Editor
- FMA
- The Fabricator
- FABTECH
- Canadian Metalworking
Cobot helps build capacity at Skyvington Manufacturing
Store fixture supplier invests in new welding tables, flexible automation
- By Rob Colman
- October 2, 2023
- Article
- Automation and Software
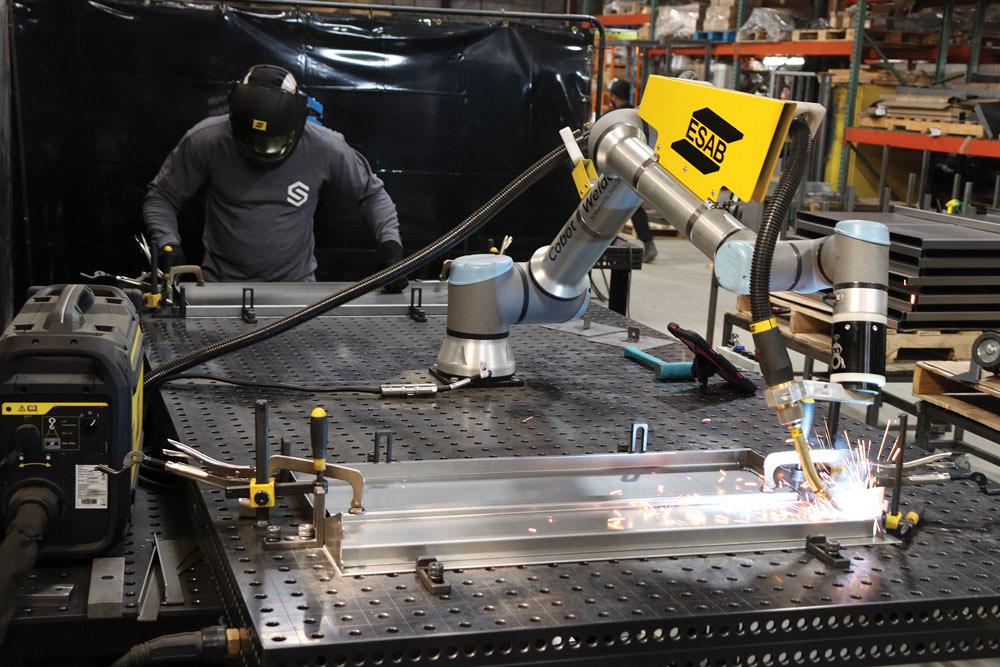
When SMI was considering investing in welding automation, everyone in the shop agreed that a cobot was a very good option. Photos: SMI
When Skyvington Manufacturing Inc. (SMI) wanted to add capacity to its welding shop, the management team knew that it would require either an investment in more skilled welders or automation. Although automation was the obvious choice in this era of ever-decreasing lead times, finding the right fit for the shop’s product mix still needed to be considered.
Skyvington Company History
Founded by Ray Skyvington in 1995, the Mississauga, Ont.-based SMI is a turnkey supplier of store fixtures and retail displays for customers across North America. For most of that time, the company focused on the design side of the business and outsourced the custom fabrication work. But eventually, to ensure timely delivery to customers, management decided to bring fabrication in-house.
“Initially, we worked as a sales and engineering service for our customers, but we kept running into supply chain issues,” said Brett Skyvington, manager of the company’s fabrication operations. “Six years ago, we took control of our metal fabrication needs by purchasing the equipment necessary to build what we considered our dream shop.”
“The companies we work with have very high-quality control expectations, and the biggest thing that Brett picked up on when he set up the manufacturing operation was the quality that was required to be able to build and sustain a profitable company,” said Ray Skyvington.
“We have clients that have been with us since we were founded in 1995. They are extremely loyal because of our attention to detail and ability to exceed their expectations.”
Continuous Investments
Although its manufacturing operations have only been up and running for six years, SMI has continually invested in new equipment to ensure it can deliver what its customers require on time, to spec, and designed in such a way that it is comparatively easy and cost efficient to manufacture. The shop works in steel, stainless, aluminum, and other specialty metals in sheet, wire, and tube. The company has also moved into supplying glass, plastic, and wood fabrications to its customers, as well as peripherals like assembly, packaging, and graphics.
