- FMA
- The Fabricator
- FABTECH
- Canadian Metalworking
Attention to detail
Optimize the elements of your spray painting system to achieve better efficiency and lower costs.
- January 25, 2012
- Product Release
- Metalworking
In the current economic climate, a new spray booth is not in the cards for most Canadian in-house and independent spray paint operations. But there’s lots you can do to boost the efficiency of the existing spraying system.
A recent article by Timothy Kurcz, director of sales, Jessup Engineering (in Product Finishing magazine), notes that instead of buying a new paint installation, the lowest-cost solution is often to “increase demand on already stressed human/machine resources. This is risky given the operator-sensitive nature of the finishing business and finicky, well-worn machines. A better choice is targeted investment of carefully engineered upgrades designed to enhance existing plating, anodizing, coating, and other types of finishing systems.”
Some of this you may already know, but just like reading articles on winter driving tips every November, it never hurts to review the details.
Target: energy savings
Variable frequency drives may reduce energy costs on equipment that uses electric motors. In a paint booth, VFDs can be used to control motors on the air makeup intake and the exhaust system.
They provide a smooth motor start, and if your utility rate is calculated on your highest peak usage, then they have the potential to reduce electricity costs in that way too.
If your booth is not already equipped with VFDs, consider a retrofit. An upgrade to the booth control system may also be required.
Other energy saving upgrades are a recirculating system for when the booth is in bake/dry mode, and a heat recovery system that recovers heat from the air exhausted by process equipment and uses it to warm intake air brought into the building.
Target: mixing accuracy
Exel North America, in partnership with Air Electric Tool & Equipment, was able to improve the throughput and quality of the metal parts painting operation of a manufacturer of car wash equipment.
Exel worked with Sonny’s Enterprises of Florida to replace its hand mixing process with a system that incorporates Cyclomix™ Micro and four 17A2 Kremlin pumps.
Cyclomix™ Micro is Excel’s smallest electronic mechanical two component system. It comes standard with up to three colour controls and a remote booth mounted control panel.
The benefits for Sonny’s are accurate coating mixing, lower labour costs, and less waste generated.
The system has also improved the quality of finish, thanks to Exel’s Airmix® technology, and proper catalyzing of the material by using Cyclomix™ Micro instead of hand mixing.
Target: dust
There are two benefits of proper dust collection: quality and safety, according to Marty Powell, industrial territory manager with Global Finishing Solutions. A high quality finish is the direct result of adequate removal of airborne particles that may contaminate finished surfaces, says Powell in an article on spray booth fires in Product Finishing magazine. Contamination causes rejects or rework that results in lost profits.
But, it’s not just surface finish that particle build-up can affect, says Powell. If not cleaned, particles can migrate to areas where operators may not have proper breathing protection, and fire becomes a real hazard. Sufficient airflow is key.
For safety purposes, spray booth manufacturer Col-met offers as a rule of thumb: It’s time to clean the ventilation ducts and duct discharge points when residue accumulates to a thickness of 1/8 inch. At that point, shut down the operation until the cleaning is complete.
Target: fire safety
While you’re giving thought to your spraying system, spare a thought for fire safety. The Booth Blog on Global Finishing Solutions’ web site points to the NFPA 33 Annex D Fire Record to help booth users understand the reasons behind various fire prevention regulations.
This section lists, as the leading causes of fire in conventional systems (air spray, HVLP, airless):
- Use of spark producing equipment such as cutting, welding, and grinding near the spray area.
- Friction, in most cases by overheated bearings on the exhaust fan or by rubbing of exhaust fan blades against the overspray deposits on the wall of the duct.
- Arcing electrical equipment.
- Spontaneous combustion.
- Discharge of static electricity.
Target: filters
What makes a paint booth filter cost effective? Long life? Efficiency rating? Ease of installation? Low purchase price? Low initial resistance? Compliance compatibility? The answer is “all of the above”, according to Mike Snow, filter sales manager for Global Finishing Solutions.
In a Global Finishing blog entry last year, Snow noted that identifying the characteristics of the coating material is the logical starting point for filter selection. “Although, there are several aspects of a coating material that directly affect filter performance, viscosity has a large role. Viscosity dictates how a coating is atomized for application. Atomization consequently, dictates how dense, or open, a filter’s fiber matrix must be to yield maximum performance from the paint arrestor. Too dense, and the efficiency may be acceptable but the service life is unacceptable. Open the fiber matrix to extend the service life, and the diminished efficiency leads to bleed-through that would create excessive fugitive emissions. In turn, that would contaminate the plenum, fan, and stack, possibly leading to the discharge of pollutants into the atmosphere.”
