Editor
- FMA
- The Fabricator
- FABTECH
- Canadian Metalworking
Abrasives safety classes make a difference at Saskatchewan Polytechnic
Guest instructor J.R. Kuntz of Saint-Gobain Abrasives emphasizes understanding the tool in your hands and your complete environment
- By Rob Colman
- September 28, 2016
- Article
- Metal Finishing
Safety instruction in any part of a shop can make a big difference in the smooth running of operations. School environments are no different. Saskatchewan Polytechnic’s Moose Jaw campus has experienced this firsthand. Since John (J.R.) Kuntz started serving as a guest instructor at the polytechnic in 2013, teaching students in the welding program about abrasives safety in a special seminar, no grinding accidents have occurred. The school has also experienced tooling cost savings.
Kuntz is a Saint-Gobain Abrasives sales representative in the region. When he originally visited the polytechnic, it was strictly a sales call. But he has a real passion for teaching about safety, and so he offered to share his expertise.
“If we teach students the right way to use products, whether they be ours or those of a competitor, we are likely to see more of them remain in the trades, and fewer will get injured,” said Kuntz. “It also gives me the opportunity to combat the words that drive me crazy: ‘This is the way we’ve always done it.’ When a young person starts as an apprentice, they may enter a shop that has three or four very experienced tradespeople, and there is a tendency to pick up their bad habits, corners they cut maybe just because they don’t know that there is a safer way to do the job. By getting this training, hopefully the students enter their first job with a little bit more confidence in their own skills and practices.”
Kuntz noted that he also offers training to end users through his company’s safety training program.
“Saint-Gobain encourages us to promote and train as many people as possible on safe grinding applications,” he said. “I conduct at least 10 training courses a year on-site for end users that want to invest in employee safety.”
Top Problem: Speed Ratings
When asked what he emphasizes most in his safety seminars, Kuntz doesn’t hesitate to answer speed ratings.
“I encourage students to pay attention to the speed rating on the product as well as the tool,” Kuntz said. “This is something that a lot of people take for granted, and it is the primary cause of most failures.
“For instance, the use of 5-inch products is very common in western Canada, and the average speed of most tools on the market is 10,000 RPM,” he continued. “However, there are some models of 5-inch grinders that actually spin at 12,000 RPM. Depending on the particular grinding wheel that you’re using, some may not be rated high enough to mount on the 12,000-RPM tool, which can lead to a catastrophic failure. And it is not usually the operator who ends up injured in this situation; it’s usually someone working nearby.”
Storage
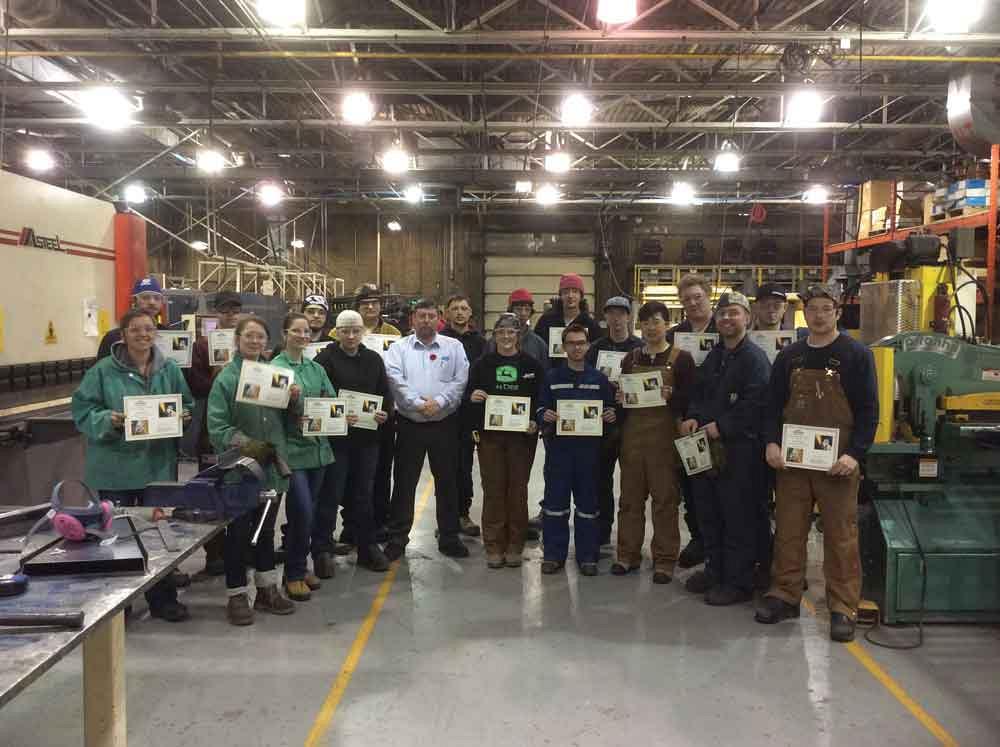
These students are graduates of the Norton / Saint Gobain Abrasives Safety Seminar at Saskatchewan Polytechnic.
