- FMA
- The Fabricator
- FABTECH
- Canadian Metalworking
Airbus Helicopters uses 3D printing to mass-produce aircraft components
- October 24, 2023
- News Release
- Metalworking
Airbus Helicopters has announced plans to use TRUMPF 3D printers to manufacture components for its helicopters and aircraft from its parent company, Airbus.
Airbus Helicopters is expanding its additive manufacturing capabilities with a new 3D printing centre in Donauwörth, Germany. TRUMPF is supplying the machines for metal 3D printing.
"With innovative manufacturing processes, we are working on the helicopters of the future in Donauwörth," said Helmut Färber, site manager of Airbus Helicopters in Donauwörth. "Among other things, 3D printing helps reduce the weight of components."
Lightweighting helps aircraft operators reduce fuel consumption and lower their costs. It can also help reduce CO2 emissions in flight. Airbus Helicopters will use the 3D printing process to produce components for the electric-powered CityAirbus, the experimental high-speed Racer helicopter, and the Airbus A350 and A320 passenger aircraft, among others.
"With its manufacturing know-how, TRUMPF is a reliable partner to the aviation industry worldwide," said Richard Bannmueller, CEO of TRUMPF Laser and System Technology. "Our 3D printing systems are a key technology on the path to sustainable flying and reduced dependency on long supply chains."
Additive manufacturing allows entire assemblies to be printed as one component, which saves weight. At the same time, the components are very stable and meet the strict safety requirements of the aviation industry.
Airbus Helicopters uses 3D printers from TRUMPF to manufacture structural components made of titanium and high-strength aluminum.
"Additive manufacturing saves expensive raw material and can lower production costs in the aviation industry. 3D printers only use the material that designers actually need for their components and that ends up taking off in the aircraft," said Bannmueller.
3D printing users can also reuse unused metal powder. Conventional manufacturing processes, on the other hand, require up to ten times more raw material than the final product. Therefore, when milling or chipping, much of the raw material ends up as waste.
subscribe now
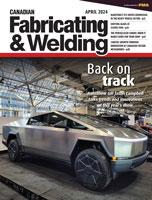
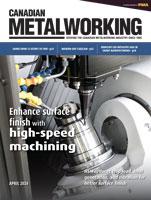
Keep up to date with the latest news, events, and technology for all things metal from our pair of monthly magazines written specifically for Canadian manufacturers!
Start Your Free Subscription- Trending Articles
Automating additive manufacturing
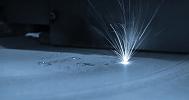
Sustainability Analyzer Tool helps users measure and reduce carbon footprint
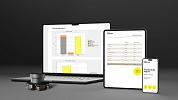
CTMA launches another round of Career-Ready program
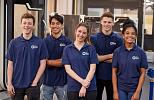
Sandvik Coromant hosts workforce development event empowering young women in manufacturing
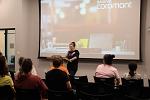
GF Machining Solutions names managing director and head of market region North and Central Americas
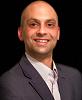
- Industry Events
MME Winnipeg
- April 30, 2024
- Winnipeg, ON Canada
CTMA Economic Uncertainty: Helping You Navigate Windsor Seminar
- April 30, 2024
- Windsor, ON Canada
CTMA Economic Uncertainty: Helping You Navigate Kitchener Seminar
- May 2, 2024
- Kitchener, ON Canada
Automate 2024
- May 6 - 9, 2024
- Chicago, IL
ANCA Open House
- May 7 - 8, 2024
- Wixom, MI