Associate Editor
- FMA
- The Fabricator
- FABTECH
- Canadian Metalworking
Regulation drives the need for NDT
A look at the non-destructive testing sector in Canada
- By Lindsay Luminoso
- February 16, 2016
- Article
- Measurement
When it comes to non-destructive testing (NDT), all signs point to an extremely profitable and burgeoning market both globally and in Canada, according to the January 2016 MarketsandMarkets report “Non Destructive Testing (NDT) Market worth 18.88 Billion USD by 2020”. It states that: “With the increase in automation in the industrial manufacturing and infrastructure sectors, there has been a substantial hike in the demand for flaw detection related to cracks, porosity, manufacturing disorders, and so on. Adherence to industrial safety norms is also a significant factor behind the growth of the global NDT market.”
Aerospace and defense, oil and gas, power generation and automotive are leading sectors that use NDT techniques to ensure the quality of products. In 2015, it is estimated that North America had the largest NDT market; however, Asia and the South Pacific regions are expected to see the highest market growth rate from 2015-2020.
According to the Canadian Occupational Projection System (COPS) maintained by Employment and Social Development Canada, over the 2013-2022 period there will be approximately 32,500 job openings for National Occupations Code (NOC) 226 for “other technical inspectors and regulatory officers” with only some 27,000 job seekers, demonstrating a shortfall of skilled workers. Within that the NOC code 2261 is dedicated to non-destructive testers and inspectors. With the boomer generation starting to retire and changes now being implanted by the NRCan NDT Certification Body to the NDT personnel re-certification scheme, more jobs will become available. And NDT employment growth is projected to be higher than average, fuelled in part by the continuous need to comply with mandated safety standards and regulations regardless of how the economy performs.
“Any market report that I’ve seen in the last five years points to a growing demand for products and services in the NDT area,” explains Larry Cote, president/CEO for the Canadian Institute for Non Destructive Evaluation (CINDE).
NDT Certification Standards
Through the efforts of the International Standards Organization (ISO) Technical Committee 135 for Non-destructive Testing, there has been a worldwide effort to harmonize the international standard for the qualification and certification of NDT personnel. This effort began in the 80s when Canadian industry icons such as John Zirnhelt helped lead the development of ISO 9712. Canada ultimately adopted the standard in the 90s, and more recently, in March 2015, the CAN/CGSB-48.9712-2014 standard was approved as the identical adoption of the International Standard ISO-9712:2012, which is now the basis for all third-party NDT certification programs around the world.
“Canada should be proud of the role it’s played in the development of ISO 9712,” says Cote. “Now we can say we have one singular worldwide standard that everyone can adopt more consistently. The impact of this will be to help open up the borders for goods and services, and eliminate barriers for the people who have the skills to do mission-critical inspection tasks based on the standard. We’re not all the way there yet with reciprocity between national NDT certification programs, but we’re the closest we’ve ever been.”
The ISO 9712 standard addresses many NDT methods, but the practical emphasis for industry is usually on: (1) magnetic particle testing; (2) liquid penetrant testing; (3) ultrasonic testing; (4) radiographic testing; and (5) eddy current testing.
Other similarly useful and technically advanced techniques include acoustic emission testing, strain gauge testing, vibration analysis, infrared thermography, leak testing and visual inspection. Any of these on their own can offer meaningful and challenging employment.
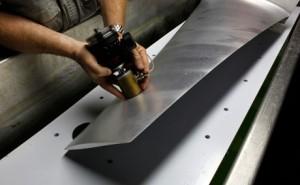
Ultrasonic methods use beams of mechanical waves of short wavelength and high frequency, transmitted from a probe and detected by the same or other probes. (Photo: Victor Aviation Services)
New inspection technologies have emerged and are now becoming commonplace in the many sectors.
“The new technology areas such as phased array ultrasound, phased array eddy current and digital radiography are making great strides in the way we can look at things to determine their quality or whether they are fit for continued service,” explains Cote.
NDT and Aerospace Manufacturing
As quality standards continue to become stricter, the need for NDT techniques becomes more prominent in many sectors, including aerospace and defense, where NDT is widely used. NDT is not always the simplest way to test and inspect parts; however, it is often a necessary option. With low volume high-cost parts, sacrificing even one part can be detrimental both from a time and cost standpoint.
When it comes to aerospace manufacturing, the need to test components is paramount, especially when it comes to new advanced materials. For example, as aerospace designs move towards composites new NDT methods were sought to help ensure the integrity of the wings and control surfaces.
Cote points out that at a recent NDT in Canada national conference, a student from the Royal Military College spoke about the best way to inspect the newer jet fighter aircraft, which now make use of composite materials. “It’s a good example of how some of the traditional NDT methods have had to make way for new approaches for composites.” With the adoption of new NDT methods, inspection technicians can say with the same certainty that the bonds on the composite material are strong and maintain their integrity every bit as well as the more familiar aluminum riveted airplane.
In 2011, the Magellan Aerospace facility in Winnipeg (MAW) opened its state of the art Advanced Composites Manufacturing Centre. Today, production of parts for the F-35 program is underway, and among the centre’s leading-edge technologies is a PaR Laser UT Non-Destructive Inspection facility. According to Magellan, its Laser UT system is one of four in the world, and the only one outside of the U.S.
