Editor
- FMA
- The Fabricator
- FABTECH
- Canadian Metalworking
Northern College celebrates 50th with welding investments
New plasma tables, advanced welding machines offer newer tools to students in varied programs
- By Rob Colman
- August 28, 2017
- Article
- Fabricating
Northern College of Kirkland Lake, Ont., has made a name for itself with its welding engineering technician and technologist programs. The college is the only one in North America authorized by the International Institute of Welding as an Authorized Training Body, which means that the school can graduate welding engineering technologists with the International Welding Technologist (IWT) designation, a certification valid in 59 countries.
But the college has also introduced innovations in its welder/fitter program. It is a two-year program that has been compressed into one full year of learning to allow students to enter the workforce more rapidly. Like many other colleges, Northern tries to adapt its programs to the needs of the market.
Plasma Programming Benefits
The two Torchmate plasma cutting tables are a big change for the college. One is a 4-ft. by 8-ft. table and the other is 4-ft. by 4-ft. The tables have a relatively small footprint and come preassembled, benefits for the college.
The college’s shop cuts mostly 1/16-in., 1/8-in., and 20-gauge material, and Tim Skjonsby, who teaches CAD and fixture design, says the new tables allow students to get clean cuts with great precision on complex parts in these materials.
However, it’s the CNC programming part of the equation that really makes a big difference for the students, according to Skjonsby.
“Students get AutoCAD® free from the day they enroll, and although students do learn how to draft technical drawings manually, for very complex shapes it’s quick and efficient to use these programs,” Skjonsby explained. “And realistically, that is probably what they would be doing out in the field. It also teaches them the efficiency of doing things in AutoCAD, and brings drafting to life. Using AutoCAD, you can bring a file down to the shop floor quickly and almost instantly have a working part made.”
It also demonstrates errors quickly because if a student sends a bad drawing to the cutting table, the controls will tell them immediately. So, in the process the student learns and the school saves on scrap material.
“The CNC programming makes cutting quick and simple, but it also shows students that you can’t take shortcuts,” said Skjonsby.
“In the process, we also demonstrate how the math that we’ve taught them in the classroom ties into the practical processes on a shop floor,” said Tyy Dearden, welder/fitter professor at the college.
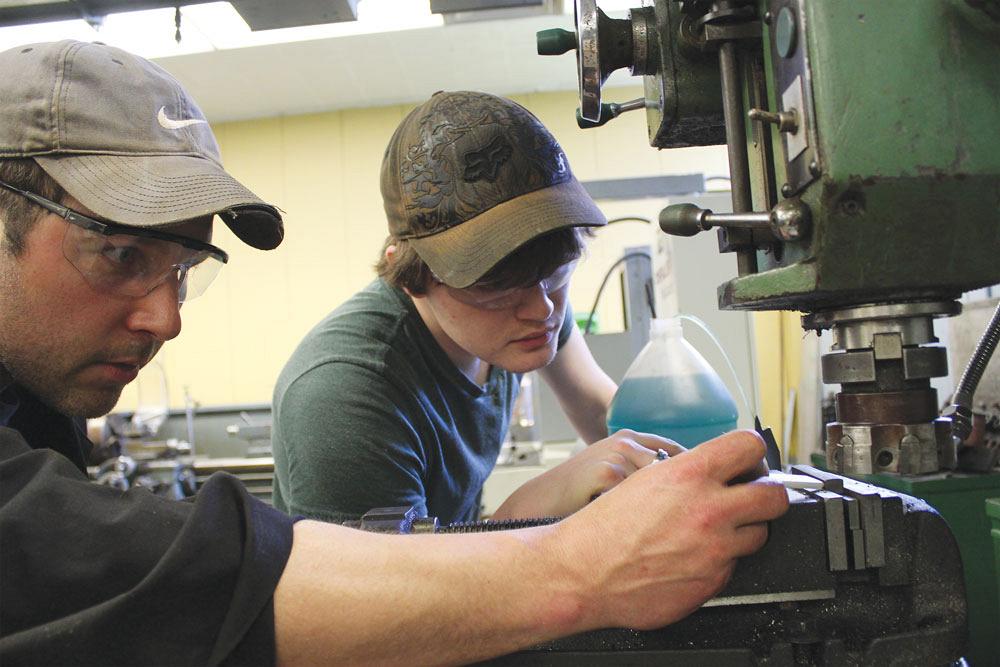
Welding fitter student Reuben Desjardins learns from professor Tim Skjonsby how to machine specimens for a Charpy impact test.
