- FMA
- The Fabricator
- FABTECH
- Canadian Metalworking
That’s Crazy! You Can’t Turn on a Machining Center!
Well actually, you can.
- By Canadian Metalworking
- September 5, 2014
How many times have you quoted a job that was primarily a milling job, but that required one or more features that just HAD to be turned. Perhaps the surface call-out required a turned surface for a sealing face. Maybe the circular profile of a feature is so complex that any form mill would be too expensive, exert excessive cutting forces, or would not yield an acceptable finish. In such a case, you would quote for workholding, tooling, set-up and run time on the machining center AND a lathe. Quoting the workholding and time for the lathe is complicated by the fact that the feature to be turned must be located on the centerline of the lathe spindle. This presents a problem if the feature is not located at the center of a round part. The problem is even greater if you have multiple turned features at different locations of the part. Fixturing and/or repositioning the part for each feature is expensive and/or time consuming. Furthermore, each time the part is repositioned the chances of scrapping the part increases. Is your bid doomed? If you have an Okuma machining center, definitely not!
“Turn-Cut” Turns a Profit
We have a solution that can help you quote this job at a rate that’s low enough to beat the competition while allowing you a nice profit margin. The solution is called “Turn-Cut.” Turn-Cut is an option that allows 2-axis lathe operations to be performed on a machining center. This is achieved by synchronizing the spindle rotation with the X- and Y-axis motions of the machine. The machine’s X- and Y-axis motions are synchronized such that the spindle centerline moves in a circular motion. Simultaneously, the machine spindle rotation is synchronized with the circular motion so that the tool tip stays “on-center” with the part. The diameter of this circle is the X-axis diameter command. The machine’s Z-axis moves longitudinally and corresponds to the lathe Z-axis. Using a standard, off-the-shelf turning tool mounted to a V-flange holder, this option allows your machining center to actually turn either the ID or OD of a part. Other lathe operations such as ID/OD grooving, face grooving, threading and backfacing can be performed on a machining center equipped with Turn-Cut.
Does Your Machining Center Need Turn-Cut?
Okuma has provided Turn-Cut to customers in the oil, aerospace, heavy machinery, hydraulic component and other industries. It’s a great fit for the following applications (and more):
- Valves
- Manifolds
- Large and/or irregularly shaped workpieces with turned features
Using Turn-Cut already? Please share your thoughts below!
Dennis Nichols is Senior Applications Engineer, Okuma America Corporation.
This blog originally appeared on www.okuma.com. It has been republished on Canadian Metalworking’s website with permission from the Okuma Corporation.
subscribe now
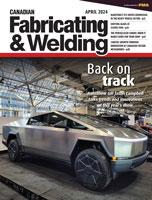
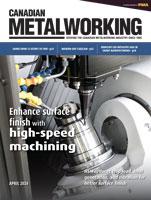
Keep up to date with the latest news, events, and technology for all things metal from our pair of monthly magazines written specifically for Canadian manufacturers!
Start Your Free SubscriptionAbout the Author
- Trending Articles
Automating additive manufacturing
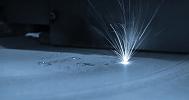
Sustainability Analyzer Tool helps users measure and reduce carbon footprint
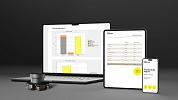
CTMA launches another round of Career-Ready program
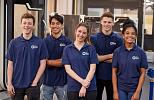
Sandvik Coromant hosts workforce development event empowering young women in manufacturing
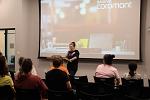
GF Machining Solutions names managing director and head of market region North and Central Americas
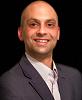
- Industry Events
MME Winnipeg
- April 30, 2024
- Winnipeg, ON Canada
CTMA Economic Uncertainty: Helping You Navigate Windsor Seminar
- April 30, 2024
- Windsor, ON Canada
CTMA Economic Uncertainty: Helping You Navigate Kitchener Seminar
- May 2, 2024
- Kitchener, ON Canada
Automate 2024
- May 6 - 9, 2024
- Chicago, IL
ANCA Open House
- May 7 - 8, 2024
- Wixom, MI