SMI currently runs an LVD 6-kW fibre laser equipped with a six-pallet tower and the company’s CADMAN programming software, a SafanDarley 100-ton electric press brake, and Baykal 160-ton and 60-ton hydraulic press brakes.
“The Safan is a relatively new purchase, with Wila premium tooling and hydraulic clamping,” said Brett. “We are also planning on investing in new software for the brakes so all of the programming can be programmed off-line.
"We are primarily a small to medium-run job shop,” Brett continued. “However, occasionally, jobs are much larger. We manufactured and distributed display cabinets to convenience stores and gas stations when a large vaping company came to Canada, which amounted to 30,000 cabinets in a year. We are equipped for those large runs. Today, you need that versatility to both prototype or run small jobs as well as be able to scale up and run mass production.”
Welding Upgrades
“We are continuously assessing the tools and technology across the shop in order to upgrade as necessary,” said Brett. “Most recently, that has involved working through the welding department to see how we can become more efficient.”

The cobot is equipped with an Aristo 500ix power source and a Universal Robots robotic arm with a maximum reach of 51.2 in. Although it can be moved throughout the shop, SMI also attaches the arm to a 5- by 10-ft. table, allowing the operator to load parts on one side while the cobot welds on the other side. Longer parts can be affixed to be processed on the table.
The first investment, which occurred last November, was to replace all stations in the welding shop with Siegmund fixture tables.
“The simplicity that comes from not having to build jigs and fixtures is a huge time saver,” said Ray. “When you’re making a prototype for a client, that is very important. The first week we had the tables, we had to build three prototypes that would have taken the guys three to four days to make if they had to traditionally jig how they were going to put it together. With the efficiency gained by the fixture tables, we had all three prototypes made in less than a day.
“Previously, we would have tied up critical production of our top guys to building fixtures and lose floor space to fixture storage for those jobs,” continued Ray.
The newest purchase at the shop, however, is an ESAB cobot equipped with an Aristo 500ix power source and a Universal Robots robotic arm with a maximum reach of 51.2 in. Although it comes with a cart that allows it to be moved throughout a shop, SMI also attaches the arm to a 5- by 10-ft. table, allowing the operator to load parts on one side of the table while the cobot welds on the other side. Longer parts also can be affixed to be processed on the table.
“We previously had a traditional turntable-style welding cell,” said Brett. “It was difficult to program and not really suited to what we need on a day-to-day basis. We would run it a few times a year for very large-run production jobs that involved anywhere between 60 and 120 welds, but it would take forever to fixture and program. It didn’t suit our production mix and took up a lot of room.”
Cobot Choice
After talking with his team, Brett agreed that a cobot was a very good option. “It is really the way a lot of the industry is going, particularly for manufacturers of our size and weight class,” he noted.
Since installing the cobot in February, SMI has already seen an impact.
“For example, we have been running a large fixture job, welding end caps and weld nuts onto thousands of tubes,” said Brett. “Each tube requires about 20 linear inches of welding, plus handling. We would have needed to bring on a second shift to run this program, but because of the versatility of the cobot, we can affix a number of these tubes to the side of the table as well as fixture them vertically and just run right through them. The cobot allows us to push quite a bit more volume through the shop without going out and having to staff additional shifts.”
At this time last year, SMI’s production ran 24 hours a day, six days a week. Now, it is running a shift and a half a day during the week and a single shift on Saturdays.
“And we are doing more volume at this point than we were doing last year,” said Brett. “Having the cobot and the tables has allowed us to specialize and to really focus on our core group of welders instead of scaling to handle production. Adding people for multiple shifts can lead to quality concerns; we want a core group of people who have a lot of industry experience or people with great attitudes who want to learn and who share our philosophy and attention to detail. These days, it’s crucial to understand what equipment is available to produce better and faster products because that is where the industry is heading.”