Both Dearden and Skjonsby noted that the price of the tables also made the decision to invest in two easier, which in turn gives each student more time with the technology.
Aluminum Welding Growth
Joshua Fuller, program coordinator for Northern’s School of Welding Engineering Technology, noted that a lot of the college’s graduates go on to work in the mining industry, and having some exposure to aluminum welding can be beneficial to them.
“In mining, a lot of the time, weight is everything,” Fuller said. “At the local mine here in Kirkland Lake, a lot of people are getting certified for aluminum welding, and we can now offer support in that area.”
The reason Northern can do so is that it has invested in a Lincoln POWER MIG® 350MP MIG machine. The machine features an aluminum pulse process, making it easier to get a clean weld on this challenging material. “The machine allows control of pre-flow, post-flows, run-ins, and crater fill. There is so much control that it can confuse new students, so we start them off on the pre-programmed numbers and work them up from there,” said Dearden.
Hand-held Upgrades
Fuller and others are quick to note that they try to give students introductions to a broad selection of processes and technologies they will likely see out in the field. “We like to make sure that students are exposed to all of the major welding power source makes—whether it be ESAB, Miller, Lincoln, or more exotic ones such as Fronius,” said Fuller.
For instance, the school also recently invested in a Victor 200i hand-held plasma cutting machine. This unit is capable of hand cutting up to 2-3/4-in. mild steel at 200 amps. At full output, it can cut 10 inches per minute on 2-in. carbon steel. It has dual gas system capability, which makes it possible to cut ferrous and non-ferrous materials cleanly. This last ability was key for Northern.
“This machine allows us to easily transition from using compressed air as a cutting gas and shielding gas to mixed gases so we can have very clean cuts on stainless steels and nickels,” said David Rogalsky, professor in the welding engineering technician and technologist programs. “That gives us the opportunity to work on some more exotic alloys. Basically, we use this to review different types of materials and determine the fastest way to make production cuts in certain materials. It’s important for us that we can transfer this knowledge to the workforce quickly. Time is money. This allows the students to understand how to specify a cutting process, apply that process, and write up cutting procedures to improve productivity and increase quality.”
Northern is equipped to run the cutter as a hand-held or on an automated carriage.
