- FMA
- The Fabricator
- FABTECH
- Canadian Metalworking
CAM software boosts productivity for programming advanced machining centres
- December 14, 2023
- Product Release
- Automation and Software
GibbsCAM has released its 2024 version, which updates the software’s core strengths while bringing a stronger emphasis on digital connectivity, including a direct integration with Sandvik Coromant’s CoroPlus Tool Library.
The updated software introduces new post-processor configuration options for setting standard and custom post defaults, including support for TCP and rotary clamps. A new tool also has been added to help streamline the CAM environment setup that enables editing and restricting work fixture offsets. It supports multiple fixture stacking, and now unused fixtures can be retained on the machine for simulation and collision checking purposes.
Alongside many other enhancements, generic probing now supports rotary part alignment and positioning. Selecting only the rotary axis, clearance, and shifting parameters will drive the system to probe the surface and calculate the part rotation alignment.
The update improves the flexibility of form tools in milling processes. Users can choose how to drive the tool by using the real profile option that uses the exact cutting tool profile, or the monotonic profile, which will disable any toolpath that uses the tool undercut form. For 3D solid form tools, another option for nominal parameters will only use the major diameter and tip radius for toolpath calculation according to tool manufacturer recommendations, while using the 3D form tool for simulation.
A new mill cutoff process for mill/turn machines and bar-fed mills now supports perpendicular cutting with an end mill and parallel cutting with a side mill or slitting saw.
Rest machining has been improved when contouring and pocketing strategies are used together with “material only” active now, creating a more efficient toolpath with reduced air cuts. Other contour improvements include smoother ramping that generates a continuous contour wherever possible instead of multiple ramping lead-in and lead-out movements.
Also new is variable-depth engraving, which improves the use of complex fonts with tapered tooling and corner ramping. In addition, selectable alignment options are added to control the starting position of operations using a rotary axis. Users can override the default singularity rules, which is useful for keeping the toolpath within machine limits (frequently Y axis) and machining on the opposite side of a mill/turn part.
New 5-axis features include an optimized stepover feature for finishing walls and cylindrical and conical floors that creates a better, more consistent surface finish. New geodesic operations perform straight cuts on end boundaries and improve hole filling to prevent the tool from dropping down into open cavities. Other improvements include user-defined tool orientation on lead-in and lead-out movements and linked entry feed distance. Multiaxis machining enhancements include better management of 3D containments, improved point distribution, ramp offset for the first pass on roughing cycles, user-defined start points for finishing, and tool tilting during helix entries.
GibbsCAM | www.gibbscam.com
subscribe now
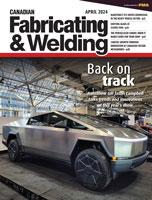
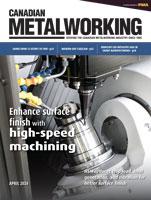
Keep up to date with the latest news, events, and technology for all things metal from our pair of monthly magazines written specifically for Canadian manufacturers!
Start Your Free Subscription- Trending Articles
Automating additive manufacturing
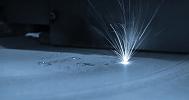
Sustainability Analyzer Tool helps users measure and reduce carbon footprint
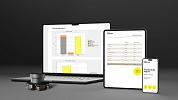
CTMA launches another round of Career-Ready program
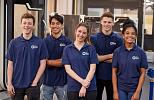
Sandvik Coromant hosts workforce development event empowering young women in manufacturing
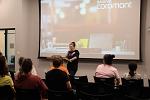
GF Machining Solutions names managing director and head of market region North and Central Americas
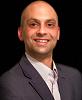
- Industry Events
MME Winnipeg
- April 30, 2024
- Winnipeg, ON Canada
CTMA Economic Uncertainty: Helping You Navigate Windsor Seminar
- April 30, 2024
- Windsor, ON Canada
CTMA Economic Uncertainty: Helping You Navigate Kitchener Seminar
- May 2, 2024
- Kitchener, ON Canada
Automate 2024
- May 6 - 9, 2024
- Chicago, IL
ANCA Open House
- May 7 - 8, 2024
- Wixom, MI