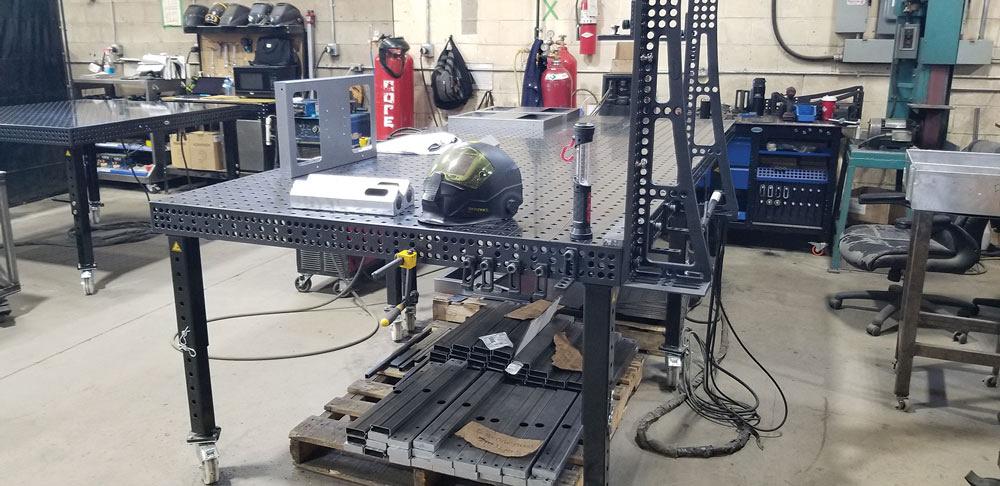
Before even investing in the cobot, SMI improved its welding precision by replacing all stations in the welding shop with Siegmund fixture tables.
Dialed-In Precision
Like so many other shops, SMI is concerned about finding skilled employees. The company is fortunate to have very experienced employees heading up its forming, machining, and welding departments, but new technology will have to do the heavy lifting to keep production numbers high.
“Experienced welders and press brake operators are the hardest to find,” said Brett. “Finding press brake operators who understand integers, formulas, and bend radiuses are hard to find; and experienced welders in general are difficult to find. This is why we are investing in technology like the cobot and off-line press brake programming software.”
In terms of improving weld throughput and quality, Brett noted, “How do you make a mediocre welder better? Give him better notches, better fit and finish in the parts that he is getting so then they’re not having to fill large gaps or get creative with their approach. Between our engineering department, the fibre laser, press brakes, and the fixturing tables, we are doing what we can to make that happen.”
In addition, being able to dial-in the cobot to make more precise welds also saves time in post-processing operations such as polishing.
Flexible Operations
The cobot is shipped on one skid and takes about two hours to put together, and it includes a cart. SMI often mounts the cobot on its 5- by 10-ft table but likes having the ability to be able to move it to the cart in a matter of minutes for use elsewhere.
“We sometimes have three or four setups on the table that we run through at once,” said Brett. “At one point, we positioned it next to our spot welder. The operator spot welds the product where necessary, then turns around with the part, clamps it down, and the cobot MIG welds that part as the operator spot welds the next one. As long as it has an internet connection wherever it is placed, it can run without a problem.
”Using the fixturing tables, which are very precisely built, we can mount the cobot as required, repeatably to a very tight tolerance. There’s no need to touch up and check its alignment constantly, which was necessary with the robot on our old cell.”
SMI does its best to use the welding cobot where it can run three to four times faster than a person. Often, an operator will be doing whatever TIG work is necessary on an assembly while the cobot takes care of the MIG welds.
“It used to be that we needed large-run jobs to be able to utilize our robotic solutions, but now we can do it for much smaller runs. Being able to use an automated solution on jobs that were previously unfeasible for us is a big gain,” said Brett. In terms of programming, Ray and Brett note that even non-welders in the shop have learned to run the cobot.
“Using the app on your phone or tablet makes programming the cobot simple, and the app is very intuitive,” said Brett. “The guys got an hour training on it, watched a few videos, and we were programming jobs because it was so easy to use. It doesn’t involve a teach pendant, it doesn’t require you to program a lead-in to the weld. It’s very easy. In the same amount of time, with a traditional robot you’re still in the theory stage of how it is going to run.
