite a bit of money on tools each year. So it was pleasantly surprised when a new toolholding system began doubling tool life and cutting overall costs.
“We’re always looking at ways we can improve our processes,” said Greg Husman, the company’s optimization manager. “What we’ve found is that balancing and heat shrinking our toolholders gives us repeatable and predictive results.”
Based in Yankton, South Dakota, Applied Engineering is a 165-employee shop that specializes in short- and long-run aluminum components for several industries, mainly aerospace and aircraft. Many of those components are used in navigation and weather radar systems for commercial aircraft. The company also launched its own line of compound bows, making itself more diversified and competitive in a different market.
With dozens of horizontal machining centers that rotate up to 20,000 RPMs, Applied Engineering knows that proper toolholding is critical to extending its tool life and investment. It’s also a key factor in machining accuracy and repeatability.
But until recently, proper toolholding came at a high cost.
Pressure is On
Applied Engineering had been spending $40,000 per year on parts for its existing toolholding system, which required specially designed collets to be pressed into toolholders. Though the system achieved decent runout, the costs were difficult to justify.
A few years ago, Applied Engineering began searching for a comparable system that was less expensive. It found one in 2012, while visiting the Haimer USA booth at the IMTS show.
A key difference for Haimer’s shrink fit system is that it uses heat rather than collets or hydraulics to grip a part. With the push of a button, the toolholder is heated up and the cutting tool is inserted. Then the holder is cooled down in 30 seconds. As a result, the toolholder and cutting tool become virtually one piece.
Applied Engineering decided to give the Haimer system a try and the results were eye-opening. They reflected an improvement in runout, gripping force, and balance, the three main variables in toolholding. Tool life increased from 80 parts to more than 600 parts on a consistent basis.
“The Haimer system paid for itself in less than a year,” Husman said. “Not only have we increased tool life on many of our tools, but the quality of our parts is increasing just from the repeatability of tooling. We’ve also noticed an improvement in surface finishes and cycle times.”
Another key benefit was balance repeatability and balance options. Because there are no moving parts with the shrink fit system, additional fine tuning is not often necessary. However, the company decided to purchase Haimer’s modular balancing system to improve tool life for its other toolholding system.
“The balancer alone has helped us beat tool life expectations by at least 20 percent,” Husman said. “When combined with the shrink fit system, which helped us improve runout from .0007 to .0002 of an inch, we can achieve near perfect conditions. Haimer’s balancer can be used for any of our toolholdling systems; the heat shrinking just takes it one step further.”
Because of the high gripping torque of the Haimer shrink fit system, Applied Engineering also noticed a reduction in scrap. In fact, the company was able to cut its scrap in half last year, thanks in part to the new system. Now the company is spending less money on tools and toolholding, but achieving many more benefits, including higher quality parts.
For more information, visit www.haimer-usa.com.
subscribe now
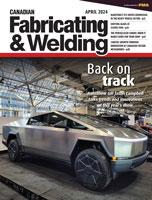
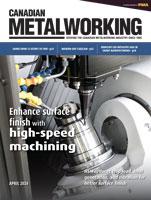
Keep up to date with the latest news, events, and technology for all things metal from our pair of monthly magazines written specifically for Canadian manufacturers!
Start Your Free SubscriptionAbout the Author
Related Companies
- Trending Articles
Automating additive manufacturing
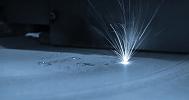
Sustainability Analyzer Tool helps users measure and reduce carbon footprint
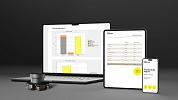
CTMA launches another round of Career-Ready program
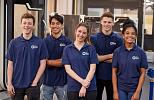
Sandvik Coromant hosts workforce development event empowering young women in manufacturing
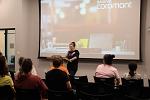
GF Machining Solutions names managing director and head of market region North and Central Americas
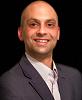
- Industry Events
MME Winnipeg
- April 30, 2024
- Winnipeg, ON Canada
CTMA Economic Uncertainty: Helping You Navigate Windsor Seminar
- April 30, 2024
- Windsor, ON Canada
CTMA Economic Uncertainty: Helping You Navigate Kitchener Seminar
- May 2, 2024
- Kitchener, ON Canada
Automate 2024
- May 6 - 9, 2024
- Chicago, IL
ANCA Open House
- May 7 - 8, 2024
- Wixom, MI