- FMA
- The Fabricator
- FABTECH
- Canadian Metalworking
Let the job determine the speed
Don’t always go for the fastest RPM
- By Sue Roberts
- September 15, 2017
- Article
- Fabricating
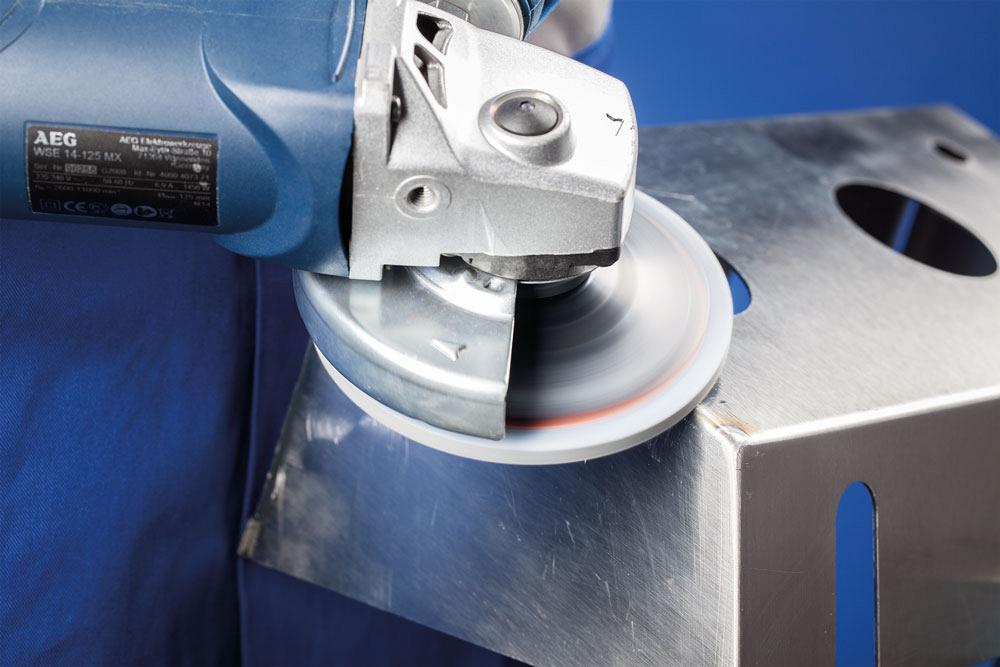
Achieving quality results in finishing applications requires using a lower RPM. Photo courtesy of Pferd Inc.
How many times do you hear, “It depends on the application”?
Well, that applies to hand-held grinder speeds too. The speed, the surface feet per minute, that will be best for productivity, finish, and consumable life might not be the maximum RPM of a single-speed grinder.
For run-of-the-mill applications, the maximum recommended RPM for most angle grinders will—and should be used to—do the job. It’s when you get into specialized or finishing operations, things like a #4 brushed look or a #8 mirror finish, that a lower RPM will produce the smoother finishes easier and with more efficiency.
“Tool manufacturers focus on developing powerful tools, not necessarily on the individual applications,” said Mark Crump, general manager at Pferd Canada. In many cases, they want to develop tools with higher RPMs. The reality is that a faster speed may not be compatible with a full range of applications.
“For instance, if I’m cutting a bolt off a swing set in the backyard, a higher-RPM tool will cut through the material and get the job done faster. But if I want to buff the paint on my car, I certainly wouldn’t use the same 12,000-RPM grinder and consumable. That type of thinking applies to all applications. Just because a consumable fits on a wheel that rotates at 12,000 RPM, it doesn’t mean that it’s OK to use that combination on any application.”
When the object is to remove a lot of stock, a single-speed tool running at its maximum RPM will quickly grind through the material to get the job done. When cosmetics are a factor, Crump said, you should make some determinations on just what the speed is going to be. “As a rule of thumb, we suggest high speed for non-cosmetic stock removal, medium speed when using medium grain abrasive material, and slow speed for fine abrasives and surface finishing to add luster.”