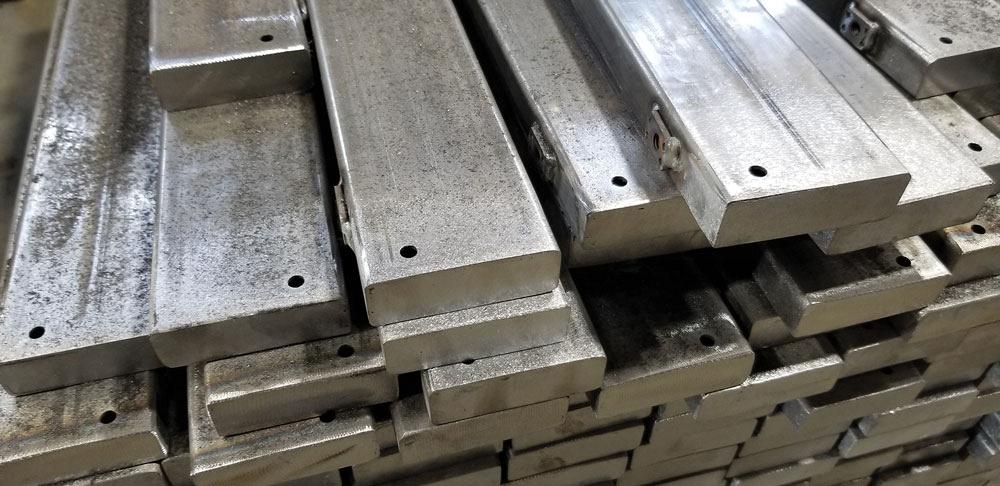
Each of the tubes pictured requires about 20 linear inches of welding, plus handling. This would have required a second shift to run, but because of the versatility of the cobot, SMI can affix a number of these tubes to the side of a table as well as fixture them vertically and run through the program efficiently.
“It’s also easy to make tweaks to the setups you’ve created. We do it all the time for different types of welds. For instance, you can globally change the wire feed speeds, heat, or voltage, depending on what you’re doing. With two clicks you can change the weld parameters across a whole program. It saves hours and hours of programming time.”
It’s also possible to monitor the welds throughout the day. The reporting software gives feedback on parts volume, wire feed speed, wire consumption, and gas consumption.
“We have full metrics on what parts are running, how many are running in a day, what programs have been run, and which operators were operating the cobot,” said Brett.
SMI ran thousands of components through the cobot in its first month of operation, amounting to 25,000 welds.
“In the first month, the ESAB cobot ran 2,600 of these different dividers that will go into a big box home improvement chain across the United Sates,” said Brett. “We then had it weld 600 tube caps and then a secondary process welding gussets for casters on 1,500 display bases. I think the cobot has averaged between 30 and 45 seconds a weld since it came into our shop. Over the course of the first month, the metrics available through the app confirmed we made 25,000 welds.”
Information Flow
This data is particularly important to SMI as it’s in the process of upgrading to the Epicor Kinetic ERP system. It will be integrating production data into the ERP system directly.
“We monitor as much as we possibly can in the company,” said Brett. “The new ERP system is going to make it easier to integrate all the data in the same place and better clarify our production flow and scheduling.”
SMI doesn’t have a huge footprint and works on a just-in-time (JIT) production model, which made Epicor’s JIT modelling capabilities a draw for them. Given that SMI can move from prototyping to full-scale production in a matter of hours is key.
“Ultimately, all of these investments are aimed at making a better, more affordable product for the customer,” said Brett.
“We encourage engineering and our designers to be able to work with production to say, ‘Hey look, how can we make a thing more effectively? What else can we modify and/or change to be able to improve the quality of the product and make it more repeatable in production?’” said Ray.
