Associate Editor
- FMA
- The Fabricator
- FABTECH
- Canadian Metalworking
Dive into predictive maintenance and planning
Gathering data and trends can help manufacturers make better business decisions
- By Lindsay Luminoso
- January 12, 2024
- Article
- Automation and Software
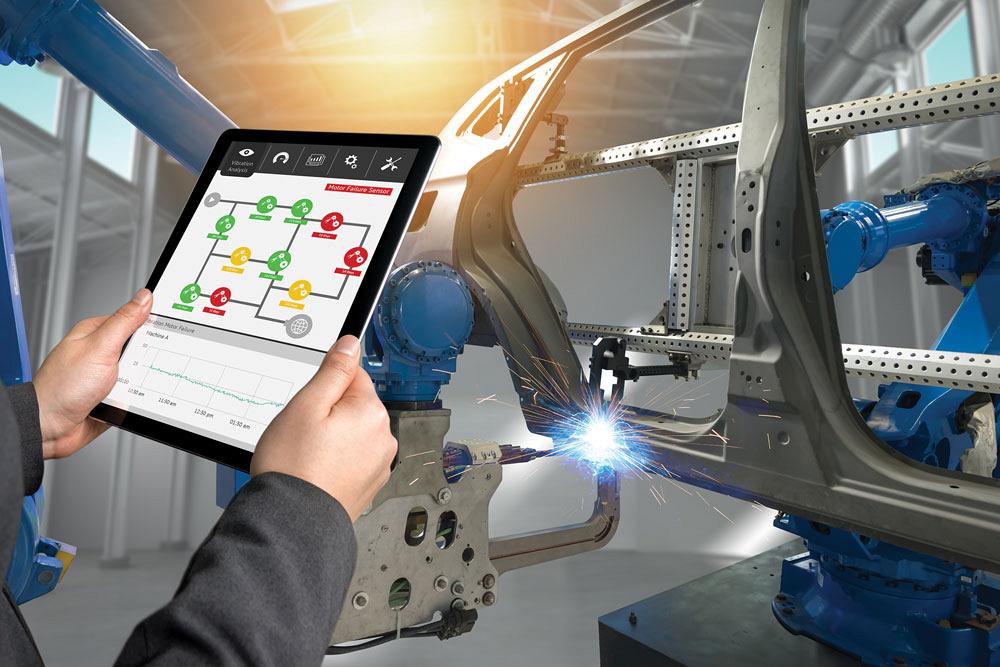
Colour-code three to five metrics that workers should be managing. If something is red or yellow, immediate action should be taken. Assigning colour codes and emphasizing metrics moves shops away from the “don’t fix something until it’s broken” mentality. JIRAROJ PRADITCHAROENKUL/iStock/Getty Images Plus
Manufacturers today are inundated with data. But that data is useless unless it can be analyzed and applied to key metrics to make actionable decisions about current processes and future plans. Here are five steps to help you get started leveraging their data to support predictive maintenance and planning.
1) Gather Data
Predictive maintenance and predictive planning are as reliable as the data that it is built upon. While you may not know how to turn data into an actionable planning resource, the first step is to start collecting data.
“Just start now,” said Kate Brown, data and analytics leader, manufacturing, retail, and distribution, Wipfli, Milwaukee, Wis. “If you want to get into any sort of AI or predictive planning in the next two to five years, you need to have a foundation with data to make that happen. Start collecting it today, and then you can later move on to exploring that data.”
It’s important to explore where your data is coming from. Is it automatically being fed into a system, or is it sitting in the heads of your shop floor workers? These are important features to understand when it comes to the quality of the data.
“The bottom line in manufacturing is that we need to get accurate data,” said Duane Clement, founder and CEO, Data Inventions, ECI Software Solutions, Erie, Pa. “Getting that foundation of accurate data is essential to then leverage actionable information to then make improvements. It’s all about building a foundation of data that a company can build upon for its improvement road map.”
You can focus on optimizing equipment utilization and operator performance, but without data, you may have no idea where they currently stand. Start with a paper checklist. But the more machines and personnel you have, the less feasible it becomes to manually collect data, find a system that can aggregate it.
“Data is essential for any shop to thrive,” said Clement. “Most manufacturers know this but really don’t know how to take advantage of it.”
One way to do this is to look at what you would like to understand better about your business. Do you want to see how accurate scheduling is or is material management a current red flag? What does your backlog look like? What are your bottlenecks?
“Pick one area that you want to know more about and determine what data will be needed to gain actionable insights,” said Brown. “There could be multiple variables needed to really understand the situation. This is known as data discovery, and this can help businesses wade through the vast amount of data available.”
2) Clean Up Existing Data and Processes
Once you start gathering data, it’s time to aggregate it and sort through how and why that data is being collected. Oftentimes, there is not a lot of consistency when it comes to data collection.