Snow goes on to say that the values from a paint arrestance test may not reflect the efficiency of a filter in actual operation. Generally, in paint arrestance tests, a high-solids enamel is the default coating. Testing of the actual coating used in your operation is the only accurate way of gauging the true performance of a paint arrestor.
Target: maintenance
A high quality air filter will provide high efficiency, and the correct diffusion to prevent inconsistent airflow and turbulence, says Snow.
It’s also important to routinely replace the filters, he reminds users. A plugged filter throws off the balance of the booth and allows buildup of overspray on some exhaust fans. Filters should be changed when the final resistance, as specified by the manufacturer of the booth, has been reached.
Col-met, in its blog, suggests monitoring filters constantly so you’ll know when they need to be changed. Consider installing a filter gauge that will automatically shut down the spray gun when the filter fails to allow a minimum amount of air to pass through.
If your booth does not have a pressure gauge, says Snow, establish a strict maintenance schedule based upon the volume of spraying taking place on a day-to-day basis. It is typically recommended that ceiling filters be changed at least twice a year. All other intake filters should be changed once a month or as needed.
Snow explains that clogged or overloaded filters may not allow proper air flow through the booth causing dust or overspray to re-circulate with the booth and affect the finish.
It’s your responsibility
Spray booths and painting equipment operate at peak efficiency when first installed. It’s up to the shop to keep the system clean and well maintained so it continues to function at optimum levels.
The Wave, optimized for water
GFS Wave Aqua paint booth filters are the world’s first to be designed specifically to achieve maximum performance with waterborne paints. Mike Snow, GFS’ filter sales manager was the driving force behind the development of the Wave Aqua filters.
He says the Wave Aqua is designed for situations where high viscosity, fast drying industrial coatings might face-load conventional polyester, paper/poly, or poly/fiberglass media.
The Wave Aqua is a versatile, non-woven, polyester media comprised of coarse fibers specifically chosen for strength, durability, and performance in overspray collection applications.
The low initial resistance of the Wave Aqua, 0.03”wg at 150 fpm, is a key feature of the product’s performance capability. The proprietary fiber blend, in conjunction with the patented Wave pattern, enables paint laden air to be captured across the surface and within the depth of the media; extending filter service life and reducing operating costs.
According to GFS, Wave Aqua can provide performance advantages that can make even under-powered exhaust systems operate more effectively than can conventional polyester collectors. The new filter has a removal efficiency of 99.73% on overspray.
The patented Wave pattern provides 2.3 times more surface area for every square foot of face area in an existing frame system.
Today’s economy dictates energy conservation as well as high output in production facilities. GFS states that the Wave Aqua has 25% lower initial resistance than the next closest polyester media and 50%, or more, lower resistance than many of today’s conventional standard and high capacity polyester overspray collectors.
Global Finishing Solutions, www.globalfinishing.com
subscribe now
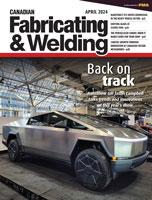
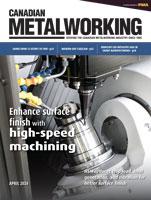
Keep up to date with the latest news, events, and technology for all things metal from our pair of monthly magazines written specifically for Canadian manufacturers!
Start Your Free Subscription- Trending Articles
Automating additive manufacturing
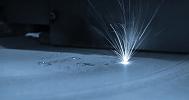
Sustainability Analyzer Tool helps users measure and reduce carbon footprint
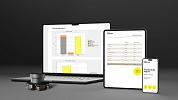
CTMA launches another round of Career-Ready program
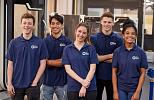
Sandvik Coromant hosts workforce development event empowering young women in manufacturing
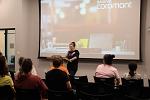
GF Machining Solutions names managing director and head of market region North and Central Americas
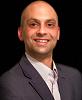
- Industry Events
MME Winnipeg
- April 30, 2024
- Winnipeg, ON Canada
CTMA Economic Uncertainty: Helping You Navigate Windsor Seminar
- April 30, 2024
- Windsor, ON Canada
CTMA Economic Uncertainty: Helping You Navigate Kitchener Seminar
- May 2, 2024
- Kitchener, ON Canada
Automate 2024
- May 6 - 9, 2024
- Chicago, IL
ANCA Open House
- May 7 - 8, 2024
- Wixom, MI