Head of Group Research and Development
- FMA
- The Fabricator
- FABTECH
- Canadian Metalworking
Technology Spotlight: Cleaner Steel Is Stronger Steel
Higher material fatigue limits impact design
- By Patrik Olund
- May 8, 2017
- Article
- Management
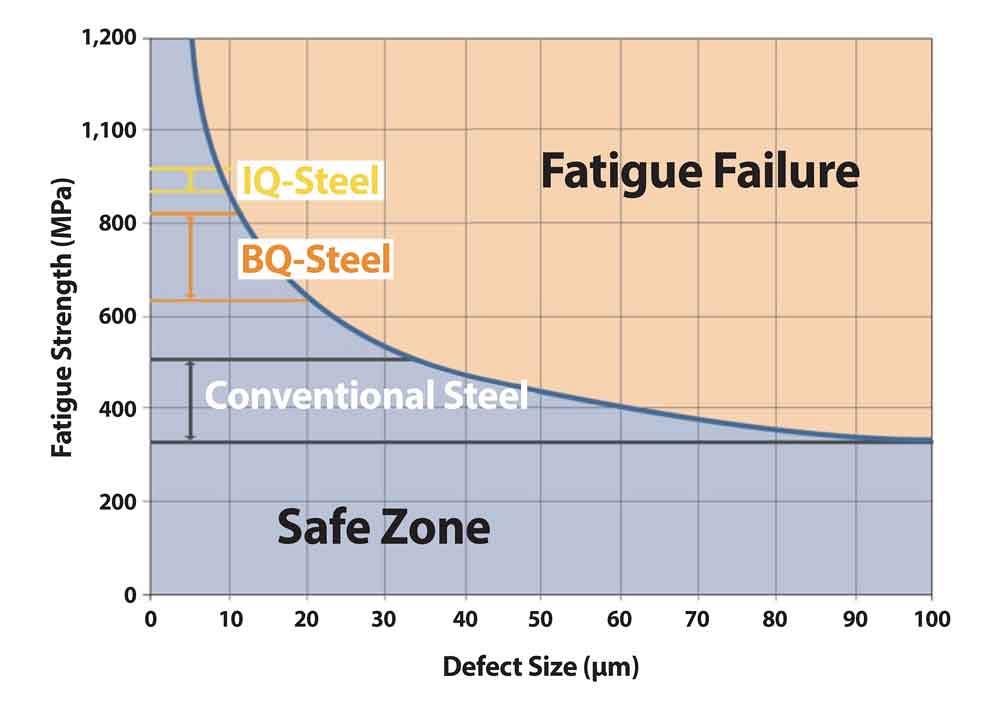
Figure 1. The chart shows the relationship between defect size and fatigue strength. Fatigue failure decreases as defect or inclusion size decreases.
As industrial designers are pushed to provide lighter, stronger, and more compact component designs, steel manufacturers are pushing to develop processes that produce lighter, stronger materials.
The process for producing conventional steels leaves a high number of inclusions in the finished material. During processing the inclusions are elongated in the steel’s rolling direction. As a result, they have poor fatigue and impact properties in the transverse rolling direction.
Clearly, at the component design stage it is imperative to carefully consider the type of steel that will be used, the size and shape of its inclusions, and the effect they will have on the component performance (see Figure 1).
Increasingly we hear from customers in the marine, transmission, engine, light and heavy vehicle, and wind power sectors that they need stronger materials for tough jobs.
So, what are the alternatives?
Conventional steels may keep your costs down, but strength and fatigue properties may be lacking. Remelted steels are a safer bet, but are costly and have a significantly greater impact on the environment.
To facilitate designs beyond present fatigue limits, IQ-Steel®, isotropic-quality, ultraclean steel, and BQ-Steel®, bearing-quality, clean steel, have been developed to provide increased fatigue strength by using a strict control of steel cleanliness. IQ-Steel offers uniform properties in all load directions for reliable components that can take the strain from higher and more complex multidirectional loads. BQ-Steel similarly is ideal for a wide array of demanding applications outside the bearing industry that require longer performance and higher load capacity.
In simple load cases, the bending fatigue strength can be increased by 40 to 100 per cent depending on the steel used. In multiaxial load cases, increases up to 130 per cent can be achieved. As design engineers strive to improve efficiency and reduce weight in their designs, they may also consider downsizing components to gain valuable space to accommodate other systems.
Clean steels enable the design of components that would not be feasible using conventional steels by allowing power density increases, reductions in size and weight, and potentially a decreased amount of steel required to manufacture a component.
