- FMA
- The Fabricator
- FABTECH
- Canadian Metalworking
Machine-to-human Communications Are Trending
What you need to know about machine events—when you need to know it
- By Sue Roberts
- March 13, 2017
- Article
- Automation and Software
Don’t blink or you’ll miss it.
The it could be an introduction of machine capabilities to speed processes, a revamping of shop floor procedures to accelerate work flow, real-time data collected from equipment sensors, or an advanced communications mode developed to capture more shop potential.
Changes in industry have been, and continue to be, occurring at lightning-speed velocity. Think Industrial Internet of Things (IIoT). Think Industry 4.0.
One way or another, collecting Information to facilitate faster, better decision-making to lead to faster, better production is at the heart of every change. The result of that information collection process is big data—more information than can easily be sorted or pared down by a human quickly enough to allow it to provide immediate value. And more data from more monitoring sensors on more equipment is being added at a rapid pace.
“Machines have all this data that is being collected, and going forward there will be more because of a predictive maintenance movement towards adding more sensors to machine components, like motors to sense and report high temperatures or excessive vibrations that might lead to a failure,” said Jonathan Kim, division manager, software operation for Amada America Inc. “The question is, how do you manage all that data so it brings value?”
Artificial intelligence (AI) is being developed to analyze and categorize big data to filter this growing, massive amount of information down to pertinent statistics that can lead to useful conclusions. Even with AI doing its rapid sort, the results need to get into the right hands at the right time or the value is lost.
Value means different things to people in different positions. For a maintenance supervisor, it may mean knowing that a setup is taking longer than usual; for quality control personnel it may be when parts are produced outside of specifications; and for management it may be when there is a catastrophic shutdown.
Practice Selective Sharing
Communicating knowledge from all those sensors and filtering systems is being assigned to the machine itself. Its task is to message or email only the people who should know about a particular situation or need. With the proper parameters in place, machine-to-human communications can improve uptime and overall equipment effectiveness and lower scrap, rework, and operating costs. It can also heighten employee engagement by creating immediacy and providing information about the cause of the problem, which allows the human response to be quicker and more relevant.
To be effective, however, the number of outbound texts, tweets, or emails, whether simple conditional alerts or complex event triggers, and who they go to need to be managed.
“Every event at a machine triggers a record that is categorized and stored in an SQL database,” said Steffen Kutz, TruTops software manager at TRUMPF Inc. “You can see how long a machine was in the production status, what is going on at the moment, and receive notifications from the machine based on your selection of events.”
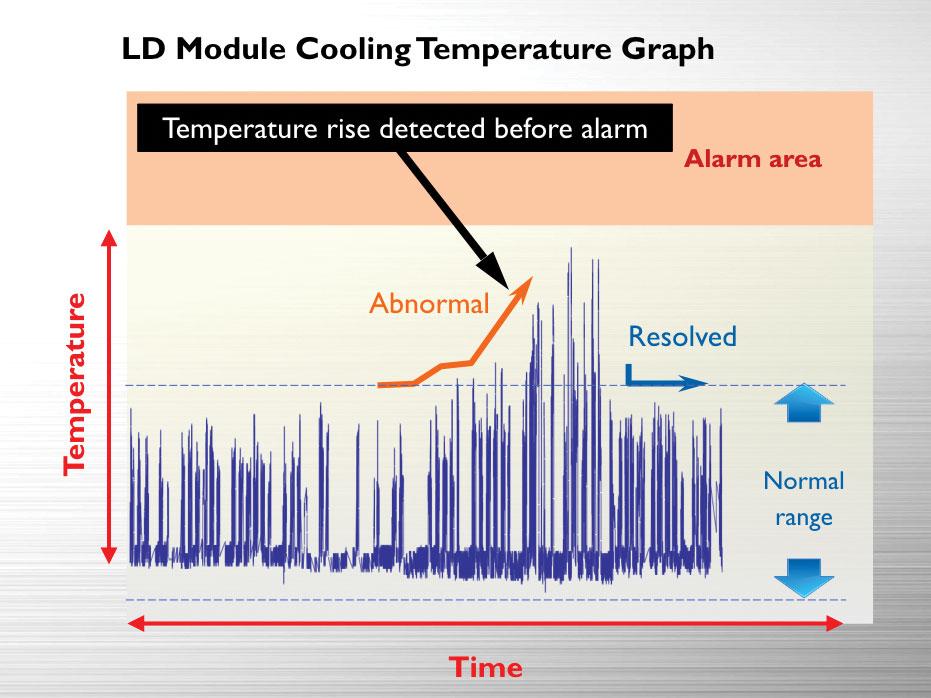
By using software to track normal operating conditions and programming the machine to send an alert when there is a variance, unexpected downtime can be avoided. Image courtesy of Amada America Inc.
