- FMA
- The Fabricator
- FABTECH
- Canadian Metalworking
Top gear
Ontario Drive and Gear started as a transmission maker for Argo off-road vehicles… but they’ve become a premier Canadian success story in gear making
- January 25, 2012
- Product Release
- Automation and Software
“Grinding gears” is not an expression that conjures up a pleasant image… unless you’re New Hamburg, Ontario-based Ontario Drive and Gear. For ODG, grinding gears using new state of the art equipment has changed the “blank-hobb-finish” paradigm and closed the gap between custom job work and mass production runs.
Founded in 1962 in Kitchener, Ontario, ODG launched the iconic ARGO amphibious vehicle in 1967. By 1969, the firm had outgrown their Kitchener facility and moved to their current 10-acre site in nearby New Hamburg, Ontario. In 2001, a new 40,000 square foot climate controlled facility on the site effectively split the operation into a Vehicle Division and a Gear Division, driving a new focus on outside customer gears and power transmission solutions.
“Actually we were a gear shop before we were a vehicle manufacturer”, says ODG general manager Joel Wright adding, “we were originally the subsidiary of a German gear company, using older hobbers and shapers. At the time there were over 40 different all terrain vehicle manufacturers and we became suppliers of parts and gearboxes; when one of the manufacturers went out of business we bought the design rights. That became the ARGO, in 1967. We went from being a gear shop to making ARGOs…..machining was an offshoot of the operation. Somewhere in the mid 80’s we asked ‘where do we go’? Part of the plan was to revive the gear business. We added CNC technology in the early 90’s. It’s almost all CNC today. This facility is built to accommodate these machines. We expanded on 2007…its been interesting going from a nothing, to a $20M dollar operation, looking at $25M next year. It’s been quite a ride.”
That ride has brought ODG’s 110 employees to a level of sophistication that the company now handles complex OEM power transmission engineering for everything from Mars rovers to hybrid buses, military machines, to automotive drivetrain assemblies, all for major, brand name manufacturers. The reliability of these types of equipment simply does not allow for failure. The majority of the shop floor personnel are licensed machinists. ODG partners with Conestoga College to rotate five apprentices and co-op students through the facility every year. ODG boasts a strong product and process engineering team that allows design from concept to production to validation under on roof. “It’s been rapid growth” says Wright. “We’ve added lots of technology. The focus has been gear grinding and hard finishing. It’s tight tolerance work and grinding has been at the centre of it. Grinding is not a cheap process…we spent about 10 million dollars in the past five years. It’s allowed us to move forward. We look to differentiate ourselves technologically… we’re not a ‘me too’ manufacturer.”
One way ODG avoids the “me too” philosophy is through the firm’s unusually broad capability. The operation is profitable with a mix of high and low volume, simple and complex, as well as fast turnaround and long lead products. What’s the minimum order? The new grinding technology allows a run to be as small as a single unit, or thousands, and ODG easily run 50 to 100 jobs per week at the facility, with over a thousand SKU’s in the ODG design library. What makes ODG’s system so flexible is a paradigm shift in the way gears are made. The traditional method is to hob a blank, then use a second op shaving process for some gears, then heat treat. This process was refined with a post heat-treat skiiving step where a hard, tough and expensive hob removed small amounts of material from the very hard surface, a process that was both hard on the expensive tool but more importantly, required custom tools with order lead times that could be 16 weeks or more. Simple tool breakage could delay delivery by weeks. The new grinding process changes the flow to hobbing, heat treating hard turning and grinding, using the new Kapp grinders. The abrasive process not only tolerates the hardened surface well, but the ability to diamond dress the wheel has opened up new possibilities in gear production by tailoring the gear profile on a level impossible with conventional hobbing, both in microfinishing and by eliminating a major source of error: heat treating. Declares Wright: “Years ago we had to live with the post-heat treat shift. That’s why transmissions were noisy. By adding the after heat treat finishing process, we get to the near perfect gear. The transmission error is significantly reduced. Even the forklift driving down the aisle at Home Depot is quiet. With the new hybrid and electric vehicles you can’t hear them driving on the road. The next revolution might be an appealing noise, for safety reasons.”
The new process is clearly better and reduces the lead times imposed by the skiving process, but it’s also more productive. “We’re probably running at higher speeds, sometimes 30 to 50 percent faster with grinding”, says Wright. “Consumable costs are less. A carbide hob could cost thousands of dollars, then make 200 or 300 pieces before it needed resharpening. For a German hob, it could be a 16 to 20 weeks lead time. If an operator crashed a hob, you were stuck. Now it’s a reliable process, and grinding is cheaper than a skiving process, at any volume. I can set up the grinder faster than the hobber.
And it gives us total flexibility. We no longer need to wait for a special hob. We can green grind a blank, heat treat and finish grind a prototype in as little as a week. We did a rush job for a major OEM that needed master gears for a dynamometer where downtime cost thousands per hour. We delivered in two weeks.”
At 50, Ontario Drive and Gear has come full circle, from a small job shop making gears to a major manufacturer that can still profitably create short runs with fast lead times hand-in-hand with big volume OEM orders.
“There’s not another gear manufacturer in North America with this variety of gear grinding, from manufacturing to design to assembly…we run the gantlet”, says Wright. It’s all from in-house engineering. We are a world leader, right here in New Hamburg”.
subscribe now
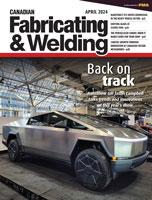
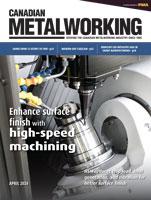
Keep up to date with the latest news, events, and technology for all things metal from our pair of monthly magazines written specifically for Canadian manufacturers!
Start Your Free Subscription- Trending Articles
Automating additive manufacturing
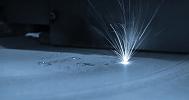
Sustainability Analyzer Tool helps users measure and reduce carbon footprint
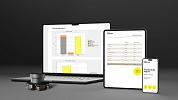
CTMA launches another round of Career-Ready program
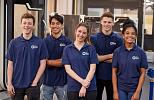
Sandvik Coromant hosts workforce development event empowering young women in manufacturing
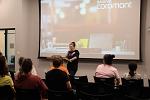
GF Machining Solutions names managing director and head of market region North and Central Americas
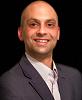
- Industry Events
MME Winnipeg
- April 30, 2024
- Winnipeg, ON Canada
CTMA Economic Uncertainty: Helping You Navigate Windsor Seminar
- April 30, 2024
- Windsor, ON Canada
CTMA Economic Uncertainty: Helping You Navigate Kitchener Seminar
- May 2, 2024
- Kitchener, ON Canada
Automate 2024
- May 6 - 9, 2024
- Chicago, IL
ANCA Open House
- May 7 - 8, 2024
- Wixom, MI