Uniform Performance Throughout
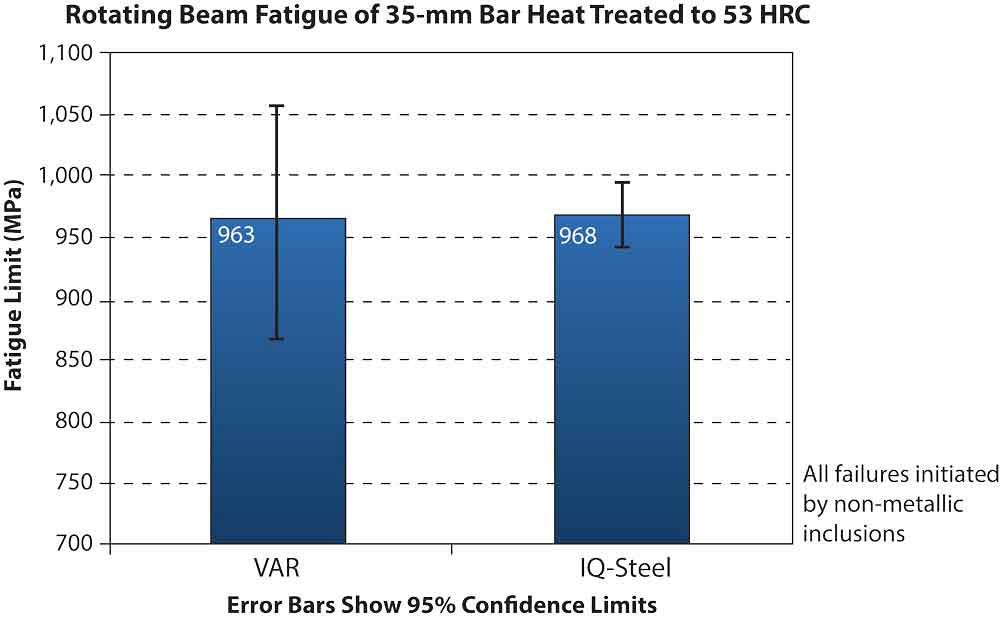
Figure 2. Benchmarking with vacuum arc remelted (VAR) steel showed that the fatigue properties obtained with clean steel are equal to the fatigue properties of remelted material.
Steel is normally an anisotropic material by nature. Metalworking deforms the inclusions which form in the metal, resulting in elongated defects in the rolling direction. A high number of large defects can initiate cracks in the material due to fatigue. Steel with small, isolated inclusions of an even size has isotropic properties that can withstand heavy loads in all directions, making it appropriate for complex load cases.
Key benefits include:
- Material properties match remelted steels’.
- Consistent high quality.
- Low microinclusion limits.
- Immersion ultrasonic testing.
- Isotropic material properties.
Benchmarking with vacuum arc remelted (VAR) steel shows that the fatigue properties obtained with clean steel are equal to the fatigue properties of remelted material (see Figure 2).
Creating New Materials
Extensive research and development carried out over the years led to substantial data being amassed on material composition and its reactions under load. This data was used to develop the clean steel processes.
Scanning electron microscopy is capable of examining large sections of material and providing rich data on microinclusions ranging in size from 2 µm to 25 µm. Data on the chemical composition of inclusions is vital for process development, while information on inclusion size and morphology contributes to product development.
Some of the most dramatic results come from ultrasonic testing of prepared samples in a water tank, which makes it possible to assess a range of larger inclusions. With the use of 10-MHz probes, 500,000 mm³ of steel could be scanned in one sample (the equivalent of 16,000 blue fracture specimens or 300,000 ASTM E45 samples). At this frequency, inclusions larger than 120 µm could be quantified with statistical accuracy. By increasing the frequency, researchers could reduce sample sizes, but inclusions smaller than 120 µm could be quantified. At 80 MHz, for example, volumes of 450 mm³ could be assessed for inclusions down to 25 µm. Combining all three qualification methods, researchers refined cleaner steel production processes (see Figure 3).