A common scenario for a machine-generated notification is when part production stops for more than four or five minutes during lights-out production. Operators aren’t available to see that the machine has stopped and get it back up and running. The machine can send a message to designated recipients, perhaps the foreman, supervisor, and production manager. They can see how long the machine has been down, in many cases see why it is down, and determine actions to be taken and who will be responsible for getting the piece of equipment back online before the next shift discovers that they don’t have the scheduled parts.
Communicate Little Things
Not all machine-to-human communications are based on problems. Some can simply be reminders to perform maintenance and ensure continued production.Don Korfhage, president, founder, and CEO of IGear Online LLC, said, “Manufacturers are continually trying to get more done with fewer operators, maintenance, and quality people—they are responsible for broader areas today. If a machine can reach out and tell them little things like when an oil change is needed or that attention is required because it is getting out of alignment, those little things can be taken care of before they become big things.
“If we can communicate the little things that matter most to an individual and funnel that information in a way that is collaborative and stimulates conversation and action as to how the machine need is satisfied and who is responsible for responding, we can avoid human information overload that triggers annoyance and makes people tune out. You want to interrupt them with actionable information.”
Monitor from Anywhere
When machine-to-human notification first became available, the messages were sent to personal computers within the facility. Now, downloading an app can make these tweet-like machine communications or emails available on tablets, smartphones, and wearable devices.
“Everyone wants transparency—information everywhere. Before it was accomplished by installing a program on a laptop, but now apps are available to share this information anywhere,” said Kutz.
“If you’re a business owner out with friends and you want to stay plugged in, you can see things like if a machine is down for more than 10 minutes. The app can send you a signal and you can click to find out what’s going on and why.”
Customize for Added Value
There is good news and bad news as the IIoT, Industry 4.0, and machine-to-human communications expand. The good news is that the cost of sensors, computation, data storage, and network or band width have come down to a point where getting involved in the advanced technologies is economically feasible. The bad news is that software standardization, such as software for machine-to-human communications, is progressing, but customization is still typically required to take advantage of all its possibilities.
Kim said, “If you are in charge of IT in a small to midsize shop and the owner wants to get involved in IIoT, there are off-the-shelf systems that are fairly easy to implement. They will generate some reports and may have some notification capabilities. From that perspective, implementing machine monitoring software is getting easier because a shop doesn’t have to develop its own. But if the system doesn’t give you the specific data, reports, and recommendations that allow you to take immediate action to improve operations, it lacks the core value.
“Every manufacturer’s operations and priorities are different, and customization of software will ensure that software creates value. Early adopters of machine monitoring software who customize will help shape the commoditized software of the future.”
Yet the software is beginning to find a home in smaller facilities and in companies that have specific needs.
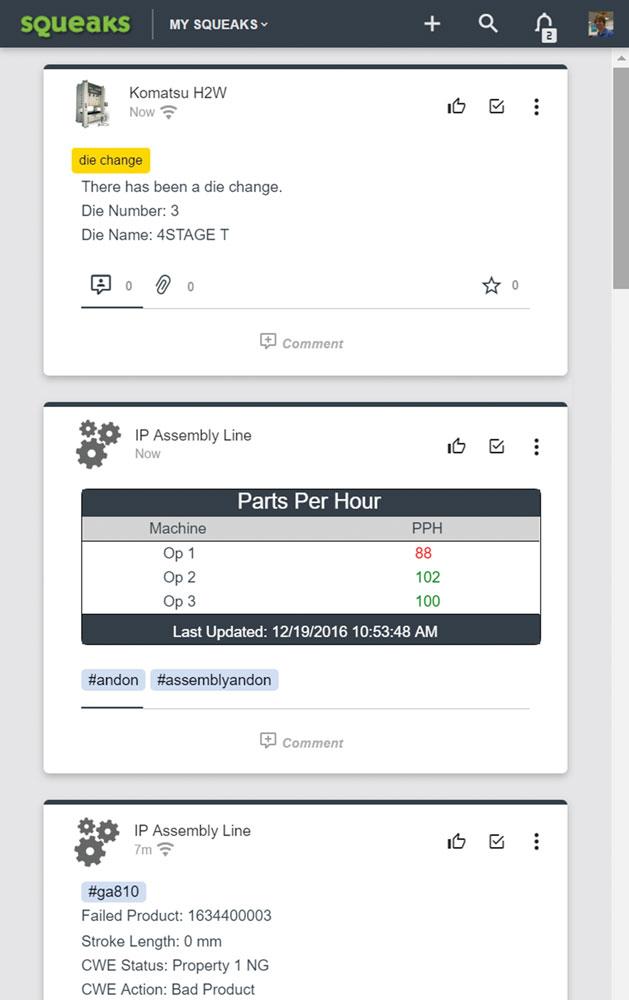
Every event at a machine triggers a record and can be monitored from any location. Photo courtesy IGear Online LLC.