Randy McDonald, national product manager at Fein Canada, said, “You really get into critical RPMs in finishing. The big thing is choosing the right tool. Say a wheel has a maximum 10,000 RPM. It will work at 6,000 RPM and might give you better performance. And you will get better wheel life. When a shop invests in a grinder/polisher, it can run a high RPM for fast material removal then dial down to a lower RPM for the polishing part of a job.
“In some consumables, like fleece, the wheel will work at the maximum RPM. Less heat is generated, however, when run at a lower speed, which can extend the life of the wheel and protect the finish. High speeds and pressure applied during grinding can generate enough heat to melt the fleece. Sometimes the heat from the process can discolour the material, and if you are working on very thin material, the heat can warp the sheet.”
FINISH WITH CONTROL
Dropping speeds can give an operator more control to go after a cosmetic finish. Ryan Boyd, international product manager for tooling and power tools at Walter Surface Technologies, said, “On the finishing side of grinding operations, an operator needs to have more control than when he’s removing regular stock material from an I-beam or blending down a weld.
“He needs control over the workpiece as well as the abrasive. If he was to work at 11,000 RPMs on a 6-in. grinder when trying to produce a #4 brushed finish, the abrasive or finishing disc might bounce all over the place because he is working against the speed of the grinder when trying to move more slowly than usual.
“But if he is trying to achieve a mirror finish in stainless, for example, and using a variable-speed polishing or finishing tool, paired with a fine-grit wheel or polishing abrasive rated to 5,000 or 6,000 RPM, he would be more efficient by dropping his RPM for more control over the abrasive on the wheel and more control along the workpiece.
“Finishing tools have the gear systems and electronic components built-in to allow the wheel to turn consistently at a lower RPM but still apply enough pressure to adjust the finish of the surface much more than when working at 11,000 RPMs.”
WATCH OUT FOR GLAZING
Be cautious and use the proper equipment to slow down.
The amount of pressure applied by the operator comes into play as well as the equipment power levels, said Marc Brunet-Gagné, product manager for bonded abrasives at Walter Surface Technologies: “If you use a low-power grinder running at a high RPM, normally you will get full rotation when the wheel is free—not touching any metal. But as soon as you contact the material, which applies pressure to the wheel, the RPM automatically goes down. You can get a buildup of heat in the material, which transfers and overheats the wheel’s bond. It will glaze the wheel and prevent it from cutting or grinding well anymore.”
Glazing is visually apparent on the wheels and can be caused by a wheel running too slow. McDonald said it almost looks like the wheel is burnt. The abrasive grain becomes dull and doesn’t cut or grind efficiently. Slowing for a finishing job done per equipment and consumable recommendations can provide a cosmetic finish and increase the life of the disc.
“If a wheel is glazed, it must be deglazed to work again, Brunet-Gagné said. “Otherwise you are just going to polish the workpiece. If you are using a high-power machine with a coarse grit for grinding and you apply high pressure with a high RPM, you will get maximum performance and dig into the material without overheating. The heat will be ejected by the sparks, which creates good performance.”
“If it’s a coated abrasive, either a standard sanding disc or non-woven material, nylon-based material, or even a finishing compound, then the consumable’s performance and life are going to improve by going a little slower. Adjust speed based on grit size,” said Crump.
Non-woven materials, he added, can be relatively speed-sensitive because the abrasive grain builds up friction and the nylon can melt, so it is better to have a range of speeds available.
“The harmonics that affect control and noise may also be reduced with a small adjustment on overall RPM," said Crump.
Boyd said, “Working at the highest RPM, even if it is a variable speed machine, may give you the fastest removal rate for grinding. But depending on the tool or abrasive, the abrasive could wear more quickly, and you might not get the overall productivity. “If you switch to more of the finishing side of the grinding application, then adjusting your RPMs is very important.”