Different Grades of Clean Steel
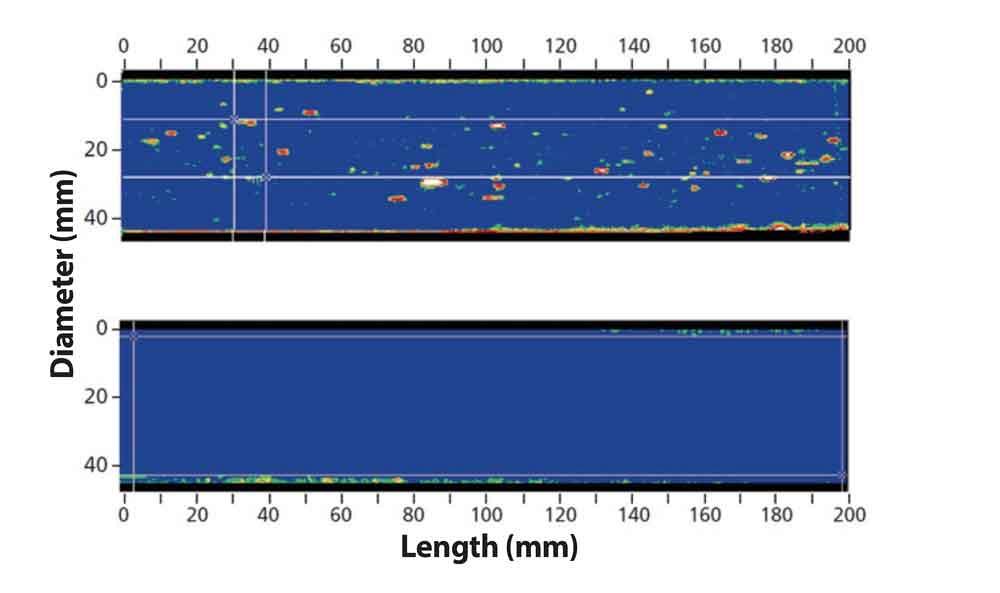
Figure 3. Inclusions on conventional steel (top) and IQ-Steel (bottom) are shown in 10 MHz ultrasonic scans.
The IQ-Steel process can be applied to many steel grades. For example, it can be combined with a type of steel that gives very little oxidation depth compared to conventional steels, resulting in improvements to surface properties (see Figure 4). This could potentially eliminate the need for surface enhancement processes such as shot peening.
Processed as a grade for use in manufacturing gears, clean steel’s equal performance in all directions, and its strength can make it possible to reduce component size. When designing a gear to be produced from clean steel, for example, you don’t need an extra-healthy safety margin, thicker walls or spacing to guard against failure. As one manufacturer commented: “In hybrid drives, more things need to share the same space under the hood, so you need cost-efficient steel that enables compact, light, and strong design.”
Components, Systems, and Processes
To get the most out of manufacturing with clean steel, it is vital that design engineers and metallurgical engineers work in close partnership. By selecting the right quality of clean steel, you can achieve a huge impact on the performance of a component.
One step is to move from conventional steel to a bearing-quality steel resulting in an increase in fatigue strength. A second step is to select an isotropic-quality, ultra clean steel to increase the performance and often the life cycle of a component. Such applications include transmission gears, high-pressure diesel injectors, and any component subjected to high, complex loads (see Figure 5).
Research continues to develop further clean steel products. To fully appreciate the features of clean steel, it is important to take a holistic view that considers the performance of the components and systems together with their manufacturing processes.
Patrik Ölund is head of group research and development, Ovako, 803-802-4590, www.ovako.com.
About the Author
subscribe now
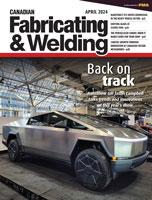
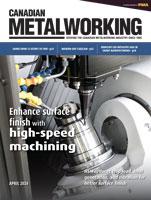
Keep up to date with the latest news, events, and technology for all things metal from our pair of monthly magazines written specifically for Canadian manufacturers!
Start Your Free Subscription- Trending Articles
Automating additive manufacturing
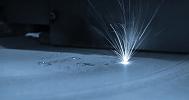
CTMA launches another round of Career-Ready program
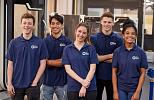
Collet chuck provides accuracy in small diameter cutting
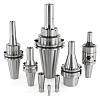
Sandvik Coromant hosts workforce development event empowering young women in manufacturing
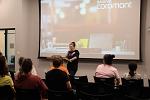
GF Machining Solutions names managing director and head of market region North and Central Americas
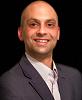
- Industry Events
MME Winnipeg
- April 30, 2024
- Winnipeg, ON Canada
CTMA Economic Uncertainty: Helping You Navigate Windsor Seminar
- April 30, 2024
- Windsor, ON Canada
CTMA Economic Uncertainty: Helping You Navigate Kitchener Seminar
- May 2, 2024
- Kitchener, ON Canada
Automate 2024
- May 6 - 9, 2024
- Chicago, IL
ANCA Open House
- May 7 - 8, 2024
- Wixom, MI