- FMA
- The Fabricator
- FABTECH
- Canadian Metalworking
IMTS 2014 Preview: Hardinge
Hardinge will be showcasing products at IMTS in booth S-8738 and N-6936.
- August 20, 2014
- Product Release
- Metalworking
Hardinge Inc. will be showcasing products at IMTS in booth S-8738 and N-6936.
TURNING
All new Hardinge CONQUEST H51 SUPER-PRECISION features the Hardinge Collet-Ready Spindle, Hardinge is pleased to debut the “ultimate bar machine” at IMTS. The machine is available in both high performance and SUPER-PRECISION® models. The Hardinge CONQUEST H51 SP machine sets the standard for SUPER-PRECISION turning with outstanding performances specifications such as:
- Part Roundness – Main Spindle .000020" (.5μm)
- Continuous Machining Accuracy deviation on diameter within .0002” (5μm)
- Part Finish – Main Spindle .000008" (.2μm)
The CONQUEST H51 features a 20hp, 5000rpm A2-6” main spindle with 2” bar capacity. It offers a generous maximum turning diameter of 12.3” and a maximum turning length of 25.6”. The 12 station turret offers ½ station index for up to 24 tools. High performance and SUPER‐PRECISION productivity packages are available for choosing from features that include Live Tooling with C‐Axis, Sub-Spindle and Y‐axis. The CONQUEST H51 is offered with either a Fanuc 0i-D or Mitsubishi 720 control, each packed with a host of standard features.
The Hardinge T 42 SUPER‐PRECISION Turning centers are the benchmark in high‐precision, high‐performance turning. The T‐42 machine is designed to exceed expectations and is ideal for two axis high precision machining or complex multi‐tasking operations that require a high level of precision, delicate part handling and parts made complete in a single setup. High‐Performance and SUPER‐PRECISION productivity packages are available for choosing from with features that include but are not limited to: Live Tooling with C‐Axis, Sub Spindle, Y‐axis, Main Spindle Parts Catcher, and unique Sub Spindle Parts Catcher. This Parts Catcher is designed for removing delicate high precision parts with critical surface finish requirements without damage to the part.
The QUEST GT 27SP combines high performance with high productivity. Surface finishes of 8 micro-inch and exacting part roundness of .000015 inches can be achieved. Plus, a continuous machining accuracy of .0002 inches* gives the QUEST GT27SP a machining consistency to support SPC requirements. With the Hardinge-exclusive patented interchangeable tool top plate and world-renowned quick change collet-ready spindle, setup and cycle times are dramatically reduced. The machine features the super-stable HARCRETE base which offers enhanced dynamic stability and has 1/3 less vibration at the spindle. This results in increased tool life and improved surface finishes.
The QUEST CHNC 42 turning center designed for quick changeover with an interchangeable top plate that can be pre-tooled for a particular job or range of jobs. This next generation CHNC design configuration allows the use of interchangeable top plates and tooling used on thousands of CHNC machine installations worldwide. Some of the enhancements to this next generation CHNC machine include 4X Faster Index Time, 172% More X-Axis Travel, 18% Faster X-Axis Traverse Rate, 57% Faster Z-Axis Traverse Rate, More Rigidity with Fanuc Servo Turret Index Motor and 30% Less Floor Space. The machine features the Mitsubishi M70V Series control - the most advanced in the industry and capable of supporting complex turning applications
The GS 51 MS is a complete turning center with sub-spindle and live tooling capability. This machine is supplied with the Hardinge world-renowned collet ready spindle. This machine provides an exceptional combination of features and offers accuracy, flexibility and durability in a compact design. Hardinge’s unique collet-ready main spindle increases part accuracy and surface finish quality. The machine utilizes a robust one-piece cast iron base, and heavy-duty linear guide ways and ball screws. The GS 51 MS is ideal for job shops or OEMS looking to increase productivity and performance at an affordable price. The machine is equipped with a Fanuc 01-TD control.
