- FMA
- The Fabricator
- FABTECH
- Canadian Metalworking
Business Profile: Russel Metals
This Winnipeg shop is focused on efficiency.
- By Canadian Metalworking
- May 27, 2015
- Article
- Fabricating
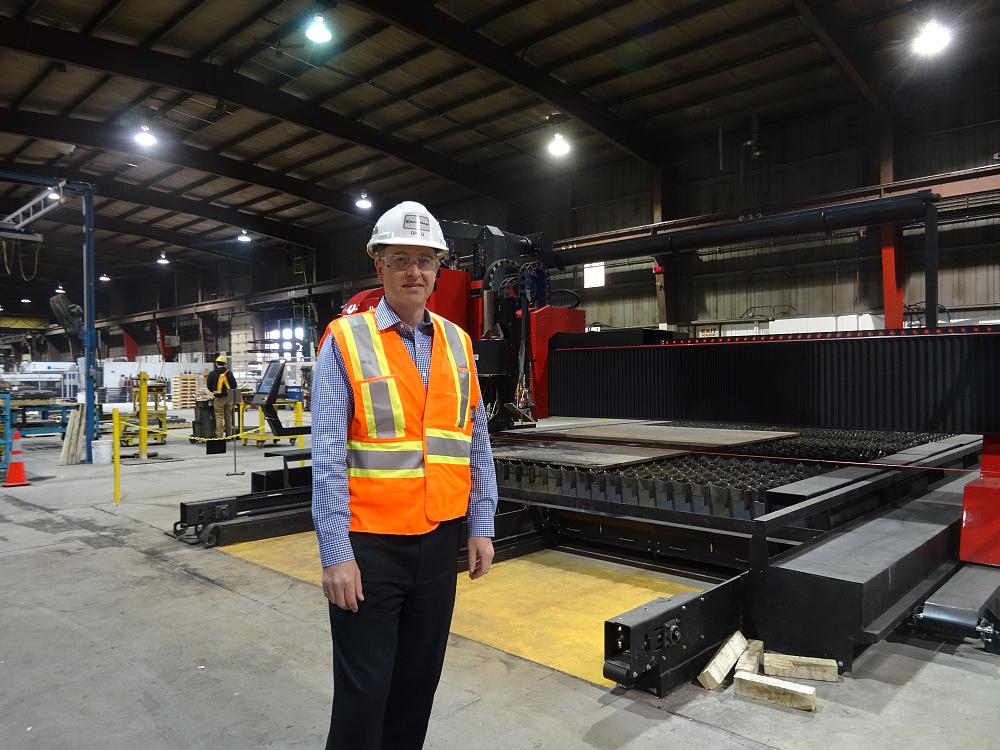
Greg Ozog, branch manager of the Russel Metal’s Winnipeg facility, stands in front of the company’s new machine, a Kinetic K5000xmc multi-functional cutting and drilling machine.
The success of any large organization relies on the efficient performance of every division. Russel Metals is among the largest metal distribution and processing companies in North America with 139 locations. And while the company is able to take advantage of its scale to provide value to customers, it’s the added touches that each of its localized service centres demonstrate that leads to its continuing growth.
Headquartered in Mississauga, Ontario, Russel Metals has a long history in Canada tracing its roots back to Montreal in 1784. The company passed through many generations, and in the 1940s expanded beyond Montreal with its first locations in Winnipeg, Vancouver, Saint John, Windsor and Toronto. Growing through acquisition over the years, in 1984 Russel became part of the multi-disciplined conglomerate Federal Industries. A decade later, after deciding to focus exclusively on the metals business, the parent company took on the Russel Metals name. In 2014 the organization reported sales of $3.87 billion, up 21 per cent from 2013, marking five consecutive years of sales growth.
Despite its size and scale, Russel Metals manages its businesses in a decentralized fashion, with local managers accountable for day-to-day operations, profitability and growth of their business. The service centers across the organization distribute primarily carbon steel products, along with stainless steel, aluminum and other specialty products, offering plate, bars, sheet, pipe, tubing and structural steels offering various processing services as well.
In Winnipeg the company operates three facilities, a main distribution hub which offers cut-to-length, distribution and some processing capabilities, a specialty metals branch and a more dedicated processing facility where the recent installation of a new combination cutting and drilling machine is adding another level of service to its local clients.
“In recent years Russel service centers have continued to garner market share by adding this sophisticated processing equipment allowing us to add value for our customers, a strategy adopted and implemented several years ago at our Winnipeg facility,” notes Greg Ozog, branch manager of the Russel Metals Winnipeg processing facility. Within its 78,000 sq. ft. industrial space the shop has a line-up of flat and tube laser cutters, various press brakes and some welding capabilities.
“We assist our customers in primary processing that is one step beyond raw material,” explains Ozog. But while the branch is largely focused on simple processing of metal parts, they’re also what he calls a contract processing center or a “build to print” organization.
“We do a lot of program work, where we’ve worked with customers to develop certain projects and continue to do those year over year.” Russel has worked with clients from prototyping right through to production. Aside from operators on the shop floor, the team includes an engineering support group and CAD designers/programmers.
[gallery type="slideshow" link="none" size="full" ids="110707,110706,110703"]
For his part, Ozog, as branch manager, works with around 85 people, running a 24/7 operation.
A mechanical engineer and MBA graduating from the University of Manitoba, prior to joining Russel he spent over 20 years working in the local aerospace industry where he was exposed to lean manufacturing concepts.