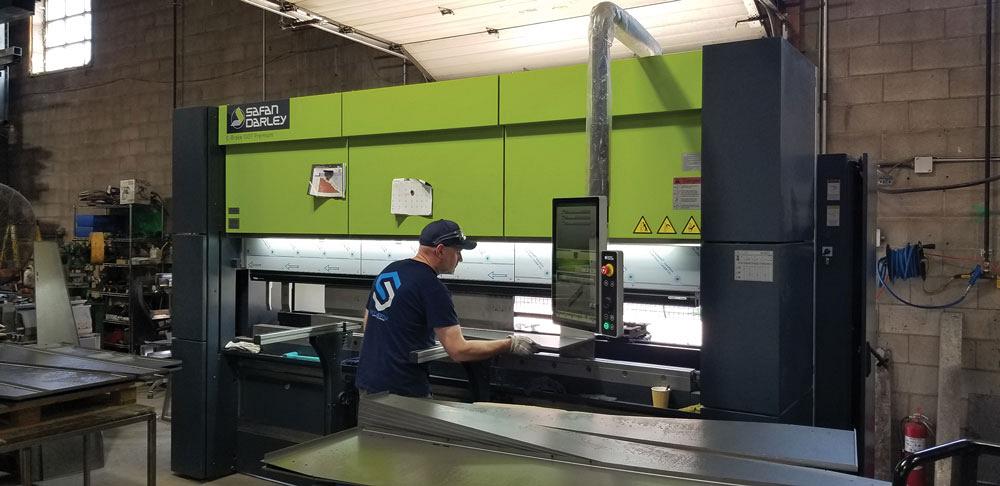
SMI has continually invested in new equipment over the last six years. In addition to this recently acquired SafanDarley 100-ton electric press brake, the shop also has an LVD 6-kW fibre laser equipped with a six-pallet tower, and Baykal 160-ton and 60-ton hydraulic press brakes.
“Our goal is to pass the savings we are able to realize through good investments in technology and people back to our clients, while also being a lot more profitable ourselves. That has always been the directive right from the day Brett set the manufacturing operation up: we invest in good products that are going to be in the marketplace for a long time; we learn and teach our team better ways to do things and build that depth of knowledge so that the next time we're confronted with something, there's fewer questions that have to be asked between the front office and the shop to get to what we think is the right solution,” Ray continued.
“In the end, everyone benefits.”
Editor Robert Colman can be reached at rcolman@fmamfg.org.
Skyvington Manufacturing Inc., skymfg.com
Bernd Siegmund, siegmund.com
ESAB, esab.com
SafanDarley, safandarley.com
Westway Machinery, westwaymachinery.com
About the Author
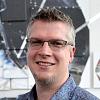
Rob Colman
1154 Warden Avenue
Toronto, M1R 0A1 Canada
905-235-0471
Robert Colman has worked as a writer and editor for more than 25 years, covering the needs of a variety of trades. He has been dedicated to the metalworking industry for the past 13 years, serving as editor for Metalworking Production & Purchasing (MP&P) and, since January 2016, the editor of Canadian Fabricating & Welding. He graduated with a B.A. degree from McGill University and a Master’s degree from UBC.
subscribe now
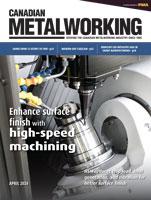
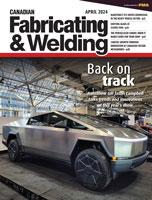
Keep up to date with the latest news, events, and technology for all things metal from our pair of monthly magazines written specifically for Canadian manufacturers!
Start Your Free Subscription- Trending Articles
Aluminum MIG welding wire upgraded with a proprietary and patented surface treatment technology
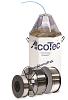
Achieving success with mechanized plasma cutting
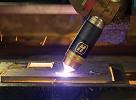
Hypertherm Associates partners with Rapyuta Robotics
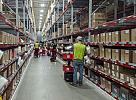
Gema welcomes controller

Brushless copper tubing cutter adjusts to ODs up to 2-1/8 in.
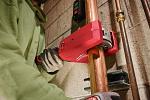
- Industry Events
MME Winnipeg
- April 30, 2024
- Winnipeg, ON Canada
CTMA Economic Uncertainty: Helping You Navigate Windsor Seminar
- April 30, 2024
- Windsor, ON Canada
CTMA Economic Uncertainty: Helping You Navigate Kitchener Seminar
- May 2, 2024
- Kitchener, ON Canada
Automate 2024
- May 6 - 9, 2024
- Chicago, IL
ANCA Open House
- May 7 - 8, 2024
- Wixom, MI