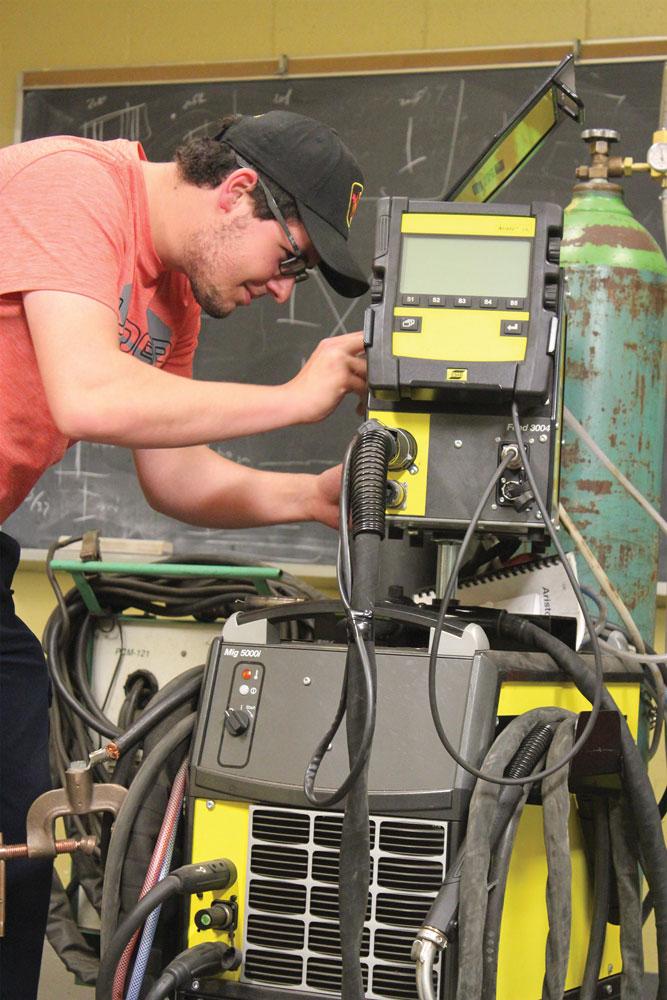
First-year welding engineering technician student Eric Roy checks the wire feed tension on an ESAB 5000i welding system.
“Doing tests with an automated system is nice because we eliminate the human error factor in the tests,” said Rogalsky. “At the same time, being able to do the cuts by hand, the students learn what type of field issues there might be.”
Celebration Support
Northern has always been very involved in the Kirkland Lake community, creating sculptures and other projects in its shop for the community. For its 50th anniversary, students in the welder/fitter program are helping to create two park benches that will be located on walking trails in town. It’s a small gesture to the community while being a real-life project for the students involved.
That connection to industry and the community at large is something that is very important to the college. And with its new investments, it is even better prepared to offer the sort of outreach Northern always hopes to encourage.
Editor Robert Colman can be reached at rcolman@canadianfabweld.com.About the Author
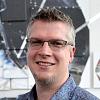
Rob Colman
1154 Warden Avenue
Toronto, M1R 0A1 Canada
905-235-0471
Robert Colman has worked as a writer and editor for more than 25 years, covering the needs of a variety of trades. He has been dedicated to the metalworking industry for the past 13 years, serving as editor for Metalworking Production & Purchasing (MP&P) and, since January 2016, the editor of Canadian Fabricating & Welding. He graduated with a B.A. degree from McGill University and a Master’s degree from UBC.
subscribe now
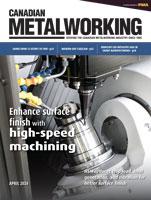
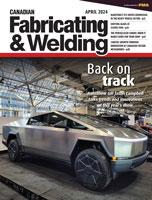
Keep up to date with the latest news, events, and technology for all things metal from our pair of monthly magazines written specifically for Canadian manufacturers!
Start Your Free Subscription- Trending Articles
Aluminum MIG welding wire upgraded with a proprietary and patented surface treatment technology
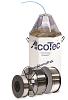
CWB Group launches full-cycle assessment and training program
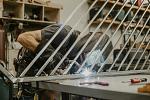
Achieving success with mechanized plasma cutting
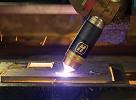
Hypertherm Associates partners with Rapyuta Robotics
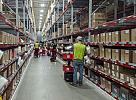
Brushless copper tubing cutter adjusts to ODs up to 2-1/8 in.
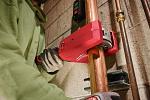
- Industry Events
MME Winnipeg
- April 30, 2024
- Winnipeg, ON Canada
CTMA Economic Uncertainty: Helping You Navigate Windsor Seminar
- April 30, 2024
- Windsor, ON Canada
CTMA Economic Uncertainty: Helping You Navigate Kitchener Seminar
- May 2, 2024
- Kitchener, ON Canada
Automate 2024
- May 6 - 9, 2024
- Chicago, IL
ANCA Open House
- May 7 - 8, 2024
- Wixom, MI