It’s a philosophy that he’s brought with him, with the plant going through a lean transformation over the past six years. It’s an ongoing continuous improvement process that extends from the office and onto the shop floor. “We’ve worked with CME for a lot of the training,” says Ozog. Russel also part of a Lean Consortium, with some 12 companies, which he describes as a great way for sharing lean culture experiences and best practices.
“It’s allowed us to become a lot more flexible, nimble and able to react. Our focus is always to make our customers successful through ease of transaction. The concepts of lean manufacturing and continuous improvement through technological advancement are not novel to any industry. The talented group of people who I am fortunate to work with every day implemented the concepts in extraordinary fashion and continue to search for improvement daily. Our team’s unrivaled commitment, which is driven by a desire to partner with our customers by adding value, creates an energetic culture that is refreshing and challenging to work in every day,” he says.
By improving Russel’s own internal processes, it’s enabled the branch to maximize its lean practices to the benefit of its customers. During the process Russel has evolved and continues to improve to a more organized and streamlined operation leading to better inventory management and just-in-time delivery practices.
He points to the lack of congestion on the shop floor as an example. Where the shop used to keep two weeks of work in progress on the floor, now only two days WIP is common. “It looks like we don’t have as much work, but actually we’re busier than we’ve been in the past.”
Russle has also recently created room on the floor for a new Kinetic K5000 multi-functional cutter and drilling machine. The new machine will introduce plasma cutting and light machining to the operation. Russel had access to a plasma cutter at the other Winnipeg distribution facility, but it was an older machine that had come to the end of its life where it was beyond economical to repair. “We knew we had to replace it, and when we considered customer demands it led to us expanding what we could offer,” explains Ozog.
The K5000 arrived in January and was commissioned in March under the supervision of the operations manager, Mark Somogyi and his maintenance team, and the shop is still in the early stages of the learning curve. “This machine allows Russel to do processes that were done on multiple machines before, so now we will reduce our material handling, improve our delivery lead times, and ultimately improve our cost competitiveness, because there’s constant pressure for cost reductions.”
The new services include including bevel cuts, drilling holes, tapping holes, countersinking and more. “It’s exciting for us to see what it can do,” he says, noting that it’s already opened up the envelope of work opportunities the shop can now offer to clients.
“We’ve quoted some interesting projects and should be executing them in the third quarter. These are thick parts with some heavy bevelling on them, so it will be interesting to figure out how we can best do those.”
He’s also been impressed with how clean the machine operates, its chip removal and compact operating design, which is a good fit in the branch’s clean and lean culture.
[gallery type="slideshow" link="none" size="full" ids="110704,110705"]
The remaining challenge is getting the operators experience with the new technology in order to overcome the learning curve. “It will take time to go through all of the different materials, thicknesses, different drill bits and cutting speeds, but that’s part of the process,” says Ozog, noting that it’s all in the manual, but a much more complex operation than traditional burning.
We have great operators on our team and are investing in further training by sending them to machining courses in order to gain a broader context on those aspects of the technology.
At the same time, the Russel team is introducing the new technology to its customers collectively evaluating the new possibilities and potential efficiencies in an effort to add value to the supply chain.
Russel is excited about the opportunity to grow the business. “Winnipeg is a manufacturing hotbed,” says Ozog, noting that there is a lot of laser cutting capacity in the province and this further diversifies the RMI offering.
Despite the cyclical nature of the service center industry, Russel’s processing business remains steady, supporting numerous local industries including plenty of agricultural, transportation including transit buses and coaches, tractors, industrial materials serving the oil and gas industries among others.
One thing you can’t prepare for are broad industry declines like the oil industry has experienced lately, and the residual industries it’s affected. Ozog credits Russel’s continuous improvement culture for keeping the processing component of the business focused and on track.
“Our whole lean journey has enabled Russel to be more flexible and nimble throughout the various economic cycles focusing on further efficiencies and improved response times. We are more versatile allowing us to adapt and continuously improve in order to partner with our customers providing them a competitive advantage to grow their businesses.”
About the Author
subscribe now
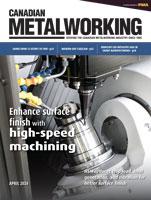
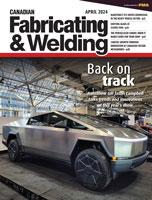
Keep up to date with the latest news, events, and technology for all things metal from our pair of monthly magazines written specifically for Canadian manufacturers!
Start Your Free Subscription- Trending Articles
Aluminum MIG welding wire upgraded with a proprietary and patented surface treatment technology
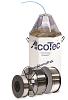
CWB Group launches full-cycle assessment and training program
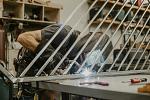
Achieving success with mechanized plasma cutting
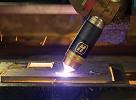
Hypertherm Associates partners with Rapyuta Robotics
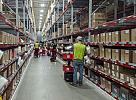
Brushless copper tubing cutter adjusts to ODs up to 2-1/8 in.
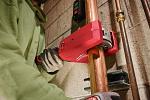
- Industry Events
MME Winnipeg
- April 30, 2024
- Winnipeg, ON Canada
CTMA Economic Uncertainty: Helping You Navigate Windsor Seminar
- April 30, 2024
- Windsor, ON Canada
CTMA Economic Uncertainty: Helping You Navigate Kitchener Seminar
- May 2, 2024
- Kitchener, ON Canada
Automate 2024
- May 6 - 9, 2024
- Chicago, IL
ANCA Open House
- May 7 - 8, 2024
- Wixom, MI