For example, Korfhage said that shops with as many as 200 machines have installed software with machine-to-human communication capabilities and companies with some limited but extreme production requirements have installed it on as few as two machines. “It depends on the immediate need. We have a company with two machines that require precise monitoring and report generation. There are specific criteria and measurements that need to be documented for every part produced on those machines. So the company implemented the software only on those machines, and they send out messages anytime the processes are in danger of slipping outside the acceptable range.”
Manage Server Options
Dealing with the electronic information flow for any type of Internet-based computing involves the question of security regarding transmission of information and storage.
Manufacturers have two choices according to Kim. They can leverage a service that accesses the cloud using a proven secure method for transferring data to a server in a remote location, or they can set up their own in-house server. Both have advantages.
“One advantage of using a service is that you don’t have to set up and maintain a server in your own facility,” said Kim. “And each service offers a set of data analytics and interfaces to choose from. If you have multiple shop locations or if you want to collect information from your customer base, it is easier to aggregate information on the cloud.”
Setting up an in-house server gives the manufacturer the power to control its own data and configure analytics and report tools as desired, but it can be a significant amount of work and require a learning curve, particularly for a company just beginning to build its own IT department.
Just a handful of years ago, security worries made many companies hesitant to initiate technology that required electronic transmission of their data much less depend on their machines to reach out when there was a problem. But personal experiences with cloud technology, like online banking, has increased understanding and confidence in cloud technology.
As manufacturers of all sizes continue to search for ways to become more competitive, IIoT, Industry 4.0, and machine-to-human communications are becoming more widespread and offering more tools to accelerate manufacturing processes. Humans are becoming accustomed to relying on machines to reach out and ask for what they need to keep production running profitably.
Chances are, though, a “tweet” from a machine will require more than passing along.
Amada America Inc., 714-739-2111, www.amada.com
IGear Online LLC, 502-423-0999, www.igearonline.com
TRUMPF Inc., 860-255-6000, www.us.trumpf.com
About the Author
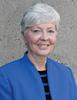
Sue Roberts
2135 Point Blvd
Elgin, IL 60123
815-227-8241
Sue Roberts, associate editor, contributes to both Canadian Metalworking and Canadian Fabricating & Welding. A metalworking industry veteran, she has contributed to marketing communications efforts and written B2B articles for the metal forming and fabricating, agriculture, food, financial, and regional tourism industries.
Roberts is a Northern Illinois University journalism graduate.
subscribe now
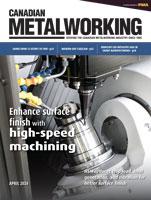
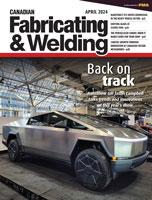
Keep up to date with the latest news, events, and technology for all things metal from our pair of monthly magazines written specifically for Canadian manufacturers!
Start Your Free Subscription- Trending Articles
Aluminum MIG welding wire upgraded with a proprietary and patented surface treatment technology
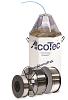
CWB Group launches full-cycle assessment and training program
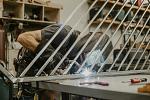
Achieving success with mechanized plasma cutting
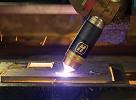
Hypertherm Associates partners with Rapyuta Robotics
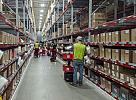
Brushless copper tubing cutter adjusts to ODs up to 2-1/8 in.
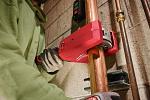
- Industry Events
MME Winnipeg
- April 30, 2024
- Winnipeg, ON Canada
CTMA Economic Uncertainty: Helping You Navigate Windsor Seminar
- April 30, 2024
- Windsor, ON Canada
CTMA Economic Uncertainty: Helping You Navigate Kitchener Seminar
- May 2, 2024
- Kitchener, ON Canada
Automate 2024
- May 6 - 9, 2024
- Chicago, IL
ANCA Open House
- May 7 - 8, 2024
- Wixom, MI