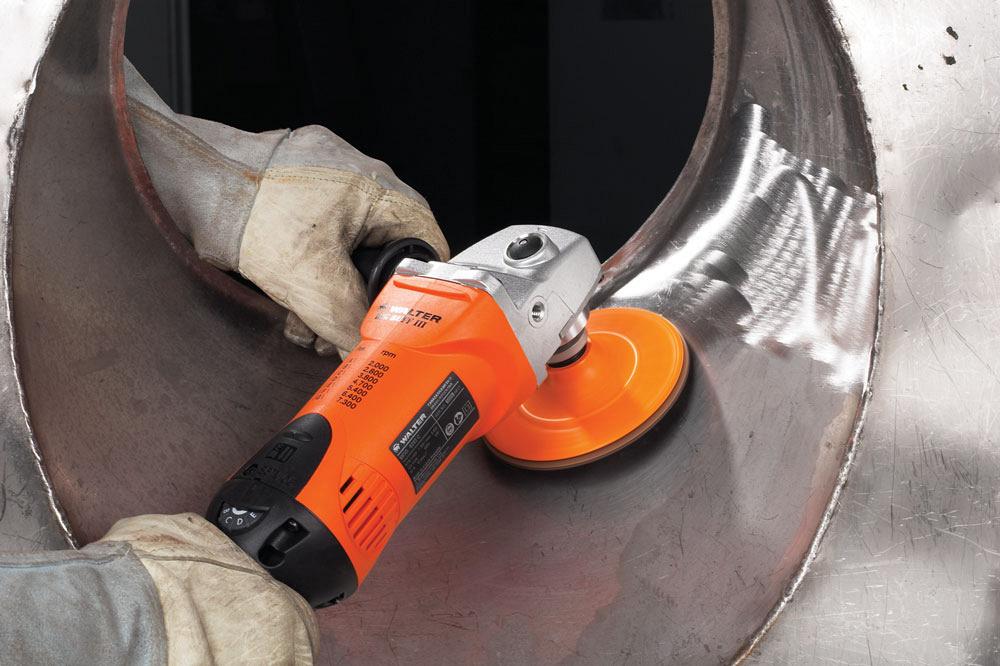
Finishing tools have gear systems and electronic components built-in to allow the wheel to run consistently at a lower RPM to achieve a quality result. Photo courtesy of Walter Surface Technologies.
Associate Editor Sue Roberts can be reached at sroberts@canadianfabweld.com.
Fein Canada, 800-265-2581, www.fein.ca
Pferd Inc., 866-245-1555, www.pferdcanada.ca
Walter Surface Technologies, 514-630-2800, www.walter.com
About the Author
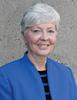
Sue Roberts
2135 Point Blvd
Elgin, IL 60123
815-227-8241
Sue Roberts, associate editor, contributes to both Canadian Metalworking and Canadian Fabricating & Welding. A metalworking industry veteran, she has contributed to marketing communications efforts and written B2B articles for the metal forming and fabricating, agriculture, food, financial, and regional tourism industries.
Roberts is a Northern Illinois University journalism graduate.
subscribe now
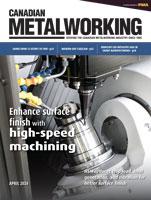
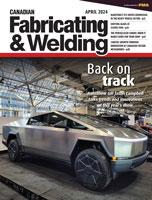
Keep up to date with the latest news, events, and technology for all things metal from our pair of monthly magazines written specifically for Canadian manufacturers!
Start Your Free Subscription- Trending Articles
Aluminum MIG welding wire upgraded with a proprietary and patented surface treatment technology
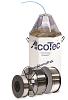
CWB Group launches full-cycle assessment and training program
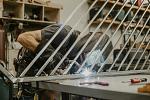
Achieving success with mechanized plasma cutting
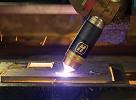
Hypertherm Associates partners with Rapyuta Robotics
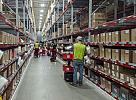
Brushless copper tubing cutter adjusts to ODs up to 2-1/8 in.
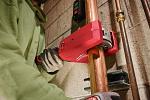
- Industry Events
MME Winnipeg
- April 30, 2024
- Winnipeg, ON Canada
CTMA Economic Uncertainty: Helping You Navigate Windsor Seminar
- April 30, 2024
- Windsor, ON Canada
CTMA Economic Uncertainty: Helping You Navigate Kitchener Seminar
- May 2, 2024
- Kitchener, ON Canada
Automate 2024
- May 6 - 9, 2024
- Chicago, IL
ANCA Open House
- May 7 - 8, 2024
- Wixom, MI