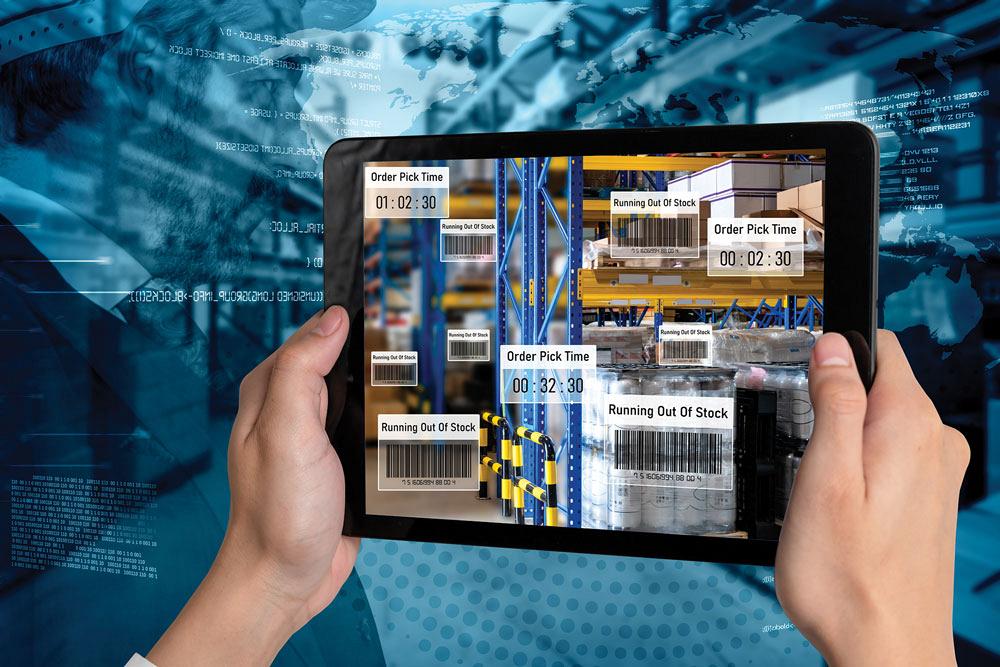
Start simple. Use a barcode scanner to upload data rather than entering it manually. Automated data collection allows the software to then deliver analytics and actionable information. NanoStockk/iStock/Getty Images Plus
“If your organization has a CRM system, is it passing any information onto the ERP system?” said Brown. “Does the information need to be manually added? Could each system be creating different records for the same customers or projects? Are the systems holding on to outdated information? Are the systems auto-updating across connected programs? You can have lots of useless or inaccurate data and it’s important to ensure that it is an accurate source of truth to make any good decisions based on it.”
It may take a while to understand just how much data cleansing is needed, but it’s an important step. Leadership and decision-makers must have confidence in the data coming in. In situations where there is a lot of data transformation or cleansing, it might be worth going back to see how it is being collected and how to fix the collection processes.
3) Implement AI and Technology Tools
“Machines are generating information and you have systems that you're either entering information [into] or pulling information from,” said Clement. “Historically, the industry's been far too reliant on manual data collection. We really have to be able to automate that. Or the other thing that you hear loud and clear on the floor is if it's not easy, they won't do it.”
Assess the whole value stream. How does an order get created? What are the different steps it goes through? Does that order need to travel in between different systems and if so, is it manual right now? And is there an easy way to automate that?
“Sensors are very affordable,” said Brown. “You can just attach it to a machine without needing the invest in new equipment. A sensor will be able to tell you how the machine is running at any given time. This is a low-cost and low-barrier point of entry into automating data collection.”
There are a number of tools on the market, including cloud-based options, that require little to no customizations. These tools will deploy analytics technology so that fabricators can connect the sensors and data to the tool and have access to a dashboard to monitor machine performance.
“In the past, the problem in manufacturing has been that the average company is using many different systems,” said Clement. “They have an ERP system, a quoting system, a quality system, a document system, a program, and more. And in most cases, they weren’t integrated with each other.”
Consistency in the way you collect data is important, but so is how you analyze and view the data. The ultimate goal to move into predictive planning and maintenance is to be able to compare similar metrics from various sources to determine actual versus target performance.
It’s important to make sure that the tools fit the environment and people, not the other way around.
Today’s data software tools are becoming more advanced with additional AI capabilities and advanced analytics. Choose something that will help you grow your business and will grow with your business. It can be overwhelming when deciding what will work best for your business, but it should be simple and easy to work with.
“It can be as simple as investing in barcode scanners to upload data rather than manual entry,” said Brown. “These tools will provide the software with data to then deliver analytics and actionable information. Don’t start with a big implementation, work with what makes sense for your business.”
4) Get Data Literate
Change can be hard, and sometimes there is pushback when implementing new technology. This is why it is critical to develop a base level of data literacy within an organization. Everyone, regardless of their role with the business, needs to understand why gathering information is important and how they can use it going forward.