Ensuring that abrasives don’t freeze because of improper storage comes in second as a concern for Kuntz.
“On the prairies it’s cold seven months of the year,” he said. “So it’s a matter of making the students aware of the conditions in which they are going to work, their surroundings, and making sure the product is stored properly. When an abrasive freezes, the resins that hold the wheel together crystallize, become brittle, and can come apart.”
Tool Modification
Kuntz repeated an adage that if you have to alter the tool to do the job, it’s probably not the right tool. Unfortunately, that doesn’t stop enthusiastic operators from trying to change their tools.
“The biggest issue is the lack of guards on grinders in shops,” Kuntz said. “It’s typically one of the first things that operators remove when handed a brand-new tool. They view it as an encumbrance. What I do in the classroom is explain why it is in the best interests for the students to leave the guard there.”
Kuntz noted that pneumatic tools in larger facilities are often plagued by modifications: overpressuring the tool, removing the regulating valve, and enlarging the exhaust ports to make the tool run faster are just a few examples of what he has seen. He encourages students and other users not to make these modifications as they put everyone at risk.
Ergonomics
Kuntz noted that most thin-wheeled products on a right-angle grinder should be used on an angle of between 15 and 30 degrees. Yet he often sees operators using them virtually flat on the workpiece, with the back side of the wheel coming into contact with the workpiece as well as the front of the wheel.
“This isn’t great for the wheel because no matter how much pressure you put on it, you won’t be able to hold the wheel down so you’re not actually grinding on the back side of the wheel,” Kuntz explained. “All it’s really doing is rubbing, and you run the risk of severing the fiberglass reinforcement that holds the wheel together. Once you do that, typically the wheel comes apart. It’s a sobering thought that on a typical 5-in. grinder that spins at 10,000 RPM, when a wheel fails, the pieces leave the wheel at over 200 MPH.”
Kuntz uses a lot of show-and-tell in his classes – samples of wheels that have failed catastrophically and what the result looks like depending on the type of failure. The students are certainly paying attention.
“My class often comments on how engaging and interesting the course is,” said Scott Parent, a welding instructor at the polytechnic.
And it appears to be sinking in with the students.
“One thing that Saskatchewan Polytechnic has seen as a derivative of this training that I would never have dreamed of is that they have noticed a substantial reduction in tool repairs because the students have taken ownership of the tool and the process,” Kuntz explained. “They are starting to turn tools in when they feel there is something wrong, which might mean replacing a $17 bearing rather than a $200 gear head.”
It’s a positive exchange for the school and for Kuntz: students get his expertise, and he meets potential customers. Most importantly for everyone, however, is that many of these students will take safe practices into their future workplaces.
Editor Robert Colman can be reached at rcolman@canadianfabweld.com.
Saskatchewan Polytechnic, 866-467-4287, http://saskpolytech.ca
Saint-Gobain Abrasives, 508-795-2317, www.saint-gobain-abrasives.com.
About the Author
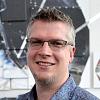
Rob Colman
1154 Warden Avenue
Toronto, M1R 0A1 Canada
905-235-0471
Robert Colman has worked as a writer and editor for more than 25 years, covering the needs of a variety of trades. He has been dedicated to the metalworking industry for the past 13 years, serving as editor for Metalworking Production & Purchasing (MP&P) and, since January 2016, the editor of Canadian Fabricating & Welding. He graduated with a B.A. degree from McGill University and a Master’s degree from UBC.
subscribe now
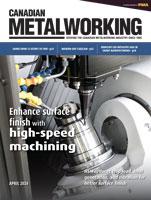
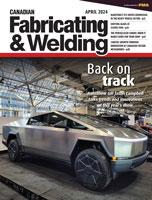
Keep up to date with the latest news, events, and technology for all things metal from our pair of monthly magazines written specifically for Canadian manufacturers!
Start Your Free Subscription- Trending Articles
Aluminum MIG welding wire upgraded with a proprietary and patented surface treatment technology
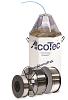
CWB Group launches full-cycle assessment and training program
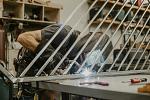
Achieving success with mechanized plasma cutting
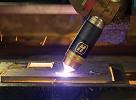
Hypertherm Associates partners with Rapyuta Robotics
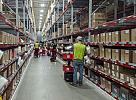
Brushless copper tubing cutter adjusts to ODs up to 2-1/8 in.
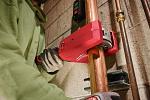
- Industry Events
MME Winnipeg
- April 30, 2024
- Winnipeg, ON Canada
CTMA Economic Uncertainty: Helping You Navigate Windsor Seminar
- April 30, 2024
- Windsor, ON Canada
CTMA Economic Uncertainty: Helping You Navigate Kitchener Seminar
- May 2, 2024
- Kitchener, ON Canada
Automate 2024
- May 6 - 9, 2024
- Chicago, IL
ANCA Open House
- May 7 - 8, 2024
- Wixom, MI