MILLING
All new Bridgeport Conquest V1000 Vertical Machining Center provides very fast rapid traverse of 1693 inches per minute on X&Y axes and 1417 inches per minute on the Z- axis and a highly sophisticated yet user-friendly Mitsubishi M70M control with NAVI MILL Programming and 10.4” LCD. The machine features a powerful direct-drive 20HP, 10,000 RPM spindle motor with 75.2 ft.-lbs. of torque a 30-tool swing-arm automatic tool changer. The machine is designed for outstanding rigidity. Large, robust 45mm ball screws are provided on all axes and 35mm linear guides are standard on the X-axis with 45 size guides on the Y & Z-axes. Axis travels are: X 40” (1020mm), Y 24” 610mm) and Z: 24” (610mm).
The Bridgeport GX‐1000 OSP Vertical Machining Center features the Okuma THINC‐OSP Control. Standard features on the Open Architecture PC‐based THINC control include Microsoft WINDOWS™ Operation System, 512 MB DDR RAM, Large file handling for “Drip Feed” applications, 2 open USB Ports on the control for “plug and play” devices and data transfer, and a robust 40 GB hard drive. This machine was developed for the US Market and is a welcomed addition to the Bridgeport GX family.
The Bridgeport GX 300 Vertical Machining Center packs a lot in a small footprint. The GX 300 is designed and built for a production environment. These machines can overlap one another to utilize valuable floor space better and to promote cell manufacturing. The unique design provides service and operator interface to only the front or back of the machines. This design allows the machine to be stacked in a line side by side since there is no need to access the sides of the machine. An exceptional feature of this machine is the spindle torque and horsepower compared to other small footprint machines. With 20 horsepower and 99 ft.-lbs. of torque, the GX 300 provides a solution for the aerospace, medical, defense, 3C, automotive and other industries requiring high-value, complex parts from difficult to machine materials.
The Bridgeport GX 480 APC Vertical Machining Center with Integrated Automatic Pallet Changing capability is a lightning quick extremely compact yet rugged machine; developed for applications that require speed, as well as accuracy. The GX 480 APC is manufactured from quality sourced grey cast iron to the highest standards and possesses a level of reliability unsurpassed in the industry. It offers a fully digital machine with a rapid traverse rate of 1,417 ipm X, Y and Z and acceleration rates of 4.8 m/sec².
The Bridgeport GX 250 5AX Vertical Machining Center is Bridgeport’s newest 5-Axis vertical machining center. Bridgeport’s new generation 5-Axis Vertical Machining Center is a fully-digital, high-quality machine tool designed for leading edge machining in the Aerospace, Mold & Die, Medical and Automotive Industries and other manufacturing sectors. This machine has been developed to provide a powerful and precise solution to meet today's high demands of the metal cutting users. The machine features heavy duty linear guide ways, ball screws and axis drives. In addition, it utilizes a large capacity, fast performance automatic tool changers a fully integrated 5-axis rotary table and a BIG-PLUS dual contact spindle system. A custom designed FANUC 31iMB5 control is used to provide for the ultimate in productivity.
GRINDING
The Jones & Shipman Suprema 650 Easy Cylindrical Grinder, from the newly acquired Jones & Shipman group, features the Jones & Shipman Easy “Self‐Teach” Software Suite. The extremely easy‐to‐use Touch screen control system utilizes fast‐to‐set ‘Easy’ software suite. This simple yet powerful multi-axis control system enables an inexperienced operator to progress quickly from a manual single diameter application to linked cycle/multi‐diameter single or batch operations.
The KELLENBERGER Kel‐Vista Cylindrical Grinding Machine is designed to be a cost-effective CNC-alternative to hydraulically-controlled cylindrical grinding machines. The Kel-Vista is one of Kellenberger’s most popular CNC universal grinding machines. It comes standard with the user friendly Kellenberger menu programming. The Kel-Vista is a compact machine with optimal visibility of the working process. Designed for use in highly demanding tool and moldmaking, in machine and prototype construction, in maintenance workshops, laboratories, for economical small and medium batch production, or, in other words, wherever flexibility, precision and cost-effectiveness are indispensable.
The KELLENBERGER Kel‐Vita High‐Precision Cylindrical Grinding Machine with eight different wheel head variations is loaded with many standard features as well as state-of-the-art Kellenberger software to assist the operator with even the most difficult tasks. The latest generation Fanuc 310is control is offered with such features as with Windows CE, graphic programming with DXF Import, user guided ISO programming with expanded functionality, tool administration for a maximum of 99 grinding wheels and more. Due to the machines ergonomic design, many optional automation solutions are available including integrated loading cells and robotics.