“These tools can create dashboards and reports for someone on the shop floor, but if they aren’t data literate, knowing what to do with that data and how to act on it, it may not yield the expected ROI.”
Workers need to understand how they're going to act on this. Start making more data-driven decisions on the shop floor. Determine what truly matters and what data points make sense to share. Don’t inundate workers with information that isn’t important.
“Highlight three to five metrics that workers should be managing,” said Brown. “Colour-code them. If something is red or yellow, immediate action should be taken. The good news is that a lot of tools have this natural language processing functionality, like ChatGPT. This will make it easier for employees to ask questions, and the software will respond with a cohesive story about the data while explaining trends.”
Assigning colour codes and emphasizing metrics moves shops away from the “don’t fix something until it’s broken” mentality. It alerts people to trends that they may otherwise be unaware of. You’ll become more efficient the more aware you are of the processes and trends, and you can use this information to take steps to stop problems before they begin.
“Once everybody can really start to engage on the real information, it's amazing the kind of collaboration you can get,” said Clement. “However, it’s important to note that this won’t happen overnight. Companies have to grow into this and model how to use data effectively in day-to-day operations so that they can plan better for the future. Without showing workers what that looks like, it can be difficult.”
5) Apply Insights to Targets
The whole purpose of gathering and organizing data is to help you use that information to take actionable steps. Most manufacturers use a variety of tools to both on the shop floor and to manage business.
One of the biggest challenges is connecting real-time shop floor data with office systems. In some instances, management may have a surface-level understanding of what is going on in and around the shop floor, but they may not know specifics.
“It’s important to develop a whole data strategy around bringing all that information together and being able to do it in more of a reproducible way,” said Clement. “Putting that information in the right place, you can drive upwards of 15 to 20 per cent improvements in things like utilization in a matter of a month. If you give people accurate information with visibility into it, they take more ownership, they feel more accountability.”
By collecting data in a consistent, methodical way, you can plug in a couple of data points into a model and very accurately predict future revenue outcomes, which can help with predictive planning.
If you quote a job using bad data, that could be a big drain on the business. Constantly comparing targets with actual insights will give you a clearer picture of what’s working and what isn’t.
“Once you have fundamentals in place, you can start to introduce a higher level of analytic products, like predictive analytics,” said Clement. “You still have to maintain it. You still have to make it as automated as it can possibly be. It cannot be siloed. You need to measure conditions of the machines and understand what was running on them to be able to develop models and AI that can effectively trigger when a machine might be ready to fail.”
Predictive maintenance and planning are about modelling the data from the machine in a way that allows you to predict certain types of failure. Setting targets and seeing how closely aligned real-time data fits within those will allow not only future optimization, but better analytics for future initiatives.
Associate Editor Lindsay Luminoso can be reached at lluminoso@fmamfg.org.
ECI Software Solutions, www.ecisolutions.com
Wipfli, www.wipfli.com
About the Author
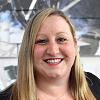
Lindsay Luminoso
1154 Warden Avenue
Toronto, M1R 0A1 Canada
Lindsay Luminoso, associate editor, contributes to both Canadian Metalworking and Canadian Fabricating & Welding. She worked as an associate editor/web editor, at Canadian Metalworking from 2014-2016 and was most recently an associate editor at Design Engineering.
Luminoso has a bachelor of arts from Carleton University, a bachelor of education from Ottawa University, and a graduate certificate in book, magazine, and digital publishing from Centennial College.
subscribe now
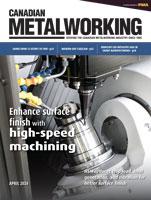
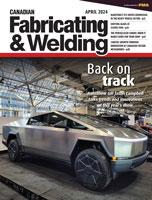
Keep up to date with the latest news, events, and technology for all things metal from our pair of monthly magazines written specifically for Canadian manufacturers!
Start Your Free Subscription- Trending Articles
Aluminum MIG welding wire upgraded with a proprietary and patented surface treatment technology
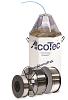
Achieving success with mechanized plasma cutting
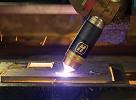
Hypertherm Associates partners with Rapyuta Robotics
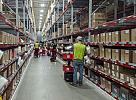
Gema welcomes controller

Brushless copper tubing cutter adjusts to ODs up to 2-1/8 in.
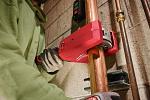
- Industry Events
MME Winnipeg
- April 30, 2024
- Winnipeg, ON Canada
CTMA Economic Uncertainty: Helping You Navigate Windsor Seminar
- April 30, 2024
- Windsor, ON Canada
CTMA Economic Uncertainty: Helping You Navigate Kitchener Seminar
- May 2, 2024
- Kitchener, ON Canada
Automate 2024
- May 6 - 9, 2024
- Chicago, IL
ANCA Open House
- May 7 - 8, 2024
- Wixom, MI