“The productivity enhancements, when compared to other traditional methods of inspection are significant,” noted Don Boitson, vice president and general manager of Magellan Aerospace. “A component that would take eight hours to inspect using conventional methods can take as little as one hour to inspect utilizing Laser UT.”
The Laser UT provides non-destructive ultrasonic inspection for composite materials. However, when it comes to aerospace NDT a wide gamut of different methods are employed. At Magellan’s Winnipeg facility for example, activities currently include; radiography (film & fluoroscopy), ultrasonic (conventional & laser), eddy current (phase impedance & direct reading), fluorescent penetrant inspection, and magnetic particle inspection.
“Our NDT operating procedures are compliant with our customers’ and applicable ASTM specifications,” notes John Derkach, technical team leader—process engineering, at MAW. “Our NDT inspectors are NAS 410 and CGSB certified. We maintain NADCAP NDT accreditations to be an eligible supplier to the U.S. Defense Department and prime OEM aircraft and aero engine manufacturers.”
The entire quality department at MAW consists of about 80 staff of which 12 (approximately 15 per cent) are involved with NDT.
Future of NDT
In aerospace manufacturing, the increasing use of new materials demands a high integrity and traceability of NDT measurements.
“There are new and emerging NDT methods being tested and developed to keep pace with the various NDT challenges new aerospace materials provide,” notes Derkach. “Currently our traditional NDT methods have met our current customer requirements. The biggest challenge is to be more efficient when conducting the required NDT testing to allow MAW to be cost competitive globally and maintain the required high probability of flaw detection to ensure compliant hardware is delivered to the customer on time.”
As manufacturing environments become more automated, the need for NDT and quality assurance to keep up is increasing. And in turn, testing itself has become automated.
These systems are being widely integrated in aerospace manufacturing facilities, and also in the hundreds of nuclear power utilities across North America that cannot operate without ongoing NDT inspection to meet strict regulatory requirements to protect human lives and the environment.
“There are some tremendous quality efficiencies that can be obtained. If you don’t have a regulatory reason to be doing NDT, you should have a manufacturing and continuous improvement reason to be looking at the proper use of these technologies,” explains Cote. “Improving the maintenance and reliability of physical assets through condition-based monitoring using NDT is a competitive edge any company should want to have.”
Cote sees more automation in the future of the NDT sector. He explains that Pratt & Whitney Canada’s Longueuil facility has manufacturing cells and their inspections are much more automated. Today, Canada is a market leader when it comes to advancing technology through the efforts of Canadian companies that specialize in automating NDT techniques.
“Technology wise we are adept, and the other area we should mention is research, which is another example of how Canadians are at the forefront of NDT technology and applications,” he explains. “We have universities across the country with professors and post-grad students actively engaged in researching the new approaches that industry needs.”
Overall, Canada’s NDT sector is thriving. Industries like nuclear and aerospace are rapidly developing new processes and technologies, and the NDT sector is working to advance new standards for this new era of manufacturing. This is an area where Canada needs to start focusing its energy, explains Cote, “Many of the technology areas already mentioned are changing faster than the standards or certification organizations can keep up with. This has created some pressure in Canada to improve the supply chain of qualified people so that employers have a skilled workforce capable of using new NDT technology.”
Cote emphasizes, “We will either become a net importer of NDT inspectors from other countries or we will be a net exporter to other countries, and my preference is for our education, training and certification programs to make Canada renowned for an NDT workforce that is sought after around the world.”
About the Author
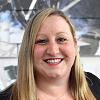
Lindsay Luminoso
1154 Warden Avenue
Toronto, M1R 0A1 Canada
Lindsay Luminoso, associate editor, contributes to both Canadian Metalworking and Canadian Fabricating & Welding. She worked as an associate editor/web editor, at Canadian Metalworking from 2014-2016 and was most recently an associate editor at Design Engineering.
Luminoso has a bachelor of arts from Carleton University, a bachelor of education from Ottawa University, and a graduate certificate in book, magazine, and digital publishing from Centennial College.
subscribe now
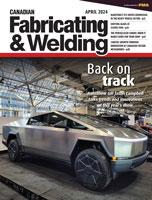
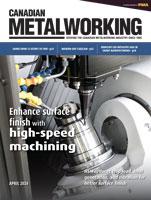
Keep up to date with the latest news, events, and technology for all things metal from our pair of monthly magazines written specifically for Canadian manufacturers!
Start Your Free Subscription- Trending Articles
Automating additive manufacturing
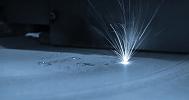
Identifying the hallmarks of a modern CNC
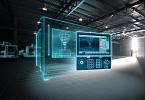
CTMA launches another round of Career-Ready program
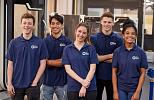
Collet chuck provides accuracy in small diameter cutting
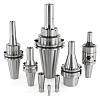
Sandvik Coromant hosts workforce development event empowering young women in manufacturing
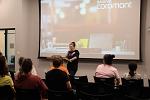
- Industry Events
MME Winnipeg
- April 30, 2024
- Winnipeg, ON Canada
CTMA Economic Uncertainty: Helping You Navigate Windsor Seminar
- April 30, 2024
- Windsor, ON Canada
CTMA Economic Uncertainty: Helping You Navigate Kitchener Seminar
- May 2, 2024
- Kitchener, ON Canada
Automate 2024
- May 6 - 9, 2024
- Chicago, IL
ANCA Open House
- May 7 - 8, 2024
- Wixom, MI