The Jones and Shipman Ultragrind 2000 High‐Volume Cylindrical Grinding Machine is the next generation of precision grinding. The UltraGrind cylindrical grinding machine offers the highest levels of precision, accuracy, flexibility and speed of operation, featuring a brand new modular wheel head design, and multiple wheel spindles configured to suit customer requirements. Operators benefit from the most advanced grinding software suite operated through a touchscreen, utilizing the latest generation Fanuc® control and motion hardware. This ensures the machine is simple to operate, set up and quick to change over in demanding production environments.
Built on a large single piece cast iron bed, this robust high precision machine offers maximum rigidity and stability with fully supported table slide and “intelligent layout.” Available with a modular wheel head with multiple configuration options, two (2) grinding length capacities and a Fanuc 0i-TD Touchscreen CNC with a Windows embedded system. The machine features easy-to-operate grinding software for simple, fast set-ups / changeovers, even for sophisticated and complex parts.
The Usach 100-T4 CNC Grinding Machine is the ideal machine for grinding both IDs and ODs. The machine has four high-frequency motors with speeds ranging from 6,000 to 90,000 rpm. The machine has a swing diameter of up to 17.71” and is offered with the latest Siemens 840D control and Usach Open Architecture software system.
All new Usach 75 I.D. Specialty CNC Grinding Machine delivers accuracy and power in a compact design. This new model is extremely flexible in handling a wide variety of work pieces for both job shops and high-production applications, especially where high-precision is required. The machine features an 8.5” swing diameter and handles parts up to 5” in length and utilized the Mitsubishi M70V control.
Hardinge Workholding
The precision-engineered Hardinge FlexC Collet Systems mount to A2-5, A2-6 and A2-8 and select flat-back spindle noses. Pull-back thru-hole, pull-back dead-length and push-to-close dead-length styles are available for single and dual-spindle CNC lathes. Purchase one spindle mount and interchange vulcanized collet heads from job to job. Hardinge collet heads are fully interchangeable with competitor’s models.
Hardinge Swiss-type Collets are ground to precise size and TIR to meet precision machining requirements with a standard accuracy. Hardinge round Swiss Guide Bushings are carbide-lined to keep the stock clean and unmarked. Hardinge manufactures bar feed collets for FMB, IMECA, LNS and Robobar bar feeders. Collets are available for other brands on request. Hardinge offers a complete line of tool holders, tap holders, tool holder collets, tap collets and bushings that can be used on Swiss-type lathes.
For more information, visit www.hardinge.com.
subscribe now
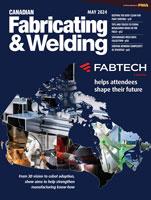
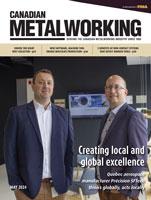
Keep up to date with the latest news, events, and technology for all things metal from our pair of monthly magazines written specifically for Canadian manufacturers!
Start Your Free Subscription- Trending Articles
Automating additive manufacturing
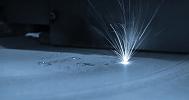
Sustainability Analyzer Tool helps users measure and reduce carbon footprint
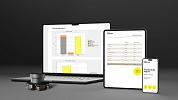
GF Machining Solutions names managing director and head of market region North and Central Americas
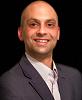
Mitutoyo updates its end-user portal
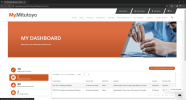
Enhance surface finish with high-speed machining
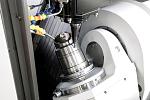
- Industry Events
CTMA Economic Uncertainty: Helping You Navigate Kitchener Seminar
- May 2, 2024
- Kitchener, ON Canada
Automate 2024
- May 6 - 9, 2024
- Chicago, IL
ANCA Open House
- May 7 - 8, 2024
- Wixom, MI
17th annual Joint Open House
- May 8 - 9, 2024
- Oakville and Mississauga, ON Canada
MME Saskatoon
- May 28, 2024
- Saskatoon, SK Canada